Introduction to PCB Manufacturing
PCB (Printed Circuit Board) manufacturing is a crucial process in the electronics industry. It involves the creation of electronic circuits on a non-conductive substrate, typically made of fiberglass or other composite materials. The quality of PCB manufacturing directly impacts the performance, reliability, and longevity of electronic devices.
In this article, we will explore the key factors that determine the best PCB manufacturing practices and how to ensure that your PCB manufacturer is delivering the highest quality products.
The Importance of High-Quality PCB Manufacturing
High-quality PCB manufacturing is essential for several reasons:
- Reliability: Well-manufactured PCBs ensure that electronic devices function reliably and consistently over their intended lifespan.
- Performance: High-quality PCBs minimize signal interference, maintain signal integrity, and enable optimal performance of electronic components.
- Durability: Robust PCB manufacturing processes result in boards that can withstand various environmental factors, such as temperature fluctuations, vibrations, and moisture.
- Cost-effectiveness: Investing in high-quality PCB manufacturing reduces the risk of product failures, minimizes rework, and ultimately saves costs in the long run.
Key Factors in Determining the Best PCB Manufacturing
1. Material Selection
The choice of materials used in PCB manufacturing significantly influences the quality and performance of the final product. High-quality PCB Manufacturers use premium materials that meet industry standards and are suitable for the specific application. Some key considerations include:
- Substrate Material: FR-4 is the most common substrate material used in PCB manufacturing due to its excellent electrical and mechanical properties. However, for high-frequency or high-temperature applications, other materials like Rogers, Polyimide, or Teflon may be more appropriate.
- Copper Thickness: The thickness of the copper layer on the PCB affects its current-carrying capacity and signal integrity. PCB manufacturers should select the appropriate copper thickness based on the design requirements and industry standards.
- Solder Mask: A high-quality solder mask ensures proper insulation, prevents short circuits, and enhances the PCB’s durability. The solder mask should be evenly applied, have good adhesion, and meet the specified color and finish requirements.
2. Manufacturing Processes
The manufacturing processes employed by a PCB manufacturer directly impact the quality and consistency of the final product. Best-in-class PCB manufacturers adhere to strict process controls and utilize advanced technologies to ensure the highest quality standards. Some critical manufacturing processes include:
- Etching: The etching process removes unwanted copper from the PCB substrate, leaving only the desired circuit pattern. High-quality PCB manufacturers use precise etching techniques, such as photochemical etching or plasma etching, to achieve fine feature sizes and maintain the integrity of the circuit design.
- Drilling: Holes are drilled into the PCB substrate to accommodate components and enable electrical connections between layers. The drilling process should be accurate, with minimal deviation from the specified hole sizes and positions. Advanced drilling technologies, such as laser drilling or controlled-depth drilling, ensure high precision and minimize damage to the substrate.
- Plating: Copper plating is applied to the drilled holes and on the PCB surface to establish electrical connectivity and improve the board’s conductivity. The plating process should result in a uniform and consistent copper layer thickness, without any voids or defects.
- Lamination: Multi-layer PCBs require the lamination of multiple substrate layers together using heat and pressure. The lamination process should ensure proper alignment of layers, minimize air gaps, and maintain the overall structural integrity of the PCB.
3. Quality Control and Testing
Rigorous quality control and testing procedures are essential to ensure that PCBs meet the required specifications and perform reliably. Best-in-class PCB manufacturers employ comprehensive quality assurance measures at various stages of the manufacturing process. Some key quality control and testing practices include:
- Automated Optical Inspection (AOI): AOI systems use high-resolution cameras and advanced algorithms to detect surface defects, such as solder bridges, missing components, or incorrect component placement. AOI helps identify issues early in the manufacturing process, reducing the risk of defective boards reaching the final product.
- X-Ray Inspection: X-ray inspection is used to detect internal defects, such as voids in solder joints, damaged vias, or misaligned components. This non-destructive testing method provides a detailed view of the PCB’s internal structure, ensuring the integrity of hidden connections.
- Electrical Testing: Electrical testing verifies the functionality and performance of the PCB. This includes continuity testing to ensure proper electrical connections, insulation resistance testing to detect potential short circuits, and high-potential (HiPot) testing to verify the board’s dielectric strength.
- Functional Testing: Functional testing involves subjecting the PCB to real-world operating conditions to validate its performance and reliability. This may include temperature cycling, vibration testing, and power cycling to simulate the expected environmental stresses the PCB will encounter in its intended application.
4. Certifications and Standards Compliance
Reputable PCB manufacturers adhere to industry-recognized certifications and standards to demonstrate their commitment to quality and reliability. Some key certifications and standards to look for include:
- ISO 9001: This quality management system standard ensures that the PCB manufacturer has a robust and consistent approach to quality control, customer satisfaction, and continuous improvement.
- IPC Standards: IPC (Association Connecting Electronics Industries) develops and maintains industry standards for PCB design, fabrication, and assembly. Compliance with relevant IPC standards, such as IPC-A-600 (Acceptability of Printed Boards) or IPC-6012 (Qualification and Performance Specification for Rigid Printed Boards), demonstrates a manufacturer’s adherence to internationally recognized quality guidelines.
- UL Certification: Underwriters Laboratories (UL) is a global safety certification company that tests and certifies PCBs for safety and performance. UL certification ensures that the PCB meets stringent safety requirements and can be used in products that require UL compliance.
5. Customer Support and Collaboration
The best PCB manufacturers prioritize customer support and collaboration throughout the manufacturing process. They work closely with their clients to understand their specific requirements, provide design recommendations, and offer technical assistance when needed. Some key aspects of customer support and collaboration include:
- Design for Manufacturability (DFM) Feedback: High-quality PCB manufacturers review the customer’s design files and provide feedback on potential manufacturability issues. They suggest improvements to enhance the PCB’s reliability, reduce manufacturing costs, and optimize the overall production process.
- Prototyping and Sampling: Reputable PCB manufacturers offer quick-turn Prototyping Services to help customers validate their designs before moving to full-scale production. They provide high-quality samples that closely represent the final product, allowing customers to test and refine their designs.
- Technical Support: Best-in-class PCB manufacturers have knowledgeable technical support teams that can assist customers with any questions or issues that arise during the manufacturing process. They provide prompt and accurate responses, helping to resolve problems quickly and efficiently.
- Flexibility and Customization: The best PCB manufacturers are flexible and willing to accommodate custom requirements. They work with customers to develop tailored solutions that meet their specific needs, whether it involves unique materials, special finishes, or non-standard design features.
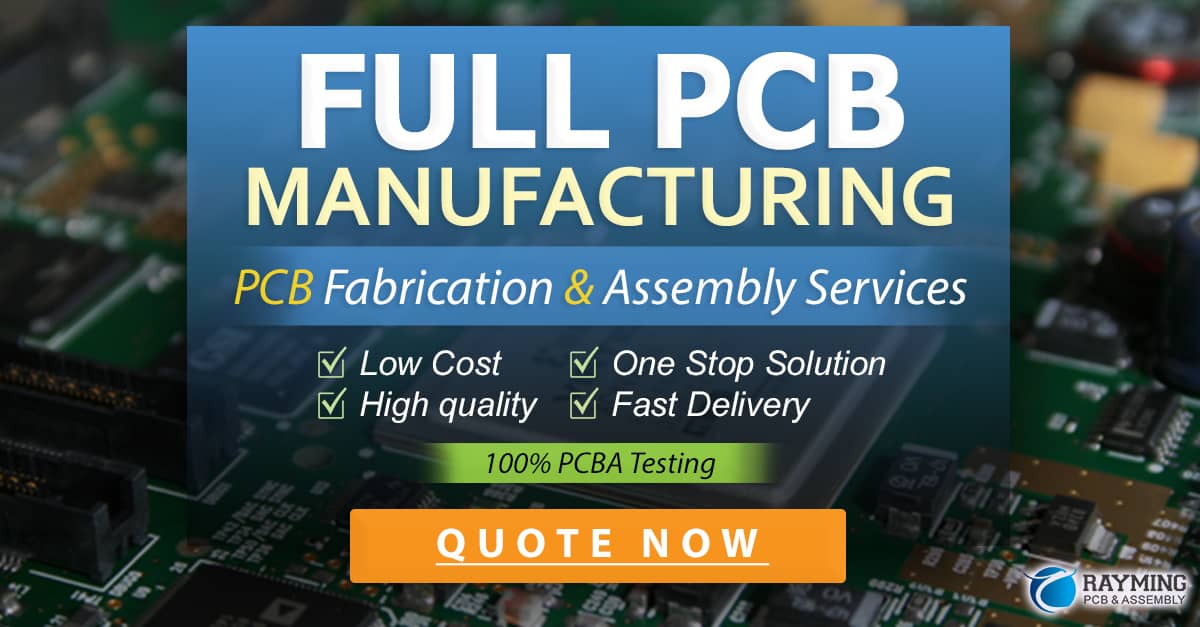
Choosing the Right PCB Manufacturer
Selecting the right PCB manufacturer is crucial to ensure the success of your electronic products. Here are some key factors to consider when choosing a PCB manufacturer:
- Experience and Expertise: Look for a manufacturer with extensive experience in producing PCBs for your specific industry or application. They should have a proven track record of delivering high-quality products and possess the necessary technical expertise to address any challenges that may arise.
- Manufacturing Capabilities: Evaluate the manufacturer’s manufacturing capabilities, including their equipment, facilities, and production capacity. Ensure that they have the necessary technology and resources to handle your specific PCB requirements, such as multi-layer boards, high-density interconnects, or advanced surface finishes.
- Quality Management System: Choose a manufacturer with a robust quality management system in place. They should have well-defined quality control processes, regular audits, and a commitment to continuous improvement. Look for certifications like ISO 9001 or compliance with relevant industry standards.
- Customer References: Request references from the manufacturer’s existing customers, particularly those in industries similar to yours. Reach out to these references to gather feedback on the manufacturer’s quality, reliability, customer service, and overall experience.
- Communication and Responsiveness: Effective communication is essential for a successful partnership with your PCB manufacturer. Assess their responsiveness, clarity in communication, and willingness to address your concerns or questions. They should keep you informed about project progress, potential issues, and delivery timelines.
- Cost and Lead Time: While cost is an important consideration, it should not be the sole deciding factor. Strike a balance between competitive pricing and the manufacturer’s ability to deliver high-quality PCBs consistently. Also, consider their lead times and whether they can meet your production schedule without compromising quality.
Frequently Asked Questions (FAQ)
- What is the difference between PCB Assembly and PCB manufacturing?
-
PCB manufacturing refers to the process of fabricating the bare PCB substrate, including etching, drilling, and plating. PCB assembly involves soldering components onto the manufactured PCB to create a functional electronic circuit.
-
How long does it typically take to manufacture a PCB?
-
The lead time for PCB manufacturing varies depending on the complexity of the design, the selected materials, and the manufacturer’s production capacity. Standard lead times range from a few days for simple, quick-turn prototypes to several weeks for complex, high-volume production runs.
-
What is the minimum order quantity (MOQ) for PCB manufacturing?
-
The MOQ for PCB manufacturing varies among manufacturers. Some offer low MOQs for prototyping and small-batch production, while others may require higher quantities for cost-effective manufacturing. It’s best to discuss your specific requirements with the manufacturer to determine their MOQ policies.
-
Can I provide my own design files for PCB manufacturing?
-
Yes, most PCB manufacturers accept customer-provided design files in various formats, such as Gerber files, ODB++, or IPC-2581. However, it’s important to ensure that your design files adhere to the manufacturer’s design guidelines and are properly formatted to avoid any issues during the manufacturing process.
-
How can I ensure the reliability and longevity of my PCBs?
- To ensure the reliability and longevity of your PCBs, consider the following:
- Choose high-quality materials that are suitable for your application and environment.
- Follow best practices for PCB design, including proper trace spacing, impedance control, and thermal management.
- Select a reputable PCB manufacturer with strict quality control processes and compliance with industry standards.
- Conduct thorough testing and validation of your PCBs, including environmental stress testing and accelerated life testing.
- Implement robust quality assurance measures throughout the manufacturing process, such as AOI, X-ray inspection, and electrical testing.
Conclusion
Determining the best PCB manufacturing for your electronic products requires careful consideration of various factors, including material selection, manufacturing processes, quality control, certifications, and customer support. By partnering with a reputable PCB manufacturer that demonstrates expertise, adherence to industry standards, and a commitment to quality, you can ensure the reliability, performance, and longevity of your PCBs.
When selecting a PCB manufacturer, evaluate their experience, manufacturing capabilities, quality management system, customer references, communication, and cost-effectiveness. A strong collaboration between you and your PCB manufacturer, along with open communication and a shared focus on quality, will lead to successful outcomes for your electronic products.
Remember, investing in high-quality PCB manufacturing is crucial for the success and competitiveness of your products in the market. By following the guidelines outlined in this article and working with a trusted PCB manufacturer, you can confidently navigate the complex world of PCB manufacturing and deliver exceptional electronic products to your customers.
Factor | Importance | Key Considerations |
---|---|---|
Material Selection | High | – Substrate material – Copper thickness – Solder mask quality |
Manufacturing Processes | High | – Etching precision – Drilling accuracy – Plating consistency – Lamination quality |
Quality Control and Testing | High | – Automated Optical Inspection (AOI) – X-ray inspection – Electrical testing – Functional testing |
Certifications and Standards Compliance | Medium to High | – ISO 9001 – IPC standards – UL certification |
Customer Support and Collaboration | High | – Design for Manufacturability (DFM) feedback – Prototyping and sampling – Technical support – Flexibility and customization |
By carefully evaluating these factors and selecting a PCB manufacturer that excels in each area, you can ensure that your PCB manufacturing is of the highest quality and best suited for your specific requirements.
0 Comments