Introduction to PCB Design
Printed Circuit Boards (PCBs) are essential components in modern electronics. They provide a platform for mounting and interconnecting electronic components, allowing for the creation of complex circuits in a compact and efficient manner. With the advent of online PCB design tools and services, it has become easier than ever for individuals and small businesses to create their own Custom PCBs.
In this article, we will explore the world of online PCB design, covering the basics of PCB design, the tools and resources available, and the steps involved in creating your own PCBs. Whether you’re a hobbyist, a student, or a professional, this guide will provide you with the knowledge and skills necessary to dive into the exciting field of PCB design.
What is a PCB?
A Printed Circuit Board (PCB) is a flat, insulating substrate that supports and connects electronic components using conductive pathways, tracks, or signal traces etched from copper sheets laminated onto the substrate. PCBs are used in virtually all electronic devices, from simple single-layer boards to complex multi-layer boards with thousands of components.
The main functions of a PCB include:
- Providing mechanical support for electronic components
- Electrically connecting components through conductive pathways
- Insulating components from one another to prevent short circuits
- Dissipating heat generated by components
Types of PCBs
PCBs can be classified based on various factors, such as the number of layers, the material used, and the manufacturing process. Some common types of PCBs include:
- Single-layer PCBs: These boards have conductive tracks on only one side of the substrate.
- Double-layer PCBs: These boards have conductive tracks on both sides of the substrate, allowing for more complex circuits and higher component density.
- Multi-layer PCBs: These boards have multiple layers of conductive tracks, separated by insulating layers. They are used for highly complex circuits and offer better signal integrity and EMI reduction.
- Flexible PCBs: These boards are made from flexible materials, allowing them to bend and conform to different shapes. They are often used in wearable devices and applications where space is limited.
- Rigid-flex PCBs: These boards combine rigid and flexible sections, providing the benefits of both types of PCBs in a single board.
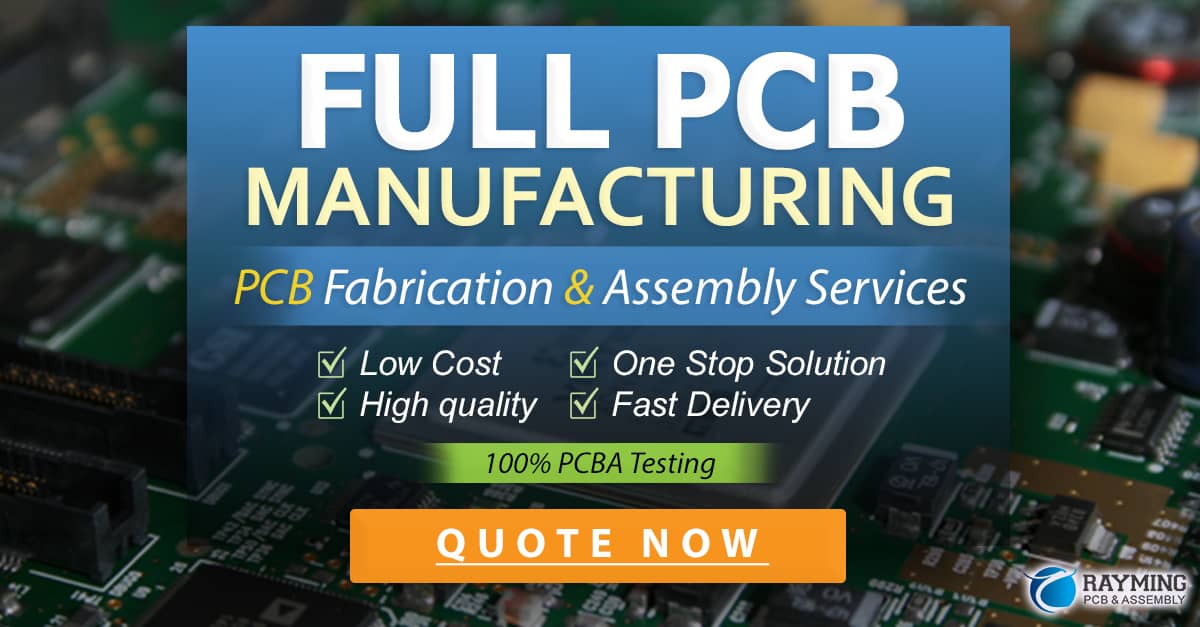
Advantages of Online PCB Design
Online PCB design offers several advantages over traditional methods:
- Accessibility: Online PCB design tools are available to anyone with an internet connection, making it easier for individuals and small businesses to create custom PCBs without investing in expensive software or hardware.
- Cost-effectiveness: Online PCB design services often offer competitive pricing, making it more affordable to prototype and manufacture PCBs in small quantities.
- Collaboration: Many online PCB design platforms allow for easy collaboration between team members, enabling remote work and streamlining the design process.
- Rapid prototyping: With online PCB design and manufacturing services, you can quickly iterate on your designs and receive prototypes in a matter of days, accelerating the development process.
Getting Started with Online PCB Design
To begin designing your own PCBs online, you’ll need to familiarize yourself with the basic concepts and tools involved in the process.
PCB Design Software
There are several online PCB design software options available, each with its own features and pricing models. Some popular choices include:
- EasyEDA: A free, web-based PCB design tool with a large component library and integrated manufacturing services.
- CircuitMaker: A free, community-driven PCB design platform with a focus on collaboration and open-source hardware.
- Upverter: A web-based PCB design tool with a user-friendly interface and built-in version control.
- PCBWeb Designer: A free, online PCB design tool with a simple interface and support for multi-layer boards.
When choosing a PCB design software, consider factors such as ease of use, feature set, component library, and integration with manufacturing services.
Component Libraries
A component library is a collection of pre-designed electronic components that can be used in your PCB designs. These libraries include schematic symbols, footprints, and 3D models for a wide range of components, such as resistors, capacitors, ICs, and connectors.
Most online PCB design software comes with built-in component libraries, but you can also create your own custom components or import libraries from third-party sources. Using a well-maintained component library can save time and ensure the accuracy of your designs.
Design Rules and Guidelines
To ensure that your PCBs are manufacturable and function as intended, it’s essential to follow a set of design rules and guidelines. These rules cover aspects such as:
- Minimum trace width and spacing
- Minimum drill hole size
- Clearance between components and traces
- Soldermask and silkscreen requirements
- Layer stackup and impedance control
Most online PCB design software includes built-in design rule checks (DRC) that help you identify and resolve any violations of these rules. Familiarizing yourself with the design rules specific to your chosen manufacturing service can help you create designs that are more likely to be successfully manufactured on the first attempt.
The PCB Design Process
The PCB design process typically involves the following steps:
- Schematic capture: Create a schematic diagram that represents the electrical connections between components in your circuit.
- Component placement: Arrange the components on the PCB layout, taking into account factors such as signal integrity, thermal management, and mechanical constraints.
- Routing: Create the conductive traces that connect the components according to the schematic diagram, following the design rules and guidelines.
- Design rule check: Run a DRC to ensure that your design complies with the manufacturing requirements and resolve any violations.
- Output files generation: Generate the necessary output files for manufacturing, such as Gerber files, drill files, and bill of materials (BOM).
Schematic Capture
Schematic capture involves creating a graphical representation of your circuit using schematic symbols. This step is crucial for defining the electrical connections between components and serves as a blueprint for the PCB layout.
When creating a schematic, consider the following best practices:
- Use a consistent naming convention for components and nets
- Group related components together for better organization
- Use hierarchical design techniques for complex circuits
- Annotate components with relevant information, such as values and part numbers
Component Placement
Component placement is the process of arranging the components on the PCB layout in a way that optimizes signal integrity, thermal management, and manufacturability. Some guidelines for component placement include:
- Place components in a logical order based on the signal flow
- Minimize the distance between connected components to reduce trace lengths
- Provide adequate spacing between components for heat dissipation and ease of assembly
- Consider the mechanical constraints of the enclosure or mounting system
Routing
Routing involves creating the conductive traces that connect the components according to the schematic diagram. When routing your PCB, keep the following tips in mind:
- Use the shortest possible trace lengths to minimize signal degradation and EMI
- Avoid sharp corners and use 45-degree angles for better signal integrity
- Provide adequate trace width for current-carrying capacity and impedance control
- Use ground planes and power planes to improve signal integrity and reduce EMI
- Follow the design rules and guidelines provided by your chosen manufacturing service
Design Rule Check
Running a design rule check (DRC) is essential for identifying and resolving any violations of the manufacturing requirements. Most online PCB design software includes built-in DRC tools that automatically check your design against a set of predefined rules.
Some common DRC checks include:
- Minimum trace width and spacing
- Minimum drill hole size
- Clearance between components and traces
- Soldermask and silkscreen requirements
- Layer stackup and impedance control
Resolving DRC violations may require adjusting your component placement, routing, or design parameters. It’s essential to iterate on your design until it passes all DRC checks to ensure successful manufacturing.
Output Files Generation
Once your design has passed the DRC, you’ll need to generate the necessary output files for manufacturing. The most common output files include:
- Gerber files: These files contain the layer-by-layer information for the PCB, including the copper layers, soldermask, and silkscreen.
- Drill files: These files contain information about the size and location of the drill holes on the PCB.
- Bill of Materials (BOM): This file lists all the components used in the design, along with their quantities, part numbers, and other relevant information.
Most online PCB design software can generate these files automatically, but it’s essential to review them for accuracy and completeness before submitting them for manufacturing.
PCB Manufacturing and Assembly
After generating the output files, you’ll need to choose a PCB manufacturing and assembly service to bring your design to life. Many online PCB design platforms, such as EasyEDA and CircuitMaker, offer integrated manufacturing services that streamline the process of ordering and receiving your PCBs.
When choosing a manufacturing service, consider factors such as:
- Cost: Compare the prices of different services based on the quantity, size, and complexity of your PCBs.
- Turnaround time: Consider how quickly you need your PCBs and choose a service that can meet your deadlines.
- Quality: Look for services with a reputation for producing high-quality PCBs and a low defect rate.
- Capabilities: Ensure that the service can accommodate your specific requirements, such as the number of layers, material type, and surface finish.
PCB Assembly
PCB assembly involves soldering the components onto the manufactured PCB. There are two main types of assembly:
- Through-hole assembly: Components with wire leads are inserted through holes in the PCB and soldered on the opposite side.
- Surface-mount assembly: Components are mounted directly onto the surface of the PCB and soldered using a reflow process.
Many PCB manufacturing services also offer assembly services, allowing you to receive a fully assembled and tested PCB. When choosing an assembly service, consider factors such as the component sourcing options, the level of quality control, and the testing and inspection procedures.
Troubleshooting and Testing
Once you’ve received your assembLED PCBs, it’s essential to test and troubleshoot them to ensure they function as intended. Some common issues that may arise include:
- Incorrect component placement or orientation
- Solder bridges or poor solder joints
- Damaged or missing components
- Incorrect trace connections or shorts
To troubleshoot your PCBs, you can use various tools and techniques, such as:
- Visual inspection: Carefully examine the PCB for any visible defects or anomalies.
- Multimeter: Use a multimeter to check for continuity, shorts, and proper component values.
- Oscilloscope: Use an oscilloscope to analyze signals and identify any issues with timing or waveforms.
- Functional testing: Perform end-to-end testing of your PCB to ensure it meets the desired specifications and performance requirements.
Keeping detailed records of your testing and troubleshooting process can help you identify and resolve issues more efficiently in future designs.
Advanced PCB Design Techniques
As you gain experience with PCB design, you may want to explore more advanced techniques to improve the performance, reliability, and manufacturability of your boards. Some advanced PCB design techniques include:
- High-speed design: Techniques for designing PCBs that can handle high-frequency signals, such as impedance matching, differential pairs, and length matching.
- EMI reduction: Strategies for minimizing electromagnetic interference, such as proper grounding, shielding, and filtering.
- Thermal management: Techniques for dissipating heat generated by components, such as using thermal vias, copper pours, and heatsinks.
- Design for manufacturing (DFM): Designing PCBs with manufacturability in mind, such as using standard component sizes, providing adequate spacing, and minimizing the number of unique parts.
- Embedded components: Integrating passive components, such as resistors and capacitors, directly into the PCB substrate to save space and improve performance.
Exploring these advanced techniques can help you create more sophisticated and optimized PCB designs that meet the demands of modern electronics.
Frequently Asked Questions (FAQ)
-
What is the difference between a schematic and a PCB layout?
A schematic is a graphical representation of the electrical connections between components, while a PCB layout is the physical arrangement of components and traces on the printed circuit board. -
Can I design a PCB without knowing how to code?
Yes, most online PCB design software offers graphical user interfaces that allow you to create designs without writing code. However, some advanced features may require scripting or programming knowledge. -
How do I choose the right PCB manufacturing service?
When choosing a PCB manufacturing service, consider factors such as cost, turnaround time, quality, and capabilities. Look for services with a reputation for producing high-quality PCBs and a low defect rate, and ensure they can accommodate your specific requirements. -
What are the most common PCB design mistakes to avoid?
Some common PCB design mistakes include violating design rules, using incorrect component footprints, neglecting thermal management, and failing to consider manufacturability. Following best practices and conducting thorough design reviews can help you avoid these mistakes. -
How can I learn more about advanced PCB design techniques?
To learn more about advanced PCB design techniques, you can explore online resources such as tutorials, webinars, and forums. Joining professional organizations, attending conferences, and collaborating with experienced designers can also help you expand your knowledge and skills.
Conclusion
Online PCB design has revolutionized the way individuals and small businesses create custom printed circuit boards. By leveraging web-based tools and services, anyone with an internet connection can design, prototype, and manufacture PCBs more efficiently and cost-effectively than ever before.
In this article, we’ve covered the basics of PCB design, including the types of PCBs, the advantages of online design, and the essential tools and concepts involved in the process. We’ve also explored the PCB design process, from schematic capture to output files generation, and discussed the importance of PCB manufacturing and assembly.
As you embark on your journey into the world of online PCB design, remember to start with simple designs, follow best practices and design rules, and continuously refine your skills through learning and experimentation. With dedication and practice, you can create sophisticated and reliable PCBs that power the next generation of electronic devices.
Resource | Description |
---|---|
EasyEDA | A free, web-based PCB design tool with integrated manufacturing services |
CircuitMaker | A free, community-driven PCB design platform focused on collaboration |
Upverter | A web-based PCB design tool with a user-friendly interface |
PCBWeb Designer | A free, online PCB design tool with support for multi-layer boards |
PCB Design Tutorial | A comprehensive guide to PCB design basics and best practices |
Advanced PCB Design Guide | An in-depth exploration of advanced PCB design techniques and considerations |
By leveraging these resources and the knowledge gained from this article, you’ll be well-equipped to start designing and manufacturing your own custom PCBs online. Happy designing!
0 Comments