What is a Circuit Board?
A circuit board, also known as a printed circuit board (PCB), is a flat plastic or fiberglass board that connects electronic components using conductive tracks, pads and other features. Circuit boards are foundational building blocks of most electronic devices and equipment. They mechanically support and electrically connect electronic components using conductive pathways or traces.
History of Circuit Boards
The origins of printed circuit boards go back to the early 20th century:
- In 1903, a German inventor named Albert Hanson filed a patent for flat foil conductors laminated to an insulating board.
- Thomas Edison experimented with chemical methods of plating conductors onto linen paper in 1904.
- In 1925, Charles Ducas filed a patent for a method of electroplating circuit patterns.
- Austrian engineer Paul Eisler manufactured the first operational printed circuit board in 1936 for a radio set.
- The transition from vacuum tubes to transistors in the 1950s revolutionized electronics and spurred the adoption of PCBs.
- The development of integrated circuits in 1958 further increased the density and complexity of components that could be placed on a circuit board.
Since then, PCBs have evolved from relatively simple single-layer boards to complex multi-layer boards that can be found in everything from smartphones to medical devices to aerospace equipment.
How are Circuit Boards Made?
The circuit board manufacturing process typically involves the following steps:
-
Design: The PCB design is created using Computer-Aided Design (CAD) software. This design blueprint specifies the layout of copper traces, component footprints, drill holes, etc.
-
Printing: The design is printed onto a transparent plastic sheet, known as a photo mask or photo tool.
-
Copper Lamination: A thin layer of copper foil is laminated onto the entire surface of the insulating substrate material, such as fiberglass.
-
Photoresist Application: The board is coated with a photoresist, a light-sensitive material.
-
Exposure: The photoresist is exposed to light through the photo mask. The areas exposed to light become soluble in a developing solution.
-
Developing: The board is submerged in a developing solution, which removes the photoresist from the exposed areas, leaving behind the desired copper pattern.
-
Etching: The board is placed in an etching solution, typically ferric chloride or ammonium persulfate, which eats away the copper not protected by the photoresist, leaving only the desired copper traces.
-
Stripping: The remaining photoresist is stripped off the board, revealing the copper traces.
-
Drilling: Holes are drilled through the board for through-hole components or to create vias for multi-layer boards.
-
Solder Mask Application: A solder mask, usually green, is applied over the copper layer to protect it from oxidation and to prevent solder bridges during assembly.
-
Silkscreen: White silkscreen ink is applied to add labels, logos, and identifiers for assembly and troubleshooting.
-
Surface Finish: A surface finish, such as HASL (Hot Air Solder Leveling), ENIG (Electroless Nickel Immersion Gold), or others, is applied to the exposed copper to prevent oxidation and enhance solderability.
-
Electrical Testing: The boards are electrically tested to ensure all connections are correct and there are no short circuits or open circuits.
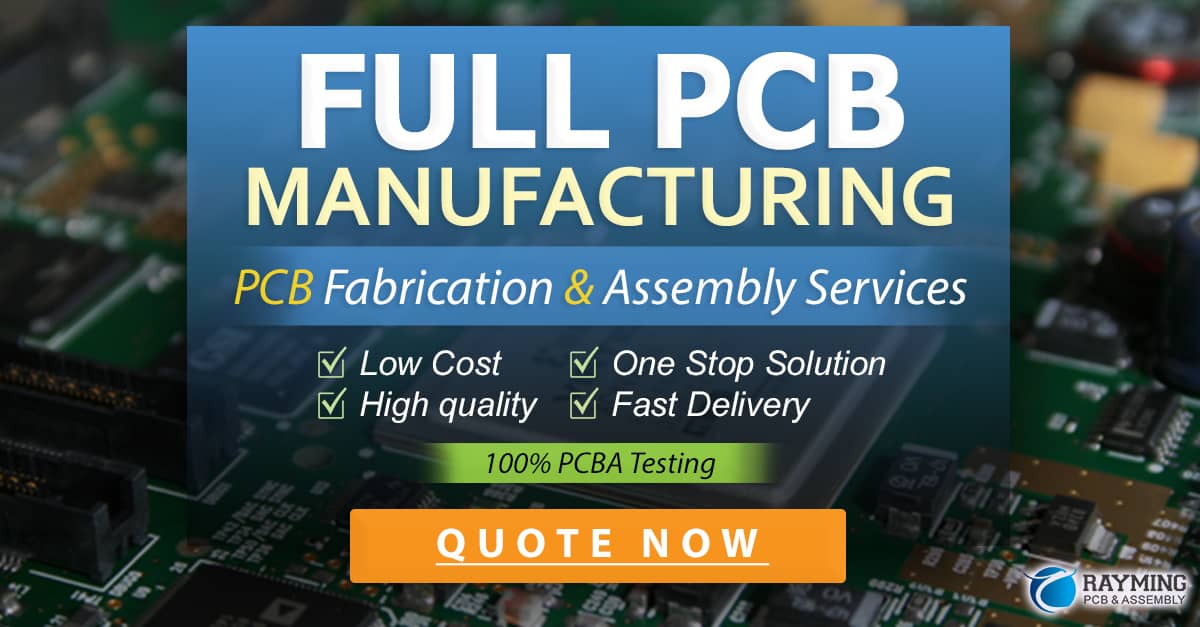
Types of Circuit Boards
There are several types of circuit boards, each with their own characteristics and applications:
Single-Layer PCBs
Single-layer or Single-sided PCBs have components and copper traces on one side of the board. They are the simplest and most inexpensive type of PCB.
Advantages:
– Low cost
– Easy to design and manufacture
– Suitable for simple circuits
Disadvantages:
– Limited routing density
– Larger board size compared to multi-layer boards
Applications:
– Simple electronics
– Low-power applications
– Prototypes and hobbyist projects
Double-Layer PCBs
Double-layer or double-sided PCBs have components and copper traces on both sides of the board, allowing for a higher component density and more complex circuitry compared to single-layer boards.
Advantages:
– Increased routing density compared to single-layer boards
– Smaller board size compared to single-layer boards
– Allows for more complex circuits
Disadvantages:
– Higher cost than single-layer boards
– More complex to design and manufacture
Applications:
– Power supplies
– Amplifiers
– Automotive electronics
– Industrial controls
Multi-Layer PCBs
Multi-layer PCBs have copper traces on multiple layers, separated by insulating layers. They can have anywhere from 4 to over 100 layers.
Advantages:
– High routing density
– Compact board size
– Allows for very complex circuits
– Better signal integrity and EMI performance
Disadvantages:
– Higher cost than single and double-layer boards
– Complex to design and manufacture
– Longer lead times
Applications:
– Smartphones and tablets
– Computers and servers
– Medical devices
– Aerospace and military electronics
Flexible PCBs
Flexible PCBs are made with a flexible substrate material, allowing the board to bend and conform to different shapes.
Advantages:
– Can bend and flex to fit in tight spaces
– Lighter and more durable than rigid boards
– Can replace multiple rigid boards and connectors
Disadvantages:
– Higher cost than rigid boards
– More complex to design and manufacture
– Limited component options
Applications:
– Wearable electronics
– Medical implants
– Aerospace and military equipment
– Automotive electronics
Rigid-Flex PCBs
Rigid-Flex PCBs are a combination of rigid and flexible PCBs, with rigid sections for mounting components and flexible sections for interconnections.
Advantages:
– Combines benefits of rigid and flexible boards
– Can replace multiple rigid boards and connectors
– Allows for 3D packaging of electronics
Disadvantages:
– Higher cost than rigid boards
– Complex to design and manufacture
– Limited flex cycles compared to fully flexible boards
Applications:
– Aerospace and military equipment
– Medical devices
– Industrial controls
– High-end consumer electronics
Circuit Board Design Considerations
Designing a circuit board involves several key considerations:
Schematic Design
The first step is creating a schematic diagram, which is a graphical representation of the electrical connections and components in the circuit. This is typically done using Electronic Design Automation (EDA) software.
Component Selection
Components are selected based on the functional and performance requirements of the circuit. Key factors include:
– Electrical ratings (voltage, current, power)
– Package type and size
– Availability and cost
– Reliability and quality
Board Size and Shape
The size and shape of the board are determined by the space constraints of the enclosure and the arrangement of components. The board shape can be rectangular, circular, or a custom shape.
Layer Stack-up
For multi-layer boards, the layer stack-up defines the number, order, and thickness of copper and insulating layers. The stack-up affects signal integrity, power distribution, and EMI performance.
Routing and Placement
Components are placed on the board and interconnected by copper traces. Key considerations include:
– Signal integrity
– Power integrity
– Electromagnetic compatibility (EMC)
– Manufacturing constraints (minimum trace width and spacing, hole sizes, etc.)
Power and Ground Planes
Solid copper planes are used for power distribution and grounding. They provide low-impedance paths for power and return currents and help with signal integrity and EMI.
Testing and Validation
The design is simulated and tested to verify functionality, performance, and reliability. This includes:
– Electrical rule checks (ERC)
– Design rule checks (DRC)
– Signal integrity simulations
– Thermal analysis
– EMC analysis
PCB Assembly Process
After the circuit board is manufactured, it needs to be populated with components. The assembly process typically involves the following steps:
-
Solder Paste Application: Solder paste, a mixture of tiny solder particles and flux, is applied to the pads on the board using a stencil or screen printing process.
-
Component Placement: Components are placed onto the board, either manually or using automated pick-and-place machines. Surface mount components are placed directly onto the solder paste, while through-hole components are inserted into drilled holes.
-
Reflow Soldering: The board is heated in a reflow oven, causing the solder paste to melt and form a permanent electrical and mechanical connection between the components and the board.
-
Inspection: The assembled board is visually inspected for defects such as misaligned components, solder bridges, or missing solder joints. Automated optical inspection (AOI) systems are often used for this purpose.
-
Testing: The board is electrically tested to ensure proper functionality. This can include in-circuit testing (ICT), boundary scan testing, or functional testing.
-
Rework and Repair: Any defects found during inspection or testing are repaired, which may involve removing and replacing components or adding missing solder.
-
Conformal Coating: A protective coating may be applied to the board to protect it from moisture, dust, and other environmental factors.
-
Final Assembly: The board is integrated into the final product or enclosure.
Frequently Asked Questions (FAQ)
1. What is the difference between a printed circuit board (PCB) and a circuit board?
A printed circuit board (PCB) is a specific type of circuit board where the conductive pathways are printed or etched onto the board material. The term “circuit board” can refer to any type of board that interconnects electronic components, including breadboards, stripboards, and PCBs. In practice, however, the terms “PCB” and “circuit board” are often used interchangeably.
2. What materials are circuit boards made of?
The most common base material for rigid circuit boards is FR-4, a composite material made of woven fiberglass cloth with an epoxy resin binder. Other base materials include:
– G-10: A fiberglass-based material with better mechanical properties than FR-4
– CEM-1 and CEM-3: Composite epoxy materials with a mixture of woven glass and paper reinforcement
– Polyimide: A high-temperature material used in aerospace and military applications
– Aluminum: Used for metal-Core PCBs for high-power LED lighting and automotive applications
Flexible circuit boards are made with flexible polymer films such as polyimide or polyester.
The conductive material is typically copper, although other metals like aluminum or silver can be used for specialized applications.
3. What are vias in a circuit board?
Vias are conductive holes that allow electrical connections between different layers of a multi-layer circuit board. There are several types of vias:
– Through vias: Go through the entire thickness of the board
– Blind vias: Start on an outer layer and terminate on an inner layer
– Buried vias: Connect inner layers without reaching the outer layers
– Micro vias: Very small vias (typically less than 150 microns in diameter) used in high-density interconnect (HDI) boards
4. What is the solder mask on a circuit board?
The solder mask is a protective coating applied to the copper traces on a circuit board. It serves several purposes:
– Protects the copper from oxidation and corrosion
– Insulates the traces from accidental short circuits
– Prevents solder from bridging between closely spaced pads
– Provides a smooth, non-conductive surface for silkscreen printing
The most common color for solder mask is green, but other colors like blue, red, yellow, black, and white are also used.
5. How do I choose the right type of circuit board for my project?
The choice of circuit board type depends on several factors:
– Complexity of the circuit
– Space constraints
– Environmental conditions (temperature, humidity, vibration, etc.)
– Power requirements
– Signal integrity and EMI considerations
– Cost and volume
Here are some general guidelines:
– Single-layer boards are suitable for simple, low-power circuits and prototypes.
– Double-layer boards are a good choice for medium-complexity circuits and low-volume production.
– Multi-layer boards are necessary for complex, high-speed circuits and high-volume production.
– Flexible boards are used when the circuit needs to bend or flex, or to save space by replacing multiple rigid boards and connectors.
– Rigid-flex boards offer a combination of rigid and flexible sections for 3D packaging and complex assemblies.
It’s always a good idea to consult with a PCB design engineer or manufacturer to determine the best option for your specific application.
Conclusion
Circuit boards are the backbone of modern electronics, enabling the interconnection and packaging of complex electronic systems. Understanding the types, manufacturing processes, design considerations, and assembly techniques is essential for anyone involved in electronics design or manufacturing.
As electronic devices continue to become smaller, faster, and more powerful, circuit board technology will continue to evolve to meet these challenges. Advances in materials, manufacturing processes, and design tools will enable even more complex and compact electronic systems in the future.
By mastering the fundamentals of circuit boards, you can unlock the potential to create innovative electronic products that solve real-world problems and push the boundaries of what’s possible.
0 Comments