Understanding the Differences Between HDI and PCB
When it comes to printed circuit boards (PCBs), there are two main types: High Density Interconnect (HDI) and regular PCBs. While both serve the purpose of connecting electronic components, there are significant differences between the two that can impact the performance, cost, and manufacturability of your product. In this article, we’ll explore the key distinctions between HDI and regular PCBs, and provide guidance on how to determine which type is best suited for your specific application.
What is a Regular PCB?
A regular PCB, also known as a conventional PCB, is a printed circuit board that consists of a flat insulating substrate with conductive traces, pads, and vias. These boards are typically made of FR-4, a glass-reinforced epoxy laminate material, and feature copper traces that are etched onto the surface to create the desired electrical connections.
Regular PCBs can be single-sided, double-sided, or multi-layered, depending on the complexity of the circuit design. They are commonly used in a wide range of electronic devices, from simple consumer products to industrial equipment and automotive applications.
What is an HDI PCB?
HDI PCBs, on the other hand, are a more advanced type of printed circuit board that offers higher density and performance compared to regular PCBs. These boards feature finer trace widths, smaller vias, and higher layer counts, allowing for more complex and compact designs.
The key characteristics of HDI PCBs include:
- Microvia technology: HDI boards utilize microvias, which are small, laser-drilled holes that connect the inner layers of the PCB. This enables higher density interconnections and reduces the overall size of the board.
- Blind and buried vias: Unlike regular PCBs, which typically only have through-hole vias, HDI boards can incorporate blind (connecting an outer layer to an inner layer) and buried (connecting inner layers only) vias. This further increases the routing density and flexibility of the design.
- Thinner dielectrics: HDI PCBs use thinner dielectric materials between layers, allowing for more layers to be stacked within the same overall thickness.
- Finer pitch components: The higher density of HDI boards enables the use of smaller components with finer pitch, such as Ball Grid Arrays (BGAs) and Chip Scale Packages (CSPs).
HDI PCBs are commonly used in applications that require high performance, miniaturization, and reliability, such as smartphones, tablets, wearables, and medical devices.
Key Differences Between HDI and Regular PCBs
To help you determine whether your product requires an HDI or a regular PCB, let’s explore the key differences between the two in more detail.
Density and Size
One of the most significant differences between HDI and regular PCBs is the density of the interconnections and the overall size of the board. HDI PCBs can accommodate much higher densities, thanks to their use of microvias, blind/buried vias, and finer trace widths.
Parameter | Regular PCB | HDI PCB |
---|---|---|
Trace width | ≥ 0.1 mm | ≥ 0.05 mm |
Via diameter | ≥ 0.3 mm | ≥ 0.1 mm |
Via pitch | ≥ 0.8 mm | ≥ 0.4 mm |
Layer count | Typically ≤ 16 | Can exceed 24 |
As a result, HDI PCBs can be much smaller than regular PCBs for the same functionality, making them ideal for space-constrained applications like mobile devices and wearables.
Performance and Signal Integrity
HDI PCBs offer superior performance and signal integrity compared to regular PCBs. The shorter interconnections and reduced parasitic capacitance and inductance of microvias and fine-pitch traces lead to improved signal quality, reduced crosstalk, and better high-frequency performance.
Additionally, the ability to place components closer together on an HDI board reduces the overall signal path length, further enhancing signal integrity and reducing electromagnetic interference (EMI).
Cost and Manufacturability
While HDI PCBs offer numerous benefits in terms of density, size, and performance, they also come with higher manufacturing costs and complexity compared to regular PCBs. The advanced technologies and processes required for HDI fabrication, such as laser drilling, sequential lamination, and high-precision alignment, contribute to the increased cost.
However, it’s important to consider the total cost of ownership when comparing HDI and regular PCBs. In many cases, the miniaturization and performance advantages of HDI can lead to overall cost savings at the system level, by reducing the number of components, simplifying assembly, and improving reliability.
Manufacturability is another factor to consider when choosing between HDI and regular PCBs. HDI boards typically require more advanced fabrication capabilities and tighter process controls, which may limit the number of suppliers capable of producing them. It’s essential to work closely with your PCB manufacturer to ensure they have the necessary expertise and equipment to meet your HDI requirements.
Determining Your Product’s PCB Requirements
Now that we’ve explored the differences between HDI and regular PCBs, let’s discuss how to determine which type is best suited for your product. Consider the following factors:
-
Size and density: If your product requires a high degree of miniaturization or has a large number of components in a small space, HDI is likely the better choice.
-
Performance requirements: If your design demands high signal integrity, low EMI, or excellent high-frequency performance, HDI’s superior electrical characteristics may be necessary.
-
Cost constraints: Regular PCBs are generally more cost-effective than HDI boards, particularly for simpler designs or larger production volumes. However, consider the total cost of ownership, including assembly and system-level costs.
-
Reliability and environment: HDI PCBs can offer improved reliability due to their reduced size and interconnect lengths. If your product will be exposed to harsh environments or requires high reliability, HDI may be the preferred option.
-
Time-to-market: HDI PCBs may have longer lead times and require more complex design and fabrication processes. If your project has tight deadlines, a regular PCB might be a more suitable choice.
Ultimately, the decision between HDI and regular PCBs should be based on a careful analysis of your product’s specific requirements, balancing performance, cost, and manufacturability factors.
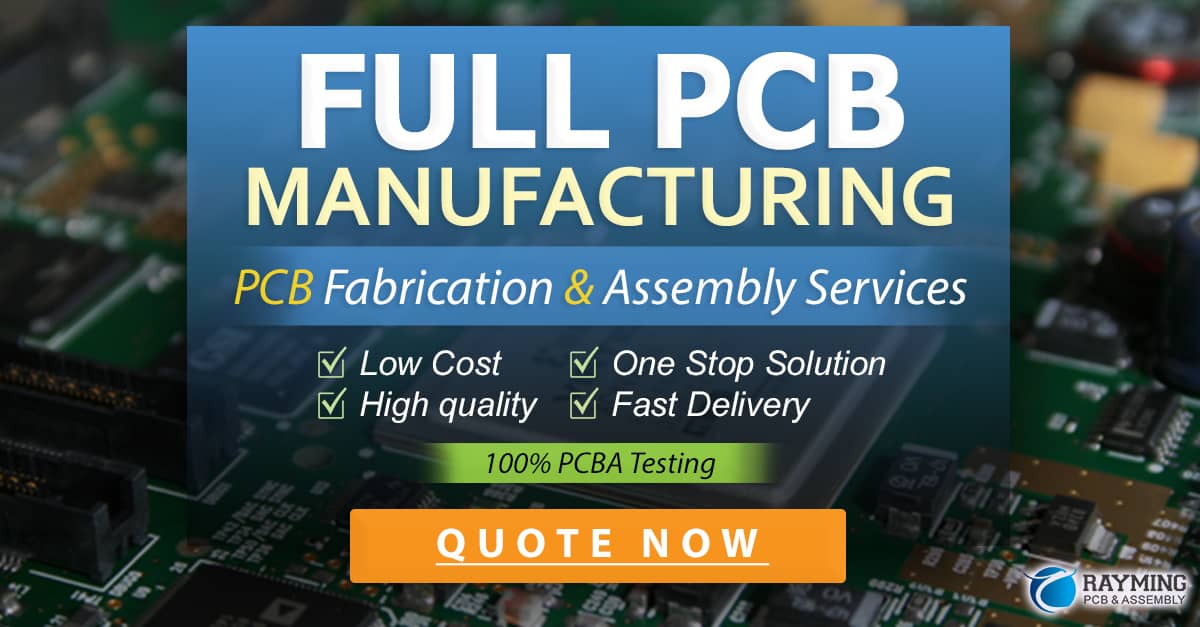
FAQ
- Q: Can I combine HDI and regular PCB technologies in the same design?
A: Yes, it’s possible to use a hybrid approach, incorporating HDI features in specific areas of a regular PCB where higher density or performance is required. This can help balance cost and performance while still benefiting from HDI’s advantages.
- Q: Are there any limitations on the number of layers in an HDI PCB?
A: While HDI PCBs can support a higher number of layers compared to regular PCBs, there are practical limitations based on the fabrication capabilities of the manufacturer. Most HDI PCBs have between 8 and 24 layers, but some advanced designs can exceed 30 layers.
- Q: How do I choose the right PCB manufacturer for my HDI project?
A: When selecting a PCB manufacturer for an HDI project, look for companies with extensive experience in HDI fabrication, advanced equipment, and strict process controls. Request references, samples, and quality certifications to ensure they can meet your specific requirements.
- Q: Are there any special design considerations for HDI PCBs?
A: Yes, designing HDI PCBs requires a thorough understanding of the specific design rules and constraints associated with the technology. This includes considerations for via sizes, pad sizes, trace widths, and clearances. It’s essential to work closely with your PCB manufacturer and follow their HDI design guidelines to ensure a successful outcome.
- Q: How do I decide between an HDI PCB and a regular PCB for my product?
A: The choice between an HDI PCB and a regular PCB depends on your product’s specific requirements for size, performance, cost, and reliability. Consider factors such as the number and density of components, signal integrity needs, environmental conditions, and production volume when making your decision. If your design demands high density, superior performance, and reliability in a compact form factor, HDI is likely the better choice. However, if your requirements are less stringent and cost is a primary concern, a regular PCB may be sufficient.
Conclusion
Choosing between an HDI PCB and a regular PCB is a critical decision that can significantly impact the performance, cost, and manufacturability of your electronic product. By understanding the key differences between the two technologies and carefully evaluating your specific requirements, you can make an informed choice that balances the benefits and trade-offs of each approach.
HDI PCBs offer unparalleled density, performance, and miniaturization, making them an ideal choice for cutting-edge applications in industries like consumer electronics, telecommunications, and medical devices. However, they also come with higher costs and complexity compared to regular PCBs.
Regular PCBs, on the other hand, provide a cost-effective solution for a wide range of electronic products, from simple consumer goods to industrial equipment. While they may not offer the same level of density or performance as HDI boards, they are easier to design and manufacture, and can still meet the requirements of many applications.
Ultimately, the key to successful PCB selection is a thorough understanding of your product’s needs and a close collaboration with your PCB manufacturer. By leveraging their expertise and carefully weighing the factors discussed in this article, you can make the right choice between HDI and regular PCBs, ensuring your product’s success in the marketplace.
0 Comments