What is a PCB and Why are Blank PCBs Useful?
A Printed Circuit Board, or PCB, is the foundation that allows electronic components to be connected together to create a functional electronic device or system. PCBs provide the conductive pathways, through copper traces, to electrically connect the various components.
Blank PCBs are circuit boards that have the copper traces and pads already etched on but do not have any components soldered to them yet. They provide a convenient starting point for hobbyists, engineers, and manufacturers to quickly prototype and produce custom electronic devices.
Some key advantages of blank PCBs include:
- Cost-effective for low-volume production and prototyping
- Faster turnaround time compared to custom manufactured boards
- Ability to hand-solder components for more control
- Modular design allows for easy modifications and troubleshooting
Types of Blank PCBs
Blank PCBs come in a variety of materials, sizes, and specifications to suit different project requirements. Here are some of the most common types:
FR-4 PCBs
FR-4 (Flame Retardant 4) is the most widely used material for PCBs. It is a glass-reinforced epoxy laminate that provides good electrical insulation properties and mechanical strength. FR-4 is suitable for a wide range of applications and is the go-to choice for most PCB projects.
Aluminum PCBs
Aluminum PCBs have an aluminum substrate that provides excellent thermal conductivity, making them ideal for high-power applications that generate a lot of heat. They are commonly used in LED lighting, power electronics, and automotive applications.
Flexible PCBs
Flexible PCBs are made from thin, flexible materials like polyimide or PEEK. They can bend and conform to different shapes, making them suitable for applications where space is limited or the PCB needs to flex during operation. Flexible PCBs are often used in wearable electronics, medical devices, and aerospace applications.
High Frequency PCBs
High frequency PCBs are designed to handle high-speed signals and minimize signal loss and interference. They use low-loss dielectric materials like Rogers or Teflon and have controlled impedance traces. High frequency PCBs are used in RF and microwave applications, high-speed digital circuits, and telecommunications equipment.
Choosing the Right Blank PCB
When selecting a blank PCB for your project, there are several factors to consider:
-
Size and Shape: Choose a PCB size that fits your enclosure and accommodates all your components. Consider any mounting holes or cutouts that may be required.
-
Number of Layers: Determine how many copper layers your design requires. Simple designs can use single or double-sided PCBs, while more complex designs may require multi-layer boards.
-
Material: Select the appropriate PCB material based on your application requirements, such as temperature range, mechanical strength, and electrical properties.
-
Copper Thickness: Choose the appropriate copper thickness for your traces based on the current-carrying requirements of your circuit. Thicker copper allows for higher current capacity but may be more expensive.
-
Surface Finish: Consider the type of surface finish required for your components and soldering process. Common finishes include HASL (Hot Air Solder Leveling), lead-free HASL, immersion silver, and gold plating.
Here is a comparison table of some common blank PCB Options:
PCB Type | Material | Layers | Typical Applications |
---|---|---|---|
FR-4 | Epoxy-glass | 1-16 | General purpose |
Aluminum | Aluminum | 1-2 | High-power, LED |
Flexible | Polyimide | 1-6 | Wearables, medical |
High Frequency | Rogers, Teflon | 1-32 | RF, high-speed digital |
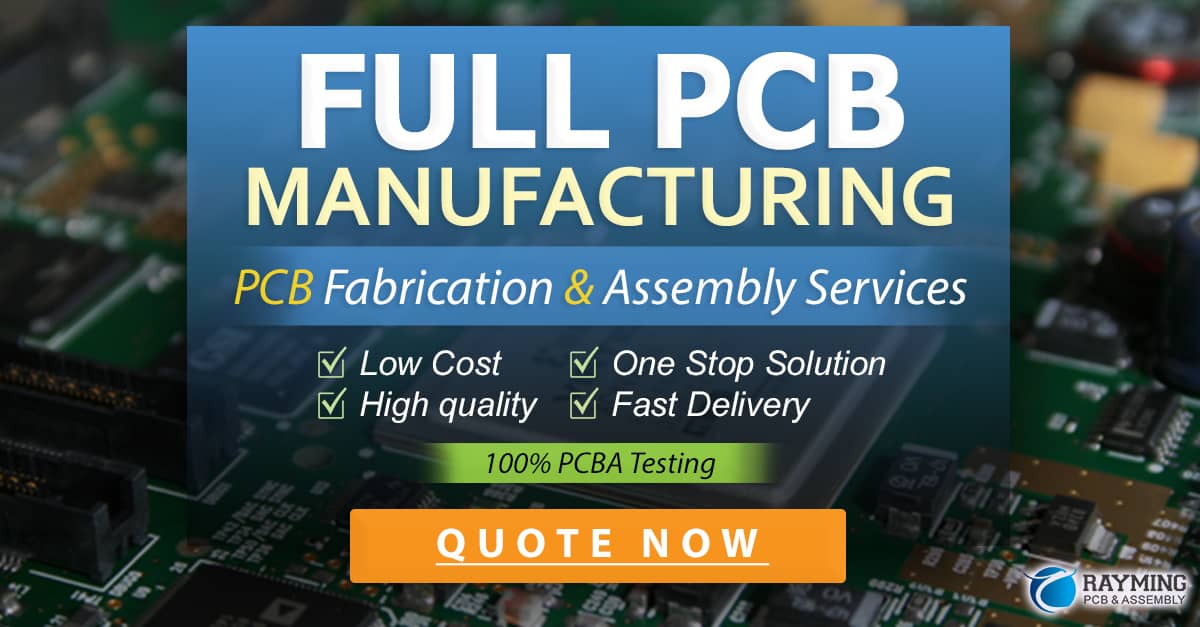
Designing Your PCB
Once you have selected your blank PCB, the next step is to design your circuit and layout the components on the board. Here are the basic steps involved in PCB design:
-
Schematic Capture: Create a schematic diagram of your circuit using EDA (Electronic Design Automation) software. This involves placing the component symbols and connecting them with wires to define the electrical connections.
-
Component Placement: Arrange the physical components on the PCB layout, taking into account factors like signal integrity, thermal management, and manufacturability. Use the schematic as a reference to ensure the correct connections are made.
-
Routing: Create the copper traces that connect the components according to the schematic. Consider factors like trace width, spacing, and length to minimize signal integrity issues and ensure manufacturability.
-
Design Rule Check (DRC): Run a DRC to verify that your PCB layout meets the manufacturing requirements and design rules specified by your PCB fabricator. This helps to catch any potential issues before sending the design for manufacturing.
-
Gerber File Generation: Export your PCB layout as a set of Gerber files, which are the industry-standard format for PCB manufacturing. These files contain the information needed to fabricate the PCB, including the copper layers, drill holes, and silkscreen.
Assembling Your PCB
Once you have your blank PCB and components, you can start the assembly process. Here are the basic steps involved:
-
Solder Paste Application: Apply solder paste to the pads on the PCB using a stencil or syringe. Solder paste is a mixture of tiny solder spheres and flux that helps the components adhere to the pads during soldering.
-
Component Placement: Place the components onto the pads on the PCB, ensuring correct orientation and alignment. You can use tweezers or a pick-and-place machine for more precise placement.
-
Reflow Soldering: Place the PCB with components into a reflow oven, which heats up the board to melt the solder paste and form a permanent connection between the components and the pads. The reflow profile depends on the type of solder paste and components used.
-
Inspection and Rework: Visually inspect the soldered joints for any defects or misalignments. Use a multimeter or oscilloscope to test the functionality of the assembled board. If any issues are found, perform rework by desoldering and resoldering the affected components.
Frequently Asked Questions (FAQ)
1. What is the difference between a blank PCB and a finished PCB?
A: A blank PCB is a circuit board that has the copper traces and pads etched but does not have any components soldered onto it. A finished PCB, on the other hand, has all the components soldered and is ready for use in the final application.
2. Can I use a blank PCB for any electronic project?
A: Blank PCBs are versatile and can be used for a wide range of electronic projects, from simple circuits to complex devices. However, you need to ensure that the PCB specifications (size, material, layers, etc.) match your project requirements.
3. How do I choose the right copper thickness for my PCB?
A: The copper thickness depends on the current-carrying requirements of your circuit. Thicker copper allows for higher current capacity but may be more expensive. Generally, 1 oz copper (35 μm) is sufficient for most low-power applications, while 2 oz copper (70 μm) or more may be needed for high-power applications.
4. What is the typical turnaround time for blank PCBs?
A: The turnaround time for blank PCBs varies depending on the supplier and the PCB specifications. Some suppliers offer quick-turn services with turnaround times as short as 24 hours, while others may take several days or weeks. It’s best to check with your supplier for their specific lead times.
5. Can I hand-solder components onto a blank PCB?
A: Yes, blank PCBs are designed to be hand-solderable. However, for more complex designs or higher volumes, using reflow soldering or Wave Soldering may be more efficient and reliable.
Conclusion
Blank PCBs are a convenient and cost-effective solution for prototyping and low-volume production of electronic devices. They provide a pre-made foundation that allows engineers and hobbyists to quickly assemble and test their designs.
When selecting a blank PCB, it’s important to consider factors like size, material, layers, and copper thickness to ensure it meets your project requirements. Proper PCB design and assembly techniques are also crucial for ensuring the functionality and reliability of the final product.
As technology continues to advance, the demand for custom electronic devices will only grow, and blank PCBs will continue to play a vital role in enabling innovation and rapid prototyping. Whether you’re a seasoned engineer or a beginner hobbyist, blank PCBs offer a powerful tool for bringing your electronic ideas to life.
0 Comments