Introduction to PCB Temperature Management
Printed Circuit Boards (PCBs) are the backbone of modern electronics, found in everything from smartphones and laptops to industrial control systems and aerospace applications. As electronic devices become more compact and powerful, managing the temperature of PCBs has become increasingly important. High temperatures can lead to reduced performance, decreased reliability, and even complete failure of electronic components.
In this comprehensive guide, we’ll explore the fundamentals of PCB temperature management, including the causes of high temperatures, the effects on electronic components, and strategies for managing and mitigating heat. We’ll also discuss the importance of thermal design in PCB layout and the role of thermal simulation software in optimizing PCB Performance.
Causes of High PCB Temperatures
Several factors can contribute to high temperatures on PCBs:
Power Dissipation
Electronic components, such as processors, resistors, and transistors, generate heat as they consume power. The more power a component consumes, the more heat it will generate. In high-performance applications, such as gaming computers or data centers, power dissipation can be a significant source of heat.
High Ambient Temperatures
PCBs may be exposed to high ambient temperatures in certain environments, such as industrial settings or outdoor applications. When the surrounding air temperature is high, it becomes more difficult for the PCB to dissipate heat, leading to increased component temperatures.
Inadequate Cooling
If a PCB lacks sufficient cooling mechanisms, such as heatsinks, fans, or ventilation, heat can build up quickly. This is particularly problematic in compact devices where space is limited, and air circulation is restricted.
Poor Thermal Design
Suboptimal PCB layout and design can contribute to high temperatures. For example, placing heat-generating components too close together or failing to provide adequate thermal paths can lead to localized hot spots on the board.
Effects of High PCB Temperatures
High temperatures can have several detrimental effects on PCBs and their components:
Reduced Performance
As the temperature of electronic components increases, their performance may degrade. For example, high temperatures can cause processors to throttle their clock speeds to prevent overheating, resulting in slower system performance.
Decreased Reliability
Exposure to high temperatures can accelerate the aging process of electronic components, leading to a shorter lifespan and increased failure rates. This is particularly concerning in mission-critical applications where reliability is paramount.
Component Damage
In extreme cases, high temperatures can cause permanent damage to electronic components. This can include melting of solder joints, delamination of PCB Layers, and even complete component failure.
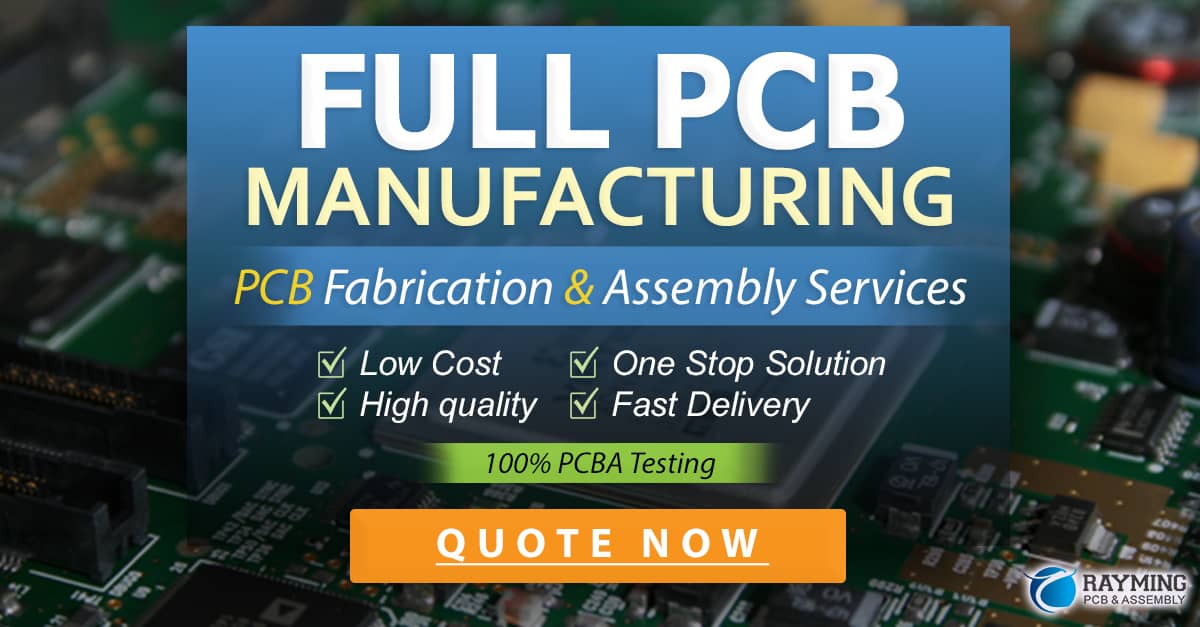
Strategies for Managing PCB Temperatures
To mitigate the effects of high temperatures on PCBs, several strategies can be employed:
Heatsinks and Cooling Fans
Heatsinks are passive cooling devices that help dissipate heat from electronic components. They work by providing a larger surface area for heat to be conducted away from the component and into the surrounding air. Cooling fans can be used in conjunction with heatsinks to actively move air across the PCB, enhancing heat dissipation.
Thermal Interface Materials
Thermal interface materials (TIMs), such as thermal paste or thermal pads, are used to improve the thermal conductivity between electronic components and heatsinks. By filling in the microscopic air gaps between the surfaces, TIMs help facilitate better heat transfer.
PCB Layout Optimization
Careful consideration of PCB layout can help manage temperatures. This includes:
- Placing heat-generating components strategically to minimize thermal interactions
- Providing adequate spacing between components to allow for air circulation
- Using thermal vias to conduct heat through the PCB layers
- Incorporating copper pours or heat spreaders to distribute heat evenly across the board
Thermal Simulation Software
Thermal simulation software, such as ANSYS Icepak or Mentor Graphics FloTHERM, can be used to model and analyze the thermal behavior of PCBs. These tools allow designers to identify potential hot spots, evaluate the effectiveness of cooling solutions, and optimize the PCB layout for better thermal performance.
Thermal Design Considerations in PCB Layout
When designing a PCB with thermal management in mind, several key considerations should be taken into account:
Component Placement
Heat-generating components should be placed strategically to minimize thermal interactions and allow for adequate cooling. For example, placing high-power components near the edge of the board can help facilitate heat dissipation through convection.
Thermal Paths
Providing low-resistance thermal paths from heat-generating components to the PCB surface or heatsinks is crucial for effective heat dissipation. This can be achieved through the use of thermal vias, which are small holes filled with conductive material that transfer heat through the PCB layers.
Copper Pours and Heat Spreaders
Incorporating copper pours or heat spreaders in the PCB layout can help distribute heat more evenly across the board. Copper pours are large areas of copper that act as heat sinks, while heat spreaders are dedicated layers within the PCB that conduct heat laterally.
Airflow and Ventilation
Adequate airflow and ventilation are essential for effective cooling. When designing enclosures or casings for PCBs, it’s important to provide sufficient openings for air intake and exhaust. In some cases, forced air cooling using fans may be necessary to maintain acceptable temperatures.
Thermal Simulation and Analysis
Thermal simulation software plays a crucial role in optimizing PCB thermal performance. These tools allow designers to:
- Model the thermal behavior of PCBs and components
- Identify potential hot spots and thermal bottlenecks
- Evaluate the effectiveness of cooling solutions, such as heatsinks and fans
- Optimize component placement and PCB layout for better heat dissipation
By using thermal simulation early in the design process, designers can make informed decisions and avoid costly redesigns later on.
Thermal Simulation Workflow
A typical thermal simulation workflow involves the following steps:
-
Import PCB Design: The PCB layout is imported into the thermal simulation software, including component placement, copper layers, and any existing cooling solutions.
-
Define Boundary Conditions: Boundary conditions, such as ambient temperature, airflow, and power dissipation of components, are specified to reflect the intended operating environment.
-
Mesh Generation: The PCB model is divided into small elements or cells, forming a mesh that allows for numerical analysis of the thermal behavior.
-
Solve Thermal Equations: The software solves the governing thermal equations, taking into account the boundary conditions and material properties, to determine the temperature distribution across the PCB.
-
Post-Processing and Visualization: The simulation results are visualized using color plots, temperature contours, and flow vectors, allowing designers to identify hot spots and evaluate the effectiveness of cooling solutions.
-
Optimization and Iteration: Based on the simulation results, the PCB layout and cooling solutions can be optimized iteratively until the desired thermal performance is achieved.
Thermal Simulation Software | Key Features |
---|---|
ANSYS Icepak | – Comprehensive thermal analysis for electronic systems – Supports both component-level and system-level modeling – Integrates with ANSYS Mechanical for structural analysis |
Mentor Graphics FloTHERM | – Specialized thermal simulation for electronics cooling – Intuitive user interface and workflow – Extensive library of component models and material properties |
Siemens Simcenter Flotherm | – Thermal simulation for electronic systems and PCBs – Advanced meshing capabilities for complex geometries – Parametric modeling for design optimization |
Autodesk Fusion 360 | – Integrated thermal simulation within a CAD environment – Supports both steady-state and transient thermal analysis – Cloud-based solving for faster simulation times |
Frequently Asked Questions (FAQ)
1. What is the ideal operating temperature range for electronic components?
The ideal operating temperature range for electronic components varies depending on the specific component and its intended application. However, most components are designed to operate reliably within the commercial temperature range of 0°C to 70°C (32°F to 158°F). Some components, such as automotive-grade or military-grade parts, may be rated for extended temperature ranges.
2. How can I measure the temperature of my PCB during operation?
There are several methods for measuring PCB temperature during operation:
- Thermocouples: These are small, inexpensive sensors that can be attached directly to the PCB or components to measure temperature.
- Infrared (IR) thermometers: Non-contact IR thermometers can be used to measure the surface temperature of PCBs and components from a distance.
- Thermal imaging cameras: These devices provide a visual representation of the temperature distribution across the PCB, allowing for easy identification of hot spots.
- Built-in temperature sensors: Some components, such as processors, have built-in temperature sensors that can be monitored through software.
3. What is the difference between passive and active cooling?
Passive cooling relies on natural heat transfer mechanisms, such as conduction and convection, to dissipate heat from electronic components. Examples of passive cooling include heatsinks and thermal interface materials. Active cooling, on the other hand, involves the use of powered devices, such as fans or thermoelectric coolers, to forcibly remove heat from the system.
4. How do I choose the right heatsink for my PCB?
When selecting a heatsink for your PCB, consider the following factors:
- Thermal Resistance: Choose a heatsink with a thermal resistance that is appropriate for the power dissipation of the components it will be cooling.
- Size and compatibility: Ensure that the heatsink fits within the available space on the PCB and is compatible with the component package and mounting requirements.
- Material: Heatsinks are typically made from aluminum or copper. Copper has better thermal conductivity but is more expensive than aluminum.
- Surface finish: A black anodized or painted finish can improve the heatsink’s emissivity and radiative heat transfer properties.
5. What are some common mistakes to avoid when designing PCBs for thermal management?
Some common mistakes to avoid when designing PCBs for thermal management include:
- Placing high-power components too close together without adequate cooling
- Failing to provide sufficient thermal paths, such as thermal vias, to conduct heat away from components
- Neglecting to consider the impact of ambient temperature and airflow on PCB cooling
- Not using thermal simulation software to identify potential hot spots and optimize the PCB layout
- Overlooking the importance of thermal interface materials in facilitating heat transfer between components and heatsinks
Conclusion
Managing high temperatures is crucial for ensuring the performance, reliability, and longevity of PCBs in electronic devices. By understanding the causes and effects of high temperatures, designers can employ various strategies, such as heatsinks, thermal interface materials, and optimized PCB layouts, to effectively manage heat.
Thermal simulation software plays a vital role in analyzing and optimizing the thermal performance of PCBs, allowing designers to make informed decisions and avoid costly redesigns. By considering thermal management early in the design process and following best practices for PCB layout and component selection, designers can create PCBs that operate reliably even in challenging thermal environments.
As electronic devices continue to push the boundaries of performance and miniaturization, effective thermal management will remain a critical aspect of PCB design. By staying up-to-date with the latest techniques and technologies in PCB temperature management, designers can ensure that their products meet the demanding requirements of modern electronics while maintaining optimal performance and reliability.
0 Comments