Introduction to PCB cooling
Printed Circuit Boards (PCBs) are essential components in modern electronic devices, from smartphones and computers to industrial equipment and aerospace systems. As these devices continue to advance and become more compact, the need for effective heat dissipation techniques becomes increasingly critical. Overheating can lead to component failure, reduced performance, and even complete system breakdowns. In this article, we will explore the primary PCB cooling methods and discuss how they can help protect your circuit board from the damaging effects of excessive heat.
Why is PCB Cooling Important?
PCBs are designed to carry electrical signals and power between various components, such as microprocessors, transistors, and resistors. As these components operate, they generate heat, which must be effectively dissipated to maintain optimal performance and prevent damage. Here are some key reasons why PCB cooling is crucial:
-
Component longevity: Excessive heat can accelerate the aging process of electronic components, leading to premature failure and reduced overall system lifespan.
-
Performance stability: High temperatures can cause components to operate outside their specified range, resulting in erratic behavior, reduced accuracy, and potential system crashes.
-
Safety: In extreme cases, overheating can cause components to melt, short-circuit, or even catch fire, posing serious safety risks to users and the surrounding environment.
-
Compliance with industry standards: Many industries have specific temperature requirements for electronic devices to ensure reliability and safety. Effective PCB cooling helps meet these standards.
Factors Affecting PCB Heat Generation
To effectively address PCB cooling, it is essential to understand the factors that contribute to heat generation on a circuit board. Some of the primary factors include:
-
Power consumption: Higher power consumption by components leads to increased heat generation.
-
Component density: As PCBs become more compact, the density of components increases, making it more challenging to dissipate heat effectively.
-
Ambient temperature: The surrounding environment’s temperature can affect the PCB’s ability to dissipate heat. Higher ambient temperatures make cooling more difficult.
-
PCB design: The layout and design of the PCB, including the placement of components and the use of thermal management materials, can significantly impact heat dissipation.
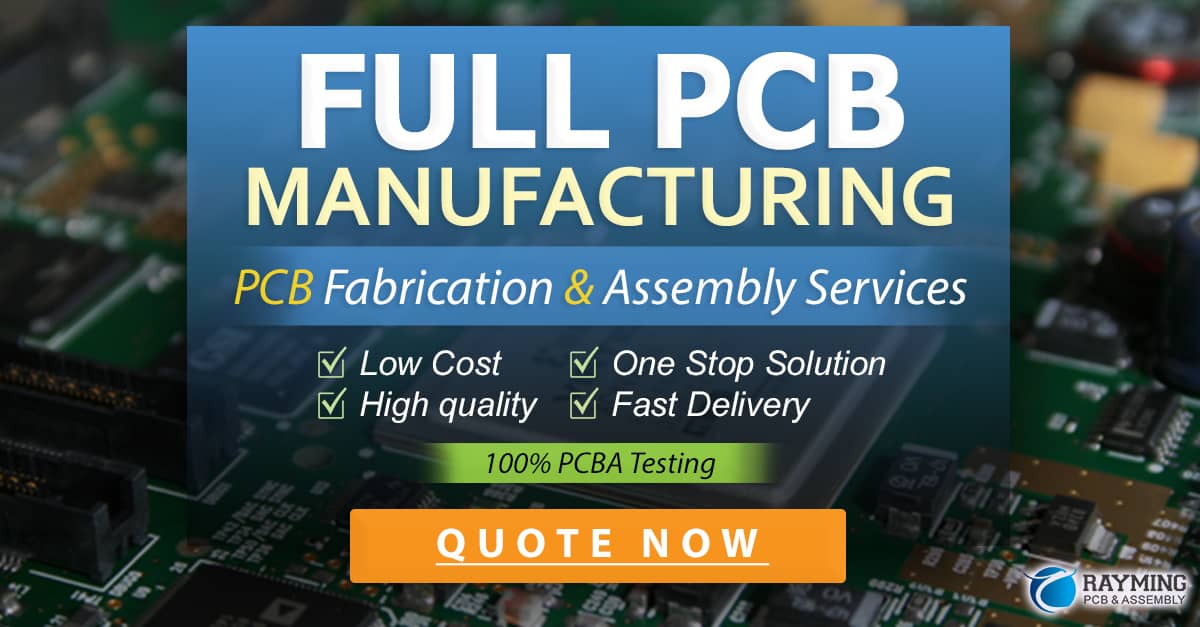
Primary PCB Cooling Techniques
There are several techniques used to dissipate heat from PCBs effectively. The choice of method depends on factors such as the amount of heat generated, the available space, and the operating environment. Let’s explore some of the most common PCB cooling techniques.
1. Natural Convection
Natural convection is the simplest and most cost-effective method of PCB cooling. It relies on the natural movement of air around the circuit board to dissipate heat. As the air near the hot components rises, cooler air takes its place, creating a continuous circulation that helps remove heat from the PCB.
To optimize natural convection cooling, consider the following:
- Provide adequate spacing between components to allow for better airflow.
- Orient the PCB vertically to promote natural air circulation.
- Use larger PCBs with more surface area for improved heat dissipation.
- Incorporate ventilation holes or slots in the enclosure to facilitate airflow.
2. Forced Air Cooling
When natural convection is insufficient, forced air cooling can be employed to enhance heat dissipation. This method involves the use of fans or blowers to actively move air across the PCB, increasing the rate of heat transfer.
Forced air cooling can be implemented in several ways:
-
Component-level cooling: Small fans can be mounted directly onto high-heat-generating components, such as processors or power regulators, to provide targeted cooling.
-
Board-level cooling: Larger fans can be placed strategically within the enclosure to create airflow across the entire PCB.
-
Ducted cooling: Air ducts can be used to direct the airflow from fans to specific areas of the PCB, ensuring optimal cooling of critical components.
When designing a forced air cooling system, consider the following factors:
-
Fan size and placement: Select fans with appropriate airflow and pressure ratings, and position them to maximize cooling effectiveness.
-
Airflow direction: Ensure that the airflow direction is consistent across the PCB to avoid hot spots and promote even cooling.
-
Noise levels: Choose fans with acceptable noise levels for the intended application and environment.
3. Heatsinks
Heatsinks are passive cooling devices that work by increasing the surface area available for heat dissipation. They are typically made of materials with high thermal conductivity, such as aluminum or copper, and are attached to heat-generating components using thermal adhesives or mechanical fasteners.
Heatsinks come in various shapes and sizes, including:
-
Extruded heatsinks: These are the most common type, featuring a flat base and an array of fins to maximize surface area.
-
Stamped heatsinks: Constructed from sheet metal, these heatsinks are lightweight and cost-effective, making them suitable for low-power applications.
-
Forged heatsinks: Offering superior thermal performance, forged heatsinks are machined from solid metal blocks and are ideal for high-power components.
When selecting a heatsink, consider the following factors:
-
Thermal resistance: Choose a heatsink with a thermal resistance that matches the cooling requirements of the component.
-
Surface finish: A black anodized or painted finish can improve the heatsink’s emissivity, enhancing its heat dissipation capabilities.
-
Compatibility: Ensure that the heatsink is compatible with the component’s package type and dimensions.
4. Thermal Interface Materials
Thermal Interface Materials (TIMs) are used to fill the air gaps between heat-generating components and heatsinks, improving thermal conductivity and heat transfer. TIMs come in various forms, including:
-
Thermal greases: These are viscous, silicone-based compounds that are applied between the component and heatsink. They offer good thermal conductivity and can fill surface irregularities.
-
Thermal pads: Made from materials such as silicone or graphite, thermal pads are pre-cut to fit specific component sizes and offer a more user-friendly alternative to thermal greases.
-
Phase-change materials: These materials change from a solid to a liquid state at a specific temperature, allowing them to conform to surface irregularities and improve thermal conductivity.
When choosing a TIM, consider the following factors:
-
Thermal conductivity: Select a TIM with a thermal conductivity that matches the cooling requirements of the component.
-
Ease of application: Consider the ease of applying and removing the TIM, particularly for maintenance or component replacement.
-
Long-term stability: Choose a TIM that maintains its performance over the expected lifespan of the device, without drying out or degrading.
5. Liquid Cooling
For high-power applications or densely packed PCBs, liquid cooling can provide a more effective solution than air cooling. Liquid cooling systems circulate a coolant, such as water or a dielectric fluid, through a closed loop that includes a cold plate, tubing, and a radiator.
The cold plate is mounted directly onto the heat-generating component, absorbing heat from the component and transferring it to the coolant. The heated coolant then flows through the tubing to the radiator, where it is cooled by air flowing through the radiator’s fins. The cooled coolant then returns to the cold plate to repeat the process.
Liquid cooling offers several advantages over air cooling:
-
Higher thermal conductivity: Liquids have a much higher thermal conductivity than air, enabling more effective heat transfer.
-
Targeted cooling: Cold plates can be designed to fit specific component packages, providing targeted cooling for high-power components.
-
Quieter operation: Liquid cooling systems typically generate less noise than air cooling systems, as the radiator fans can operate at lower speeds.
However, liquid cooling also has some disadvantages:
-
Complexity: Liquid cooling systems are more complex than air cooling systems, requiring additional components and assembly.
-
Cost: The added complexity of liquid cooling systems often results in higher costs compared to air cooling solutions.
-
Maintenance: Liquid cooling systems require regular maintenance, such as checking for leaks and replacing the coolant periodically.
Thermal Management Materials
In addition to the cooling techniques discussed above, various thermal management materials can be incorporated into PCB designs to improve heat dissipation. These materials help to spread heat more evenly across the board, reducing hot spots and improving overall cooling performance.
Some common thermal management materials include:
-
Copper planes: Adding copper planes to the PCB layers can help spread heat more efficiently, as copper has excellent thermal conductivity.
-
Thermal vias: These are small, plated holes that transfer heat from one layer of the PCB to another, helping to distribute heat more evenly.
-
Metal core PCBs: These PCBs have a metal core, typically aluminum, which acts as a heat spreader, improving thermal performance compared to standard FR-4 PCBs.
-
Ceramic substrates: For high-temperature applications, ceramic substrates can be used instead of traditional PCB materials. Ceramics offer excellent thermal stability and conductivity.
PCB Design Considerations for Improved Cooling
Effective PCB cooling starts with good design practices. By considering thermal management early in the design process, you can minimize heat generation and improve overall cooling performance. Some key design considerations include:
-
Component placement: Place high-heat-generating components away from each other and near the edge of the board to facilitate better airflow and heat dissipation.
-
Trace width and thickness: Use wider and thicker traces for power-carrying circuits to minimize resistive heating.
-
Ground planes: Incorporate ground planes into the PCB design to help spread heat more evenly across the board.
-
Thermal isolation: Use thermal isolation techniques, such as splitting power and ground planes, to prevent heat from spreading to temperature-sensitive components.
-
Thermal simulations: Perform thermal simulations during the design phase to identify potential hot spots and optimize the placement of components and cooling solutions.
Monitoring and Testing
To ensure that your PCB cooling solution is effective, it is crucial to monitor and test the system under realistic operating conditions. This can be done using various methods, such as:
-
Thermocouples: These are temperature sensors that can be attached to specific components or areas of the PCB to measure local temperatures.
-
Infrared cameras: Infrared cameras can provide a non-contact method of measuring the temperature distribution across the entire PCB.
-
Thermal test chambers: These chambers can be used to subject the PCB to different ambient temperatures and humidity levels, simulating real-world operating conditions.
By monitoring and testing your PCB cooling solution, you can identify any issues and make necessary adjustments to ensure optimal performance and reliability.
FAQ
-
Q: What is the most cost-effective PCB cooling method for low-power applications?
A: For low-power applications, natural convection cooling is often the most cost-effective solution. This method relies on the natural movement of air around the PCB to dissipate heat and can be enhanced by providing adequate spacing between components and incorporating ventilation holes in the enclosure. -
Q: When should I consider using liquid cooling for my PCB?
A: Liquid cooling is typically recommended for high-power applications or densely packed PCBs where air cooling methods are insufficient. If your PCB has components that generate significant amounts of heat, or if the ambient temperature is expected to be high, liquid cooling can provide a more effective solution. -
Q: Can I use thermal interface materials with any type of heatsink?
A: Yes, thermal interface materials can be used with any type of heatsink to improve thermal conductivity and heat transfer. However, it is essential to choose a TIM that is compatible with the specific heatsink material and surface finish, as well as the component package type and dimensions. -
Q: How can I identify potential hot spots on my PCB during the design phase?
A: Thermal simulations can be performed during the design phase to identify potential hot spots on your PCB. These simulations take into account factors such as component placement, power dissipation, and the thermal properties of materials used, allowing you to optimize your design for better cooling performance. -
Q: What are the advantages of using metal core PCBs for thermal management?
A: Metal core PCBs (MCPCBs) offer several advantages for thermal management compared to standard FR-4 PCBs. The metal core, typically made of aluminum, acts as a heat spreader, allowing for more efficient heat dissipation. MCPCBs also have a lower thermal resistance, which means that heat can be transferred more effectively from the components to the metal core and then to the surrounding environment. Additionally, MCPCBs can help reduce thermal stresses on components, improving overall reliability.
Conclusion
Effective PCB cooling is essential for ensuring the reliability, performance, and longevity of electronic devices. By understanding the factors that contribute to heat generation and the various cooling techniques available, you can design and implement a thermal management solution that meets the specific needs of your application.
From simple natural convection cooling to advanced liquid cooling systems, there are numerous options available for dissipating heat from PCBs. By incorporating thermal management materials, such as copper planes and thermal vias, and following best practices for PCB design, you can further enhance the cooling performance of your system.
Remember to monitor and test your PCB cooling solution under realistic operating conditions to identify any issues and make necessary adjustments. By taking a proactive approach to thermal management, you can protect your circuit board from the damaging effects of excessive heat and ensure optimal performance over its entire lifespan.
0 Comments