Understanding the Properties of Rogers Materials
Before diving into the design tips, it’s essential to understand the properties of Rogers materials and how they differ from traditional FR-4 substrates. Rogers offers a wide range of high-frequency laminates, each with unique characteristics suited for different applications. Some popular Rogers materials include:
Material | Dielectric Constant | Dissipation Factor | Thermal Conductivity (W/m·K) |
---|---|---|---|
RO4003C | 3.38 | 0.0027 | 0.71 |
RO4350B | 3.48 | 0.0037 | 0.69 |
RT/duroid 6002 | 2.94 | 0.0012 | 0.60 |
RT/duroid 5880 | 2.20 | 0.0009 | 0.20 |
These materials offer lower dielectric constant and dissipation factor compared to FR-4, resulting in reduced signal loss and improved high-frequency performance. Additionally, their higher thermal conductivity helps dissipate heat more effectively, enhancing the PCB’s power handling capability.
Tip 1: Select the Right Rogers Material for Your Application
Choosing the appropriate Rogers material is crucial for achieving the desired performance in your PCB design. Consider factors such as the operating frequency, signal speed, loss requirements, and environmental conditions when selecting the material. For example:
- For high-speed digital applications, RO4003C or RO4350B are excellent choices due to their low loss and controlled dielectric constant.
- For RF and microwave applications, RT/duroid 6002 or RT/duroid 5880 offer even lower dielectric constant and dissipation factor, enabling superior signal integrity at higher frequencies.
Consult the Rogers material data sheets and work with your PCB manufacturer to determine the most suitable material for your specific application.
Tip 2: Optimize the PCB Stack-up for Signal Integrity
Designing an optimized PCB stack-up is essential for maintaining signal integrity and minimizing crosstalk in Rogers PCBs. Consider the following guidelines:
- Use symmetrical stack-ups with ground planes on the outer layers to provide shielding and reduce electromagnetic interference (EMI).
- Maintain consistent dielectric thickness between signal layers and their reference planes to control impedance and minimize signal reflections.
- Use thin dielectric layers for high-speed signals to reduce the propagation delay and improve signal quality.
- Employ micro-strip or strip-line configurations for controlled impedance transmission lines.
Work closely with your PCB fabricator to develop a stack-up that meets your performance requirements while considering manufacturing feasibility and cost.
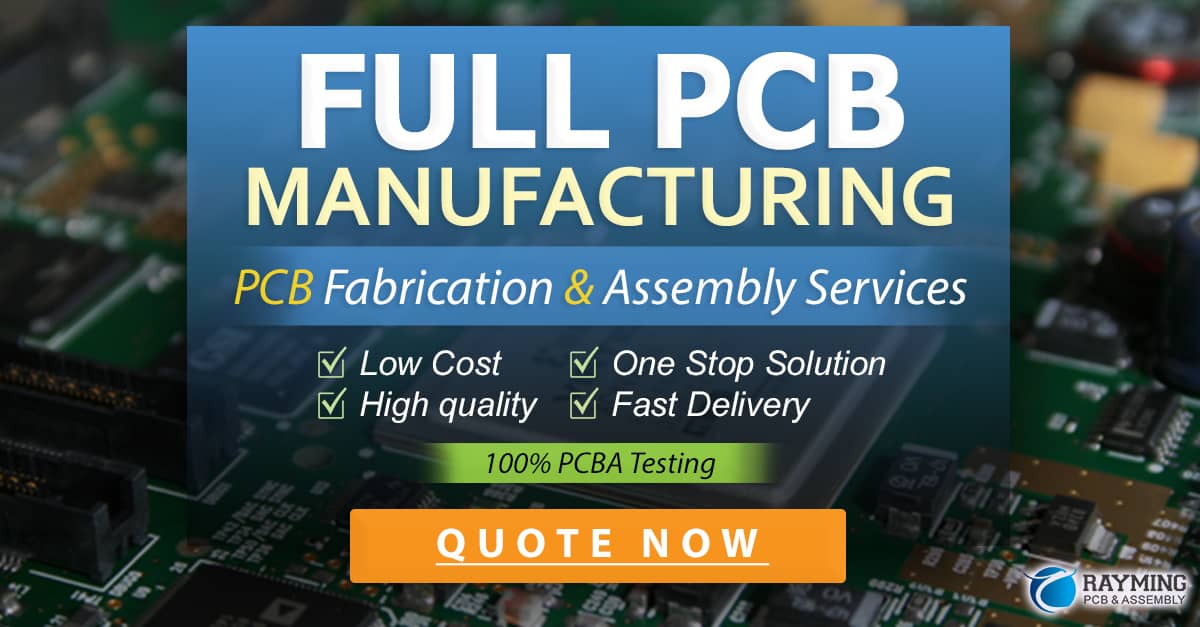
Tip 3: Control Impedance for High-Speed Signals
Controlling impedance is crucial for maintaining signal integrity in high-speed Rogers PCBs. Impedance mismatches can lead to signal reflections, crosstalk, and increased electromagnetic emissions. To control impedance:
- Calculate the required trace width and spacing based on the dielectric constant, thickness, and copper weight of the Rogers material.
- Use impedance calculators or simulation tools to determine the optimal trace geometry for your desired characteristic impedance (e.g., 50 ohms for RF circuits).
- Employ differential pair routing for high-speed differential signals, ensuring matched length and spacing between the pairs.
- Avoid abrupt changes in trace width or direction, as they can cause impedance discontinuities.
Regularly communicate with your PCB manufacturer to ensure that the impedance requirements are met during fabrication.
Tip 4: Minimize Loss and Dispersion
Rogers materials offer low loss and low dispersion, but careful design practices can further minimize these effects in your PCB:
- Keep high-speed traces as short as possible to reduce the overall loss and signal attenuation.
- Use smooth, curved traces instead of sharp corners to minimize reflections and impedance discontinuities.
- Avoid using vias whenever possible, as they introduce additional loss and reflections. If vias are necessary, use micro-vias or buried vias to minimize their impact.
- Consider the skin effect and adjust trace width accordingly for high-frequency signals to minimize resistive losses.
By minimizing loss and dispersion, you can ensure that your signals maintain their integrity over longer distances and at higher frequencies.
Tip 5: Implement Proper Grounding and Shielding Techniques
Effective grounding and shielding are essential for reducing EMI, crosstalk, and ground bounce in Rogers PCBs. Follow these techniques:
- Use dedicated ground planes for each signal layer to provide a low-impedance return path and minimize ground noise.
- Implement a solid ground plane beneath high-speed signals to reduce crosstalk and provide shielding.
- Use guard traces or co-planar waveguides to isolate sensitive signals from adjacent traces.
- Employ ground vias near connectors and at regular intervals along high-speed traces to provide a low-impedance path to the ground plane.
- Use shielding cans or compartments to isolate sensitive circuits from external interference.
Proper grounding and shielding techniques help ensure signal integrity, reduce emissions, and improve the overall performance of your Rogers PCB.
Tip 6: Manage Thermal Dissipation
Rogers materials have higher thermal conductivity compared to FR-4, which helps dissipate heat more efficiently. However, proper thermal management is still crucial for maintaining the reliability and performance of your PCB. Consider the following tips:
- Use wider traces for power-carrying conductors to minimize current density and reduce resistive heating.
- Employ thermal vias or metal-core PCBs to transfer heat away from hot components and distribute it evenly across the board.
- Incorporate heatsinks or cooling solutions for high-power components to prevent overheating and ensure reliable operation.
- Monitor the temperature of critical components during testing and validation to ensure they operate within their specified limits.
Effective thermal management helps prevent component failure, improves reliability, and ensures the long-term performance of your Rogers PCB.
Tip 7: Optimize the PCB Layout for Manufacturing
Designing your Rogers PCB with manufacturing considerations in mind can help ensure a smooth and cost-effective production process. Follow these tips:
- Adhere to the minimum trace width and spacing requirements specified by your PCB manufacturer to ensure reliable fabrication.
- Use standard hole sizes and pad dimensions for vias and components to avoid manufacturing challenges and additional costs.
- Provide adequate clearance between components and traces to facilitate assembly and prevent short circuits.
- Incorporate design for manufacturing (DFM) guidelines, such as avoiding acute angles, minimizing the number of vias, and using consistent trace widths.
- Communicate regularly with your PCB manufacturer to address any design concerns and ensure manufacturability.
By optimizing your PCB layout for manufacturing, you can minimize production issues, reduce costs, and achieve a high-quality final product.
Tip 8: Perform Thorough Simulation and Testing
Before finalizing your Rogers PCB design, it’s essential to perform comprehensive simulation and testing to validate its performance. Use the following approaches:
- Conduct signal integrity simulations to analyze impedance matching, crosstalk, and signal reflections.
- Perform electromagnetic compatibility (EMC) simulations to assess the board’s EMI performance and ensure compliance with relevant standards.
- Use 3D modeling and thermal simulation tools to evaluate the thermal performance of your PCB and identify potential hot spots.
- Conduct physical testing on prototype boards to validate the simulation results and ensure the PCB meets your performance requirements.
- Perform accelerated life testing and environmental stress testing to assess the reliability and durability of your Rogers PCB under various conditions.
Thorough simulation and testing help identify and address design issues early in the development process, reducing the risk of costly revisions and ensuring a high-performance final product.
Frequently Asked Questions (FAQ)
-
Q: What are the benefits of using Rogers materials for PCB design?
A: Rogers materials offer several benefits, including lower dielectric constant, lower loss, higher thermal conductivity, and better high-frequency performance compared to traditional FR-4 laminates. These properties make Rogers PCBs ideal for applications that demand superior signal integrity, power handling, and reliability. -
Q: How do I select the right Rogers material for my application?
A: When selecting a Rogers material, consider factors such as the operating frequency, signal speed, loss requirements, and environmental conditions. Consult the Rogers material data sheets and work with your PCB manufacturer to determine the most suitable material based on your specific application requirements. -
Q: Why is impedance control important in Rogers PCB design?
A: Controlling impedance is crucial for maintaining signal integrity in high-speed Rogers PCBs. Impedance mismatches can lead to signal reflections, crosstalk, and increased electromagnetic emissions, which can degrade the performance of your PCB. By carefully designing traces and employing impedance control techniques, you can ensure that signals maintain their integrity and minimize signal distortion. -
Q: How can I manage thermal dissipation in Rogers PCBs?
A: To manage thermal dissipation in Rogers PCBs, use wider traces for power-carrying conductors, employ thermal vias or metal-core PCBs to transfer heat away from hot components, incorporate heatsinks or cooling solutions for high-power components, and monitor the temperature of critical components during testing and validation. Effective thermal management helps prevent component failure and ensures reliable operation of your PCB. -
Q: Why is simulation and testing important for Rogers PCB design?
A: Simulation and testing are essential for validating the performance of your Rogers PCB design before finalizing it. By conducting signal integrity simulations, EMC simulations, thermal simulations, and physical testing on prototype boards, you can identify and address design issues early in the development process. This helps reduce the risk of costly revisions and ensures that your PCB meets the desired performance requirements.
Conclusion
Designing performance-driven Rogers PCBs requires careful consideration of material selection, stack-up optimization, impedance control, loss minimization, grounding and shielding techniques, thermal management, manufacturability, and thorough simulation and testing. By following the eight technical tips outlined in this article, you can effectively leverage the benefits of Rogers materials and create PCBs that deliver superior signal integrity, power handling, and reliability for your high-performance applications.
Remember to work closely with your PCB manufacturer throughout the design process to ensure that your requirements are met and that your design is optimized for manufacturability and cost-effectiveness. With the right design approach and attention to detail, you can unlock the full potential of Rogers materials and create PCBs that excel in performance and reliability.
0 Comments