What is Selective Soldering?
Selective soldering, also known as Selsoldering, is a process in which specific components are soldered onto a printed circuit board (PCB) using a precisely controlled soldering iron or nozzle. This technique is commonly used in electronics manufacturing when certain components cannot withstand the high temperatures of a reflow oven or when components need to be added after the initial soldering process.
Advantages of Selective Soldering
Selective soldering offers several advantages over traditional Wave Soldering and Reflow Soldering methods:
-
Precision: Selsoldering allows for precise control over the soldering process, ensuring that only the desired components are soldered onto the PCB.
-
Flexibility: This technique enables the soldering of components that are sensitive to high temperatures or cannot be exposed to the entire PCB’s soldering process.
-
Cost-effective: Selective soldering can be more cost-effective than other methods, as it reduces the need for expensive masks or stencils.
-
Reduced thermal stress: By targeting only specific components, selective soldering minimizes the thermal stress on the PCB and surrounding components.
The Selective Soldering Process
The selective soldering process typically involves the following steps:
-
PCB preparation: The PCB is cleaned and inspected to ensure it is free of contaminants and defects.
-
Solder Paste application: Solder paste is applied to the specific areas where components will be soldered. This can be done using a dispensing machine or a solder paste printer.
-
Component placement: The components are placed onto the PCB, either manually or using a pick-and-place machine.
-
Flux application: Flux is applied to the components and solder joints to improve solder wetting and prevent oxidation.
-
Soldering: The selective soldering machine uses a precisely controlled soldering iron or nozzle to apply heat and solder to the specific components and solder joints.
-
Inspection: The soldered PCB is inspected for quality and accuracy, typically using automated optical inspection (AOI) systems or manual visual inspection.
Selective Soldering Equipment
Several types of selective soldering equipment are available, each with its own advantages and applications:
-
Laser selective soldering: This method uses a laser to heat and solder specific components, offering high precision and minimal thermal stress.
-
Miniwave selective soldering: This technique uses a small wave of molten solder to selectively solder components, providing a balance between speed and precision.
-
Robotic selective soldering: This approach employs a Robotic Arm equipped with a soldering iron or nozzle, allowing for high flexibility and customization.
Challenges in Selective Soldering
While selective soldering offers numerous benefits, it also presents some challenges:
-
Complexity: Selsoldering requires precise control and programming, which can be complex and time-consuming.
-
Cost: The initial investment in selective soldering equipment can be high, although the long-term benefits often outweigh the upfront costs.
-
Compatibility: Not all components are suitable for selective soldering, and some may require special handling or preparation.
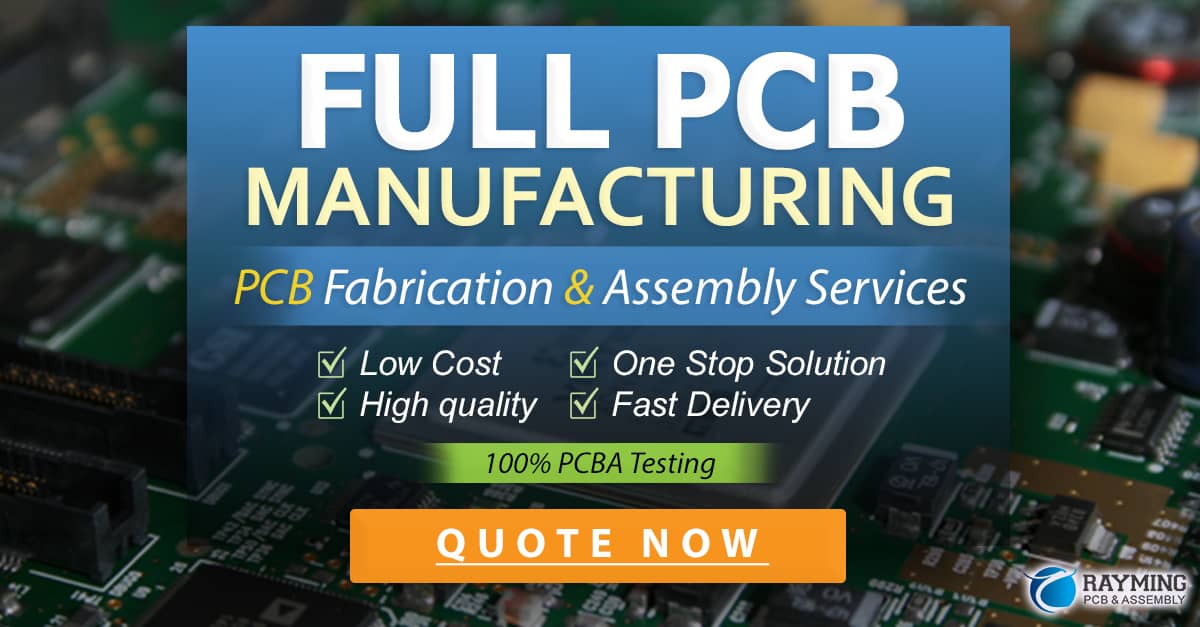
Best Practices for Selective Soldering
To ensure optimal results and minimize defects, consider the following best practices when implementing selective soldering:
-
Proper PCB design: Design the PCB with selective soldering in mind, ensuring adequate spacing between components and solder joints.
-
Correct solder paste and flux selection: Choose the appropriate solder paste and flux for the specific components and PCB materials.
-
Regular maintenance: Regularly clean and maintain the selective soldering equipment to ensure consistent performance and minimize downtime.
-
Operator training: Provide thorough training to operators to ensure they understand the selective soldering process and can troubleshoot issues effectively.
Applications of Selective Soldering
Selective soldering is used in various industries and applications, including:
-
Automotive electronics: Selsoldering is commonly used in the production of Automotive PCBs, which often require the soldering of high-temperature components or connectors.
-
Aerospace and defense: The high precision and reliability of selective soldering make it well-suited for aerospace and defense applications, where PCBs must withstand harsh environments and meet stringent quality standards.
-
Medical devices: Selective soldering is used in the production of medical device PCBs, which require high accuracy and consistency to ensure patient safety.
-
Consumer electronics: Selsoldering is employed in the manufacturing of consumer electronics, such as smartphones, tablets, and wearables, where miniaturization and high component density are common.
Selective Soldering vs. Other Soldering Methods
Selective soldering offers several advantages over other soldering methods, such as wave soldering and reflow soldering:
Soldering Method | Advantages | Disadvantages |
---|---|---|
Selective Soldering | – Precise control – Flexibility – Reduced thermal stress |
– Higher initial investment – Complexity – Not suitable for all components |
Wave Soldering | – High throughput – Cost-effective for large volumes – Suitable for through-hole components |
– Limited control over individual components – Potential for thermal damage – Not suitable for SMT components |
Reflow Soldering | – Suitable for SMT components – High throughput – Consistent results |
– Not suitable for through-hole components – Potential for thermal damage – Limited flexibility |
The Future of Selective Soldering
As electronics continue to evolve, selective soldering is expected to play an increasingly important role in PCB manufacturing. Some trends and developments to watch for include:
-
Increased automation: Advances in robotics and machine learning will likely lead to more automated and intelligent selective soldering systems.
-
Improved process control: The development of more advanced sensors and monitoring systems will enable better process control and quality assurance.
-
Miniaturization: As electronic devices continue to shrink, selective soldering will become even more crucial for precisely soldering small, densely packed components.
-
New materials and processes: The introduction of new solder alloys, fluxes, and substrate materials may require adaptations in selective soldering techniques and equipment.
Frequently Asked Questions (FAQ)
-
What is the difference between selective soldering and wave soldering?
Selective soldering targets specific components on a PCB, while wave soldering exposes the entire board to a wave of molten solder. Selective soldering offers more precision and control, while wave soldering is better suited for high-volume production of through-hole components. -
Can selective soldering be used for both through-hole and surface-mount components?
Yes, selective soldering can be used for both through-hole and surface-mount components. However, the process may need to be adapted depending on the specific component types and PCB design. -
Is selective soldering more expensive than other soldering methods?
The initial investment in selective soldering equipment can be higher than other methods, but the long-term benefits, such as reduced defects and increased flexibility, often justify the cost. Additionally, selective soldering can be more cost-effective than other methods for certain applications, such as low-volume production or rework. -
How does selective soldering handle temperature-sensitive components?
Selective soldering minimizes thermal stress on temperature-sensitive components by targeting only the specific areas that need to be soldered. This helps prevent damage to the components and surrounding areas of the PCB. -
What skills are required for operators working with selective soldering equipment?
Operators should have a good understanding of the selective soldering process, including the programming and maintenance of the equipment. They should also be familiar with PCB design principles, component handling, and quality control procedures. Proper training is essential to ensure consistent and high-quality results.
Conclusion
Selective soldering is a versatile and precise method for soldering specific components onto PCBs. By offering flexibility, reduced thermal stress, and cost-effectiveness, selsoldering has become an essential technique in electronics manufacturing. As the industry continues to evolve, the importance of selective soldering is likely to grow, driven by trends such as miniaturization, automation, and new materials. By understanding the principles, best practices, and future developments in selective soldering, manufacturers can leverage this technology to produce high-quality, reliable electronic products.
0 Comments