What is Rogers PCB?
Rogers PCB, also known as High-Frequency PCB or Microwave PCB, is a specialized type of printed circuit board that uses Rogers materials as the substrate. Rogers materials are a family of high-performance dielectric materials developed by Rogers Corporation, which offer excellent electrical and mechanical properties for high-frequency applications.
Rogers PCBs are widely used in various industries, such as telecommunications, aerospace, defense, automotive, and medical devices, where high-frequency signals, low dielectric loss, and stable performance under harsh conditions are critical.
Key Features of Rogers PCB
- High-frequency performance
- Low dielectric loss
- Excellent thermal stability
- Tight dielectric constant tolerance
- Low moisture absorption
- High resistance to chemicals and solvents
Rogers Material Types and Properties
Rogers Corporation offers a wide range of dielectric materials suitable for different high-frequency applications. Some of the most commonly used Rogers materials for PCBs include:
1. Rogers RO4000 Series
The RO4000 series is a popular choice for high-frequency applications up to 18 GHz. It offers a low dielectric constant (3.38-3.55) and low Loss Tangent (0.0027-0.0037), making it suitable for applications such as cellular base stations, radar systems, and satellite communications.
Material | Dielectric Constant | Dissipation Factor | Thermal Conductivity (W/m/K) |
---|---|---|---|
RO4003C | 3.38 | 0.0027 | 0.71 |
RO4350B | 3.48 | 0.0037 | 0.69 |
RO4360G2 | 3.55 | 0.0037 | 0.69 |
2. Rogers RT/duroid Series
The RT/duroid series is known for its excellent thermal stability and low dielectric loss, making it ideal for applications up to 77 GHz. Common materials in this series include:
Material | Dielectric Constant | Dissipation Factor | Thermal Conductivity (W/m/K) |
---|---|---|---|
RT/duroid 5870 | 2.33 | 0.0012 | 0.26 |
RT/duroid 5880 | 2.20 | 0.0009 | 0.26 |
RT/duroid 6002 | 2.94 | 0.0012 | 0.60 |
3. Rogers TMM Series
The TMM series offers a range of dielectric constants (3.27-12.85) and low loss tangents, making it suitable for various high-frequency applications, such as automotive radar, aerospace, and defense systems.
Material | Dielectric Constant | Dissipation Factor | Thermal Conductivity (W/m/K) |
---|---|---|---|
TMM3 | 3.27 | 0.0020 | 0.70 |
TMM4 | 4.50 | 0.0020 | 0.70 |
TMM6 | 6.00 | 0.0023 | 0.70 |
TMM10 | 9.20 | 0.0022 | 0.70 |
TMM13i | 12.85 | 0.0019 | 0.70 |
Advantages of Using Rogers PCB
1. Superior High-Frequency Performance
Rogers materials offer low dielectric loss and stable dielectric constant over a wide frequency range, ensuring optimal signal integrity and reduced signal distortion in high-frequency applications.
2. Excellent Thermal Stability
Rogers PCBs maintain their electrical and mechanical properties over a wide temperature range, making them suitable for applications exposed to harsh environmental conditions, such as automotive and aerospace systems.
3. Tight Dielectric Constant Tolerance
Rogers materials are manufactured with tight dielectric constant tolerances, ensuring consistent performance across different production batches and reducing the need for design adjustments.
4. Low Moisture Absorption
Rogers PCBs have low moisture absorption rates, minimizing the risk of performance degradation due to humidity and ensuring long-term reliability.
5. High Resistance to Chemicals and Solvents
Rogers materials are resistant to various chemicals and solvents commonly used in PCB manufacturing processes, ensuring the integrity of the final product.
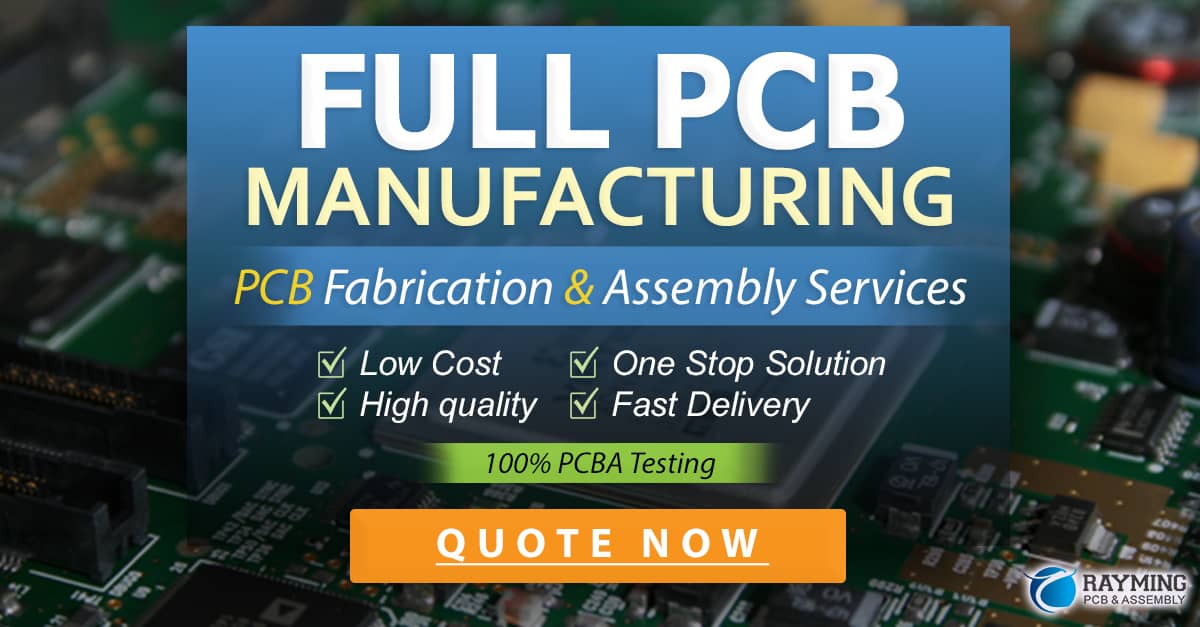
Applications of Rogers PCB
Rogers PCBs find applications in various high-frequency and high-performance systems, such as:
- Telecommunications
- 5G networks
- Cellular base stations
- Satellite communications
-
Microwave links
-
Aerospace and Defense
- Radar systems
- Avionics
- Military communications
-
Missile guidance systems
-
Automotive
- Advanced driver assistance systems (ADAS)
- Autonomous vehicles
- Automotive radar
-
Vehicle-to-vehicle (V2V) communications
-
Medical Devices
- MRI machines
- High-frequency medical imaging systems
-
Microwave ablation devices
-
Industrial Applications
- High-frequency power amplifiers
- Microwave heating systems
- Non-destructive testing equipment
RAYPCB’s Expertise in Rogers PCB Manufacturing
RAYPCB is a leading PCB manufacturer specializing in high-quality Rogers PCB fabrication. With state-of-the-art facilities and a team of experienced engineers, RAYPCB offers a wide range of Rogers PCB solutions for various high-frequency applications.
RAYPCB’s Rogers PCB Manufacturing Capabilities
- Multilayer Rogers PCBs (up to 24 layers)
- Mixed-material PCBs (combining Rogers and FR-4)
- Controlled impedance Rogers PCBs
- Blind and buried via Rogers PCBs
- High-density interconnect (HDI) Rogers PCBs
- Rigid-flex Rogers PCBs
RAYPCB’s Quality Assurance and Certifications
- ISO 9001:2015 certified
- IATF 16949:2016 certified
- UL certified
- IPC Class 2 and Class 3 standards
- 100% electrical testing and visual inspection
FAQ
1. What is the main difference between Rogers PCB and standard FR-4 PCB?
Rogers PCBs use high-performance dielectric materials designed for high-frequency applications, offering lower dielectric loss, better thermal stability, and tighter dielectric constant tolerance compared to standard FR-4 PCBs.
2. Can Rogers PCBs be combined with other materials, such as FR-4?
Yes, it is possible to create mixed-material PCBs that combine Rogers materials with FR-4 or other substrates. This approach allows for cost optimization while maintaining high-frequency performance in critical areas of the circuit.
3. What are the main challenges in designing and manufacturing Rogers PCBs?
Designing and manufacturing Rogers PCBs requires specialized knowledge and experience due to the unique properties of Rogers materials. Challenges include managing controlled impedance, ensuring proper grounding and shielding, and selecting the appropriate Rogers material for the specific application and frequency range.
4. How does the cost of Rogers PCBs compare to standard FR-4 PCBs?
Rogers PCBs are generally more expensive than standard FR-4 PCBs due to the higher cost of Rogers materials and the specialized manufacturing processes required. However, the superior performance and reliability of Rogers PCBs often justify the added cost in high-frequency and critical applications.
5. What should I consider when choosing a Rogers PCB manufacturer?
When selecting a Rogers PCB manufacturer, consider factors such as their experience with Rogers materials, manufacturing capabilities, quality assurance processes, certifications, and customer support. It is essential to choose a manufacturer that can provide high-quality Rogers PCBs that meet your specific application requirements and industry standards.
Conclusion
Rogers PCBs are an essential component in various high-frequency and high-performance applications, offering superior electrical and mechanical properties compared to standard PCBs. By understanding the different Rogers material types, their properties, and the advantages they offer, engineers and designers can select the most suitable Rogers PCB solution for their specific application needs.
RAYPCB, with its extensive experience and advanced manufacturing capabilities, is well-positioned to provide high-quality Rogers PCB solutions for a wide range of industries and applications. By partnering with RAYPCB, customers can benefit from expert guidance, state-of-the-art facilities, and a commitment to quality and reliability in every Rogers PCB project.
0 Comments