Introduction to Thermal conductivity in Printed Wiring Boards
Printed Wiring Boards (PWBs), also known as Printed Circuit Boards (PCBs), are essential components in modern electronic devices. They provide mechanical support and electrical connections for various components, such as integrated circuits, resistors, and capacitors. One crucial aspect of PWB design is thermal management, which involves the efficient dissipation of heat generated by the components. Thermal conductivity plays a vital role in this process, as it determines the material’s ability to conduct heat. In this article, we will discuss how to calculate thermal conductivity in PWBs and its significance in the design process.
What is Thermal Conductivity?
Thermal conductivity is a physical property that measures a material’s ability to conduct heat. It is defined as the rate at which heat is transferred through a material per unit thickness, per unit area, and per unit temperature difference. The SI unit for thermal conductivity is watts per meter-kelvin (W/mK). Materials with higher thermal conductivity values are better at conducting heat, while those with lower values are considered thermal insulators.
Importance of Thermal Conductivity in PWBs
In PWBs, thermal conductivity is crucial for several reasons:
-
Component reliability: Excessive heat buildup can lead to component failure and reduced lifespan. By ensuring proper thermal conductivity, designers can maintain component temperatures within acceptable limits, enhancing reliability.
-
Performance optimization: High temperatures can negatively impact the performance of electronic components, such as increased resistance in conductors and reduced switching speeds in semiconductors. Adequate thermal conductivity helps maintain optimal operating temperatures, ensuring consistent performance.
-
Safety and regulatory compliance: Overheating can pose safety risks, such as fire hazards or user injuries. Regulations often specify maximum allowable temperatures for electronic devices. Proper thermal management through appropriate thermal conductivity ensures compliance with safety standards.
Factors Affecting Thermal Conductivity in PWBs
Several factors influence the thermal conductivity of PWBs:
Material Properties
The choice of materials used in PWB construction significantly impacts thermal conductivity. Some common materials and their thermal conductivity values are:
Material | Thermal Conductivity (W/mK) |
---|---|
FR-4 | 0.3 – 0.4 |
Copper | 385 – 400 |
Aluminum | 205 – 220 |
Ceramic | 20 – 30 |
The thermal conductivity of the substrate material, such as FR-4, and the conductive layers, like copper, determines the overall thermal performance of the PWB.
Layer Thickness and Geometry
The thickness and geometry of the conductive layers in a PWB also affect thermal conductivity. Thicker copper layers provide better Heat Dissipation due to their increased cross-sectional area. Additionally, the layout and placement of components and traces can influence heat distribution and thermal conductivity.
Thermal Vias and Heat Spreaders
Thermal vias are plated through-holes that provide a low-resistance thermal path between layers in a PWB. They help transfer heat from hot spots to other layers or external heat sinks. Heat spreaders, such as metal planes or Thermal Pads, are also used to distribute heat more evenly across the board, improving overall thermal conductivity.
Calculating Thermal Conductivity in PWBs
To calculate the thermal conductivity of a PWB, several methods can be employed:
Analytical Methods
Analytical methods involve using mathematical equations to estimate thermal conductivity based on material properties and board geometry. One common approach is the series-parallel method, which considers the PWB as a combination of series and parallel Thermal Resistances.
The series-parallel method equation for a two-layer board is:
k_effective = (t_1 + t_2) / (t_1/k_1 + t_2/k_2)
Where:
– k_effective is the effective thermal conductivity of the board
– t_1 and t_2 are the thicknesses of layers 1 and 2, respectively
– k_1 and k_2 are the thermal conductivities of layers 1 and 2, respectively
This equation can be extended to Multi-layer Boards by considering additional layers and their respective thicknesses and thermal conductivities.
Numerical Methods
Numerical methods involve using computational techniques, such as finite element analysis (FEA) or computational fluid dynamics (CFD), to simulate heat transfer in PWBs. These methods provide more accurate results by considering complex geometries, material properties, and boundary conditions.
FEA software divides the PWB into small elements and solves heat transfer equations for each element, providing a detailed temperature distribution. CFD simulations can account for fluid flow and convective heat transfer, which are relevant in scenarios with cooling solutions like fans or heat sinks.
Experimental Methods
Experimental methods involve measuring the thermal conductivity of PWBs using specialized equipment. One common technique is the guarded hot plate method, where a sample PWB is placed between two temperature-controlled plates, and the heat flux through the sample is measured.
Another approach is the laser flash method, which involves heating one side of the PWB with a laser pulse and measuring the temperature rise on the opposite side. The thermal diffusivity can be calculated from the temperature response, and thermal conductivity can be derived using the material’s density and specific heat capacity.
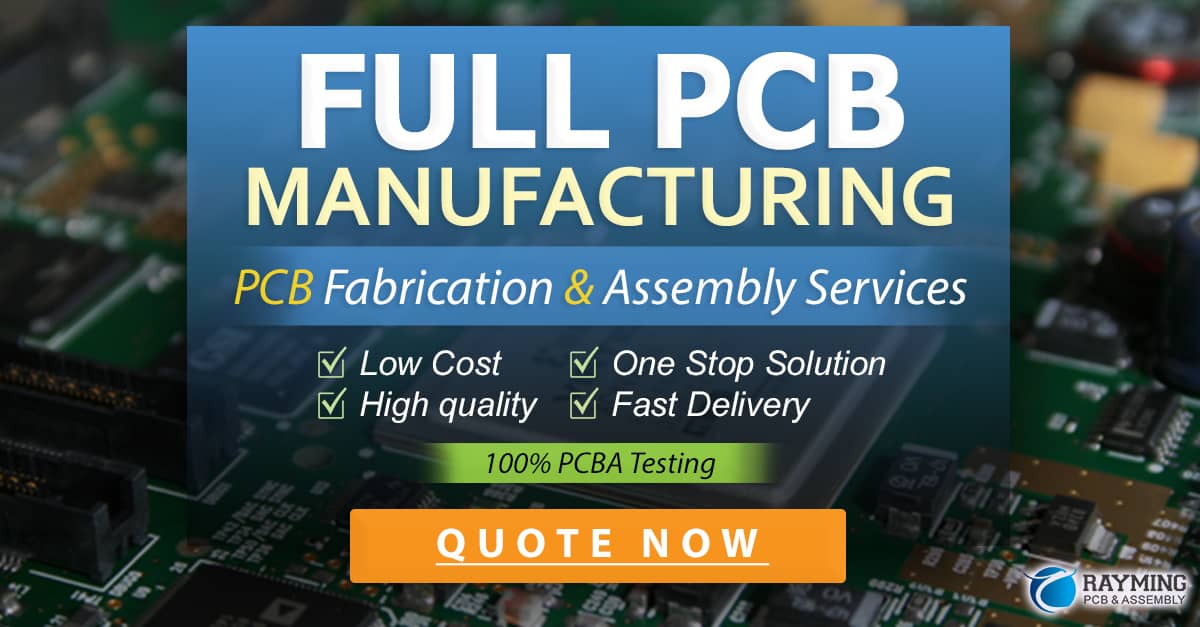
Design Considerations for Optimizing Thermal Conductivity
When designing PWBs for optimal thermal conductivity, several factors should be considered:
Material Selection
Choose materials with higher thermal conductivity values for the substrate and conductive layers. For example, using a metal core substrate instead of traditional FR-4 can significantly improve thermal performance.
Layer Thickness and Copper Weight
Increase the thickness of the copper layers to enhance heat dissipation. Higher copper weights, such as 2 oz or 3 oz copper, provide better thermal conductivity compared to the standard 1 oz copper.
Thermal Via Placement
Strategically place thermal vias near heat-generating components to provide a low-resistance thermal path to other layers or external heat sinks. Optimize via size, pitch, and location to maximize heat transfer while considering manufacturing constraints.
Component Placement and Routing
Arrange components and route traces in a manner that promotes even heat distribution across the board. Avoid clustering high-power components together, and provide sufficient spacing for heat dissipation. Use thermal simulation tools to identify hot spots and optimize component placement accordingly.
External Cooling Solutions
Consider incorporating external cooling solutions, such as heat sinks, fans, or liquid cooling systems, to enhance overall thermal management. These solutions work in conjunction with the PWB’s thermal conductivity to effectively dissipate heat from critical components.
Frequently Asked Questions (FAQ)
-
What is the difference between thermal conductivity and thermal resistance?
Thermal conductivity is a material property that measures the ability to conduct heat, while thermal resistance is a measure of a material’s opposition to heat flow. Thermal resistance is inversely proportional to thermal conductivity and depends on the material’s thickness and cross-sectional area. -
How does the number of layers in a PWB affect thermal conductivity?
The number of layers in a PWB can influence thermal conductivity in two ways. First, increasing the number of layers provides more paths for heat to dissipate through the board. Second, the presence of additional copper layers increases the overall thermal conductivity of the board. However, the effectiveness of multi-layer designs depends on factors such as layer thickness, material properties, and the presence of thermal vias. -
Can thermal conductivity be improved by using different materials for the substrate?
Yes, the choice of substrate material significantly impacts the thermal conductivity of a PWB. Traditional FR-4 substrates have relatively low thermal conductivity values (0.3 – 0.4 W/mK). Using alternative materials, such as metal core substrates (e.g., aluminum or copper) or ceramIC Substrates, can greatly enhance thermal conductivity. However, the choice of substrate material also depends on other design considerations, such as cost, manufacturability, and electrical properties. -
How accurate are analytical methods for calculating thermal conductivity in PWBs?
Analytical methods, such as the series-parallel method, provide a simplified estimation of thermal conductivity in PWBs. They are useful for quick calculations and initial design evaluations. However, analytical methods have limitations, as they often assume ideal conditions and may not account for complex geometries or non-uniform heat distribution. For more accurate results, numerical methods like FEA or experimental measurements are recommended. -
What are some common challenges in achieving optimal thermal conductivity in PWBs?
Some common challenges in achieving optimal thermal conductivity in PWBs include: - Limited space for thermal management features due to miniaturization and high component density
- Trade-offs between thermal performance and other design requirements, such as signal integrity and manufacturability
- Increased power densities of modern electronic components, leading to higher heat generation
- Cost constraints that may limit the use of advanced materials or cooling solutions
- Ensuring reliable and consistent thermal performance across different manufacturing batches and environmental conditions
Conclusion
Calculating thermal conductivity in PWBs is crucial for effective thermal management and ensuring the reliability and performance of electronic devices. By understanding the factors that influence thermal conductivity, such as material properties, layer thickness, and board geometry, designers can make informed decisions to optimize heat dissipation.
Analytical methods, numerical simulations, and experimental techniques provide different approaches to estimating thermal conductivity, each with its own advantages and limitations. Designers should choose the appropriate method based on the level of accuracy required and the available resources.
Furthermore, considering design strategies like material selection, thermal via placement, and component arrangement can significantly enhance the thermal performance of PWBs. By carefully balancing thermal management with other design requirements, engineers can create robust and reliable electronic systems that operate within acceptable temperature ranges.
As electronic devices continue to advance in terms of power density and miniaturization, the importance of effective thermal management and accurate thermal conductivity calculations will only increase. By staying informed about the latest techniques and best practices, designers can tackle the challenges of thermal management head-on and develop innovative solutions for the next generation of electronic products.
0 Comments