Understanding the Relationship Between Pin Length and PCB Thickness
When designing printed circuit boards (PCBs) that utilize through hole components, it is crucial to consider the relationship between the length of the component pins and the thickness of the PCB. Proper selection of pin length and PCB thickness ensures reliable electrical connections, mechanical stability, and ease of assembly. In this article, we will delve into the factors that influence pin length and PCB thickness decisions, explore industry standards, and provide guidelines for optimal design choices.
Factors Affecting Pin Length and PCB Thickness
Several key factors come into play when determining the appropriate pin length and PCB thickness for a given design:
-
Component dimensions: The physical size of the through hole components dictates the minimum pin length required to achieve a secure connection. Larger components often necessitate longer pins to accommodate their size and ensure proper soldering.
-
PCB application: The intended use of the PCB influences the choice of thickness. Boards subjected to higher mechanical stresses or used in harsh environments may require thicker substrates for enhanced durability and reliability.
-
Manufacturing constraints: PCB fabrication capabilities and assembly processes can impose limitations on the minimum and maximum pin lengths and PCB thicknesses that can be accommodated.
-
Electrical requirements: Signal integrity and power handling needs may dictate specific PCB thicknesses to minimize signal loss, control impedance, or dissipate heat effectively.
Industry Standards for Pin Length and PCB Thickness
To promote compatibility and interchangeability, various industry standards provide guidelines for pin lengths and PCB thicknesses. Two widely recognized standards are:
- IPC-2221: Generic Standard on Printed Board Design
- Specifies a range of acceptable PCB thicknesses based on the number of layers and intended application.
-
Provides recommendations for minimum and maximum pin lengths for different component types and package sizes.
-
IEC 61188-5-1: Printed boards and printed board assemblies – Design and use – Part 5-1: Attachment (land/joint) considerations – Generic requirements
- Defines land pattern geometries and dimensions for common through hole components.
- Offers guidance on selecting appropriate pin lengths and PCB thicknesses to ensure reliable solder joints.
Adhering to these standards helps ensure compatibility with industry practices and facilitates smooth manufacturing and assembly processes.
Determining Optimal Pin Length
The optimal pin length for a through hole component depends on several factors, including the PCB thickness, the size of the component, and the specific requirements of the design. Here are some general guidelines to consider:
-
Minimum pin protrusion: To form a reliable solder joint, the component pin should extend beyond the bottom of the PCB by a minimum distance. IPC-2221 recommends a minimum pin protrusion of 0.5 mm to 1.0 mm, depending on the PCB thickness and component type.
-
Maximum pin protrusion: Excessive pin protrusion can lead to mechanical issues and difficulties during assembly. IPC-2221 suggests limiting the maximum pin protrusion to 2.5 mm, although this may vary based on specific design requirements.
-
Solderability: Ensure that the pin length allows for adequate Solder Wicking and formation of a strong solder joint. Insufficient pin length can result in weak or incomplete solder connections.
-
Clearance: Consider the clearance required between the bottom of the PCB and any adjacent components or surfaces to avoid interference or short circuits.
The table below provides a general guide for selecting pin lengths based on common PCB thicknesses:
PCB Thickness (mm) | Minimum Pin Length (mm) | Maximum Pin Length (mm) |
---|---|---|
0.8 – 1.6 | 2.5 | 4.0 |
1.6 – 2.4 | 3.0 | 5.0 |
2.4 – 3.2 | 3.5 | 6.0 |
3.2 – 4.0 | 4.0 | 7.0 |
Note that these values are approximate and may need to be adjusted based on specific component requirements and design constraints.
Selecting Appropriate PCB Thickness
The choice of PCB thickness is influenced by various design considerations, including mechanical strength, signal integrity, and thermal management. Here are some factors to consider when selecting PCB thickness:
-
Number of layers: As the number of layers in a PCB increases, the overall thickness of the board also increases. Multilayer boards often require thicker substrates to accommodate the additional layers and maintain structural integrity.
-
Mechanical requirements: PCBs subjected to high mechanical stresses or used in demanding environments may necessitate thicker substrates to withstand the applied forces and prevent warping or damage.
-
Impedance Control: For high-speed or RF applications, the PCB thickness plays a crucial role in controlling the impedance of the traces. Thinner boards may be preferred to achieve tighter impedance control and minimize signal reflections.
-
Thermal management: Thicker PCBs offer better thermal conductivity and heat dissipation capabilities, making them suitable for power-hungry applications or designs with high component density.
The table below provides a general guideline for selecting PCB thickness based on the number of layers:
Number of Layers | Typical PCB Thickness (mm) |
---|---|
1 – 2 | 0.8 – 1.6 |
4 – 6 | 1.6 – 2.4 |
8 – 10 | 2.4 – 3.2 |
12 – 16 | 3.2 – 4.0 |
Keep in mind that these are approximate values, and the actual thickness may vary based on the specific requirements of the design, such as copper weight, dielectric material, and manufacturing capabilities.
Designing for Manufacturability and Assembly
To ensure smooth manufacturing and assembly processes, consider the following guidelines when designing through hole components and PCBs:
-
Pad size and shape: Create appropriate land patterns for through hole components, considering the pin diameter, PCB thickness, and soldering requirements. Consult industry standards and component datasheets for recommended pad dimensions.
-
Hole size: Specify the appropriate hole size for each component pin, taking into account the pin diameter and any additional clearance required for ease of insertion and soldering.
-
Solder Mask and silkscreen: Apply solder mask around the through hole pads to prevent Solder Bridging and improve the soldering process. Use silkscreen markings to indicate component placement and orientation.
-
Assembly considerations: Consider the accessibility of through hole components during manual or automated assembly processes. Ensure adequate spacing between components to allow for soldering and inspection.
-
Reflow compatibility: If the PCB will undergo a reflow soldering process, select through hole components that are compatible with the reflow temperature profile and have pins that can withstand the thermal stresses.
Frequently Asked Questions (FAQ)
-
What happens if the pin length is too short?
If the pin length is insufficient, it may not protrude enough from the bottom of the PCB to form a reliable solder joint. This can lead to weak or incomplete connections, potentially causing electrical failures or mechanical instability. -
Can I use different pin lengths for the same component?
It is generally recommended to use consistent pin lengths for a given component to ensure even soldering and mechanical stability. However, in some cases, such as when dealing with components that have pins of different diameters, using different pin lengths may be necessary. -
How do I determine the appropriate hole size for a through hole component?
The hole size for a through hole component should be slightly larger than the pin diameter to allow for easy insertion and adequate space for solder flow. Consult the component datasheet or industry standards for recommended hole sizes based on the pin diameter and PCB thickness. -
Can I use a thicker PCB than recommended for my design?
Using a thicker PCB than recommended is generally acceptable, as it can provide additional mechanical strength and thermal dissipation. However, keep in mind that thicker boards may require longer pins for through hole components and can impact the overall size and weight of the assembly. -
What are the consequences of excessive pin protrusion?
Excessive pin protrusion can lead to several issues, including difficulty in assembly, increased risk of mechanical damage, and potential interference with other components or enclosures. It can also make the PCB more susceptible to vibration-induced stresses and complicate the use of automated assembly equipment.
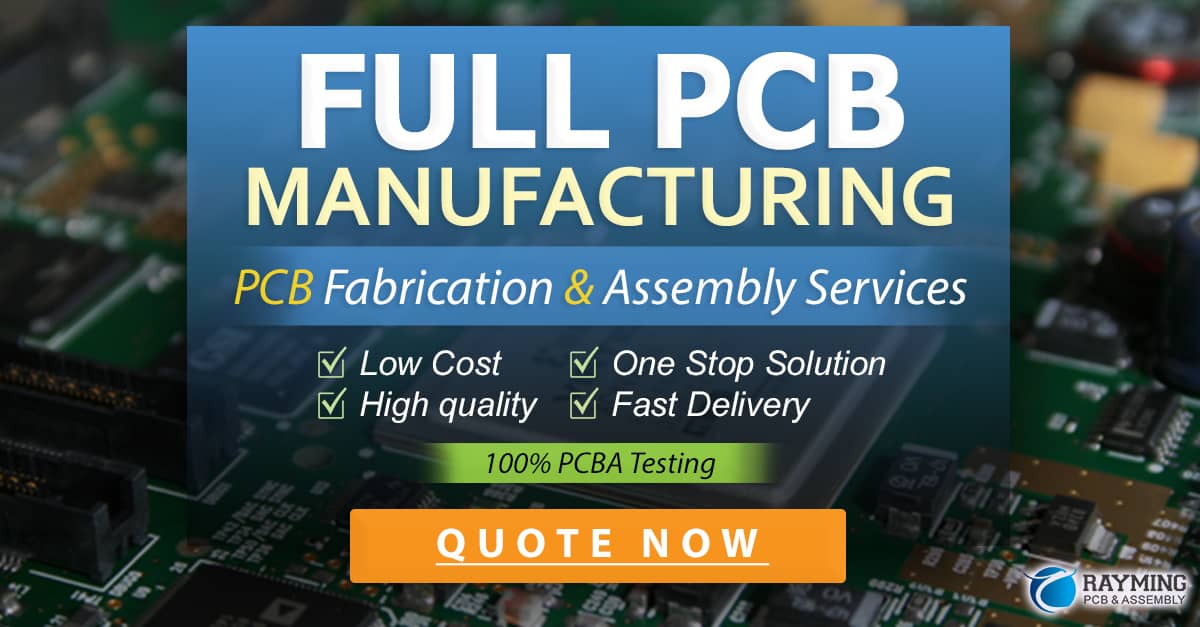
Conclusion
Selecting the appropriate pin length and PCB thickness is a critical aspect of designing reliable and manufacturable through hole assemblies. By understanding the factors that influence these choices, adhering to industry standards, and following best design practices, engineers can ensure optimal performance and compatibility of their PCBs.
When determining pin lengths, consider the PCB thickness, component size, solderability requirements, and clearance needs. Use industry guidelines and standards as a starting point, but adapt them to the specific requirements of your design.
For PCB thickness, evaluate the number of layers, mechanical demands, signal integrity needs, and thermal management considerations. Strike a balance between structural integrity, electrical performance, and manufacturing feasibility.
By carefully selecting pin lengths and PCB thicknesses, designers can create robust and reliable through hole assemblies that meet the demands of their intended applications. Proper planning and attention to detail in this area contribute to the overall success and longevity of electronic products.
0 Comments