Introduction to PCB Etching and Chemical Disposal
Printed Circuit Board (PCB) etching is a crucial process in the manufacturing of electronic devices. It involves the use of various chemicals to remove unwanted copper from the surface of the PCB, leaving behind the desired circuit pattern. While PCB etching is essential for creating functional electronic components, it also generates hazardous chemical waste that must be properly disposed of to minimize environmental impact and ensure the safety of workers and the public.
In this article, we will delve into the details of PCB etching, the chemicals involved, and the proper methods for disposing of these chemicals. We will also discuss the importance of following regulations and guidelines set by environmental agencies and explore alternative, more environmentally friendly PCB etching techniques.
The PCB Etching Process
What is PCB Etching?
PCB etching is a subtractive process used to remove unwanted copper from a PCB, leaving behind the desired circuit pattern. The process begins with a copper-clad board, which is a thin layer of copper laminated onto an insulating substrate, typically made of fiberglass or epoxy resin. The desired circuit pattern is then transferred onto the copper layer using a photoresist, a light-sensitive material that hardens when exposed to ultraviolet (UV) light.
Once the photoresist is applied and the circuit pattern is transferred, the PCB is submerged in an etching solution. The etching solution, which typically contains an oxidizing agent and an acid, reacts with the exposed copper, dissolving it and leaving behind the protected copper that forms the desired circuit pattern.
Chemicals Used in PCB Etching
The most common chemicals used in PCB etching include:
- Ferric Chloride (FeCl3): An oxidizing agent that reacts with copper to form copper chloride (CuCl2) and iron (II) chloride (FeCl2).
- Cupric Chloride (CuCl2): An alternative to ferric chloride, cupric chloride is regenerated during the etching process, making it a more sustainable option.
- Hydrochloric Acid (HCl): An acid used to maintain the pH of the etching solution and to help dissolve the copper.
- Sodium Persulfate (Na2S2O8): An oxidizing agent used in some PCB etching processes as an alternative to ferric chloride.
- Ammonia (NH3): Used to neutralize the acidic etching solution before disposal.
Chemical Name | Formula | Role in PCB Etching |
---|---|---|
Ferric Chloride | FeCl3 | Oxidizing agent, reacts with copper |
Cupric Chloride | CuCl2 | Alternative oxidizing agent, regenerated |
Hydrochloric Acid | HCl | Maintains pH, helps dissolve copper |
Sodium Persulfate | Na2S2O8 | Alternative oxidizing agent |
Ammonia | NH3 | Neutralizes acidic etching solution |
Environmental Concerns
The chemicals used in PCB etching can have significant environmental impacts if not properly handled and disposed of. Ferric chloride and cupric chloride, for example, are toxic to aquatic life and can cause long-term damage to ecosystems if released into water bodies. Hydrochloric acid and sodium persulfate are also hazardous and can cause respiratory issues, skin irritation, and other health problems if not used with proper safety precautions.
Furthermore, the etching process generates a significant amount of chemical waste, including spent etching solutions, rinse water, and contaminated disposable materials such as gloves and filters. This waste must be properly collected, treated, and disposed of to prevent environmental contamination and comply with regulations set by environmental agencies.
Proper Disposal of PCB Etching Chemicals
Regulations and Guidelines
The disposal of PCB etching chemicals is regulated by various environmental agencies, such as the United States Environmental Protection Agency (EPA) and the European Chemicals Agency (ECHA). These agencies set guidelines and standards for the handling, storage, and disposal of hazardous chemicals to protect the environment and public health.
In the United States, the Resource Conservation and Recovery Act (RCRA) governs the disposal of hazardous waste, including PCB etching chemicals. Under RCRA, generators of hazardous waste are responsible for ensuring that their waste is properly identified, stored, transported, and disposed of at a licensed hazardous waste facility.
Similarly, in the European Union, the Waste Framework Directive (2008/98/EC) sets the basic concepts and definitions related to waste management, including the “polluter pays principle,” which holds waste generators responsible for the costs of waste management.
Storing and Labeling PCB Etching Chemicals
Proper storage and labeling of PCB etching chemicals are crucial for ensuring safe handling and disposal. Chemicals should be stored in compatible, leak-proof containers that are clearly labeled with the contents, hazards, and date of generation. Storage areas should be secure, well-ventilated, and equipped with secondary containment to prevent spills from reaching drains or the environment.
Chemical Name | Storage Container | Labeling Requirements |
---|---|---|
Ferric Chloride | Plastic or glass | “Ferric Chloride, Corrosive, Toxic” |
Cupric Chloride | Plastic or glass | “Cupric Chloride, Corrosive, Toxic” |
Hydrochloric Acid | Glass or PTFE-lined | “Hydrochloric Acid, Corrosive” |
Sodium Persulfate | Plastic | “Sodium Persulfate, Oxidizer, Harmful” |
Ammonia | Glass or PTFE-lined | “Ammonia, Corrosive, Toxic” |
Treatment and Disposal Methods
The treatment and disposal of PCB etching chemicals depend on the specific chemical and the local regulations. In general, the following methods are used:
-
Neutralization: Acidic etching solutions, such as those containing hydrochloric acid, can be neutralized with a base, such as sodium hydroxide or ammonia, before disposal. The neutralized solution can then be discharged to a sewer system, provided it meets local discharge limits.
-
Precipitation: Some etching chemicals, such as ferric chloride and cupric chloride, can be treated by precipitation. This involves adding a chemical, such as sodium hydroxide or calcium hydroxide, to the etching solution to precipitate the metal ions as insoluble hydroxides. The precipitated metals can then be filtered out and disposed of as hazardous waste, while the remaining solution can be neutralized and discharged.
-
Ion Exchange: Ion exchange resins can be used to remove metal ions from etching solutions, allowing the solution to be reused or safely discharged. The metal ions are trapped on the resin, which can be regenerated or disposed of as hazardous waste.
-
Off-site Disposal: In many cases, PCB etching chemicals and their waste products must be disposed of at a licensed hazardous waste facility. This involves collecting the waste in appropriate containers, labeling them correctly, and shipping them to the disposal facility using a licensed hazardous waste transporter.
Alternative PCB Etching Methods
Given the environmental concerns associated with traditional PCB etching chemicals, there has been a growing interest in alternative, more environmentally friendly etching methods. Some of these include:
-
Laser Etching: This method uses a high-powered laser to remove the unwanted copper from the PCB, eliminating the need for hazardous chemicals. While laser etching is more environmentally friendly, it is also more expensive and may not be suitable for all PCB Designs.
-
Mechanical Etching: Mechanical etching involves using abrasive materials, such as sandpaper or a milling machine, to remove the unwanted copper. This method is less common and may not achieve the same level of precision as chemical etching.
-
Plasma Etching: Plasma etching uses a high-energy plasma to remove the copper from the PCB. This method is more environmentally friendly than chemical etching but requires specialized equipment and may not be cost-effective for small-scale PCB Production.
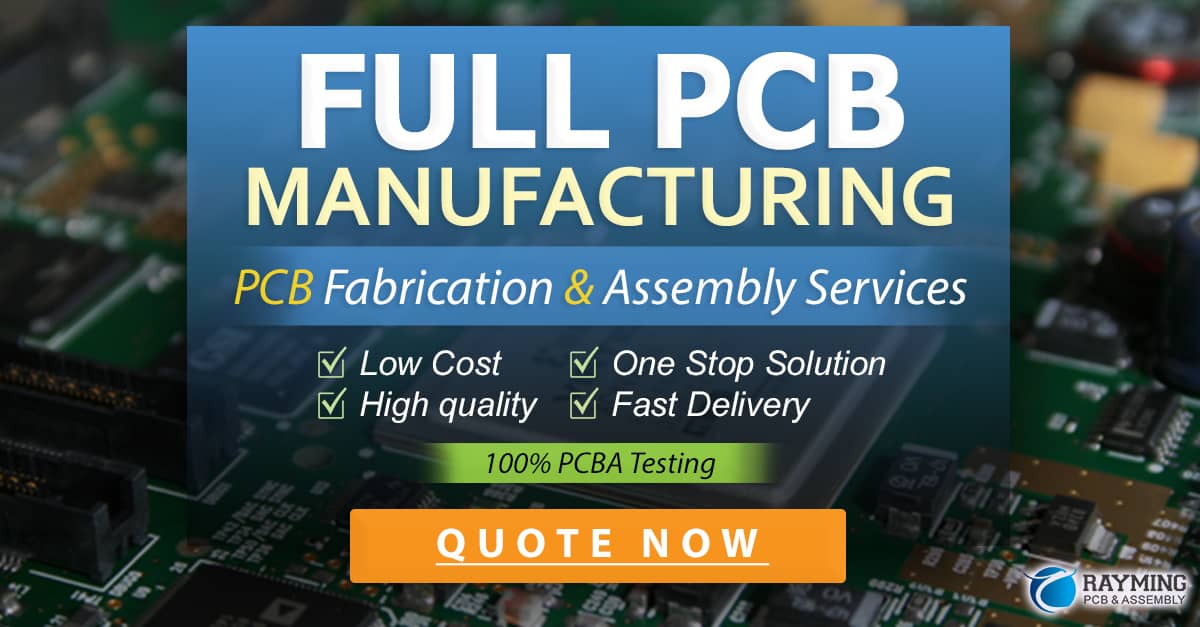
FAQ
-
Q: What are the most common chemicals used in PCB etching?
A: The most common chemicals used in PCB etching are ferric chloride (FeCl3), cupric chloride (CuCl2), hydrochloric acid (HCl), sodium persulfate (Na2S2O8), and ammonia (NH3). -
Q: How should PCB etching chemicals be stored?
A: PCB etching chemicals should be stored in compatible, leak-proof containers that are clearly labeled with the contents, hazards, and date of generation. Storage areas should be secure, well-ventilated, and equipped with secondary containment to prevent spills. -
Q: Can PCB etching chemicals be discharged into the sewer system?
A: In some cases, neutralized PCB etching solutions may be discharged into the sewer system, provided they meet local discharge limits. However, it is essential to check with local authorities and follow the appropriate regulations before discharging any waste. -
Q: What are some alternative methods for PCB etching that are more environmentally friendly?
A: Alternative methods for PCB etching include laser etching, mechanical etching, and plasma etching. These methods eliminate or reduce the need for hazardous chemicals but may be more expensive or less precise than traditional chemical etching. -
Q: Who is responsible for the proper disposal of PCB etching chemicals?
A: The generators of hazardous waste, including PCB etching chemicals, are responsible for ensuring that their waste is properly identified, stored, transported, and disposed of at a licensed hazardous waste facility, in accordance with local and national regulations.
Conclusion
PCB etching is an essential process in the manufacturing of electronic devices, but it also generates hazardous chemical waste that must be properly managed to protect the environment and public health. By understanding the chemicals involved in PCB etching, following proper storage and labeling procedures, and adhering to regulations for treatment and disposal, manufacturers can minimize the environmental impact of their operations.
As the electronics industry continues to grow, it is crucial that we explore and adopt more environmentally friendly PCB etching methods, such as laser etching and plasma etching, to reduce our reliance on hazardous chemicals. By investing in sustainable practices and technologies, we can ensure a cleaner, safer future for both the electronics industry and the planet.
0 Comments