Introduction to PCB Manufacturing
Printed Circuit Boards (PCBs) are the backbone of modern electronic devices. They are used in almost every electronic device, from smartphones and computers to medical equipment and aerospace systems. PCB manufacturing is a complex process that involves several steps, each of which must be carried out with precision and accuracy to ensure the final product meets the required specifications.
In this article, we will explore the PCB manufacturing process in detail, from design to final assembly. We will also discuss the various materials and techniques used in PCB manufacturing and the challenges and opportunities facing the industry.
PCB Design and Layout
The first step in the PCB manufacturing process is the design and layout of the circuit board. This involves creating a schematic diagram of the electronic circuit and then converting it into a physical layout that can be manufactured.
Schematic Design
The schematic design is a graphical representation of the electronic circuit, showing all the components and their interconnections. It is created using specialized software such as Altium Designer, Eagle, or KiCad. The schematic design is the blueprint for the PCB and must be carefully reviewed and verified before moving on to the next step.
PCB Layout
Once the schematic design is complete, it is converted into a physical layout using PCB layout software. The layout shows the actual size and shape of the PCB, as well as the placement of all the components and the routing of the copper traces that connect them.
The PCB layout must take into account several factors, such as:
- Component placement: The components must be placed in a way that minimizes the length of the copper traces and avoids any interference or cross-talk between them.
- Trace width and spacing: The width and spacing of the copper traces must be carefully calculated based on the current and voltage requirements of the circuit.
- Via placement: Vias are small holes drilled through the PCB to connect traces on different layers. They must be placed strategically to minimize the length of the traces and avoid any signal integrity issues.
- Manufacturing constraints: The PCB layout must take into account the limitations of the manufacturing process, such as the minimum trace width and spacing, the minimum drill size, and the maximum board size.
Design for Manufacturing (DFM)
Once the PCB layout is complete, it undergoes a process called Design for Manufacturing (DFM). This involves reviewing the layout to ensure that it can be manufactured efficiently and reliably.
The DFM process checks for several potential issues, such as:
- Copper trace width and spacing violations
- Drill size and placement errors
- Solder mask and silkscreen issues
- Component placement and orientation errors
Any issues identified during the DFM process are corrected before the design is sent for manufacturing.
PCB Fabrication
Once the PCB design is finalized and approved, it is sent for fabrication. The fabrication process involves several steps, each of which must be carried out with precision and accuracy to ensure the final product meets the required specifications.
Material Selection
The first step in PCB fabrication is the selection of the base material, which is typically a glass-reinforced epoxy laminate. The most commonly used material is FR-4, which is a flame-retardant composite material made of woven fiberglass cloth with an epoxy resin binder.
Other materials used in PCB fabrication include:
- High-frequency laminates: These materials are used for high-speed digital circuits and RF applications. They have a lower dielectric constant and dissipation factor than FR-4, which reduces signal loss and improves signal integrity.
- Flexible substrates: These materials are used for flexible PCBs that can bend and flex without breaking. They are made of polyimide or other flexible polymers and are often used in wearable devices and medical equipment.
- Metal core substrates: These materials are used for high-power applications that require efficient heat dissipation. They have a metal core, typically aluminum, that acts as a heat sink and improves thermal performance.
Copper Cladding
After the base material is selected, it is coated with a thin layer of copper on one or both sides. The copper layer is typically 1 oz. (35 µm) or 2 oz. (70 µm) thick, although thicker layers can be used for high-current applications.
The copper cladding is applied using a process called electroplating, which involves immersing the base material in a copper sulfate solution and applying an electric current. The copper ions in the solution are attracted to the surface of the base material and form a thin, even layer of copper.
Drilling
Once the copper cladding is applied, the next step is to drill holes through the board for the component leads and vias. The holes are typically drilled using a computer-controlled drill machine, which can drill hundreds or thousands of holes in a single pass.
The size and placement of the holes must be carefully controlled to ensure that they align with the copper pads on the surface of the board. Any misalignment can cause problems during the assembly process and may result in a non-functional board.
Copper Patterning
After the holes are drilled, the next step is to create the copper pattern on the surface of the board. This involves removing the unwanted copper from the surface, leaving only the desired traces and pads.
There are two main methods used for copper patterning: subtractive and additive.
Subtractive Method
The subtractive method involves coating the entire surface of the board with a photoresist material, which is sensitive to ultraviolet (UV) light. The photoresist is then exposed to UV light through a photomask, which has the desired copper pattern printed on it.
The exposed areas of the photoresist become soluble and can be washed away, leaving the unexposed areas intact. The board is then immersed in an etchant solution, typically ferric chloride or ammonium persulfate, which dissolves the copper in the exposed areas.
After etching, the remaining photoresist is removed, leaving the desired copper pattern on the surface of the board.
Additive Method
The additive method, also known as the full additive process, involves depositing copper only where it is needed on the surface of the board. This is typically done using a process called electroless copper plating, which involves immersing the board in a copper solution and applying a chemical reducing agent to the surface.
The reducing agent causes the copper ions in the solution to plate onto the surface of the board, forming a thin layer of copper. The process is repeated until the desired thickness is achieved.
The additive method has several advantages over the subtractive method, including:
- Finer feature sizes: The additive method can produce trace widths and spaces as small as 25 µm, compared to 75 µm for the subtractive method.
- Reduced waste: The additive method uses less copper and generates less waste than the subtractive method, making it more environmentally friendly.
- Improved adhesion: The electroless copper plating process produces a stronger bond between the copper and the base material, improving the reliability of the final product.
However, the additive method is more expensive and time-consuming than the subtractive method and is typically used only for high-density, high-performance applications.
Soldermask Application
After the copper patterning is complete, the next step is to apply a soldermask layer to the surface of the board. The soldermask is a thin, protective layer that covers the copper traces and pads, leaving only the areas that need to be soldered exposed.
The soldermask is typically applied using a screen printing process, which involves applying a thick layer of liquid soldermask to the surface of the board and then curing it with UV light. The soldermask is available in a variety of colors, with green being the most common.
The soldermask serves several important functions, including:
- Protecting the copper traces from oxidation and corrosion
- Preventing solder bridges from forming between adjacent pads
- Providing electrical insulation between the copper traces and the environment
- Improving the aesthetics of the final product
Silkscreen Application
The final step in the PCB fabrication process is the application of the silkscreen layer. The silkscreen is a thin, white layer that is printed on top of the soldermask and contains text and graphics that identify the components and their locations on the board.
The silkscreen is typically applied using a screen printing process, similar to the soldermask application. The silkscreen ink is a specially formulated epoxy that is resistant to abrasion and chemicals.
The silkscreen serves several important functions, including:
- Identifying the components and their locations on the board
- Providing a visual reference for assembly and troubleshooting
- Improving the aesthetics of the final product
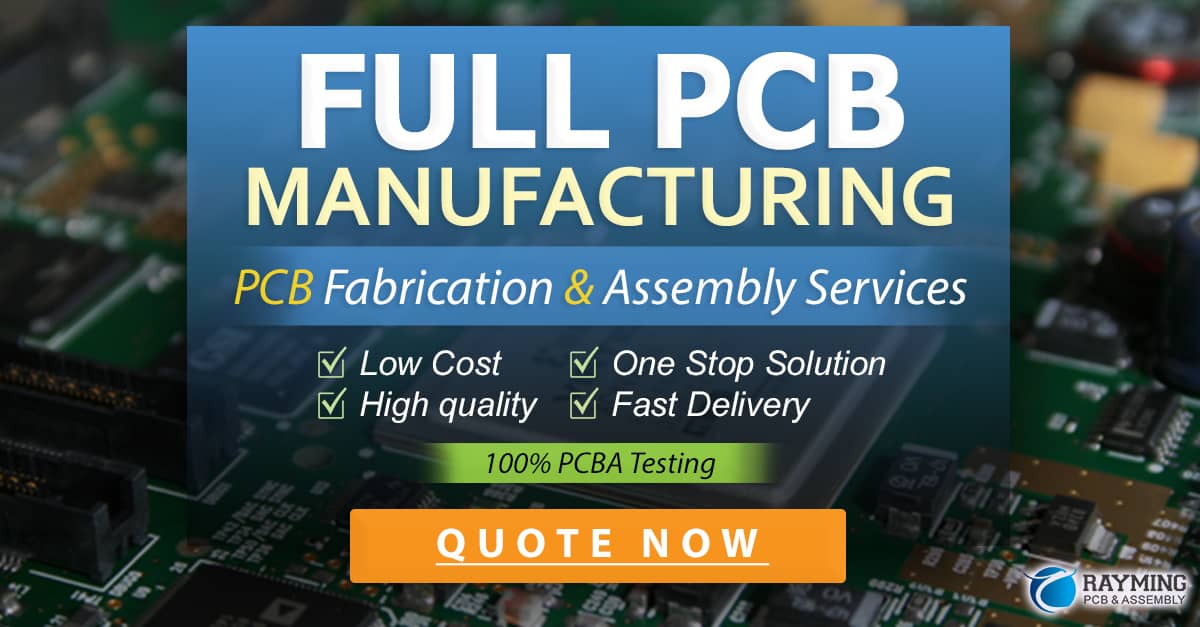
PCB Assembly
Once the PCB fabrication process is complete, the next step is to assemble the components onto the board. The assembly process involves several steps, each of which must be carried out with precision and accuracy to ensure the final product functions correctly.
Component Placement
The first step in PCB assembly is to place the components onto the board. This is typically done using a pick-and-place machine, which uses a vacuum nozzle to pick up the components from a feeder and place them onto the board.
The pick-and-place machine is programmed with the location and orientation of each component on the board, and can place thousands of components per hour with high accuracy and repeatability.
Soldering
After the components are placed, the next step is to solder them onto the board. There are two main methods used for soldering: wave soldering and reflow soldering.
Wave Soldering
Wave soldering involves passing the board over a molten solder wave, which wets the exposed pads and component leads and forms a strong mechanical and electrical bond.
Wave soldering is typically used for through-hole components, which have leads that extend through the holes in the board. The leads are trimmed and bent to the correct shape before the board is passed over the solder wave.
Reflow Soldering
Reflow soldering involves applying a solder paste to the pads on the board and then heating the entire board in an oven until the solder melts and forms a bond with the component leads.
Reflow soldering is typically used for surface-mount components, which have flat leads that sit on top of the pads on the board. The solder paste is applied using a stencil or screen printing process, and the components are placed onto the pads using a pick-and-place machine.
The reflow soldering process involves several stages, including:
- Preheating: The board is gradually heated to a temperature just below the melting point of the solder, typically around 150°C. This helps to evaporate any moisture and activate the flux in the solder paste.
- Soaking: The board is held at the preheat temperature for a period of time, typically 60-90 seconds, to ensure that all the components and the board have reached thermal equilibrium.
- Reflow: The board is quickly heated to a temperature above the melting point of the solder, typically around 240°C. This causes the solder to melt and form a bond with the component leads and pads.
- Cooling: The board is allowed to cool slowly back to room temperature, allowing the solder to solidify and form a strong mechanical and electrical bond.
Inspection and Testing
After the soldering process is complete, the board undergoes a series of inspections and tests to ensure that it functions correctly and meets the required specifications.
The inspection process typically involves several steps, including:
- Visual inspection: The board is visually inspected for any defects or anomalies, such as solder bridges, missing components, or damaged traces.
- Automated optical inspection (AOI): The board is scanned using a high-resolution camera and computer vision software, which compares the actual board to the expected design and identifies any defects or deviations.
- X-ray inspection: The board is subjected to X-ray imaging to inspect the solder joints and other internal features that are not visible from the surface.
The testing process typically involves several steps, including:
- In-circuit testing (ICT): The board is connected to a test fixture that applies electrical signals to the various test points on the board and measures the response. This allows the tester to verify that each component and connection is functioning correctly.
- Functional testing: The board is connected to a test system that simulates the actual operating conditions of the final product and verifies that the board functions correctly under normal and abnormal conditions.
- Burn-in testing: The board is subjected to a period of extended operation at elevated temperature and voltage to identify any early failures or reliability issues.
Challenges and Opportunities in PCB Manufacturing
The PCB manufacturing industry faces several challenges and opportunities in the coming years, driven by advances in technology, changes in market demand, and increasing competition from low-cost manufacturers.
Miniaturization
One of the biggest challenges facing the PCB manufacturing industry is the trend towards miniaturization. As electronic devices become smaller and more powerful, the PCBs that power them must also become smaller and more complex.
This trend towards miniaturization poses several challenges for PCB manufacturers, including:
- Smaller feature sizes: As PCBs become smaller, the traces and spaces between them must also become smaller, pushing the limits of current manufacturing technologies.
- Higher layer counts: As PCBs become more complex, the number of layers required to route all the signals and power planes increases, requiring more advanced fabrication techniques and materials.
- Tighter tolerances: As PCBs become smaller and more complex, the tolerances for manufacturing defects and variations become tighter, requiring more advanced inspection and testing techniques.
High-Frequency Applications
Another trend driving the PCB manufacturing industry is the increasing demand for high-frequency applications, such as 5G wireless networks, automotive radar, and aerospace and defense systems.
High-frequency PCBs pose several challenges for manufacturers, including:
- Materials selection: High-frequency PCBs require specialized materials with low dielectric constant and loss tangent to minimize signal loss and distortion.
- Impedance control: High-frequency PCBs require careful control of the impedance of the traces and planes to ensure signal integrity and minimize reflections and crosstalk.
- Shielding and grounding: High-frequency PCBs require careful shielding and grounding techniques to minimize electromagnetic interference (EMI) and ensure compatibility with other systems.
Environmental Regulations
The PCB manufacturing industry is subject to increasingly stringent environmental regulations, driven by concerns over the use of hazardous materials and the disposal of waste products.
Some of the key environmental regulations affecting the PCB manufacturing industry include:
- Restriction of Hazardous Substances (RoHS): This European Union directive restricts the use of certain hazardous substances, such as lead, cadmium, and mercury, in electronic products.
- Waste Electrical and Electronic Equipment (WEEE): This European Union directive requires manufacturers to take responsibility for the collection, treatment, and disposal of waste electrical and electronic equipment.
- Registration, Evaluation, Authorization and Restriction of Chemicals (REACH): This European Union regulation requires manufacturers to register and evaluate the safety of the chemicals used in their products and to restrict or ban the use of certain hazardous substances.
Cost Pressures
The PCB manufacturing industry is subject to intense cost pressures, driven by increasing competition from low-cost manufacturers in Asia and the ongoing commoditization of many types of PCBs.
To remain competitive, PCB manufacturers must continually seek ways to reduce costs and improve efficiency, while maintaining high quality and reliability. Some of the strategies used by PCB manufacturers to reduce costs include:
- Automation: Automated manufacturing equipment and processes can help to reduce labor costs and improve consistency and quality.
- Lean manufacturing: Lean manufacturing techniques, such as just-in-time inventory management and continuous improvement, can help to reduce waste and improve efficiency.
- Supply chain optimization: Optimizing the supply chain, including sourcing materials and components from low-cost suppliers and consolidating shipments, can help to reduce costs and improve margins.
Opportunities for Innovation
Despite the challenges facing the PCB manufacturing industry, there are also many opportunities for innovation and growth. Some of the key opportunities for PCB manufacturers include:
- Advanced materials: The development of new materials, such as high-frequency laminates and flexible substrates, can enable new applications and designs for PCBs.
- 3D printing: The use of 3D printing technologies for PCB fabrication can enable faster prototyping and more complex geometries, as well as reduce waste and improve sustainability.
- Internet of Things (IoT): The growth of the IoT is driving demand for smaller, more complex, and more reliable PCBs, creating new opportunities for manufacturers that can meet these requirements.
- Robotics and automation: The increasing use of robotics and automation in manufacturing can help to reduce labor costs, improve consistency and quality, and enable new applications and designs for PCBs.
Frequently Asked Questions (FAQ)
- What is a PCB?
-
A PCB, or printed circuit board, is a flat board made of insulating material with conductive pathways printed on its surface. It is used to mechanically support and electrically connect electronic components using conductive tracks, pads, and other features etched from copper sheets laminated onto a non-conductive substrate.
-
What are the different types of PCBs?
-
There are several types of PCBs, including:
- Single-sided PCBs: These have conductive traces on only one side of the board.
- Double-sided PCBs: These have conductive traces on both sides of the board, with through-hole connections between the sides.
- Multi-layer PCBs: These have multiple layers of conductive traces separated by insulating layers, allowing for more complex connections and higher component density.
- Flexible PCBs: These are made from flexible materials and can bend and twist without breaking.
- Rigid-flex PCBs: These combine rigid and flexible sections to allow for more complex shapes and configurations.
-
What are the steps involved in PCB manufacturing?
- The PCB manufacturing process typically involves the following steps:
0 Comments