Introduction to PCB Stack Up Design
Printed Circuit Board (PCB) stack up design is a crucial aspect of PCB manufacturing that plays a significant role in determining the overall performance, reliability, and functionality of the final product. A well-designed PCB stack up ensures proper signal integrity, reduces electromagnetic interference (EMI), and minimizes manufacturing costs. In this article, we will explore eight essential rules for designing an effective PCB stack up.
Rule 1: Choose the Right Number of Layers
Factors to Consider When Selecting the Number of Layers
When designing a PCB stack up, the first step is to determine the appropriate number of layers. The number of layers depends on various factors, such as:
- Circuit complexity
- Signal speed
- Power requirements
- Cost constraints
- Board size
Common Layer Configurations
Here are some common layer configurations for PCBs:
Number of Layers | Typical Applications |
---|---|
2 | Simple, low-cost designs |
4 | Most common, suitable for moderate complexity |
6 to 8 | Complex designs with high-speed signals and power planes |
10 or more | High-density, high-performance applications |
Rule 2: Select the Appropriate Layer Arrangement
Signal Layer Placement
Once you have determined the number of layers, the next step is to arrange them effectively. Here are some guidelines for signal layer placement:
- Place signal layers close to the surface to minimize via length and improve signal integrity
- Alternate signal layers with ground or power planes to reduce crosstalk and provide shielding
- Group high-speed signals on inner layers to minimize EMI
Power and Ground Plane Placement
Power and ground planes play a crucial role in providing a low-impedance path for return currents and minimizing EMI. Consider the following when placing power and ground planes:
- Use dedicated planes for power and ground to reduce noise and improve signal quality
- Place power and ground planes adjacent to each other to create a Decoupling Capacitor effect
- Avoid splitting power and ground planes, as it can lead to impedance discontinuities
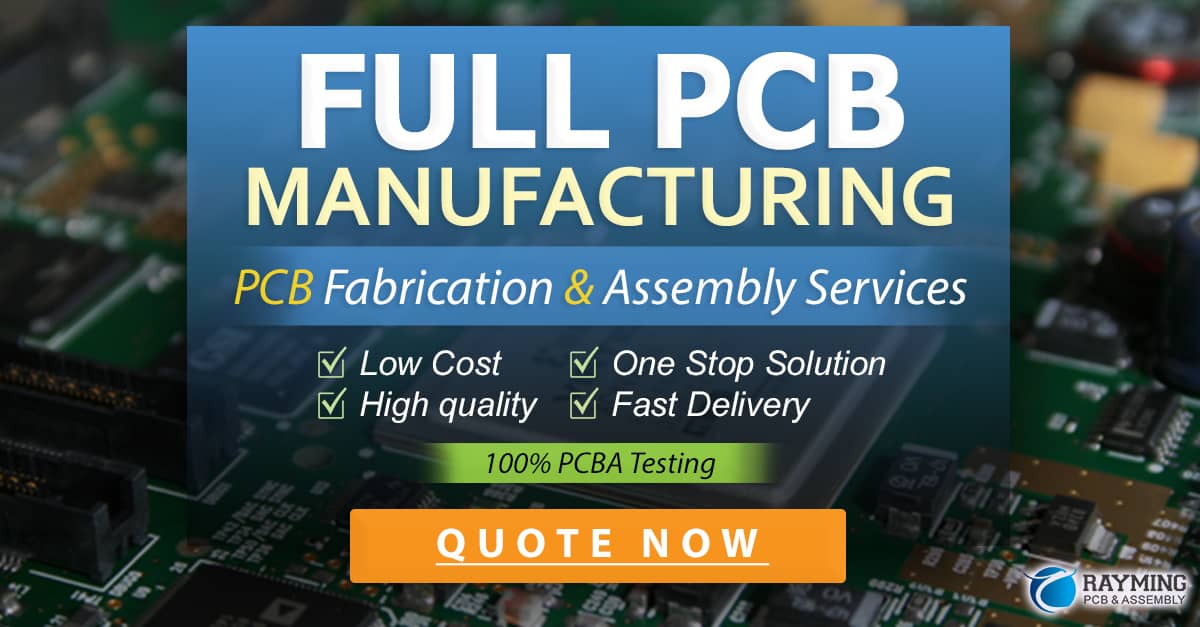
Rule 3: Determine the Appropriate Layer Thickness
Factors Affecting Layer Thickness
The thickness of each layer in a PCB stack up is determined by several factors, including:
- Signal speed and impedance requirements
- Current carrying capacity
- Manufacturing constraints
Common Layer Thicknesses
Here are some common layer thicknesses used in PCB stack ups:
Layer Type | Typical Thickness (mm) |
---|---|
Signal | 0.035 – 0.070 |
Power/Ground | 0.035 – 0.140 |
Dielectric | 0.075 – 0.200 |
Rule 4: Choose the Right Dielectric Material
Dielectric Material Properties
The dielectric material separates the conductive layers in a PCB stack up and plays a crucial role in determining the board’s electrical and mechanical properties. When selecting a dielectric material, consider the following properties:
- Dielectric constant (Dk): Affects signal speed and impedance
- Dissipation factor (Df): Influences signal loss and heat generation
- Thermal expansion coefficient: Impacts reliability and durability
Common Dielectric Materials
Here are some common dielectric materials used in PCB stack ups:
Material | Dk | Df | Thermal Expansion Coefficient (ppm/°C) |
---|---|---|---|
FR-4 | 4.2 | 0.020 | 12-16 |
Rogers RO4003C | 3.55 | 0.0027 | 11 |
Isola IS410 | 3.96 | 0.018 | 14-16 |
Rule 5: Implement Proper Grounding Techniques
Ground Plane Design
Proper grounding is essential for maintaining signal integrity and minimizing EMI. Here are some best practices for ground plane design:
- Use a continuous ground plane to provide a low-impedance return path for signals
- Avoid splitting the ground plane, as it can create ground loops and increase EMI
- Connect ground planes on different layers using vias to maintain continuity
Ground Via Placement
Ground vias play a crucial role in providing a low-impedance path between ground planes on different layers. Consider the following when placing ground vias:
- Place ground vias close to signal vias to minimize loop area and reduce inductance
- Use multiple ground vias in parallel to reduce impedance and improve current carrying capacity
- Avoid placing ground vias too close to the edge of the board to prevent manufacturing issues
Rule 6: Optimize Signal Integrity
Impedance Control
Maintaining consistent impedance throughout the signal path is crucial for ensuring signal integrity. Here are some tips for optimizing impedance control:
- Use controlled impedance traces for high-speed signals
- Match the impedance of traces to the source and load impedances
- Avoid abrupt changes in trace width or layer transitions, as they can cause impedance discontinuities
Crosstalk Reduction
Crosstalk occurs when signals on adjacent traces interfere with each other, leading to signal degradation. To minimize crosstalk, consider the following:
- Increase spacing between adjacent traces
- Use guard traces or ground planes between sensitive signals
- Route critical signals on different layers to minimize coupling
Rule 7: Consider Manufacturing Constraints
Minimum Feature Size
When designing a PCB stack up, it is essential to consider the manufacturing capabilities of your chosen PCB fabricator. Pay attention to the minimum feature sizes, such as:
- Minimum trace width and spacing
- Minimum via diameter and drill size
- Minimum Annular Ring
Layer Registration and Alignment
Ensure that your PCB stack up design accounts for layer registration and alignment tolerances. Misaligned layers can lead to manufacturing defects and reliability issues. Consider the following:
- Specify appropriate layer-to-layer registration tolerances
- Use Fiducial Marks to aid in layer alignment during manufacturing
- Allow for adequate clearance around vias and pads to accommodate alignment tolerances
Rule 8: Collaborate with Your PCB Manufacturer
Early Involvement
Involving your PCB manufacturer early in the design process can help you create a more manufacturable and cost-effective PCB stack up. Benefits of early collaboration include:
- Identifying potential manufacturing challenges early on
- Receiving guidance on material selection and layer configuration
- Optimizing the design for the manufacturer’s specific capabilities
Design for Manufacturing (DFM) Review
Before finalizing your PCB stack up design, request a Design for Manufacturing (DFM) review from your PCB manufacturer. A DFM review can help:
- Identify and resolve any design issues that may affect manufacturability
- Optimize the design for the manufacturer’s processes and equipment
- Ensure compliance with the manufacturer’s design guidelines
Frequently Asked Questions
1. What is the purpose of a PCB stack up?
A PCB stack up defines the arrangement of conductive layers, dielectric materials, and their thicknesses in a PCB. Its purpose is to ensure proper signal integrity, minimize EMI, and optimize the board’s electrical and mechanical properties.
2. How do I choose the right number of layers for my PCB?
The number of layers in a PCB stack up depends on various factors, such as circuit complexity, signal speed, power requirements, cost constraints, and board size. Choose the minimum number of layers that can accommodate your design requirements while considering manufacturability and cost.
3. What are the benefits of using dedicated power and ground planes?
Dedicated power and ground planes provide a low-impedance path for return currents, reduce noise, and improve signal quality. They also help minimize EMI by providing shielding between signal layers.
4. How does the dielectric material affect PCB Performance?
The dielectric material in a PCB stack up influences the board’s electrical and mechanical properties. The dielectric constant (Dk) affects signal speed and impedance, while the dissipation factor (Df) impacts signal loss and heat generation. The thermal expansion coefficient determines the board’s reliability and durability.
5. Why is collaboration with the PCB manufacturer important?
Collaborating with your PCB manufacturer early in the design process can help you create a more manufacturable and cost-effective PCB stack up. A Design for Manufacturing (DFM) review can identify potential issues, optimize the design for the manufacturer’s capabilities, and ensure compliance with their guidelines.
Conclusion
Designing an effective PCB stack up is a critical aspect of PCB manufacturing that directly impacts the performance, reliability, and functionality of the final product. By following the eight rules outlined in this article, you can create a well-designed PCB stack up that ensures proper signal integrity, reduces EMI, and minimizes manufacturing costs. Remember to choose the right number of layers, select the appropriate layer arrangement, determine the optimal layer thickness, choose the right dielectric material, implement proper grounding techniques, optimize signal integrity, consider manufacturing constraints, and collaborate with your PCB manufacturer. By adhering to these guidelines, you can develop a PCB stack up that meets your design requirements and exceeds performance expectations.
0 Comments