What is PCB Stackup?
PCB stackup refers to the arrangement of copper and insulating layers that make up a printed circuit board (PCB). It is a critical aspect of PCB Design as it directly impacts the performance, reliability, and manufacturability of the final product. A well-designed PCB stackup ensures proper signal integrity, power delivery, and mechanical stability while minimizing electromagnetic interference (EMI) and signal crosstalk.
Factors to Consider When Designing PCB Stackup
When designing a PCB stackup, several key factors must be considered to ensure optimal performance and manufacturability. These include:
1. Number of Layers
The number of layers in a PCB stackup is determined by the complexity of the circuit and the space constraints of the final product. More layers allow for higher component density and better signal routing but increase manufacturing costs. Common layer counts include:
Layer Count | Typical Applications |
---|---|
1 | Simple, low-cost projects |
2 | Double-sided boards for low-complexity circuits |
4 | Most common for general-purpose PCBs |
6-8 | Complex digital circuits, such as microcontrollers |
10+ | High-speed, high-density boards for advanced applications |
2. Layer Arrangement
The arrangement of copper and insulating layers in a PCB stackup plays a crucial role in signal integrity and EMI performance. A typical 4-layer stackup might consist of:
Layer | Function |
---|---|
Top | Signal layer, components |
Inner | Power plane (VCC) |
Inner | Ground plane (GND) |
Bottom | Signal layer, components |
This arrangement provides a low-impedance power delivery network and helps minimize EMI by sandwiching signal layers between power and ground planes.
3. Material Selection
The choice of materials for the PCB Substrate and copper layers affects the electrical, thermal, and mechanical properties of the board. Common substrate materials include:
- FR-4: A flame-retardant glass-reinforced epoxy laminate, widely used for general-purpose PCBs.
- Rogers: High-frequency laminates with low dielectric loss, suitable for RF and microwave applications.
- Polyimide: Flexible substrates for applications requiring bendable or conformable PCBs.
Copper thickness is typically specified in ounces per square foot (oz/ft²), with common values ranging from 0.5 oz/ft² to 2 oz/ft². Thicker copper layers provide better current-carrying capacity but may increase manufacturing costs.
4. Impedance Control
Controlling the characteristic impedance of transmission lines is essential for maintaining signal integrity in high-speed digital circuits. This is achieved by carefully selecting the dielectric thickness, copper width, and spacing between signal traces and reference planes. Common controlled impedance values include:
Impedance (Ω) | Application |
---|---|
50 | USB, Ethernet, RF circuits |
75 | Video, coaxial cables |
90-120 | High-speed digital logic (e.g., DDR memory) |
Impedance control requires close collaboration with the PCB manufacturer to ensure the desired values are achieved within acceptable tolerances.
Designing a PCB Stackup
With the key factors in mind, designing a PCB stackup involves the following steps:
- Determine the required number of layers based on the circuit complexity and space constraints.
- Arrange the layers to optimize signal integrity, power delivery, and EMI performance. This typically involves placing signal layers adjacent to power or ground planes.
- Select appropriate materials for the substrate and copper layers based on the electrical, thermal, and mechanical requirements of the application.
- Specify the copper thickness for each layer, considering current-carrying capacity and manufacturing constraints.
- Calculate the required dielectric thickness and trace geometry to achieve the desired controlled impedance values for critical signal paths.
- Collaborate with the PCB manufacturer to ensure the stackup design is feasible and meets the required specifications and tolerances.
Here’s an example of a 6-layer PCB stackup for a high-speed digital circuit:
Layer | Material | Thickness (mm) | Copper (oz/ft²) | Function |
---|---|---|---|---|
Top | FR-4 | 0.10 | 1.0 | Signal, components |
L2 | FR-4 | 0.25 | 0.5 | Signal |
L3 | FR-4 | 0.36 | 1.0 | Power plane (VCC) |
L4 | FR-4 | 0.36 | 1.0 | Ground plane (GND) |
L5 | FR-4 | 0.25 | 0.5 | Signal |
Bottom | FR-4 | 0.10 | 1.0 | Signal, components |
In this stackup, the signal layers are adjacent to power and ground planes to minimize EMI and ensure a low-impedance power delivery network. The dielectric thicknesses and copper weights are chosen to achieve the desired controlled impedance values and current-carrying capacity.
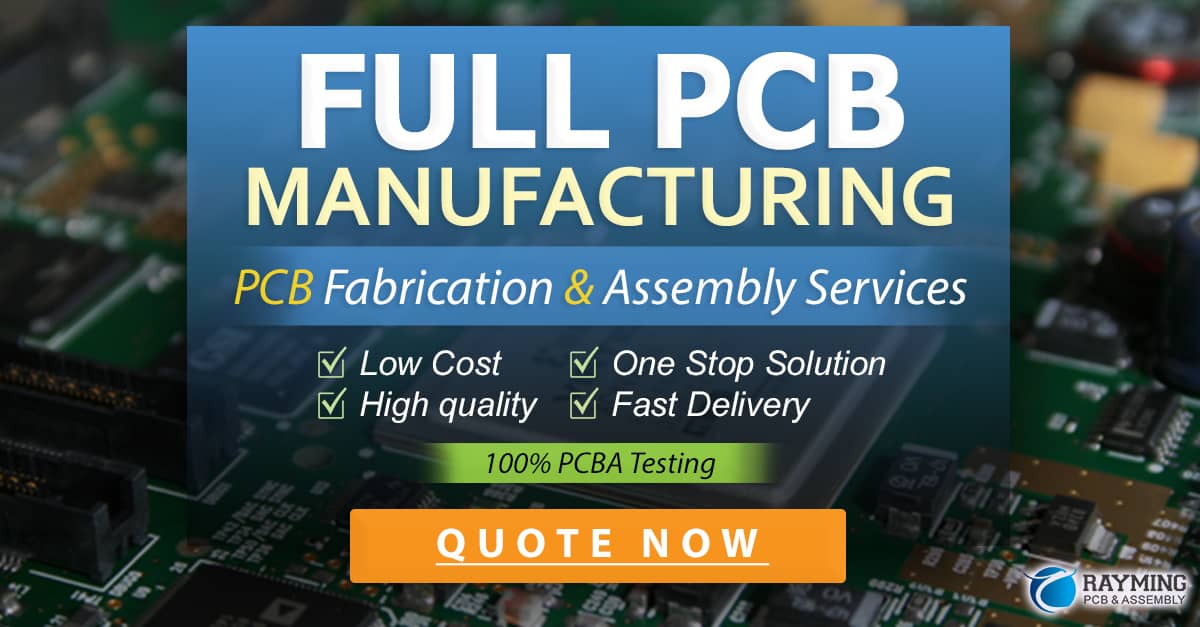
Verifying and Validating the PCB Stackup
Once the PCB stackup is designed, it is essential to verify and validate its performance through simulation and physical testing. This involves:
- Performing signal integrity simulations to ensure the desired controlled impedance values are achieved and signal quality is maintained throughout the board.
- Conducting power integrity simulations to verify that the power delivery network provides adequate current to all components with minimal voltage drop and ripple.
- Analyzing EMI performance through electromagnetic field simulations to identify potential sources of radiation and ensure compliance with relevant EMC standards.
- Fabricating prototype boards and performing physical measurements to validate the simulation results and ensure the stackup meets the required specifications.
By thoroughly verifying and validating the PCB stackup, designers can identify and address potential issues early in the development process, reducing the risk of costly redesigns and delays.
Conclusion
Designing a PCB stackup is a critical aspect of PCB design that directly impacts the performance, reliability, and manufacturability of the final product. By carefully considering factors such as the number of layers, layer arrangement, material selection, and impedance control, designers can create stackups that optimize signal integrity, power delivery, and EMI performance. Collaborating closely with PCB manufacturers and validating the stackup through simulation and physical testing ensures that the final product meets the required specifications and performs as intended.
FAQ
1. What is the difference between a power plane and a ground plane in a PCB stackup?
A power plane is a copper layer that provides a low-impedance distribution of a specific voltage level (e.g., VCC) to components on the PCB. A ground plane, on the other hand, serves as a common reference point for all signals and helps minimize EMI by providing a low-impedance return path for currents.
2. Why is impedance control important in PCB stackup design?
Impedance control is essential for maintaining signal integrity in high-speed digital circuits. By carefully controlling the characteristic impedance of transmission lines, designers can ensure that signals propagate with minimal reflections, distortions, and crosstalk, reducing the risk of communication errors and system failures.
3. How does the choice of substrate material affect PCB Performance?
The substrate material determines the electrical, thermal, and mechanical properties of the PCB. For example, FR-4 is a common choice for general-purpose PCBs due to its good dielectric properties, thermal stability, and cost-effectiveness. However, for high-frequency applications, materials like Rogers laminates may be preferred due to their lower dielectric loss and better-controlled dielectric constant.
4. What are the advantages of using thicker copper layers in a PCB stackup?
Thicker copper layers provide better current-carrying capacity, which is essential for power delivery and high-current applications. They also help improve thermal dissipation and mechanical stability of the PCB. However, thicker copper layers can increase manufacturing costs and may require adjustments to the stackup design to maintain the desired controlled impedance values.
5. How can PCB designers ensure that their stackup is manufacturable?
To ensure manufacturability, PCB designers should collaborate closely with their chosen PCB manufacturer throughout the design process. This involves discussing the desired layer count, material selection, copper weights, and controlled impedance requirements to ensure that the stackup is feasible and meets the manufacturer’s capabilities and tolerances. Designers should also adhere to industry-standard design guidelines and consider the manufacturer’s specific design rules and constraints.
0 Comments