Introduction to QFN and QFP Packages
QFN (Quad Flat No-lead) and QFP (Quad Flat Package) are two of the most common surface-mount package types used in modern electronic devices. These packages offer several advantages over traditional through-hole packages, including smaller size, better thermal and electrical performance, and lower manufacturing costs. However, to ensure optimal performance and reliability, it is crucial to select the right Surface Finish for these packages.
What are QFN and QFP Packages?
-
QFN Packages: QFN packages are leadless, meaning they do not have external leads extending from the package body. Instead, the electrical contacts are located on the bottom surface of the package, allowing for a smaller footprint and improved thermal performance. QFN packages are commonly used in applications requiring high density and low power consumption, such as mobile devices, wearables, and IoT devices.
-
QFP Packages: QFP packages have leads extending from all four sides of the package body, providing a larger footprint compared to QFN packages. QFP packages are available in various sizes and lead counts, making them suitable for a wide range of applications, from consumer electronics to industrial and automotive systems.
Surface Finishes for QFN and QFP Packages
When it comes to selecting a surface finish for QFN and QFP packages, two of the most common options are HASL (Hot Air Solder Leveling) and ENIG (Electroless Nickel Immersion Gold). Each surface finish has its own advantages and disadvantages, which should be considered based on the specific requirements of the application.
HASL (Hot Air Solder Leveling)
HASL is a widely used surface finish in the electronics industry, offering several benefits:
-
Cost-effective: HASL is generally less expensive compared to other surface finishes, making it an attractive option for budget-conscious projects.
-
Excellent solderability: The solder coating provided by HASL ensures good wettability and solderability, facilitating reliable solder joint formation during the assembly process.
-
Compatibility: HASL is compatible with a wide range of soldering processes, including Wave Soldering, Reflow soldering, and hand soldering.
However, HASL also has some limitations:
-
Uneven surface: The hot air leveling process can result in an uneven surface, which may cause issues with fine-pitch components or high-density designs.
-
Thermal shock: The high temperature involved in the HASL process can cause thermal shock to the PCB and components, potentially leading to warpage or damage.
-
Limited shelf life: The solder coating of HASL can oxidize over time, reducing its solderability and requiring additional processing before assembly.
ENIG (Electroless Nickel Immersion Gold)
ENIG is a high-performance surface finish that offers several advantages over HASL:
-
Flat and uniform surface: The electroless nickel and immersion gold plating process creates a flat and uniform surface, which is ideal for fine-pitch components and high-density designs.
-
Extended shelf life: The gold layer in ENIG provides excellent oxidation resistance, allowing for a longer shelf life and better solderability over time.
-
Improved Wire Bonding: The gold surface of ENIG is well-suited for wire bonding applications, making it a preferred choice for packages requiring this assembly technique.
However, ENIG also has some drawbacks:
-
Higher cost: The multi-step plating process and the use of gold make ENIG more expensive compared to HASL.
-
Black pad issue: In some cases, the interaction between the nickel and gold layers can lead to a “black pad” phenomenon, which can cause solderability issues and reduced reliability.
-
Mechanical stress: The nickel layer in ENIG can introduce additional mechanical stress to the PCB, which may cause issues in high-reliability applications.
Factors to Consider When Choosing Between HASL and ENIG
When deciding between HASL and ENIG for QFN and QFP packages, several factors should be considered:
-
Application requirements: The specific requirements of the application, such as environmental conditions, reliability expectations, and performance demands, should be the primary driver for selecting the appropriate surface finish.
-
Package type and pitch: The package type (QFN or QFP) and the lead pitch should be considered when choosing between HASL and ENIG. Fine-pitch packages and high-density designs may benefit from the flat and uniform surface provided by ENIG.
-
Cost considerations: The budget allocated for the project should be taken into account when selecting the surface finish. HASL is generally more cost-effective, while ENIG offers superior performance at a higher cost.
-
Manufacturing process: The compatibility of the surface finish with the manufacturing process, including soldering techniques and assembly equipment, should be evaluated to ensure a smooth and reliable production process.
-
Shelf life and storage: If the PCBs or components are expected to be stored for an extended period before assembly, ENIG may be the preferred choice due to its better oxidation resistance and longer shelf life.
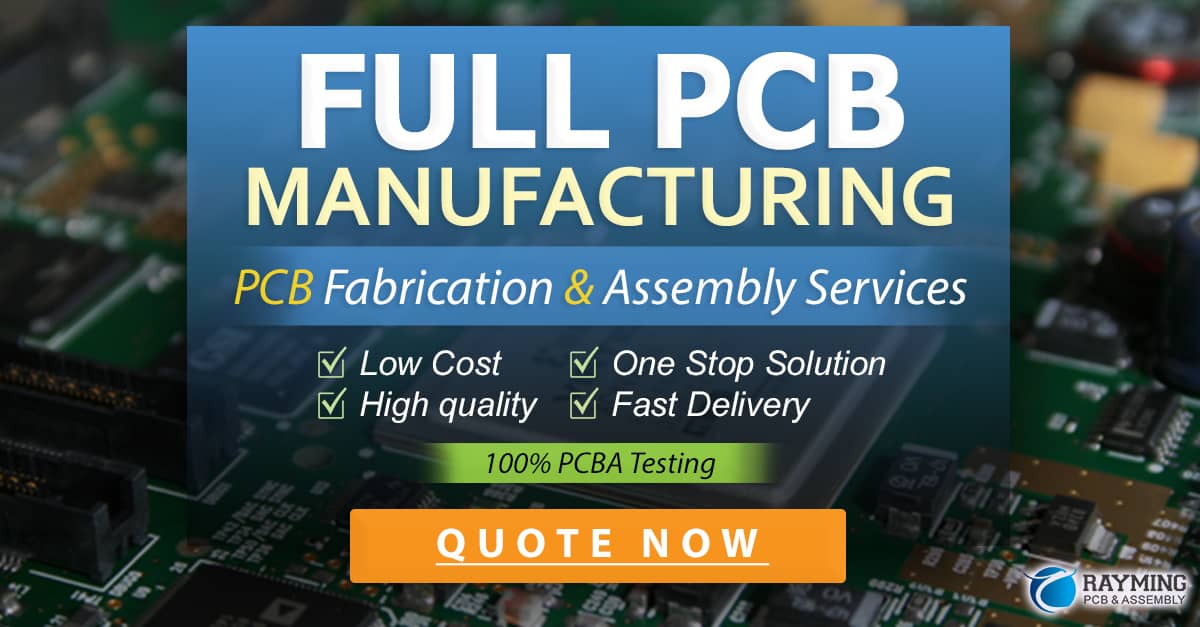
Comparison Table: HASL vs. ENIG for QFN and QFP Packages
Factor | HASL | ENIG |
---|---|---|
Cost | Lower | Higher |
Surface uniformity | Uneven | Flat and uniform |
Solderability | Good | Excellent |
Shelf life | Limited | Extended |
Compatibility | Wide range | Limited by black pad issue |
Thermal shock | Potential issue | Minimal |
Wire bonding | Not suitable | Suitable |
Mechanical stress | Minimal | Higher |
FAQ
1. Can HASL be used for fine-pitch QFN packages?
While HASL can be used for QFN packages, it may not be the best choice for fine-pitch designs due to its uneven surface. ENIG is generally recommended for fine-pitch QFN packages to ensure better solderability and reliability.
2. Is ENIG always the better choice for QFP packages?
Not necessarily. The choice between HASL and ENIG for QFP packages depends on various factors, such as the specific application requirements, lead pitch, and cost considerations. In some cases, HASL may be sufficient and more cost-effective for QFP packages.
3. How can the black pad issue in ENIG be mitigated?
The black pad issue in ENIG can be mitigated by properly controlling the plating process parameters, such as the nickel and gold thickness, plating time, and bath chemistry. Additionally, using a suitable PCB base material and designing the PCB with appropriate pad geometries can help minimize the risk of black pad formation.
4. Can HASL and ENIG be used together on the same PCB?
Yes, it is possible to use both HASL and ENIG on the same PCB, depending on the specific requirements of different components and areas of the board. However, this may increase the complexity and cost of the manufacturing process.
5. Are there any other surface finishes suitable for QFN and QFP packages?
Yes, there are other surface finishes that can be used for QFN and QFP packages, such as Immersion Silver (IAg), Immersion Tin (ISn), and Organic Solderability Preservative (OSP). Each of these surface finishes has its own advantages and disadvantages, and the choice depends on the specific requirements of the application and the manufacturing process.
Conclusion
Selecting the right surface finish for QFN and QFP packages is crucial for ensuring optimal performance, reliability, and manufacturability. HASL and ENIG are two of the most common surface finishes used in the electronics industry, each with its own set of advantages and disadvantages.
When choosing between HASL and ENIG, it is essential to consider factors such as application requirements, package type and pitch, cost considerations, manufacturing process compatibility, and shelf life. By carefully evaluating these factors and understanding the trade-offs involved, designers and manufacturers can make an informed decision that balances performance, reliability, and cost for their specific project.
Ultimately, the choice between HASL and ENIG for QFN and QFP packages depends on the unique needs of each application. By working closely with PCB Fabrication and assembly partners, and staying up-to-date with the latest industry trends and best practices, engineers can ensure that they select the most appropriate surface finish for their QFN and QFP packages, leading to successful and reliable electronic products.
0 Comments