Understanding Trace Width and Tolerance in PCB Design
What is Trace Width?
Trace width refers to the width of the copper tracks on a printed circuit board (PCB). These traces are used to electrically connect various components on the board, such as resistors, capacitors, and integrated circuits. The width of the traces is critical in determining the current-carrying capacity, resistance, and impedance of the circuit.
Why is Trace Width Important?
Trace width is important for several reasons:
- Current-carrying capacity: The wider the trace, the more current it can carry without overheating or causing voltage drops.
- Resistance: Narrower traces have higher resistance, which can lead to voltage drops and signal integrity issues.
- Impedance: Trace width, along with other factors such as the dielectric material and thickness, determines the characteristic impedance of the trace, which is critical for high-speed signals.
Factors Affecting Trace Width
Several factors influence the choice of trace width in PCB design:
- Current requirements: The amount of current flowing through the trace determines the minimum width required to prevent overheating and voltage drops.
- Signal integrity: High-speed signals require careful control of trace impedance to minimize reflections and signal distortion.
- Manufacturing constraints: The minimum trace width is limited by the capabilities of the PCB manufacturing process.
- Board space: Wider traces occupy more space on the PCB, which can be a constraint in dense designs.
Calculating Trace Width
To calculate the appropriate trace width for a given current requirement, designers can use various tools and formulas. One common method is to use the IPC-2221 standard, which provides guidelines for trace width based on the current, temperature rise, and copper thickness.
For example, consider a trace carrying 1A of current on a 1oz copper PCB with a maximum temperature rise of 10°C. Using the IPC-2221 standard, the minimum trace width can be calculated as follows:
Current (A) | Copper Thickness (oz) | Temperature Rise (°C) | Minimum Trace Width (mm) |
---|---|---|---|
1 | 1 | 10 | 0.2 |
In this case, a trace width of at least 0.2mm would be required to safely carry 1A of current.
Trace Width Tolerance
What is Trace Width Tolerance?
Trace width tolerance refers to the acceptable variation in the width of the copper traces on a PCB. Due to manufacturing limitations, it is not possible to produce traces with exactly the specified width. Instead, manufacturers specify a tolerance range within which the actual trace width must fall.
Why is Trace Width Tolerance Important?
Trace width tolerance is important for several reasons:
- Current-carrying capacity: If the actual trace width is smaller than the specified width, the current-carrying capacity of the trace may be reduced, leading to overheating and voltage drops.
- Impedance control: For high-speed signals, variations in trace width can cause changes in the characteristic impedance of the trace, leading to signal integrity issues.
- Manufacturing yield: If the trace width tolerance is too tight, it can lead to increased manufacturing costs and reduced yield.
Specifying Trace Width Tolerance
When specifying trace width tolerance, designers typically use a combination of absolute and relative values. For example, a trace width might be specified as 0.2mm ±0.05mm, meaning that the actual trace width must be between 0.15mm and 0.25mm.
The choice of trace width tolerance depends on several factors:
- Manufacturing capabilities: Different PCB manufacturers have different capabilities in terms of minimum trace width and tolerance.
- Design requirements: High-speed designs or designs with tight impedance control requirements may require tighter trace width tolerances.
- Cost: Tighter tolerances generally increase manufacturing costs, so designers must balance performance requirements with cost constraints.
Impact of Trace Width Tolerance on Impedance
For high-speed signals, trace width tolerance can have a significant impact on the characteristic impedance of the trace. The characteristic impedance of a microstrip trace is given by:
Z₀ = 87 / √(εᵣ + 1.41) × ln(5.98h / (0.8w + t))
Where:
– Z₀ is the characteristic impedance in ohms
– εᵣ is the dielectric constant of the PCB material
– h is the thickness of the dielectric in mm
– w is the width of the trace in mm
– t is the thickness of the copper in mm
As can be seen from the formula, variations in trace width (w) can cause changes in the characteristic impedance. For example, consider a microstrip trace with the following parameters:
- εᵣ = 4.5
- h = 0.2mm
- w = 0.2mm
- t = 0.035mm
Using the formula above, the nominal characteristic impedance is calculated as:
Z₀ = 87 / √(4.5 + 1.41) × ln(5.98 × 0.2 / (0.8 × 0.2 + 0.035)) ≈ 50Ω
Now, consider the impact of a trace width tolerance of ±0.05mm. The minimum and maximum characteristic impedances can be calculated as:
Z₀_min = 87 / √(4.5 + 1.41) × ln(5.98 × 0.2 / (0.8 × 0.15 + 0.035)) ≈ 54Ω
Z₀_max = 87 / √(4.5 + 1.41) × ln(5.98 × 0.2 / (0.8 × 0.25 + 0.035)) ≈ 46Ω
In this case, the trace width tolerance of ±0.05mm results in a characteristic impedance range of 46Ω to 54Ω, which may be acceptable for some designs but not for others.
Controlling Trace Width and Tolerance
Design Techniques
To control trace width and tolerance, designers can use various techniques:
- Impedance calculators: Many PCB design tools include impedance calculators that can help designers determine the appropriate trace width and spacing for a given impedance.
- Controlled impedance routing: Some PCB design tools offer controlled impedance routing features that automatically adjust trace width and spacing to maintain a target impedance.
- Design rules: Designers can create design rules that specify minimum and maximum trace widths, spacings, and tolerances for different signal types and layers.
Manufacturing Techniques
PCB manufacturers can also use various techniques to control trace width and tolerance:
- Etching process: The choice of etching process (e.g., wet etching, plasma etching) can impact the minimum achievable trace width and tolerance.
- Copper thickness: Using thicker copper can help reduce the impact of trace width variations on impedance.
- Controlled impedance materials: Some PCB materials are specifically designed for controlled impedance applications and can help reduce the impact of trace width variations.
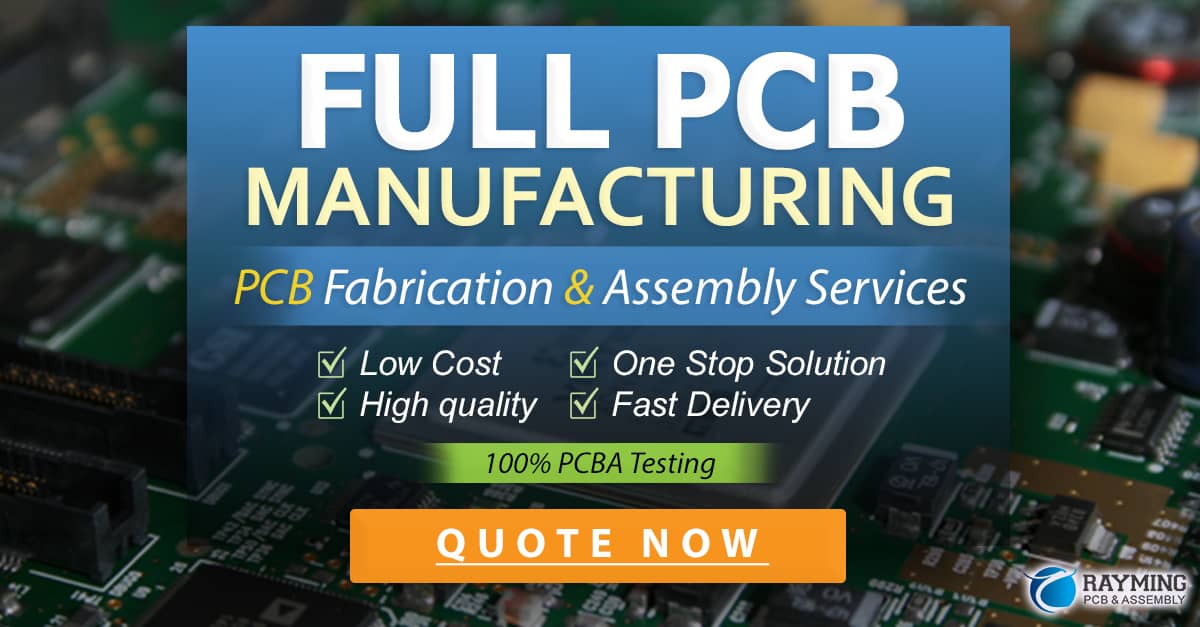
FAQ
1. What is the minimum trace width that can be manufactured?
The minimum trace width depends on the capabilities of the PCB manufacturer and the chosen fabrication process. In general, most manufacturers can produce trace widths down to 0.1mm (4 mil) or smaller, but this may increase costs and reduce yields.
2. How does trace width affect signal integrity?
Trace width can affect signal integrity in several ways:
- Narrower traces have higher resistance, which can lead to voltage drops and signal attenuation.
- Variations in trace width can cause changes in characteristic impedance, leading to reflections and signal distortion.
- Narrower traces are more susceptible to crosstalk and electromagnetic interference (EMI).
3. What is the relationship between trace width and current-carrying capacity?
The current-carrying capacity of a trace is proportional to its cross-sectional area, which is determined by the trace width and copper thickness. Wider traces can carry more current without overheating or causing voltage drops.
4. How can I calculate the appropriate trace width for my design?
To calculate the appropriate trace width, designers can use various tools and standards such as the IPC-2221 standard, which provides guidelines for trace width based on current, temperature rise, and copper thickness. Many PCB design tools also include trace width calculators that can help automate this process.
5. What are the trade-offs between trace width and board space?
Wider traces occupy more space on the PCB, which can be a constraint in dense designs. Designers must balance the need for sufficient current-carrying capacity and signal integrity with the available board space. In some cases, it may be necessary to use narrower traces or multiple layers to accommodate all the required traces.
Conclusion
Trace width and tolerance are critical aspects of PCB design that can have a significant impact on the performance, reliability, and manufacturing yield of the final product. By understanding the factors that influence trace width and tolerance, and by using appropriate design and manufacturing techniques, designers can ensure that their PCBs meet the required specifications and perform as intended.
As PCB technology continues to evolve, with faster signal speeds, smaller components, and denser layouts, the importance of trace width and tolerance will only continue to grow. Designers who stay up-to-date with the latest tools, techniques, and standards will be well-positioned to meet these challenges and create PCBs that are both functional and manufacturable.
0 Comments