Introduction
Custom LED PCB Assembly is a complex process that requires precise planning, execution, and quality control. Failure to properly manage any stage of the process can lead to costly delays, defects, and even complete project failure. In this article, we’ll discuss seven key strategies to help prevent the case of failing custom LED PCB assembly.
1. Choose the Right PCB Manufacturer
Factors to Consider When Selecting a PCB Manufacturer
Factor | Description |
---|---|
Experience | Look for a manufacturer with extensive experience in LED PCB assembly. |
Quality Control | Ensure the manufacturer has robust quality control processes in place. |
Technology | Choose a manufacturer with state-of-the-art equipment and technology. |
Communication | Select a manufacturer with clear communication channels and responsive support. |
Cost | Consider the cost of the manufacturer’s services, but don’t sacrifice quality for price. |
Choosing the right PCB manufacturer is critical to the success of your custom LED PCB assembly project. Take the time to research and compare potential manufacturers to find one that meets your specific needs and requirements.
2. Design for Manufacturability
Key Aspects of Designing for Manufacturability
- Component Selection
- Choose components that are readily available and compatible with the manufacturing process.
-
Avoid using obsolete or hard-to-find components.
- Design the PCB layout with manufacturing in mind, considering factors such as component placement, trace spacing, and via size.
-
Follow the manufacturer’s design guidelines to ensure compatibility with their processes.
-
Thermal Management
- Incorporate proper thermal management techniques, such as using thermal vias and heat sinks, to prevent overheating and ensure optimal LED performance.
Designing for manufacturability is essential to prevent issues during the assembly process. Work closely with your PCB manufacturer to ensure your design is optimized for their specific manufacturing capabilities.
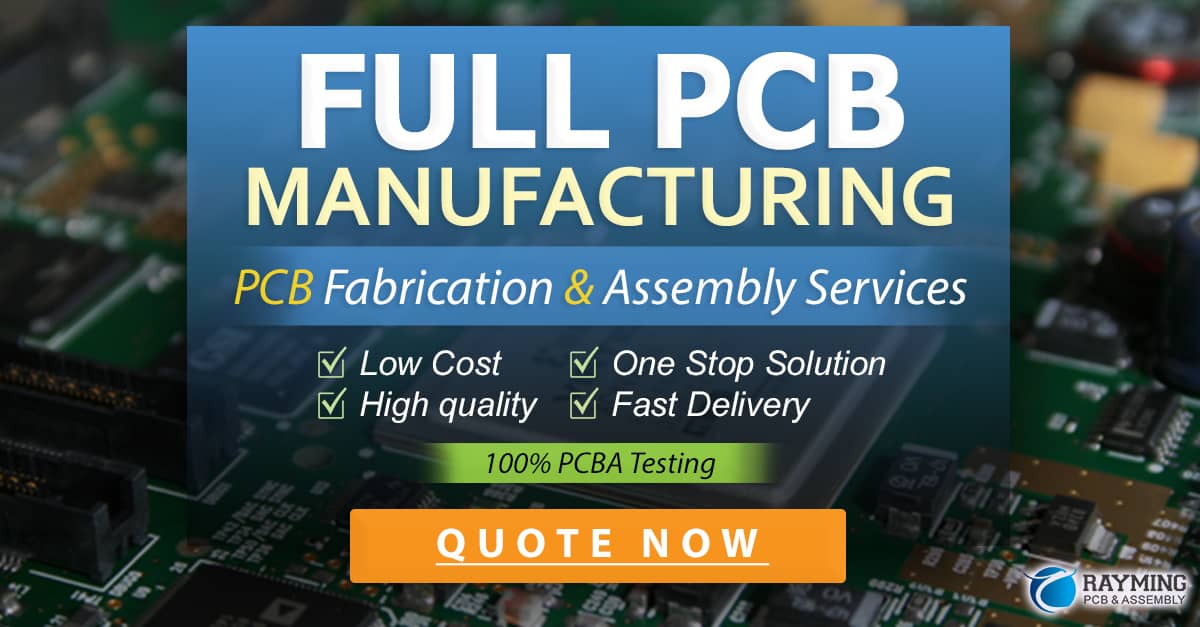
3. Conduct Thorough Testing and Quality Control
Types of Testing and Quality Control Measures
Test/Measure | Description |
---|---|
Visual Inspection | Visually inspect the PCBs for defects such as poor soldering, damaged components, or incorrect component placement. |
Functional Testing | Test the PCBs to ensure they function as intended, including LED brightness, color accuracy, and power consumption. |
Burn-In Testing | Subject the PCBs to extended periods of operation to identify any potential long-term issues or failures. |
X-Ray Inspection | Use X-ray imaging to detect internal defects, such as voids in solder joints or damaged traces. |
Quality Control Audits | Regularly audit the manufacturing process to ensure adherence to quality standards and identify areas for improvement. |
Implementing a comprehensive testing and quality control program is crucial to catching defects early and preventing them from reaching the end user. Work with your PCB manufacturer to develop a testing plan that meets your specific quality requirements.
4. Manage Your Bill of Materials (BOM)
Tips for Effective BOM Management
- Maintain Accurate and Up-to-Date BOMs
- Ensure your BOMs include all necessary components and accurately reflect the current design.
-
Update BOMs promptly when changes are made to the design or component selection.
-
Use Consistent Naming Conventions
- Employ consistent naming conventions for components to avoid confusion and errors.
-
Use industry-standard part numbers when possible to ensure compatibility with the manufacturer’s systems.
-
Collaborate with Your PCB Manufacturer
- Share your BOM with your PCB manufacturer early in the process to ensure they can source all necessary components.
- Work with the manufacturer to identify potential component substitutions or alternatives if needed.
Effective BOM management is essential to prevent component shortages, delays, and compatibility issues during the assembly process. Maintain clear communication with your PCB manufacturer to ensure your BOM is accurate and up-to-date.
5. Plan for Adequate Lead Times
Factors Affecting Lead Times
Factor | Description |
---|---|
Component Availability | Some components may have longer lead times due to limited availability or high demand. |
Manufacturing Capacity | The PCB manufacturer’s production capacity and workload can impact lead times. |
Shipping and Logistics | Shipping times and customs clearance can add significant delays, especially for international orders. |
Design Complexity | More complex designs may require additional manufacturing time or specialized processes. |
Planning for adequate lead times is crucial to prevent delays and ensure your project stays on schedule. Work closely with your PCB manufacturer to understand their lead times and plan accordingly.
6. Communicate Clearly and Effectively
Best Practices for Communication
- Establish Clear Communication Channels
- Identify key points of contact at your organization and the PCB manufacturer.
-
Set up regular meetings or status updates to keep all parties informed of progress and any issues that arise.
-
Provide Detailed Documentation
- Supply your PCB manufacturer with comprehensive documentation, including design files, BOMs, and assembly instructions.
-
Ensure all documents are clear, accurate, and up-to-date.
-
Be Responsive to Inquiries
- Promptly respond to any questions or concerns raised by your PCB manufacturer.
- Be proactive in addressing potential issues or roadblocks to keep the project moving forward.
Clear and effective communication is essential to preventing misunderstandings, delays, and errors during the custom LED PCB assembly process. Foster a collaborative relationship with your PCB manufacturer to ensure everyone is working towards the same goals.
7. Continuously Monitor and Improve the Process
Strategies for Continuous Improvement
- Collect and Analyze Data
- Gather data on key metrics such as defect rates, lead times, and cost.
-
Analyze this data to identify trends and areas for improvement.
-
Implement Corrective Actions
- Develop and implement corrective action plans to address identified issues.
-
Monitor the effectiveness of these actions and adjust as needed.
-
Seek Feedback from Stakeholders
- Actively seek feedback from your team, end-users, and the PCB manufacturer.
- Use this feedback to drive improvements in the design, manufacturing, and quality control processes.
Continuously monitoring and improving the custom LED PCB assembly process is essential to preventing future failures and ensuring long-term success. Embrace a culture of continuous improvement and work closely with your PCB manufacturer to implement necessary changes.
Conclusion
Preventing the case of failing custom LED PCB assembly requires a comprehensive approach that encompasses careful planning, effective communication, and continuous improvement. By following the seven strategies outlined in this article, you can minimize the risk of defects, delays, and project failure, ultimately ensuring the success of your custom LED PCB assembly project.
Frequently Asked Questions (FAQ)
-
Q: How do I choose the right PCB manufacturer for my custom LED PCB assembly project?
A: When selecting a PCB manufacturer, consider factors such as experience, quality control processes, technology, communication, and cost. Research and compare potential manufacturers to find one that best meets your specific needs and requirements. -
Q: What is designing for manufacturability, and why is it important?
A: Designing for manufacturability involves optimizing your PCB design to ensure compatibility with the manufacturing process. This includes selecting appropriate components, designing the PCB layout with manufacturing in mind, and incorporating proper thermal management techniques. Designing for manufacturability helps prevent issues during the assembly process and ensures a smoother, more efficient production run. -
Q: What types of testing and quality control measures should I implement for my custom LED PCB assembly project?
A: A comprehensive testing and quality control program should include visual inspection, functional testing, burn-in testing, X-ray inspection, and regular quality control audits. Work with your PCB manufacturer to develop a testing plan that meets your specific quality requirements and helps catch defects early in the process. -
Q: How can I effectively manage my Bill of Materials (BOM) to prevent issues during the assembly process?
A: To effectively manage your BOM, maintain accurate and up-to-date BOMs, use consistent naming conventions, and collaborate with your PCB manufacturer. Share your BOM with the manufacturer early in the process to ensure they can source all necessary components and identify potential substitutions or alternatives if needed. -
Q: Why is continuous monitoring and improvement important for the custom LED PCB assembly process?
A: Continuously monitoring and improving the custom LED PCB assembly process helps prevent future failures and ensures long-term success. By collecting and analyzing data, implementing corrective actions, and seeking feedback from stakeholders, you can identify areas for improvement and drive necessary changes in the design, manufacturing, and quality control processes.
0 Comments