What is PCB Panelization?
PCB panelization is the process of arranging multiple identical or different PCB designs on a single, larger panel for manufacturing purposes. This approach enables manufacturers to produce several PCBs simultaneously, reducing production time and costs. The panelized PCBs are held together by a frame and connected by breakaway tabs, which are later removed to separate the individual boards after the assembly process.
Why is PCB Panelization Important?
PCB panelization offers several benefits to both designers and manufacturers:
- Cost reduction: By producing multiple PCBs on a single panel, manufacturers can optimize material usage and minimize setup time, resulting in lower production costs.
- Improved efficiency: Panelization allows for the simultaneous fabrication and assembly of multiple PCBs, reducing overall production time.
- Enhanced quality: Properly designed panelization ensures consistent quality across all PCBs on the panel, minimizing the risk of defects and improving yield.
- Simplified handling: Panelized PCBs are easier to handle and transport throughout the manufacturing process, reducing the risk of damage to individual boards.
Key Considerations for PCB Panelization Design
When designing a PCB panel, there are several factors to consider to ensure optimal results:
1. Panel Size and Material
The first step in PCB panelization is determining the appropriate panel size and material. Standard panel sizes vary depending on the manufacturer and production equipment, but common sizes include:
Panel Size | Dimensions (mm) |
---|---|
Small | 229 x 305 |
Medium | 305 x 457 |
Large | 457 x 610 |
The choice of panel material depends on the specific requirements of the PCB, such as thermal stability, mechanical strength, and dielectric properties. Common panel materials include:
- FR-4: A glass-reinforced epoxy laminate, widely used for its good mechanical and electrical properties.
- Aluminum: Used for PCBs that require excellent thermal dissipation, such as high-power LED applications.
- Polyimide: Offers high temperature resistance and flexibility, suitable for flexible PCBs.
2. Board Orientation and Spacing
When arranging PCBs on a panel, designers must consider the orientation and spacing of the boards to ensure optimal material utilization and minimize waste. The two main board orientations are:
- Horizontal: PCBs are placed side by side on the panel.
- Vertical: PCBs are placed top to bottom on the panel.
The spacing between boards, known as the “street width,” should be sufficient to accommodate the cutting tool and prevent damage to the PCBs during the depaneling process. A typical street width ranges from 2 mm to 5 mm, depending on the cutting method and board thickness.
3. Breakaway Tabs and Mouse Bites
Breakaway tabs, also known as “mouse bites,” are small, perforated sections that connect the individual PCBs to the panel frame. These tabs hold the boards securely during the manufacturing process and are later removed to separate the PCBs. When designing breakaway tabs, consider the following:
- Tab size: Tabs should be large enough to provide adequate support for the PCBs but small enough to be easily removed without damaging the boards. A typical tab size ranges from 0.5 mm to 1.5 mm in width.
- Tab spacing: The spacing between tabs should be consistent and sufficient to prevent PCB Warpage during the assembly process. A general guideline is to place tabs every 25 mm to 50 mm along the board edges.
- Tab placement: Tabs should be placed in non-critical areas of the PCB, avoiding components, connectors, or sensitive circuitry.
4. Fiducial Marks and Tooling Holes
Fiducial marks and tooling holes are essential features in PCB panelization that aid in the alignment and registration of the boards during the manufacturing process.
Fiducial marks are small, precisely placed copper or solder mask features on the PCB panel that serve as reference points for the pick-and-place machines and automated optical inspection (AOI) systems. These marks ensure accurate component placement and help detect any misalignment during the assembly process.
Tooling holes are precisely drilled holes on the panel frame that provide a physical reference for the manufacturing equipment. These holes are used to align the panel in the fabrication and assembly machines, ensuring consistent positioning throughout the production process.
When incorporating fiducial marks and tooling holes in your panelization design, consider the following guidelines:
- Placement: Place fiducial marks and tooling holes in non-critical areas of the panel, avoiding interference with the PCBs or other panel features.
- Size: Fiducial marks typically range from 1 mm to 3 mm in diameter, while tooling holes are usually 2.4 mm or 3.2 mm in diameter, depending on the manufacturing equipment.
- Quantity: Include at least three fiducial marks and three tooling holes on the panel for optimal alignment and registration.
5. Depaneling Methods
Depaneling is the process of separating the individual PCBs from the panel after the assembly process. There are several depaneling methods available, each with its advantages and limitations:
- V-scoring: A V-shaped groove is cut along the breakaway tabs, allowing the PCBs to be easily snapped out of the panel. This method is suitable for low-volume production and prototyping.
- Routing: A CNC router is used to cut the PCBs from the panel, providing clean and precise edges. This method is ideal for high-volume production and complex board shapes.
- Punching: A die is used to punch out the individual PCBs from the panel, suitable for high-volume production of simple board shapes.
When selecting a depaneling method, consider factors such as production volume, board complexity, and the required edge quality of the final product.
6. Design for Manufacturing (DFM)
Design for Manufacturing (DFM) is a critical aspect of PCB panelization that involves designing the panel layout to optimize manufacturability and minimize potential issues during the fabrication and assembly processes. Some key DFM considerations include:
- Clearances: Ensure adequate clearances between PCBs, panel edges, and tooling features to prevent interference and damage during the manufacturing process.
- Symmetry: Where possible, design the panel layout with symmetry to balance the stress on the panel and minimize warpage.
- Panelization efficiency: Optimize the panel layout to maximize the number of PCBs per panel while minimizing waste material.
By adhering to DFM principles, designers can reduce manufacturing costs, improve yield, and ensure the quality of the final product.
7. Communication with Manufacturers
Effective communication with PCB Manufacturers is crucial for successful panelization design. Engage with your manufacturer early in the design process to discuss their specific panelization requirements, capabilities, and limitations. Some key points to discuss include:
- Panel size and material preferences
- Minimum and maximum board dimensions
- Depaneling methods and capabilities
- Fiducial mark and tooling hole specifications
- Any specific design constraints or considerations
By collaborating closely with your manufacturer, you can ensure that your panelization design is optimized for their production process, minimizing the risk of issues and delays.
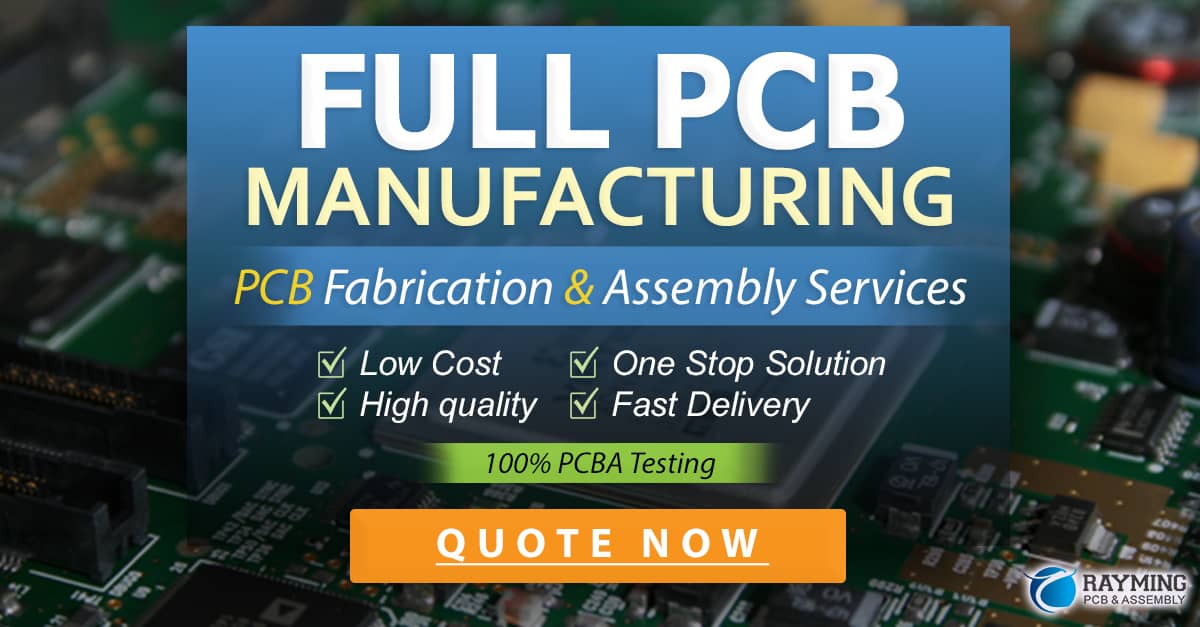
Frequently Asked Questions (FAQ)
- What is the minimum spacing between PCBs on a panel?
-
The minimum spacing between PCBs, or street width, typically ranges from 2 mm to 5 mm, depending on the cutting method and board thickness. Consult with your manufacturer for their specific requirements.
-
How many fiducial marks and tooling holes should be included on a panel?
-
It is recommended to include at least three fiducial marks and three tooling holes on a panel for optimal alignment and registration during the manufacturing process.
-
What factors should I consider when selecting a depaneling method?
-
When selecting a depaneling method, consider factors such as production volume, board complexity, required edge quality, and the capabilities of your chosen manufacturer.
-
Can different PCB designs be combined on a single panel?
-
Yes, different PCB designs can be combined on a single panel, known as a “mixed panel.” This approach can help optimize material usage and reduce production costs, especially for low-volume or prototype runs.
-
What are the benefits of working closely with my PCB manufacturer during the panelization design process?
- Collaborating closely with your PCB manufacturer during the panelization design process ensures that your design is optimized for their specific production capabilities and requirements. This approach can help minimize issues, reduce costs, and improve the overall quality of the final product.
Conclusion
PCB panelization is a critical aspect of the PCB manufacturing process that requires careful consideration and planning. By understanding the key principles of panelization design, including panel size and material selection, board orientation and spacing, breakaway tabs and mouse bites, fiducial marks and tooling holes, depaneling methods, Design for Manufacturing, and effective communication with manufacturers, designers can create optimal panel layouts that reduce costs, improve efficiency, and ensure the quality of the final product.
By following the guidelines outlined in this article and working closely with your chosen PCB manufacturer, you can successfully navigate the complexities of PCB panelization and bring your designs to life with confidence.
0 Comments