Introduction to PCB Fabrication and Common Issues
Printed Circuit Board (PCB) fabrication is a complex process that involves multiple steps and requires precise control over various factors. Multilayer PCBs, in particular, pose additional challenges due to their intricate structure and the need for precise alignment between layers. In this article, we will discuss seven common problems encountered in the multilayer PCB fabrication process and explore ways to mitigate these issues.
1. Layer Misregistration
Understanding Layer Misregistration
Layer misregistration is one of the most critical problems in multilayer PCB fabrication. It occurs when the layers of a PCB are not aligned properly, leading to issues such as short circuits, open circuits, and poor electrical performance. Misregistration can be caused by factors such as material expansion or contraction, mechanical stress, or improper handling during the fabrication process.
Mitigating Layer Misregistration
To minimize layer misregistration, consider the following strategies:
- Use high-quality materials with stable dimensions and low thermal expansion coefficients.
- Ensure proper handling and storage of PCB panels to prevent mechanical stress.
- Implement strict process controls and regular calibration of equipment.
- Use advanced registration systems, such as pin-less registration or optical alignment.
2. Copper Thickness Variation
The Impact of Copper Thickness Variation
Copper thickness variation can lead to inconsistent electrical performance and reliability issues in multilayer PCBs. It can be caused by factors such as uneven plating, etch-back problems, or incorrect copper foil thickness. Variations in copper thickness can result in impedance mismatches, signal integrity issues, and reduced current carrying capacity.
Controlling Copper Thickness Variation
To control copper thickness variation, consider the following approaches:
- Use high-quality copper foils with consistent thickness.
- Implement strict process controls for plating and etching processes.
- Monitor and adjust plating parameters regularly to maintain consistency.
- Use advanced inspection techniques, such as X-ray fluorescence (XRF) or cross-sectional analysis, to verify copper thickness.
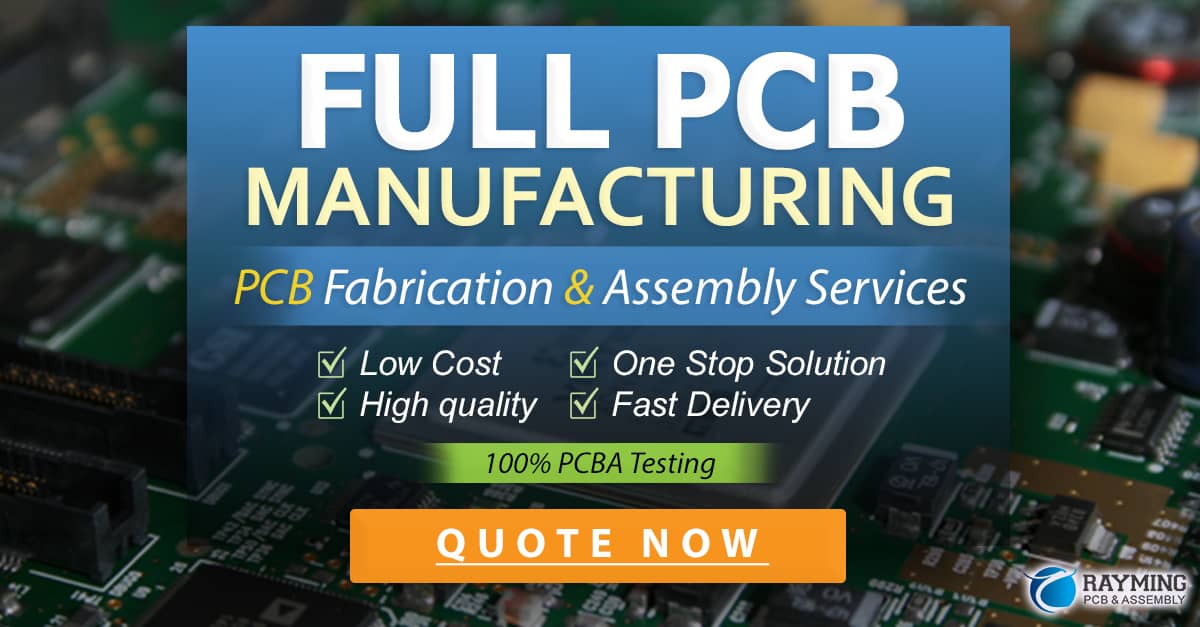
3. Drill Registration and Accuracy
The Importance of Drill Registration and Accuracy
Accurate drill registration is crucial for ensuring proper electrical connections between layers in multilayer PCBs. Poor drill registration can lead to misaligned vias, incomplete connections, and reliability issues. Drill accuracy is also essential for maintaining the integrity of the PCB structure and preventing damage to adjacent features.
Improving Drill Registration and Accuracy
To improve drill registration and accuracy, consider the following strategies:
- Use high-quality drilling equipment with precise spindle runout and depth control.
- Implement strict process controls for drill bit selection, maintenance, and replacement.
- Use advanced registration systems, such as vision-assisted drilling or real-time feedback control.
- Regularly calibrate and maintain drilling equipment to ensure consistent performance.
4. Lamination Defects
Types of Lamination Defects
Lamination defects can occur during the bonding of multiple layers in a multilayer PCB. Common lamination defects include:
- Delamination: Separation of layers due to poor adhesion or stress.
- Voids: Air pockets or gaps between layers that can lead to reliability issues.
- Resin starvation: Insufficient resin flow, resulting in poor bonding and mechanical weakness.
- Resin smear: Excess resin flow that can obstruct vias or cause short circuits.
Preventing Lamination Defects
To prevent lamination defects, consider the following approaches:
- Use high-quality prepregs and laminates with consistent resin content and flow properties.
- Control the lamination process parameters, such as temperature, pressure, and time, to ensure optimal bonding.
- Implement strict process controls for handling and storage of materials to prevent contamination or moisture absorption.
- Use advanced lamination techniques, such as vacuum lamination or sequential lamination, for improved results.
5. Soldermask Application and Alignment
The Role of Soldermask in PCB Fabrication
Soldermask is a protective coating applied to the surface of a PCB to prevent solder bridging and provide insulation between components. Proper soldermask application and alignment are essential for ensuring the reliability and functionality of the PCB. Issues such as soldermask misalignment, insufficient coverage, or excessive thickness can lead to soldering defects and reliability problems.
Ensuring Proper Soldermask Application and Alignment
To ensure proper soldermask application and alignment, consider the following strategies:
- Use high-quality soldermask materials with consistent viscosity and curing properties.
- Implement strict process controls for soldermask application, such as screen printing or photoimaging.
- Use advanced alignment systems, such as vision-assisted alignment or real-time feedback control.
- Regularly inspect and measure Soldermask Thickness and coverage to maintain consistency.
6. Surface Finish Selection and Application
Choosing the Right Surface Finish
The surface finish of a PCB plays a critical role in its solderability, corrosion resistance, and shelf life. Common surface finishes for multilayer PCBs include:
- Hot Air Solder Leveling (HASL)
- Electroless Nickel Immersion Gold (ENIG)
- Immersion Silver (IAg)
- Organic Solderability Preservative (OSP)
Each surface finish has its advantages and disadvantages, and the choice depends on factors such as the application, cost, and performance requirements.
Ensuring Proper Surface Finish Application
To ensure proper surface finish application, consider the following approaches:
- Use high-quality chemicals and processes for surface finish application.
- Implement strict process controls for surface preparation, such as cleaning and microetching.
- Monitor and control the surface finish thickness and uniformity.
- Regularly test the solderability and shelf life of the surface finish to ensure consistent performance.
7. Electrical Testing and Inspection
The Importance of Electrical Testing and Inspection
Electrical testing and inspection are critical steps in the multilayer PCB fabrication process to ensure the functionality and reliability of the final product. Common testing and inspection methods include:
- Flying Probe Testing
- In-circuit testing (ICT)
- Automated optical inspection (AOI)
- X-ray inspection
These methods help identify defects such as short circuits, open circuits, and component placement issues.
Implementing Effective Electrical Testing and Inspection
To implement effective electrical testing and inspection, consider the following strategies:
- Develop comprehensive test plans and inspection criteria based on the PCB design and performance requirements.
- Use high-quality testing and inspection equipment with appropriate resolution and accuracy.
- Implement strict process controls for testing and inspection, including operator training and certification.
- Regularly calibrate and maintain testing and inspection equipment to ensure consistent performance.
Frequently Asked Questions (FAQ)
-
What is the most common cause of layer misregistration in multilayer PCBs?
The most common cause of layer misregistration is material expansion or contraction due to thermal or mechanical stress during the fabrication process. -
How can copper thickness variation be controlled in the PCB fabrication process?
Copper thickness variation can be controlled by using high-quality copper foils, implementing strict process controls for plating and etching, and regularly monitoring and adjusting plating parameters. -
What are the consequences of poor drill registration and accuracy in multilayer PCBs?
Poor drill registration and accuracy can lead to misaligned vias, incomplete connections, and reliability issues, compromising the integrity and functionality of the PCB. -
What are some common lamination defects in multilayer PCBs?
Common lamination defects include delamination, voids, resin starvation, and resin smear, which can affect the mechanical and electrical properties of the PCB. -
Why is electrical testing and inspection important in the multilayer PCB fabrication process?
Electrical testing and inspection are critical for identifying defects such as short circuits, open circuits, and component placement issues, ensuring the functionality and reliability of the final product.
Conclusion
Multilayer PCB fabrication is a complex process that requires careful control over various factors to ensure the quality and reliability of the final product. By understanding the common problems encountered in the fabrication process and implementing effective strategies to mitigate these issues, manufacturers can improve the yield, performance, and cost-effectiveness of their PCBs. Regular process monitoring, strict quality control, and continuous improvement are essential for successfully navigating the challenges of multilayer PCB fabrication.
Problem | Description | Mitigation Strategies |
---|---|---|
Layer Misregistration | Misalignment of layers leading to short circuits, open circuits, and poor electrical performance | – Use high-quality materials with stable dimensions – Ensure proper handling and storage – Implement strict process controls and regular calibration – Use advanced registration systems |
Copper Thickness Variation | Inconsistent electrical performance and reliability issues due to uneven plating, etch-back problems, or incorrect copper foil thickness | – Use high-quality copper foils with consistent thickness – Implement strict process controls for plating and etching – Monitor and adjust plating parameters regularly – Use advanced inspection techniques |
Drill Registration and Accuracy | Misaligned vias, incomplete connections, and reliability issues due to poor drill registration and accuracy | – Use high-quality drilling equipment with precise spindle runout and depth control – Implement strict process controls for drill bit selection, maintenance, and replacement – Use advanced registration systems – Regularly calibrate and maintain drilling equipment |
Lamination Defects | Delamination, voids, resin starvation, and resin smear affecting the mechanical and electrical properties of the PCB | – Use high-quality prepregs and laminates with consistent resin content and flow properties – Control the lamination process parameters – Implement strict process controls for handling and storage of materials – Use advanced lamination techniques |
Soldermask Application and Alignment | Soldering defects and reliability problems due to soldermask misalignment, insufficient coverage, or excessive thickness | – Use high-quality soldermask materials with consistent viscosity and curing properties – Implement strict process controls for soldermask application – Use advanced alignment systems – Regularly inspect and measure soldermask thickness and coverage |
Surface Finish Selection and Application | Solderability, corrosion resistance, and shelf life issues due to improper surface finish selection and application | – Use high-quality chemicals and processes for surface finish application – Implement strict process controls for surface preparation – Monitor and control the surface finish thickness and uniformity – Regularly test the solderability and shelf life of the surface finish |
Electrical Testing and Inspection | Defects such as short circuits, open circuits, and component placement issues affecting the functionality and reliability of the PCB | – Develop comprehensive test plans and inspection criteria – Use high-quality testing and inspection equipment – Implement strict process controls for testing and inspection – Regularly calibrate and maintain testing and inspection equipment |
By addressing these seven common problems in the multilayer PCB fabrication process, manufacturers can improve the quality, reliability, and cost-effectiveness of their products. Investing in advanced technologies, implementing strict process controls, and fostering a culture of continuous improvement are key to overcoming the challenges of multilayer PCB fabrication and staying competitive in the rapidly evolving electronics industry.
0 Comments