What is a PCB Stackup?
A PCB stackup refers to the arrangement of copper and insulating layers that make up a printed circuit board (PCB). It is a cross-sectional view of the board, showing the order and thickness of each layer. The stackup is a critical aspect of PCB design, as it determines the board’s electrical properties, signal integrity, and manufacturability.
In a typical PCB stackup, the layers alternate between conductive copper and insulating material, such as FR-4. The number of layers in a stackup can vary depending on the complexity of the circuit and the desired functionality. Some common stackup configurations include:
- Single-sided: One conductive layer on one side of the board
- Double-sided: Two conductive layers, one on each side of the board
- Multi-layer: Three or more conductive layers, with insulating layers in between
Why is a PCB Stackup Important?
The PCB stackup is crucial because it directly impacts the performance and reliability of the circuit. Some of the key reasons why the stackup is important include:
-
Signal Integrity: The arrangement of layers in the stackup affects the way signals propagate through the board. Proper stackup design can minimize signal reflections, crosstalk, and electromagnetic interference (EMI), ensuring the signals remain clean and undistorted.
-
Impedance Control: The stackup determines the characteristic impedance of the traces on the board. By controlling the thickness and spacing of the layers, designers can achieve the desired impedance for various applications, such as high-speed digital circuits or RF systems.
-
Power Distribution: The stackup also plays a role in power distribution across the board. Dedicated power and ground planes can provide low-impedance paths for current flow, reducing voltage drops and minimizing noise.
-
Manufacturability: The choice of materials and layer thicknesses in the stackup can affect the ease of manufacturing and the overall cost of the board. A well-designed stackup takes into account the capabilities of the PCB Fabrication process and ensures the board can be produced reliably and cost-effectively.
6 Layer PCB Stackup Types
There are several common 6 layer PCB stackup configurations, each with its own advantages and applications. Some of the most popular 6 layer stackups include:
1. Signal-Ground-Power-Signal-Ground-Signal (S-G-P-S-G-S)
This stackup is a common choice for high-speed digital designs. It features a symmetric arrangement of layers, with signal layers on the top and bottom, ground layers next to them, and a power layer in the center. The benefits of this stackup include:
- Good signal integrity due to the proximity of ground layers to signal layers
- Low impedance power distribution through the central power plane
- Reduced EMI and crosstalk due to the shielding provided by the ground layers
Layer | Material | Thickness (mm) |
---|---|---|
Top Signal | Copper | 0.035 |
Ground | Copper | 0.035 |
Power | Copper | 0.035 |
Signal | Copper | 0.035 |
Ground | Copper | 0.035 |
Bottom Signal | Copper | 0.035 |
2. Signal-Ground-Signal-Power-Signal-Ground (S-G-S-P-S-G)
This stackup is similar to the previous one but with an additional signal layer in the center. It is suitable for designs that require more routing space or have a mix of analog and digital signals. The advantages of this stackup include:
- Increased routing density due to the extra signal layer
- Separation of analog and digital signals to minimize interference
- Good power distribution and grounding through dedicated planes
Layer | Material | Thickness (mm) |
---|---|---|
Top Signal | Copper | 0.035 |
Ground | Copper | 0.035 |
Signal | Copper | 0.035 |
Power | Copper | 0.035 |
Signal | Copper | 0.035 |
Bottom Ground | Copper | 0.035 |
3. Signal-Ground-Power-Ground-Power-Signal (S-G-P-G-P-S)
This stackup features two power planes and two ground planes, providing excellent power distribution and grounding. It is well-suited for power-hungry applications or boards with multiple voltage domains. The benefits of this stackup include:
- Low impedance power delivery through multiple power planes
- Reduced voltage drop and power supply noise
- Good EMI suppression and signal integrity
Layer | Material | Thickness (mm) |
---|---|---|
Top Signal | Copper | 0.035 |
Ground | Copper | 0.035 |
Power | Copper | 0.035 |
Ground | Copper | 0.035 |
Power | Copper | 0.035 |
Bottom Signal | Copper | 0.035 |
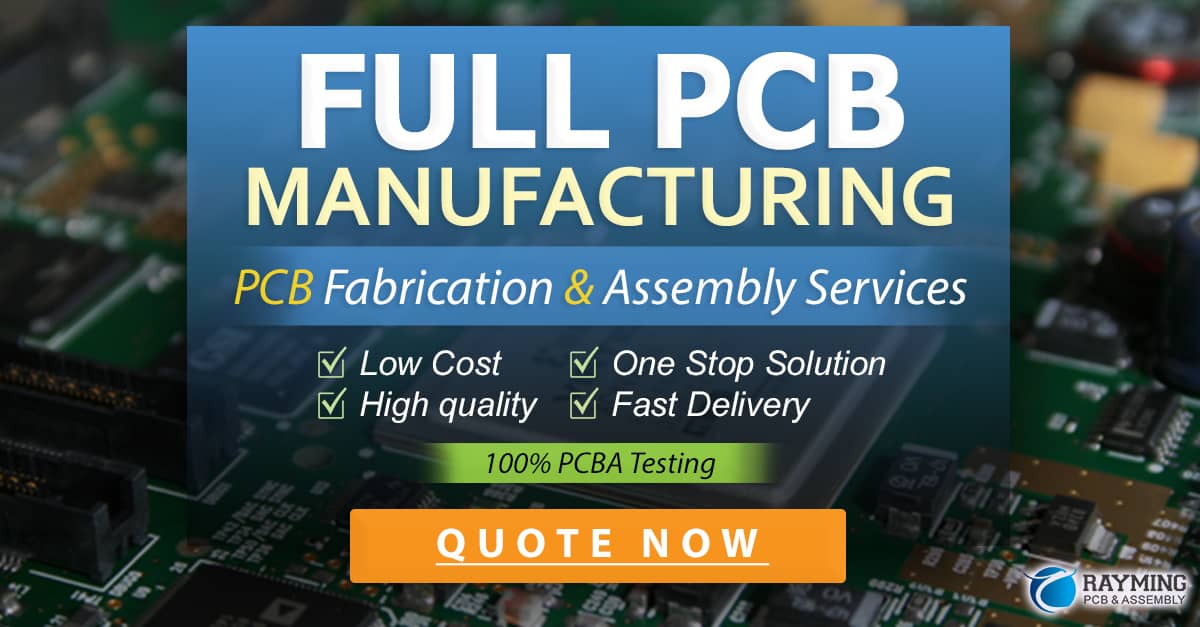
Designing a 6 Layer PCB Stackup
When designing a 6 layer PCB stackup, several factors should be considered to ensure optimal performance and manufacturability. Some key considerations include:
-
Material Selection: Choose appropriate materials for the insulating layers, such as FR-4, based on the desired dielectric constant, loss tangent, and thermal properties. The material thickness should also be selected to achieve the required impedance and mechanical strength.
-
Copper Weight: Specify the appropriate copper weight for each layer, typically measured in ounces per square foot (oz/ft²). Thicker copper can carry more current and provide better shielding, but it also increases the cost and manufacturing complexity.
-
Via Design: Consider the size, type, and placement of vias in the stackup. Through-hole vias span all layers, while blind and buried vias connect only certain layers. Via design affects signal integrity, manufacturability, and cost.
-
Trace Width and Spacing: Determine the appropriate trace width and spacing for each signal layer based on the required impedance, current carrying capacity, and manufacturing constraints. Wider traces can carry more current but also consume more space.
-
Plane Assignment: Assign power and ground planes strategically to provide low-impedance paths for current flow and minimize noise. Consider splitting planes for different voltage domains or using solid planes for better shielding.
-
Manufacturability: Consult with the PCB manufacturer to ensure the stackup is compatible with their fabrication capabilities. Consider factors such as minimum hole size, layer registration, and materials availability.
Conclusion
A well-designed 6 layer PCB stackup is essential for achieving reliable, high-performance electronic systems. By understanding the different stackup types and considering key design factors, engineers can create PCBs that meet the specific requirements of their applications. Working closely with experienced PCB Manufacturers can help ensure the stackup is optimized for both functionality and manufacturability, resulting in a successful end product.
Frequently Asked Questions (FAQ)
- What is the most common 6 layer PCB stackup?
-
The most common 6 layer PCB stackup is the Signal-Ground-Power-Signal-Ground-Signal (S-G-P-S-G-S) configuration. This stackup provides a good balance of signal integrity, power distribution, and EMI suppression.
-
Can I use different materials for each layer in a 6 layer PCB stackup?
-
Yes, it is possible to use different materials for each layer in a 6 layer PCB stackup. For example, you could use a high-performance material like Rogers for the RF layers and standard FR-4 for the digital layers. However, using multiple materials can increase the cost and complexity of the board.
-
How does the PCB stackup affect the impedance of the traces?
-
The PCB stackup determines the characteristic impedance of the traces by controlling the thickness and spacing of the layers. The impedance is a function of the dielectric constant of the insulating material, the trace width and thickness, and the distance to the reference plane. By adjusting these parameters, designers can achieve the desired impedance for their application.
-
What is the minimum hole size for vias in a 6 layer PCB?
-
The minimum hole size for vias in a 6 layer PCB depends on the capabilities of the PCB manufacturer. Typically, the minimum hole size ranges from 0.2mm to 0.3mm, but some advanced manufacturers can achieve smaller sizes. It is important to consult with the manufacturer to ensure the via design is compatible with their fabrication process.
-
How can I minimize crosstalk between layers in a 6 layer PCB stackup?
- To minimize crosstalk between layers in a 6 layer PCB stackup, you can:
- Use ground layers to shield signal layers and reduce coupling
- Increase the spacing between sensitive traces on adjacent layers
- Route critical traces perpendicular to each other on adjacent layers to minimize overlap
- Use guard traces or ground vias to provide additional shielding between traces
- Minimize the parallel run length of sensitive traces on adjacent layers
By carefully designing the PCB stackup and following best practices for signal routing, you can effectively minimize crosstalk and ensure the integrity of your signals.
0 Comments