Introduction to PCB Manufacturers and High Layer Count PCBs
In the world of electronic design and manufacturing, Printed Circuit Boards (PCBs) form the backbone of most modern devices. PCB manufacturers play a crucial role in bringing these designs to life, constantly innovating and pushing the limits of what is possible. One such advancement is the development of high layer count PCBs, with some manufacturers now offering up to 33 layers or more.
What are High Layer Count PCBs?
High layer count PCBs are circuit boards that consist of a large number of conductive layers, typically more than the standard 4-10 layers found in most PCBs. These additional layers allow for increased complexity, higher component density, and improved signal integrity. 33 layer PCBs represent the pinnacle of this technology, offering unparalleled design flexibility and performance.
Benefits of High Layer Count PCBs
- Increased Functionality: With more layers available, designers can incorporate a greater number of features and functions into a single board.
- Reduced Size: By stacking more layers, the overall footprint of the PCB can be reduced, making it ideal for space-constrained applications.
- Improved Signal Integrity: Additional layers allow for better signal routing and shielding, minimizing crosstalk and electromagnetic interference (EMI).
- Enhanced Thermal Management: More layers provide increased surface area for heat dissipation, helping to maintain optimal operating temperatures.
Leading 33 Layers PCB Manufacturers
1. AT&S (Austria Technologie & Systemtechnik)
AT&S is an Austrian-based PCB manufacturer known for their high-end, multi-layer PCBs. They offer a range of services, including:
- HDI (High Density Interconnect) PCBs
- Embedded Component Packaging
- Rigid-Flex PCBs
- High-Frequency PCBs
Layer Count | Minimum Trace Width | Minimum Via Diameter |
---|---|---|
33 | 50 μm | 100 μm |
2. Unimicron
Unimicron is a Taiwanese PCB manufacturer with a strong presence in the global market. They specialize in high layer count PCBs, offering:
- Advanced HDI PCBs
- Anylayer HDI
- Multilayer BUM (Buried/Blind Via) PCBs
- IC Substrate
Layer Count | Minimum Trace Width | Minimum Via Diameter |
---|---|---|
33+ | 30 μm | 50 μm |
3. Ibiden
Ibiden is a Japanese PCB manufacturer known for their cutting-edge technology and high-quality products. Their offerings include:
- Buildup Multilayer PCBs
- Thick Copper PCBs
- Multilayer Flex PCBs
- Optical PCBs
Layer Count | Minimum Trace Width | Minimum Via Diameter |
---|---|---|
33+ | 40 μm | 75 μm |
Manufacturing Process for 33 Layers PCBs
1. Layer Stacking and Lamination
The process begins with the stacking of multiple layers of copper-clad laminate and prepreg (pre-impregnated) materials. These layers are precisely aligned and subjected to high pressure and temperature in a lamination press, fusing them into a solid board.
2. Drilling and Plating
Once laminated, the board undergoes drilling to create vias and through-holes. These holes are then plated with copper to establish electrical connections between layers.
3. Patterning and Etching
The outer layers of the PCB are patterned using photolithography, and the unwanted copper is etched away, leaving behind the desired circuit traces.
4. Solder Mask Application
A solder mask is applied to the outer layers of the PCB to protect the copper traces from oxidation and prevent solder bridging during assembly.
5. Surface Finish
Finally, a surface finish, such as ENIG (Electroless Nickel Immersion Gold) or HASL (Hot Air Solder Leveling), is applied to the exposed copper areas to enhance solderability and protect against corrosion.
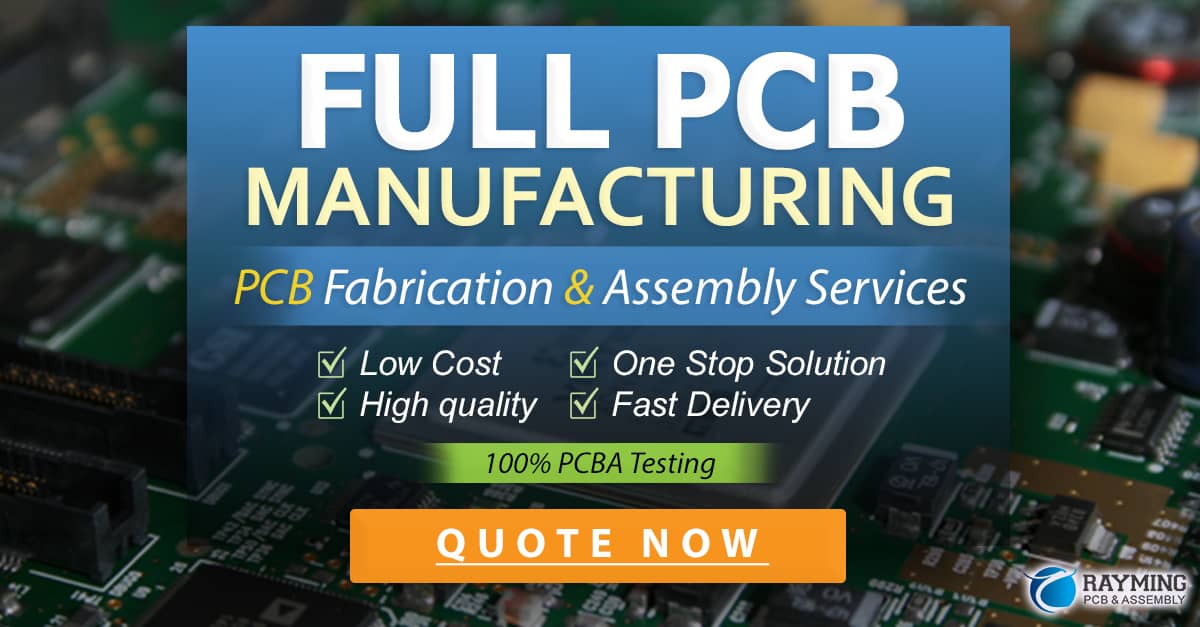
Applications of 33 Layers PCBs
1. High-Performance Computing
33 layers PCBs are essential in high-performance computing applications, such as data centers and supercomputers, where high signal speeds and densities are required.
2. Telecommunications
In the telecommunications industry, 33 layers PCBs enable the development of complex switching systems, routers, and other network equipment.
3. Aerospace and Defense
The aerospace and defense sectors rely on high layer count PCBs for advanced radar systems, satellite communications, and avionics.
4. Medical Devices
Sophisticated medical devices, such as imaging systems and diagnostic equipment, benefit from the increased functionality and miniaturization offered by 33 layers PCBs.
Challenges in 33 Layers PCB Manufacturing
1. Signal Integrity Management
As the number of layers increases, maintaining signal integrity becomes more challenging. Manufacturers must employ advanced design techniques and materials to minimize signal loss, crosstalk, and EMI.
2. Thermal Management
With higher component density and increased power consumption, thermal management becomes critical in 33 layers PCBs. Manufacturers must incorporate efficient cooling solutions to prevent overheating and ensure reliable operation.
3. Manufacturing Complexity
The production of 33 layers PCBs requires state-of-the-art equipment, skilled personnel, and stringent quality control measures. Manufacturers must continually invest in technology and training to maintain their competitive edge.
Future Trends in High Layer Count PCBs
1. Embedded Components
The integration of passive components, such as resistors and capacitors, directly into the PCB substrate is gaining traction. This approach further increases component density and reduces the overall size of the board.
2. Advanced Materials
The development of new, high-performance materials, such as low-loss dielectrics and ultra-thin laminates, will enable even higher layer counts and improved signal integrity.
3. 3D Printing
The application of 3D printing technology in PCB manufacturing is an emerging trend. This approach allows for the creation of complex, three-dimensional structures and the integration of non-planar components.
Frequently Asked Questions (FAQ)
1. What is the cost difference between a standard PCB and a 33 layers PCB?
The cost of a 33 layers PCB can be significantly higher than a standard PCB, often several times more expensive. The exact cost difference depends on factors such as the board size, complexity, and manufacturing volume.
2. How long does it take to manufacture a 33 layers PCB?
The lead time for a 33 layers PCB can range from several weeks to a few months, depending on the manufacturer’s capacity and the complexity of the design. Rush services may be available at a premium cost.
3. Are 33 layers PCBs suitable for all applications?
No, 33 layers PCBs are primarily used in high-performance, space-constrained applications where the benefits of increased functionality and density outweigh the higher cost and complexity. Many applications can be adequately served by PCBs with fewer layers.
4. How do I choose the right 33 layers PCB manufacturer?
When selecting a 33 layers PCB manufacturer, consider factors such as their experience, technology capabilities, quality certifications (e.g., ISO, AS9100), and customer support. Request references and samples to assess their quality and reliability.
5. Can 33 layers PCBs be reworked or repaired?
Reworking or repairing a 33 layers PCB can be extremely challenging due to the high density of components and the complexity of the inner layers. In most cases, it is more cost-effective to replace the entire board rather than attempt a repair.
Conclusion
33 layers PCB manufacturers represent the forefront of PCB technology, enabling the development of highly advanced and compact electronic devices. As the demand for increased functionality and performance continues to grow, these manufacturers will play a crucial role in shaping the future of the electronics industry. By understanding the capabilities, applications, and challenges associated with 33 layers PCBs, designers and engineers can make informed decisions when selecting the appropriate manufacturing partner for their projects.
0 Comments