Introduction to PCB Layers
Printed Circuit Boards (PCBs) are the backbone of modern electronics. They provide a platform for mounting and interconnecting electronic components to create a functional circuit. One of the key aspects of PCB design is the number of layers. As technology advances, the demand for more complex and compact designs has led to the development of multi-layer PCBs, with 32 layers being one of the most advanced options available. In this article, we will explore the world of 32 layer PCBs, their benefits, challenges, and what you should know before embarking on a project involving these complex boards.
What are PCB Layers?
Before diving into the specifics of 32 layer PCBs, let’s briefly discuss what PCB layers are. A PCB layer is a thin, insulating material that has conductive traces etched onto its surface. These traces are used to connect the various components mounted on the board. The number of layers in a PCB refers to the number of these insulating materials stacked together, with conductive traces on each layer.
Types of PCB Layers
PCBs can be classified based on the number of layers they contain. The most common types are:
Type | Number of Layers |
---|---|
Single-layer | 1 |
Double-layer | 2 |
Multi-layer | 4, 6, 8, 10, 12 |
High-density | 14, 16, 18, 20 |
Ultra-high-density | 22, 24, 26, 28, 30, 32 |
As the number of layers increases, so does the complexity of the design and the manufacturing process.
Benefits of 32 Layer PCBs
Increased Functionality
One of the primary benefits of using a 32 layer PCB is the ability to incorporate more functionality into a smaller space. With 32 layers, designers have more routing options, allowing them to create complex circuits with a higher component density. This is particularly useful in applications that require advanced features, such as high-speed data processing, advanced graphics, or artificial intelligence.
Improved Signal Integrity
Signal integrity is a critical factor in PCB design, especially for high-speed applications. With 32 layers, designers can optimize the signal paths, reducing the risk of signal degradation, crosstalk, and electromagnetic interference (EMI). By carefully arranging the layers and using appropriate shielding techniques, designers can ensure that the signals remain clean and stable throughout the board.
Enhanced Thermal Management
As electronic devices become more powerful, thermal management becomes increasingly important. 32 layer PCBs offer improved thermal management capabilities due to their increased surface area and the ability to incorporate dedicated thermal layers. These layers can be used to dissipate heat away from critical components, ensuring that the device operates within its optimal temperature range.
Reduced Size and Weight
In many applications, size and weight are critical factors. 32 layer PCBs allow designers to create more compact devices without sacrificing functionality. By consolidating multiple circuits onto a single board, designers can reduce the overall size and weight of the device, making it more portable and efficient.
Challenges of 32 Layer PCBs
Design Complexity
Designing a 32 layer PCB is a complex and time-consuming process. Designers must carefully plan the layout of each layer, ensuring that the signals are routed correctly and that there are no conflicts between components. This requires advanced design tools and a deep understanding of PCB design principles.
Manufacturing Challenges
Manufacturing a 32 layer PCB is also a complex process that requires specialized equipment and expertise. The high number of layers makes the board more susceptible to manufacturing defects, such as delamination, poor adhesion, or misalignment. Manufacturers must have strict quality control measures in place to ensure that the boards meet the required specifications.
Cost Considerations
Due to their complexity and the specialized equipment required for manufacturing, 32 layer PCBs are generally more expensive than their simpler counterparts. The cost of materials, labor, and testing can add up quickly, making these boards more suitable for high-end applications where performance is critical.
Testing and Debugging
Testing and debugging a 32 layer PCB can be challenging due to the high number of layers and the complexity of the circuits. Specialized testing equipment and techniques are required to ensure that the board is functioning correctly and that there are no hidden defects. This can add significant time and cost to the development process.
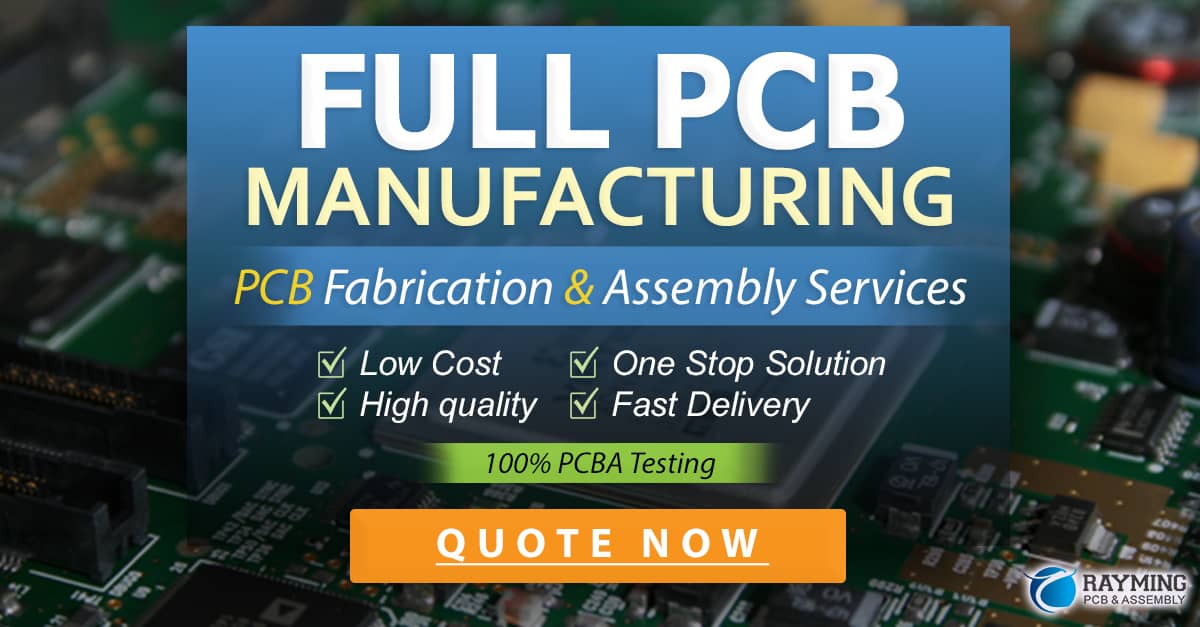
Applications of 32 Layer PCBs
High-Performance Computing
32 layer PCBs are commonly used in high-performance computing applications, such as servers, workstations, and supercomputers. These applications require high-speed data processing and advanced features that can only be achieved with complex, multi-layer boards.
Telecommunications
The telecommunications industry relies heavily on advanced PCB technology to create compact, high-performance devices. 32 layer PCBs are used in applications such as 5G networks, fiber-optic communication, and satellite systems.
Medical Devices
Medical devices, such as imaging equipment, diagnostic tools, and treatment systems, require high levels of reliability and performance. 32 layer PCBs are used in these applications to ensure that the devices operate accurately and consistently, even in demanding environments.
Aerospace and Defense
In aerospace and defense applications, size, weight, and performance are critical factors. 32 layer PCBs are used in applications such as avionics, radar systems, and satellite communication to create compact, high-performance devices that can withstand harsh environments.
FAQ
-
Q: How long does it take to design a 32 layer PCB?
A: The design time for a 32 layer PCB can vary depending on the complexity of the circuit and the experience of the designer. On average, it can take several weeks to several months to complete the design process. -
Q: Can 32 layer PCBs be manufactured by any PCB manufacturer?
A: No, not all PCB Manufacturers have the capability to produce 32 layer PCBs. These boards require specialized equipment and expertise, so it’s important to choose a manufacturer with experience in high-density, multi-layer PCBs. -
Q: Are 32 layer PCBs more reliable than boards with fewer layers?
A: When designed and manufactured correctly, 32 layer PCBs can be highly reliable. However, the increased complexity also means that there is a higher risk of manufacturing defects, so it’s important to work with a reputable manufacturer and have stringent quality control measures in place. -
Q: Can 32 layer PCBs be repaired if they malfunction?
A: Repairing a 32 layer PCB can be challenging due to the high number of layers and the complexity of the circuits. In many cases, it may be more cost-effective to replace the entire board rather than attempting a repair. -
Q: Are there any alternatives to 32 layer PCBs for high-performance applications?
A: While 32 layer PCBs offer the highest level of performance and functionality, there are other options available depending on the specific requirements of the application. These include high-density interconnect (HDI) PCBs, Rigid-flex PCBs, and 3D PCBs.
Conclusion
32 layer PCBs represent the pinnacle of PCB technology, offering unparalleled functionality, performance, and reliability. While they present significant challenges in terms of design, manufacturing, and cost, they are essential for a wide range of high-end applications in industries such as computing, telecommunications, medical devices, and aerospace.
As technology continues to advance, it’s likely that we will see even more complex PCBs in the future, with higher layer counts and more advanced features. However, for now, 32 layer PCBs remain the gold standard for high-performance electronics, and understanding their benefits and challenges is essential for anyone involved in PCB design or manufacturing.
0 Comments