Introduction to the 28BYJ-48 Unipolar Stepper Motor
The 28BYJ-48 is a popular and affordable 5-wire, 5V unipolar stepper motor widely used in DIY projects, robotics, and small-scale automation tasks. This motor offers precise control, reliability, and ease of use, making it an ideal choice for beginners and experienced users alike. In this article, we will explore the features, specifications, working principles, and applications of the 28BYJ-48 unipolar stepper motor.
Key Features of the 28BYJ-48 Unipolar Stepper Motor
- 5-wire design
- 5V operating voltage
- Unipolar configuration
- Precise step angle (5.625°/64 steps per revolution)
- Compact size and lightweight
- Low cost and easy availability
Understanding Unipolar Stepper Motors
Before diving into the specifics of the 28BYJ-48, let’s understand what unipolar stepper motors are and how they differ from other types of stepper motors.
Types of Stepper Motors
There are three main types of stepper motors:
- Unipolar stepper motors
- Bipolar stepper motors
- Variable reluctance stepper motors
Unipolar stepper motors, like the 28BYJ-48, have a simpler winding configuration compared to bipolar stepper motors. They have two windings per phase, with a center tap that allows the current to flow in only one direction through each winding. This simplifies the driver circuitry required to control the motor.
Advantages of Unipolar Stepper Motors
- Simpler driver circuitry
- Lower cost
- Easier to control
- Suitable for low-torque applications
Disadvantages of Unipolar Stepper Motors
- Lower torque compared to bipolar stepper motors
- Less efficient than bipolar stepper motors
- Limited speed range
Specifications of the 28BYJ-48 Unipolar Stepper Motor
Let’s take a closer look at the specifications of the 28BYJ-48 unipolar stepper motor:
Specification | Value |
---|---|
Rated Voltage | 5V DC |
Number of Phases | 4 |
Stride Angle | 5.625°/64 |
Frequency | 100 Hz |
DC Resistance | 50Ω ±7% (25°C) |
Idle In-traction Frequency | > 600 Hz |
Idle Out-traction Frequency | > 1000 Hz |
In-traction Torque | >34.3 mN.m (120 Hz) |
Self-positioning Torque | >34.3 mN.m |
Friction Torque | 600-1200 gf.cm |
Pull-in Torque | 300 gf.cm |
Insulated Resistance | >10 MΩ (500V) |
Insulated Electricity Power | 600 VAC/1 mA/1 s |
Insulation Grade | A |
Rise in Temperature | <40 K (120 Hz) |
Noise | <35 dB (120 Hz, no load, 10 cm) |
These specifications provide essential information about the motor’s operating voltage, step angle, torque, and other parameters that are crucial for selecting the appropriate motor for your project and designing the control circuitry.
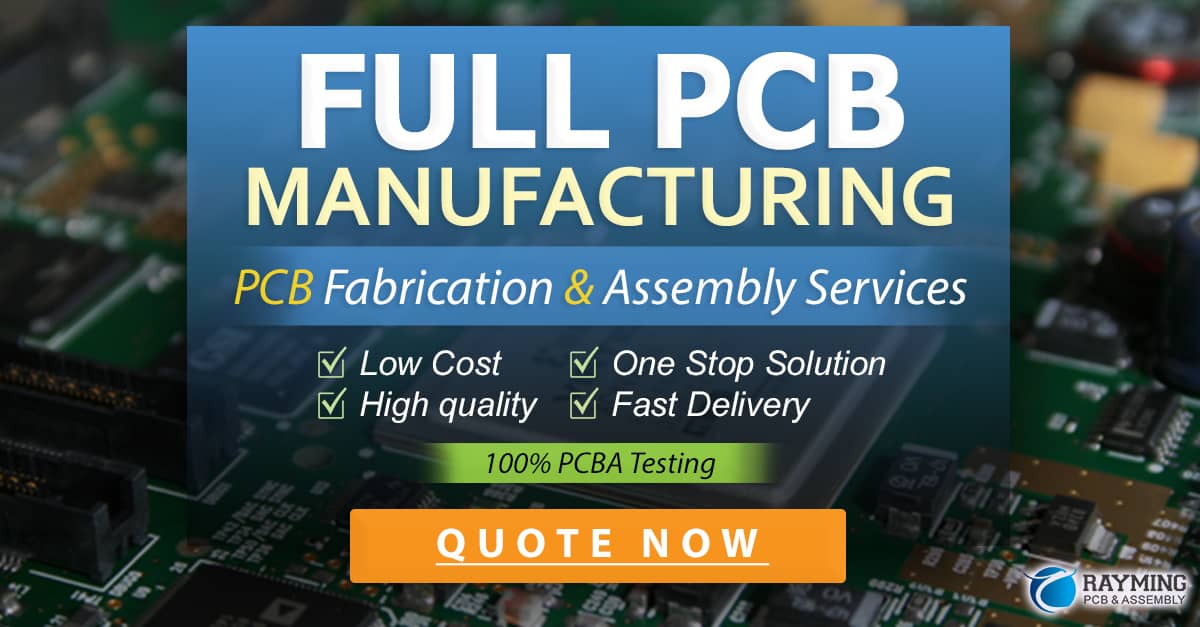
Working Principle of the 28BYJ-48 Unipolar Stepper Motor
The 28BYJ-48 unipolar stepper motor operates on the principle of electromagnetism. It consists of a rotor with permanent magnets and a stator with four phases of windings. By energizing these windings in a specific sequence, the motor creates a rotating magnetic field that causes the rotor to rotate in precise increments, or steps.
Stator and Rotor Construction
The stator of the 28BYJ-48 has eight poles, with each pole having a winding. These windings are connected in pairs, forming four phases: A, B, C, and D. The center tap of each pair is connected to the positive supply voltage, while the other ends of the windings are connected to the ground through a switching circuit.
The rotor consists of a permanent magnet with multiple poles. The number of poles on the rotor determines the step angle of the motor. In the case of the 28BYJ-48, the rotor has 32 poles, resulting in a step angle of 5.625° (360° / 64 steps per revolution).
Stepping Sequence and Control
To rotate the 28BYJ-48 unipolar stepper motor, the four phases of the stator windings must be energized in a specific sequence. The most common stepping sequences are:
- Wave Drive (1 phase on)
- Full Step Drive (2 phases on)
- Half Step Drive (alternating between 1 and 2 phases on)
The choice of stepping sequence depends on the desired resolution, torque, and speed of the motor. The more phases that are energized simultaneously, the higher the torque but the lower the resolution.
To control the 28BYJ-48, a driver circuit is required. The most popular driver for this motor is the ULN2003A, which is a Darlington transistor array IC. The ULN2003A simplifies the control circuitry by providing the necessary current amplification and switching capabilities to drive the motor windings.
Applications of the 28BYJ-48 Unipolar Stepper Motor
The 28BYJ-48 unipolar stepper motor finds applications in various fields, such as:
- Robotics: Used in small robotic arms, grippers, and actuators
- 3D Printing: Employed in low-cost, entry-level 3D printers for precise movement of the print head or bed
- Automation: Utilized in small-scale automation projects, such as door locks, window blinds, and vending machines
- Camera and Sensor Mounts: Provides precise positioning for cameras, sensors, and lasers
- Educational Projects: Serves as an excellent learning tool for students and hobbyists to understand stepper motor control and electronics
Interfacing the 28BYJ-48 with Arduino
One of the most popular ways to control the 28BYJ-48 unipolar stepper motor is by using an Arduino microcontroller board. The Arduino provides an easy-to-use platform for programming and controlling the motor through the ULN2003A driver.
Hardware Connection
To interface the 28BYJ-48 with an Arduino, follow these steps:
- Connect the positive supply voltage (5V) of the motor to the Arduino’s 5V pin
- Connect the four phase wires of the motor to the inputs of the ULN2003A driver (pins 1, 2, 3, and 4)
- Connect the ground wire of the motor to the Arduino’s GND pin
- Connect the outputs of the ULN2003A driver (pins 16, 15, 14, and 13) to the Arduino’s digital pins (e.g., 8, 9, 10, and 11)
Arduino Code for Controlling the 28BYJ-48
Here’s a sample Arduino code for controlling the 28BYJ-48 unipolar stepper motor using the ULN2003A driver:
#include <Stepper.h>
const int stepsPerRevolution = 64; // Number of steps per revolution
const int motorSpeed = 500; // Motor speed in RPM
// Initialize the stepper library
Stepper myStepper(stepsPerRevolution, 8, 10, 9, 11);
void setup() {
// Set the motor speed
myStepper.setSpeed(motorSpeed);
}
void loop() {
// Step one revolution in one direction
myStepper.step(stepsPerRevolution);
delay(500);
// Step one revolution in the other direction
myStepper.step(-stepsPerRevolution);
delay(500);
}
This code uses the Arduino’s built-in Stepper library to control the 28BYJ-48. It sets the number of steps per revolution, the motor speed, and defines the sequence in which the digital pins should be activated to rotate the motor in both directions.
Frequently Asked Questions (FAQ)
-
Q: What is the difference between a unipolar and bipolar stepper motor?
A: Unipolar stepper motors have a simpler winding configuration with a center tap, allowing current to flow in only one direction through each winding. Bipolar stepper motors have no center tap and require a more complex driver to reverse the current direction in the windings. Unipolar motors are easier to control but have lower torque and efficiency compared to bipolar motors. -
Q: Can I use the 28BYJ-48 without the ULN2003A driver?
A: While it is possible to control the 28BYJ-48 without the ULN2003A driver, it is not recommended. The ULN2003A provides the necessary current amplification and switching capabilities to drive the motor windings efficiently. Attempting to control the motor directly from a microcontroller may result in damage to the motor or the microcontroller. -
Q: How can I increase the torque of the 28BYJ-48 stepper motor?
A: To increase the torque of the 28BYJ-48, you can use a higher voltage power supply (up to 12V) or use a full-step or half-step driving sequence instead of wave drive. However, keep in mind that increasing the voltage may also increase the motor’s speed and power consumption. -
Q: What is the maximum speed I can achieve with the 28BYJ-48?
A: The maximum speed of the 28BYJ-48 depends on factors such as the driving voltage, stepping sequence, and load. In general, the motor can achieve speeds up to 1000 Hz (idle out-traction frequency) with no load. However, the practical speed limit is lower and depends on the specific application and driving circuitry. -
Q: Can I use the 28BYJ-48 for continuous rotation applications?
A: Yes, the 28BYJ-48 can be used for continuous rotation applications by providing a constant stepping sequence to the motor. However, due to the motor’s limited torque and speed, it may not be suitable for applications requiring high speed or heavy loads. In such cases, a different type of motor, such as a DC motor or a more powerful stepper motor, may be a better choice.
Conclusion
The 28BYJ-48 unipolar stepper motor is a versatile and affordable choice for a wide range of DIY projects, robotics, and small-scale automation tasks. Its 5-wire design, 5V operating voltage, and precise step angle make it easy to control and integrate into various applications. By understanding the working principles, specifications, and control methods of the 28BYJ-48, you can harness its potential and create innovative projects.
Whether you are a beginner learning about stepper motors or an experienced user seeking a reliable and cost-effective solution, the 28BYJ-48 unipolar stepper motor is an excellent choice. With its compatibility with popular microcontroller platforms like Arduino and the availability of extensive online resources and community support, you can quickly get started and bring your ideas to life.
So, go ahead and explore the possibilities with the 28BYJ-48 unipolar stepper motor, and let your creativity guide you in creating amazing projects that push the boundaries of what’s possible with this tiny but mighty motor.
0 Comments