1. PCB Design Software
PCB design software is used to create the layout and schematic of a PCB. Popular options include:
Software | Vendor | Key Features |
---|---|---|
Altium Designer | Altium | 3D modeling, real-time DRC, advanced routing |
Eagle | Autodesk | User-friendly interface, extensive part libraries |
KiCad | Open source | Free, cross-platform, growing community |
Choosing the right PCB design software depends on factors like budget, ease of use, and specific design requirements. Many vendors offer free trials to allow you to test drive before committing.
2. PCB Prototyping
Before mass production, it’s important to create a prototype PCB to test and validate the design. Rapid PCB prototyping tools allow you to quickly fabricate boards in-house. Options range from desktop CNC machines to professional pick-and-place machines.
Prototyping Method | Typical Turnaround Time | Cost |
---|---|---|
Desktop CNC | 1-2 days | $ |
PCB Milling Machine | 1 day | $$ |
Professional Pick-and-Place | < 1 day | $$$ |
The right prototyping method depends on your timeline, budget, and the complexity of the PCB design. In some cases, it may be more cost-effective to outsource prototyping to a specialized PCB fab house.
3. PCB Assembly
Once you have a validated PCB design, the next step is assembly. This involves soldering components onto the board. PCB assembly can be done manually, but for higher volumes, automated assembly using pick-and-place machines and reflow ovens is more efficient.
Manual assembly is suitable for simpler designs and lower volumes. For complex, high-volume jobs, investing in automated assembly equipment or outsourcing to an assembly house is recommended.
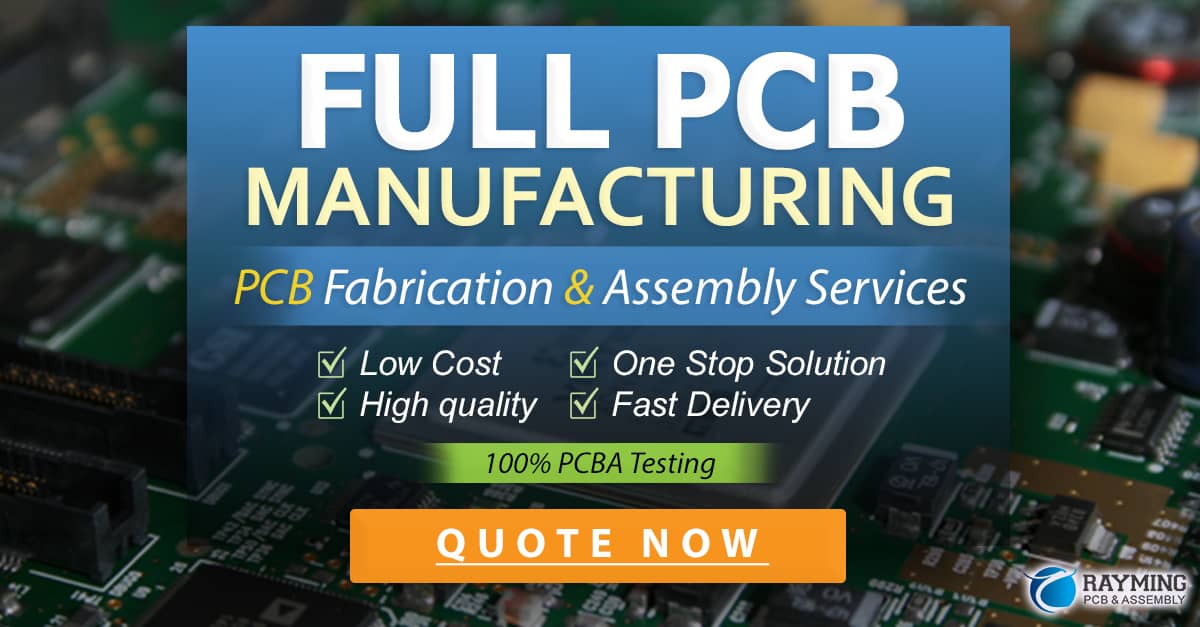
4. PCB Testing
After assembly, PCBs need to be rigorously tested to ensure proper functionality and catch any defects. Common PCB testing methods include:
- In-Circuit Testing (ICT): Probes are used to test individual components and nets on the PCB
- Flying Probe Testing: Robotic probes move around the PCB to test at various points
- Boundary Scan Testing: Uses JTAG to test components like BGA that are hard to probe
- Functional Testing: Tests the PCB as a complete system to verify end-to-end functionality
The best testing approach depends on factors like PCB complexity, target defect rate, and budget. Often a combination of methods yields the most comprehensive test coverage.
5. PCB Inspection
Visual inspection is an important complement to electrical testing. Automated optical inspection (AOI) systems use cameras and image processing to check for common defects like solder bridges, component skew, and missing parts.
Manual visual inspection using microscopes is still used, especially for lower volumes or to verify automated inspection results. Investing in inspection tools and processes helps identify defects early and improve overall quality.
6. Rework and Repair
Even with solid designs and processes, some PCB defects are inevitable. Having the right tools for rework and repair helps minimize scrap and improve yields. Key tools include:
- Soldering irons and hot air rework stations for manual component removal/replacement
- BGA Rework stations for safely removing and replacing BGAs
- Microscopes and magnifying lamps to assist manual rework
- Solder paste dispensers and stencils for localized solder paste application
Investing in training for rework/repair technicians is just as important as having the right equipment. IPC offers certification programs on PCB rework and repair standards.
7. Programming
Many PCBs include programmable components like microcontrollers and FPGAs that need to be programmed with firmware. Device programmers are used to transfer firmware via interfaces like JTAG, SPI, and I2C.
Programmer Type | Key Features |
---|---|
Universal | Supports a wide range of devices and interfaces |
Gang | Programs multiple devices in parallel |
In-System | Programs devices already soldered to PCB |
Factors to consider when selecting a programmer include supported devices, programming speed, ease of use, and data integrity features like check-sum verification.
8. Boundary Scan Tools
Boundary scan (JTAG) tools are invaluable for testing and programming complex, high-density PCBs. They allow access to device pins that would otherwise be inaccessible to probes. Boundary scan tools provide several key capabilities:
- Interconnect testing between JTAG devices
- In-system programming of FPGAs, CPLDs, and flash memories
- Cluster testing of non-JTAG devices using JTAG devices as an access point
- Functional testing using the JTAG TAP
Boundary scan tools range from simple PC-based controllers to complete systems with automated test executive software. The IEEE-1149.1 standard governs boundary scan implementation.
9. Functional Test Fixtures
Functional test fixtures, or “bed of nails” testers, allow testing of the complete assembled PCB. The fixture consists of a customized bed of spring probes that make contact with test points on the board under test.
Functional test fixtures provide several benefits:
- Testing of the full system functionality
- Testing of both JTAG and non-JTAG components
- High test coverage and diagnostic granularity
- Good signal integrity for high-speed tests
The main drawback of functional test fixtures is the upfront cost and lead time of designing and building a custom fixture for each PCB design. For high-volume products, this investment is usually justified.
10. Flying Probe Testers
Flying probe testers are an alternative to ICT fixtures that use robotic probes to access test points on the PCB. The main advantages are:
- No custom fixturing, reducing cost and lead time
- Easy to modify tests for PCB revisions
- Can test both sides of board without flipping
- Good for low-volume, high-mix environments
The tradeoffs are lower test speed and potentially reduced test coverage compared to full ICT. Flying probe testers excel in high-mix prototype and NPI environments.
11. Automated Test Equipment (ATE)
For very high-volume PCB production, automated test equipment (ATE) is used to enable fast, parallel testing. ATEs typically integrate multiple instruments like power supplies, DMMs, and signal generators to apply test stimuli and measure responses.
ATEs offer several benefits:
- Very high throughput via parallel site testing
- Advanced instruments and switching for at-speed testing
- Deep diagnostics and root cause analysis
- Can often be re-deployed for different products
The main drawbacks of ATEs are the high upfront cost and longer programming time. However, for high-volume products, the benefits in terms of test speed and quality usually justify the investment.
FAQ
What’s the best way to select PCB Tools?
Selecting the best PCB tools requires carefully assessing your specific needs and budget. Key factors to consider include:
- PCB complexity and density
- Production volume (prototype vs low volume vs high volume)
- Required test coverage and fault diagnosis
- Available skill sets and training
- Compatibility with existing tools and processes
It’s a good idea to define clear requirements and compare offerings from multiple vendors before making a decision. Attending industry trade shows and talking to peers can provide valuable insights.
How much do PCB tools cost?
PCB tool costs span a wide range depending on the type of tool and the performance level. Some rough estimates:
- PCB design software: Free to $10k+ per seat
- Desktop prototyping: $5k to $50k
- Automated assembly: $25k to $250k
- Flying probe testers: $100k to $500k
- In-circuit testers: $200k to $1M+
- Automated test equipment: $500k to $5M+
In addition to upfront costs, it’s important to factor in recurring costs for maintenance, calibration, and upgrades over the tool’s lifespan.
What skills are needed to use PCB tools effectively?
Using PCB tools effectively requires a mix of technical skills and knowledge, such as:
- Electronics and PCB design principles
- Soldering and rework techniques
- Programming and debugging
- Statistical process control and quality management
- Familiarity with relevant standards (IPC, IEEE, ISO)
Specific training may be required for complex tools like ATEs and boundary scan systems. Many equipment vendors and organizations like IPC offer courses and certifications.
How do I know what level of test coverage I need?
The required test coverage depends on factors like the PCB’s mission criticality, expected production volume, and target defect rate. More complex boards usually require higher coverage.
Some guidelines:
- Visual inspection: Catches 80-90% of common defects
- In-circuit test: ~95% typical coverage
- Flying probe: 90-95% typical coverage
- Boundary scan: Up to 100% pin-level coverage for JTAG devices
- Functional test: Catches systemic defects not detectable by other methods
A good strategy is to use a combination of methods to achieve the target coverage while balancing cost and throughput. Coverage analysis tools can help identify gaps.
What PCB Trends should I be aware of?
The world of PCBs and electronics is constantly evolving. Some key trends to watch include:
- Continued miniaturization and increasing component density
- Growing use of high-speed and high-frequency designs
- Adoption of new materials like metal core and flexible PCBs
- Increasing use of additive manufacturing technologies
- Growing focus on sustainability and environmental impact
- More sophisticated supply chain security and anti-counterfeiting measures
Keeping up with industry news, attending conferences and webinars, and networking with peers can help you stay informed about the latest tools and best practices.
As PCBs grow more complex and sophisticated, having the right programming and testing tools is more critical than ever. By understanding the key types of tools, their applications, and selection criteria, you can make informed decisions that optimize your budget, throughput, and quality. Effective use of these tools is key to success in today’s fast-paced, quality-focused electronics industry.
0 Comments