Introduction to Circuit Board Techniques
A circuit board, also known as a printed circuit board (PCB), is the foundation of most electronic devices. It is a flat board made of insulating material, such as fiberglass or plastic, with conductive tracks, pads, and other features etched onto its surface. These conductive elements connect various components, such as resistors, capacitors, and integrated circuits, to create a functional electronic circuit.
Building a circuit board requires a combination of technical knowledge, practical skills, and attention to detail. In this article, we will explore 11 essential techniques for constructing a reliable and efficient circuit board.
1. Schematic Design
Understanding the Importance of Schematic Design
The first step in building a circuit board is creating a schematic diagram. A schematic is a visual representation of the electronic circuit, showing how components are connected. It serves as a blueprint for the PCB layout and helps identify potential issues before the physical board is fabricated.
Key Elements of a Schematic Design
A well-designed schematic should include:
- Component symbols: Standardized symbols representing each component in the circuit
- Connection lines: Lines indicating the electrical connections between components
- Labels: Descriptive labels for components, pins, and nets
- Power and ground symbols: Symbols representing the power supply and ground connections
Best Practices for Schematic Design
To create an effective schematic, follow these best practices:
- Use a consistent naming convention for components and nets
- Organize the schematic logically, grouping related components together
- Provide clear and concise labels for improved readability
- double-check the schematic for errors before proceeding to PCB layout
2. PCB Layout
The Role of PCB Layout in Circuit Board Design
Once the schematic is complete, the next step is to create the PCB layout. The layout determines the physical placement of components and the routing of conductive tracks on the circuit board. A well-designed layout ensures proper functionality, minimizes noise and interference, and facilitates efficient manufacturing.
Considerations for PCB Layout
When designing a PCB layout, consider the following factors:
- Component placement: Arrange components to minimize the length of conductive tracks and reduce signal interference
- Track width and spacing: Ensure tracks are wide enough to handle the required current and spaced appropriately to avoid crosstalk
- Grounding and shielding: Implement proper grounding and shielding techniques to reduce electromagnetic interference (EMI)
- Manufacturing constraints: Consider the limitations of the PCB Fabrication process, such as minimum track width and spacing
PCB Layout Tools and Techniques
To create a PCB layout, use specialized software tools, such as:
- EDA (Electronic Design Automation) software: Comprehensive tools for schematic capture and PCB layout, e.g., Altium Designer, KiCad, or Eagle
- PCB layout guidelines: Follow industry-standard guidelines, such as the IPC-2221 standard, for track width, spacing, and hole sizes
- Design rule checking (DRC): Use DRC tools to verify that the layout adheres to the specified design rules and constraints
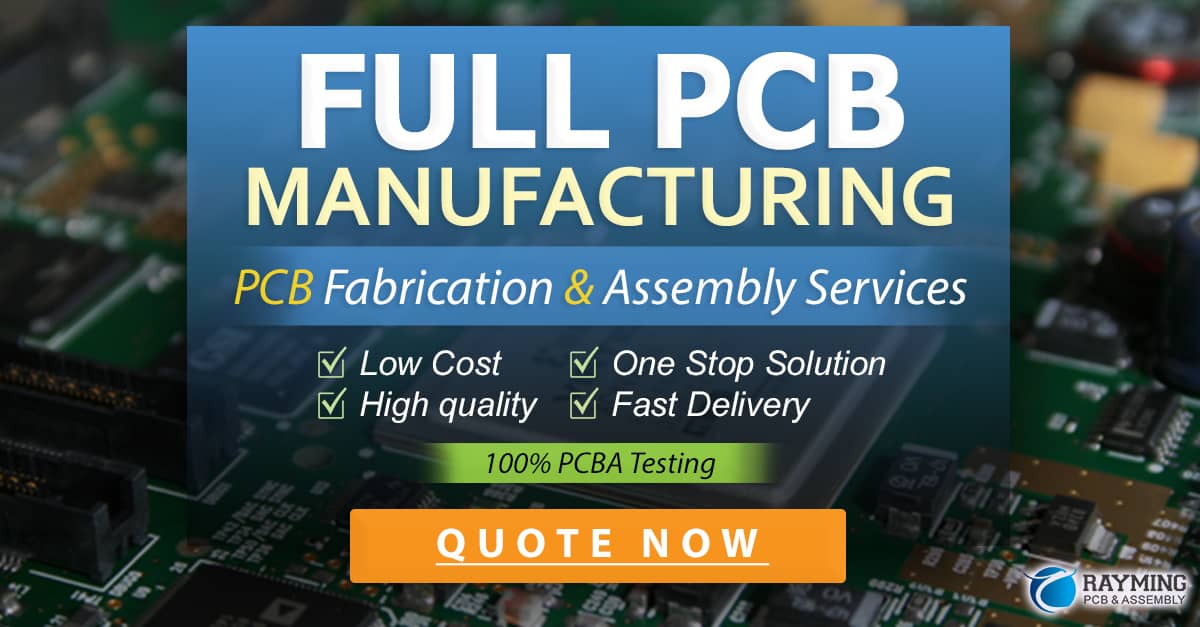
3. Component Selection
Importance of Choosing the Right Components
Selecting the appropriate components is crucial for the success of a circuit board. The right components ensure the desired functionality, reliability, and compatibility with the overall design.
Factors to Consider When Selecting Components
When choosing components for a circuit board, consider the following factors:
- Electrical specifications: Ensure the component’s ratings, such as voltage, current, and power dissipation, meet the circuit requirements
- Package type: Choose a component package that is compatible with the PCB layout and manufacturing process, e.g., through-hole or surface-mount
- Availability and cost: Consider the availability and cost of components, especially for large-scale production
- Environmental factors: Select components that can withstand the expected operating conditions, such as temperature, humidity, and vibration
Component Datasheets and Specifications
To make informed decisions about component selection, consult the following resources:
- Datasheets: Detailed technical specifications provided by the component manufacturer
- Application notes: Additional guidance on component usage and best practices
- Supplier catalogs: Comprehensive listings of available components from various suppliers
4. Soldering Techniques
The Importance of Proper Soldering
Soldering is the process of joining electronic components to the circuit board using a conductive alloy called solder. Proper soldering is essential for creating reliable electrical connections and ensuring the long-term performance of the circuit board.
Types of Soldering
There are two main types of soldering used in Circuit board assembly:
- Through-hole soldering: Components with long leads are inserted through holes in the PCB and soldered on the opposite side
- Surface-mount soldering: Components with small pads or leads are soldered directly onto the surface of the PCB
Soldering Tools and Equipment
To perform soldering effectively, use the following tools and equipment:
- Soldering iron: A hand tool that heats the solder and components to create a connection
- Solder: A conductive alloy, typically made of tin and lead (Sn/Pb) or lead-free alternatives
- Flux: A chemical agent that helps the solder flow and adhere to the components and PCB
- Solder wick: A braided wire used to remove excess solder from joints
- Solder paste: A mixture of solder particles and flux, used in surface-mount soldering
Soldering Best Practices
To achieve high-quality solder joints, follow these best practices:
- Use the appropriate soldering iron tip size and temperature for the job
- Apply the right amount of solder to create a concave fillet between the component and PCB
- Ensure the component and PCB are clean and free of oxidation before soldering
- Avoid overheating the components or PCB, which can cause damage
- Inspect the solder joints visually and with a multimeter to verify proper connections
5. Testing and Debugging
The Importance of Testing and Debugging
Testing and debugging are essential steps in building a circuit board. They help identify and resolve issues that may affect the functionality, reliability, or safety of the electronic device.
Types of Testing
There are several types of testing performed on circuit boards:
- Visual inspection: Checking for visible defects, such as solder bridges, missing components, or damaged traces
- Continuity testing: Verifying that the desired electrical connections exist between components and tracks
- Functional testing: Ensuring that the circuit board performs its intended function under various operating conditions
- Boundary scan testing: Using built-in test circuitry to diagnose faults in digital components and interconnects
Debugging Techniques
When a circuit board fails testing, use the following debugging techniques to identify and resolve the issue:
- Divide and conquer: Isolate the problem by testing sections of the circuit independently
- Signal tracing: Use an oscilloscope or logic analyzer to trace signals through the circuit and identify anomalies
- Comparative analysis: Compare the faulty board to a known working board to pinpoint differences
- Component substitution: Replace suspected faulty components with known good ones to determine the root cause
Test Equipment and Tools
To perform testing and debugging effectively, use the following equipment and tools:
- Digital multimeter (DMM): Measures voltage, current, resistance, and continuity
- Oscilloscope: Displays and analyzes time-varying signals in the circuit
- Logic analyzer: Captures and displays digital signals and bus transactions
- In-circuit emulator (ICE): Allows debugging of embedded software on the target hardware
6. Design for Manufacturing (DFM)
The Concept of Design for Manufacturing
Design for Manufacturing (DFM) is an approach that optimizes the circuit board design for efficient and cost-effective manufacturing. DFM considers the limitations and capabilities of the manufacturing process during the design phase to minimize defects, reduce costs, and improve yield.
DFM Guidelines
To implement DFM effectively, follow these guidelines:
- Adhere to the manufacturer’s design rules for minimum track width, spacing, and hole sizes
- Use standardized component packages and footprints to simplify assembly
- Avoid sharp corners and acute angles in the PCB layout to prevent manufacturing defects
- Provide adequate clearance around components for automated assembly equipment
- Minimize the number of unique components and processes to reduce inventory and setup costs
Collaboration with Manufacturing Partners
To ensure successful DFM, collaborate closely with manufacturing partners:
- Communicate the design intent and requirements clearly to the manufacturer
- Request feedback and suggestions from the manufacturer during the design process
- Provide complete and accurate documentation, including the schematic, layout, and bill of materials (BOM)
- Conduct regular design reviews with the manufacturer to identify and resolve potential issues
7. Electromagnetic Compatibility (EMC)
The Importance of Electromagnetic Compatibility
Electromagnetic Compatibility (EMC) is the ability of electronic devices to operate correctly in their electromagnetic environment without causing or suffering from excessive interference. Ensuring EMC is crucial for the reliability, safety, and regulatory compliance of circuit boards.
Sources of Electromagnetic Interference (EMI)
Electromagnetic Interference (EMI) can originate from various sources, such as:
- Switching power supplies
- High-speed digital circuits
- Wireless communication devices
- Electrostatic discharge (ESD)
- External sources, such as power lines, lightning, and other electronic devices
EMC Design Techniques
To mitigate EMI and improve EMC, employ the following design techniques:
- Proper grounding: Implement a low-impedance ground plane to provide a return path for high-frequency currents
- Shielding: Use conductive enclosures, gaskets, and coatings to contain EMI within the device and prevent external interference
- Filtering: Apply power line filters, ferrite beads, and decoupling capacitors to suppress high-frequency noise
- PCB layout: Minimize loop areas, separate sensitive signals from noisy circuits, and use ground planes to reduce coupling
EMC Testing and Compliance
To ensure EMC compliance, follow these steps:
- Conduct EMC testing in a controlled environment, such as an anechoic chamber or Faraday cage
- Measure the device’s emissions and susceptibility using specialized equipment, such as spectrum analyzers and EMI receivers
- Compare the test results to the applicable EMC standards, such as FCC Part 15, CISPR 22, or MIL-STD-461
- Make necessary design modifications to meet the required EMC limits
8. Signal Integrity
The Concept of Signal Integrity
Signal Integrity (SI) refers to the quality of electrical signals transmitted through a circuit board. It ensures that the signals remain undistorted and free from excessive noise, reflections, and crosstalk. Maintaining good signal integrity is essential for the reliable operation of high-speed digital circuits.
Factors Affecting Signal Integrity
Several factors can impact signal integrity, including:
- Impedance mismatch: Differences in the characteristic impedance of the signal path, causing reflections and distortions
- Crosstalk: Unwanted coupling of signals between adjacent traces or components
- Attenuation: Loss of signal strength due to the resistance and capacitance of the traces
- Jitter: Timing variations in the signal edges, caused by noise or other factors
Signal Integrity Analysis
To analyze and optimize signal integrity, use the following techniques:
- Time-domain reflectometry (TDR): Measures the impedance profile of a signal path by sending a fast-rising pulse and observing reflections
- S-parameter analysis: Characterizes the frequency-dependent behavior of the signal path using scattering parameters
- Eye diagram analysis: Displays the superimposed waveforms of a digital signal to assess its quality and timing margin
- Simulation: Uses specialized software to model and simulate the signal behavior in the circuit board
Best Practices for Signal Integrity
To maintain good signal integrity, follow these best practices:
- Control impedance: Design traces with consistent characteristic impedance, matched to the source and load impedances
- Minimize discontinuities: Avoid abrupt changes in trace width, layer transitions, and vias that can cause reflections
- Route carefully: Separate sensitive signals from noisy traces, use differential pairs for high-speed signals, and minimize crosstalk
- Terminate properly: Use appropriate termination techniques, such as series or parallel termination, to minimize reflections
9. Thermal Management
The Importance of Thermal Management
Thermal management is the process of controlling the temperature of electronic components on a circuit board. Proper thermal management ensures that components operate within their specified temperature range, preventing overheating, reduced performance, and premature failure.
Heat Generation and Transfer
Heat in electronic components is generated by power dissipation and transferred through three main mechanisms:
- Conduction: Heat transfer through direct contact between components and the PCB
- Convection: Heat transfer from the PCB to the surrounding air through natural or forced airflow
- Radiation: Heat transfer from the PCB to the environment through electromagnetic waves
Thermal Design Techniques
To manage heat effectively in a circuit board, employ the following thermal design techniques:
- Component placement: Arrange components to minimize heat concentration and promote airflow
- PCB layout: Use large copper planes and traces to dissipate heat, and place thermal vias near high-power components
- Heat sinks: Attach metal heat sinks to dissipate heat from high-power components
- Thermal interface materials: Use thermal paste, pads, or adhesives to improve heat transfer between components and heat sinks
- Forced convection: Implement fans or blowers to enhance airflow and heat transfer
Thermal Analysis and Simulation
To predict and optimize the thermal performance of a circuit board, use thermal analysis and simulation tools:
- Thermal resistance network: Model the heat transfer paths using a network of thermal resistances and capacitances
- Finite element analysis (FEA): Simulate the temperature distribution and heat flow in the PCB using numerical methods
- Computational fluid dynamics (CFD): Analyze the airflow and convection heat transfer around the PCB
10. Prototyping and Testing
The Role of Prototyping and Testing
Prototyping and testing are essential steps in the circuit board development process. They allow designers to validate the functionality, performance, and reliability of the board before mass production. Prototyping helps identify and correct design flaws early, reducing the risk of costly mistakes and delays.
Prototyping Methods
There are several methods for prototyping circuit boards, including:
- Breadboarding: Building a temporary circuit on a solderless breadboard for quick testing and modification
- PCB Prototyping: Fabricating a small batch of PCBs using rapid prototyping techniques, such as desktop milling or 3D printing
- Modular prototyping: Using pre-built modules or development boards to test specific functions or components
Testing Strategies
To thoroughly test a prototype circuit board, employ the following testing strategies:
- Functional testing: Verify that the board performs its intended functions under various operating conditions
- Performance testing: Measure the board’s key performance indicators, such as speed, accuracy, and power consumption
- Environmental testing: Expose the board to extreme temperatures, humidity, vibration, and shock to assess its durability
- Reliability testing: Conduct accelerated life testing or stress testing to predict the board’s long-term reliability
Test Automation and Documentation
To streamline the testing process and ensure consistency, consider the following practices:
- Automated testing: Use software tools to automate repetitive tests and data collection
- Test fixtures: Design and build custom test fixtures to facilitate consistent and efficient testing
- Test documentation: Maintain detailed test plans, procedures, and reports to track progress and communicate results
- Version control: Use a version control system to manage hardware and software revisions throughout the prototyping and testing process
11. Documentation and version control
The Importance of Documentation and Version Control
Documentation and version control are critical aspects of circuit board development. They ensure that the design information is accurately captured, maintained, and communicated throughout the product lifecycle. Effective documentation and version control help prevent errors, facilitate collaboration, and simplify future maintenance and upgrades.
Types of Documentation
Circuit board documentation typically includes the following:
- Schematic diagram: A graphical representation of the circuit’s components and connections
- PCB layout: The physical design of the circuit board, showing component placement and routing
- Bill of Materials (BOM): A list of all components used in the circuit board, including their part numbers, quantities, and suppliers
- Assembly drawings: Detailed instructions for assembling the circuit board, including component orientation and soldering techniques
- Test procedures: Step-by-step guides for verifying the functionality and performance of the circuit board
Version Control Systems
Version control systems help manage changes to the circuit board design files over time. They allow multiple team members to work on the same project simultaneously, track revisions, and revert to previous versions if necessary. Popular version control systems for hardware development include:
- Git: A distributed version control system widely used for software development, adapted for hardware projects
- Subversion (SVN): A centralized version control system that maintains a single repository for all project files
- PLM (Product Lifecycle Management) tools: Integrated systems that manage the complete product lifecycle, including design, manufacturing, and maintenance
Best Practices for Documentation and Version Control
To effectively manage documentation and version control, follow these best practices:
- Establish a consistent naming convention for files, components, and revisions
- Maintain a central repository for all project files, accessible to all team members
- Use meaningful commit messages and tags to describe changes and milestones
- Regularly back up the project files and repository to prevent data loss
- Define access controls and permissions to ensure data integrity and security
FAQ
1. What is the difference between a schematic diagram and a PCB layout?
A schematic diagram is a graphical representation of the electronic circuit, showing the components and their connections using standardized symbols. It focuses on the logical relationship between components, without considering their physical placement.
0 Comments