What is Impedance Control and Why is it Important?
Impedance control refers to the techniques used to match the impedance of interconnects (like PCB traces) with the impedance of source and load components. It is a critical aspect of high-speed PCB design for maintaining signal integrity and avoiding issues like reflections, crosstalk, and electromagnetic interference (EMI).
When the impedance of the transmission line does not match the impedance of the source or load, part of the signal energy is reflected back to the source instead of being delivered to the load. These reflections can cause signal distortions, undershoot/overshoot, ringing, and even false triggering of logic circuits. At high frequencies, even small impedance mismatches can significantly degrade signal quality.
Proper impedance control helps to:
– Minimize reflections and ensure clean signal transmission
– Reduce crosstalk between adjacent traces
– Limit EMI radiation from PCB traces
– Maintain correct logic levels and timing
So how can you implement effective impedance control in your PCB designs? Here are 10 key techniques:
1. Determine the Target Impedance
The first step is to determine the target impedance for your transmission lines based on the impedance of source and load components. Some common standard impedances are:
Impedance | Application |
---|---|
50 ohm | RF/microwave, USB, Ethernet, HDMI, PCIe |
75 ohm | Video, CATV, Telecom |
100 ohm | SCSI, Firewire, Twisted pair Ethernet |
The target impedance is usually specified by the standards for the specific interface or chosen to match the impedance of cables/connectors. Consult the datasheets of the components you are using.
2. Choose the Right Dielectric Material
The dielectric material of the PCB substrate has a major influence on the impedance of traces. Two key properties to consider are:
– Dielectric constant (Dk): Affects the capacitance of the trace. Higher Dk means lower impedance. Typical values are around 4.
– Dissipation factor (Df): Affects the losses in the trace. Higher Df means more attenuation. Typical values are 0.02 or less.
For good impedance control, choose a dielectric material with stable Dk over the frequency range of interest and low Df to minimize losses. Some commonly used materials are:
Material | Dk | Df | Applications |
---|---|---|---|
FR-4 | 4.3 | 0.02 | General purpose, low cost |
Rogers 4003C | 3.38 | 0.0027 | High frequency, low loss |
Isola I-Tera | 3.45 | 0.0031 | High speed digital |
Nelco N4000-13 | 3.7 | 0.009 | Controlled impedance |
Work with your PCB fabricator to select the right material grade for your requirements and budget.
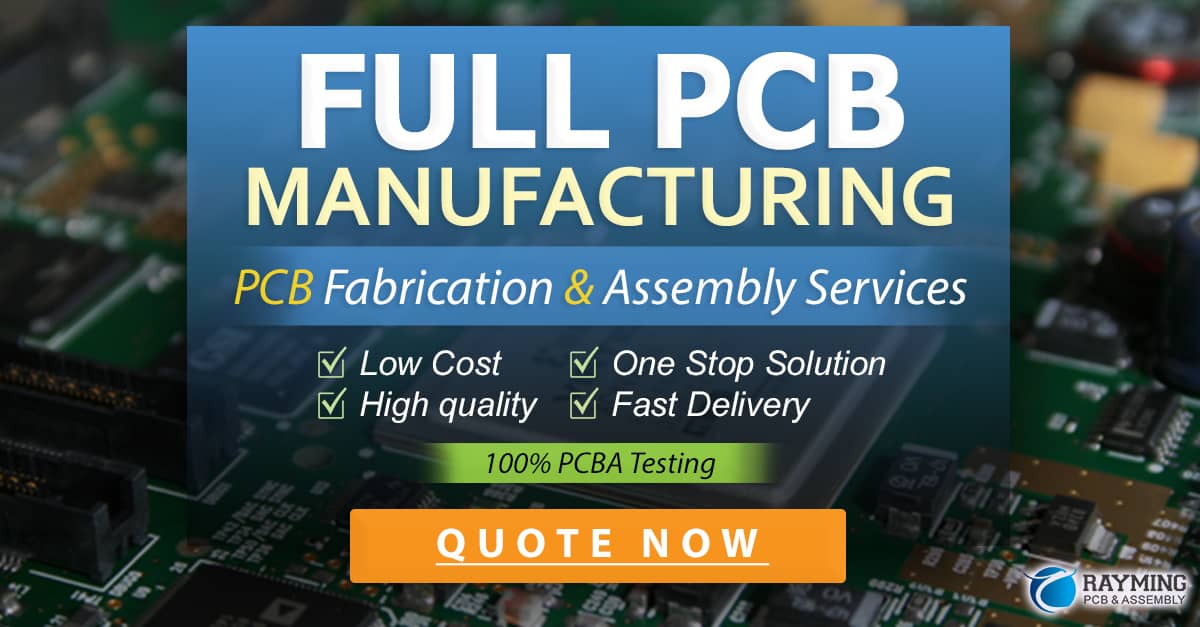
3. Set the Trace Geometry
The geometry of the traces – their width, thickness, and spacing from other traces and planes – determines their impedance. There are two main types of transmission lines on PCBs:
– Microstrip: Trace on the outer layer, above a ground plane. Easier to route but prone to EMI.
– Stripline: Trace embedded between two ground planes in inner layer. Better isolation but harder to route.
The impedance of these structures depends on:
– Trace width (W)
– Trace thickness (T)
– Dielectric height (H) between trace and ground/power plane
– Spacing (S) from adjacent traces
– Dielectric constant of substrate (Dk)
Formulas and calculators are available to determine the right trace dimensions for your target impedance. For example, for a 50 ohm microstrip with 1 oz copper (35 um thick) on 8 mil FR-4 (Dk=4.3):
W = 0.25 mm
H = 0.2 mm (8 mil)
S > 3W to avoid crosstalk
Your PCB design tool may have a built-in impedance calculator. If not, many free calculators are available online.
4. Minimize Discontinuities
Any discontinuity or change in the geometry of a trace will cause impedance mismatch and reflections. Common discontinuities to avoid are:
– Vias: Minimize the use of vias and stubs. Use smaller via holes. Remove unused pads.
– Bends: Use 45 degree bends instead of 90 degree. Keep the bends smooth and gradual.
– Connectors: Choose connectors with the same impedance as the traces. Minimize pad size.
– Stubs: Avoid stubs on traces. Keep the stubs as short as possible if unavoidable.
– Unmatched lengths: Match the lengths of differential pairs and buses. Avoid large length differences.
Route the traces as smoothly and consistently as possible. Perform an impedance check in your PCB design tool to identify and correct any impedance discontinuities.
5. Maintain Consistent Spacing
Maintain a consistent spacing between traces and reference planes (ground or power) along the entire length. Any changes in the spacing will change the impedance.
- Keep a solid reference plane under/over the traces
- Avoid splitting the planes with slots or holes under the traces
- Route the traces symmetrically in inner layers between planes
- Keep the trace spacing from plane larger than the trace width to avoid changing impedance
- Space the traces sufficiently from plane edges (at least 5x the trace width)
Use your PCB tool’s design rule checks (DRC) to enforce consistent spacing and reference plane rules.
6. Terminate Properly
Proper termination of traces is essential to control reflections. The termination resistors should match the impedance of the traces. Some common termination schemes are:
– Series: A resistor in series with the signal near the source
– Parallel: A resistor in parallel at the end of the line near the load
– Thevenin: A voltage divider at the end of the line
– AC: A resistor and capacitor in series at the end of the line
The choice of termination depends on the type of signal, the noise margins, and the drive strength of the source. Consult the datasheets and app notes for the components you are using.
7. Simulate and Tune
Before finalizing your PCB layout, simulate your critical traces to verify the impedance and signal integrity. Many PCB design tools have built-in signal integrity simulators. If not, you can export your layout to a 3rd party field solver tool.
In the simulation:
– Define the driver and receiver models
– Apply the expected rise/fall times
– Set the correct dielectric properties
– Simulate with the actual trace lengths
– Check for reflections, crosstalk, overshoot, and EMI
Tune the trace geometry and terminations until you get clean eye diagrams meeting your requirements. Compare the simulation with measurements on a prototype if possible.
8. Control Manufacturing Variations
PCB manufacturing variations can significantly affect impedance – especially the trace width and dielectric height. Work closely with your PCB fabricator to control these variations.
- Specify the impedance tolerance (e.g. ±10%) on your fab drawing
- Define the stack-up clearly with the dielectric thicknesses
- Use impedance controlled base materials with low Dk variation
- Verify the capabilities of your fabricator for fine width control
- Allow for etch factor variation in your width calculations
- Request impedance test coupons to verify the actual values
A good fabricator should be able to control the impedance within ±10% of target. Tighter tolerances are possible at higher cost.
9. Decouple and Isolate
Proper power supply decoupling is important to maintain clean and stable reference voltages for impedance control.
– Place decoupling caps close to ICs
– Use wide and short traces for power
– Provide solid power and ground planes
– Isolate analog and digital supplies
Also isolate the high-speed traces from other signals to avoid crosstalk.
– Route them away from other traces
– Provide guard traces or planes
– Use striplines instead of microstrips
– Keep them short and direct
10. Document and Review
Properly document your impedance requirements and control measures. This includes:
– The list of impedance controlled nets
– The target impedance and tolerance
– The stack-up and spacing rules
– The simulation and test reports
– The board fab notes
Review these with all the stakeholders – the design engineers, the layout designers, the fabricators, and the test engineers. Make sure everyone understands and agrees on the requirements.
Frequently Asked Questions
1. What happens if I don’t control impedance on my PCB?
Not controlling impedance can lead to signal integrity problems like:
– Reflections causing ringing, overshoot, and undershoot
– Crosstalk between traces causing noise and jitter
– EMI from the traces causing interference to other systems
– Inconsistent logic levels and timing errors
These problems get worse with faster edge rates and longer trace lengths. They can cause intermittent errors or even complete failures.
2. How much does impedance control add to the cost of PCB fabrication?
Impedance control can add about 10-30% to the fab cost of a PCB depending on:
– The number of controlled layers
– The target impedance tolerance
– The base material selection
– The testing and documentation requirements
However, this is usually a small fraction of the total development and debug cost. The cost of a board spin or product recall due to signal integrity issues would be much higher.
3. Do I need to control impedance for every signal on my board?
No, you don’t need to control impedance for every signal. The signals that typically need impedance control are:
– High-speed clocks and buses (>50 MHz)
– Sensitive analog signals
– Signals going off-board through cables
– Long traces (>1/6 wavelength at the operating frequency)
For most other signals, just following good layout practices like minimizing stubs and providing clean references is sufficient. Simulate or measure if you are unsure.
4. What is the difference between single-ended and differential impedance?
Single-ended impedance is the impedance of one trace with respect to a reference plane (ground or power). It is used for signals that switch with respect to a fixed reference. The typical values are 50 ohms or 75 ohms.
Differential impedance is the impedance between two traces that switch in opposite phase. It is used for differential pair signals like USB, LVDS, etc. The typical value is 100 ohms. The spacing between the traces is critical for differential impedance.
5. How can I verify the actual impedance on my fabricated board?
There are several ways to verify the impedance on a fabricated PCB:
– Measure with a time-domain reflectometer (TDR)
– Measure with a vector network analyzer (VNA)
– Measure the resonance frequency of test coupons
– Simulate with a field solver and the actual fab cross-section
Many PCB Fabricators will include impedance test coupons and measurements as part of their service. You can also do sample measurements yourself if you have access to the right equipment.
Conclusion
We have seen that impedance control is a critical aspect of high-speed PCB design for maintaining signal integrity. By following these 10 techniques – choosing the right materials, setting the right geometry, minimizing discontinuities, simulating and testing – you can avoid most signal integrity problems.
However, impedance control is not a one-time task. It requires close collaboration between the design, layout, fabrication, and test teams throughout the product development cycle. It also requires proper documentation and review to ensure that all the requirements are met.
With the right tools, processes, and partners, you can design PCBs that meet your impedance and signal integrity goals. The investment in impedance control will pay off in terms of fewer design iterations, faster debugging, and more reliable products.
0 Comments