Introduction to PCB Assembly
Printed Circuit Board (PCB) assembly is the process of soldering electronic components onto a printed circuit board to create a functional electronic device. There are two main types of PCB assembly: Through Hole (THT) and Surface Mount Technology (SMT). Both methods have their advantages and disadvantages, and the choice between them depends on the specific requirements of the project.
In this article, we will explore the 10 key differences between Through Hole and SMT assembly, including their manufacturing processes, component types, design considerations, and more. By understanding these differences, you can make an informed decision when choosing the right assembly method for your PCB project.
What is Through Hole Assembly?
Through Hole assembly, also known as THT (Through Hole Technology), is a traditional PCB assembly method where electronic components are inserted into drilled holes on the PCB and soldered onto the opposite side. The components used in Through Hole assembly have long leads that are inserted through the holes and then bent to secure them in place before soldering.
Advantages of Through Hole Assembly
- Strong mechanical connections
- Easier to repair or replace components
- Better for high-power applications
- Suitable for larger components
Disadvantages of Through Hole Assembly
- Slower assembly process
- Larger PCB size due to drilled holes
- Higher manufacturing costs
- Limited component density
What is SMT Assembly?
Surface Mount Technology (SMT) assembly is a more modern PCB assembly method where electronic components are mounted directly onto the surface of the PCB without the need for drilled holes. SMT components are smaller and have shorter leads or no leads at all, allowing for higher component density and smaller PCB sizes.
Advantages of SMT Assembly
- Faster assembly process
- Higher component density
- Smaller PCB size
- Lower manufacturing costs
Disadvantages of SMT Assembly
- Weaker mechanical connections
- More difficult to repair or replace components
- Requires specialized equipment and skills
- Not suitable for high-power applications
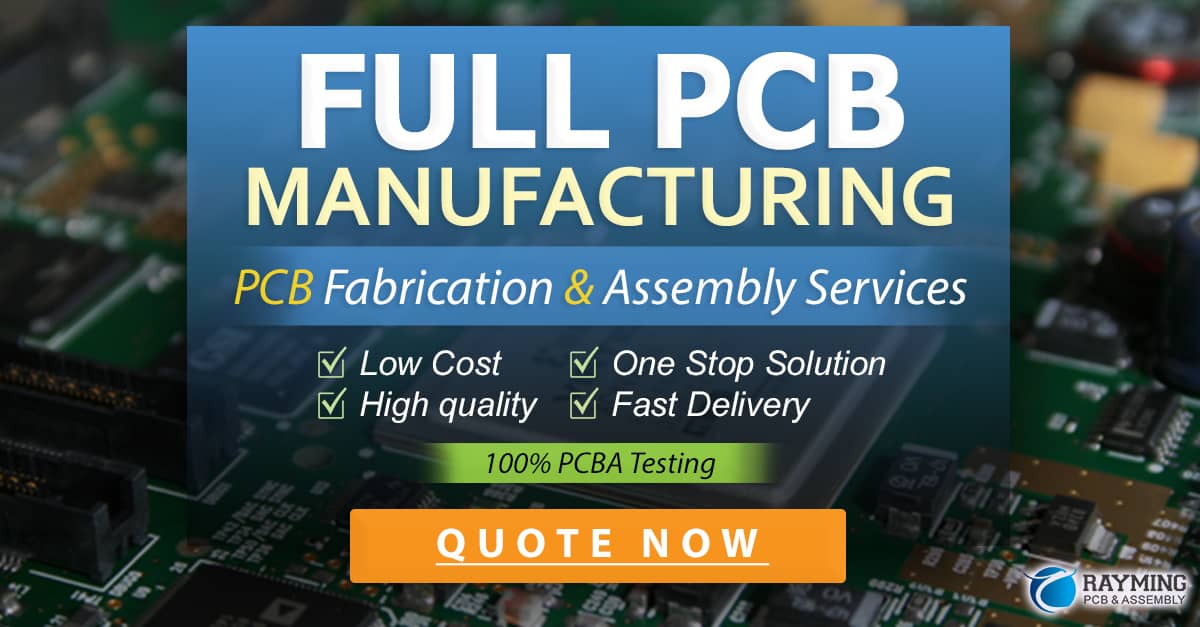
10 Differences Between Through Hole and SMT Assembly
- Component Types
- Through Hole: Uses components with long leads that are inserted into drilled holes
-
SMT: Uses smaller components with short leads or no leads that are mounted directly onto the PCB surface
- Through Hole: Requires drilled holes for component leads, resulting in larger PCB sizes
-
SMT: No need for drilled holes, allowing for smaller PCB sizes and higher component density
-
Assembly Process
- Through Hole: Components are inserted into drilled holes and soldered onto the opposite side
-
SMT: Components are placed directly onto the PCB surface and soldered using reflow or wave soldering techniques
-
Mechanical Strength
- Through Hole: Provides stronger mechanical connections due to the component leads being inserted through the PCB
-
SMT: Has weaker mechanical connections as components are only attached to the PCB surface
-
Repairability
- Through Hole: Easier to repair or replace individual components
-
SMT: More difficult to repair or replace components due to the smaller size and lack of leads
-
Manufacturing Speed
- Through Hole: Slower assembly process due to the need for manual insertion of components
-
SMT: Faster assembly process as components can be placed and soldered automatically
-
Manufacturing Costs
- Through Hole: Higher manufacturing costs due to slower assembly process and larger PCB sizes
-
SMT: Lower manufacturing costs due to faster assembly process and smaller PCB sizes
-
Component Density
- Through Hole: Limited component density due to the need for drilled holes and larger component sizes
-
SMT: Higher component density as smaller components can be placed closer together
-
Power Handling
- Through Hole: Better suited for high-power applications due to the stronger mechanical connections
-
SMT: Less suitable for high-power applications due to the weaker mechanical connections
-
Equipment and Skills
- Through Hole: Can be assembled with basic soldering equipment and skills
- SMT: Requires specialized equipment (e.g., pick-and-place machines, reflow ovens) and skills for assembly
Comparison Table: Through Hole vs. SMT Assembly
Factor | Through Hole Assembly | SMT Assembly |
---|---|---|
Component Types | Long leads, inserted into holes | Short leads or no leads, mounted on surface |
PCB Design | Requires drilled holes, larger size | No drilled holes, smaller size |
Assembly Process | Manual insertion, soldered on opposite side | Automated placement, soldered on surface |
Mechanical Strength | Stronger connections | Weaker connections |
Repairability | Easier to repair | More difficult to repair |
Manufacturing Speed | Slower | Faster |
Manufacturing Costs | Higher | Lower |
Component Density | Limited | Higher |
Power Handling | Better for high-power | Less suitable for high-power |
Equipment and Skills | Basic soldering | Specialized equipment and skills |
Choosing Between Through Hole and SMT Assembly
When deciding between Through Hole and SMT assembly for your PCB project, consider the following factors:
- Project requirements (e.g., size, power handling, component density)
- Manufacturing budget and timeline
- Available equipment and skills
- Expected product lifespan and maintenance needs
In many cases, a combination of both Through Hole and SMT assembly (known as mixed assembly) can be used to achieve the best balance of performance, cost, and reliability.
Frequently Asked Questions (FAQ)
-
Q: Can Through Hole and SMT components be used on the same PCB?
A: Yes, it is possible to use both Through Hole and SMT components on the same PCB in a mixed assembly process. This allows for the benefits of both assembly methods to be utilized in a single design. -
Q: Are SMT components more expensive than Through Hole components?
A: In general, SMT components are less expensive than their Through Hole counterparts due to their smaller size and the automated assembly process. However, the overall cost of the PCB assembly will depend on various factors, such as the specific components used and the manufacturing volume. -
Q: Which assembly method is better for prototyping?
A: Through Hole assembly is often preferred for prototyping due to the easier manual assembly process and the ability to repair or replace components more easily. SMT assembly becomes more cost-effective and efficient for larger production runs. -
Q: Can SMT components handle high-power applications?
A: While SMT components are less suitable for high-power applications compared to Through Hole components, there are some SMT components designed specifically for high-power handling. However, in general, Through Hole assembly is still preferred for high-power applications due to the stronger mechanical connections. -
Q: Is it possible to rework or repair SMT assemblies?
A: Yes, it is possible to rework or repair SMT assemblies, but it requires specialized equipment and skills compared to Through Hole assemblies. Rework stations with hot air or infrared heating, as well as microscopes and fine-tipped soldering irons, are often used for SMT Rework and repair.
Conclusion
In conclusion, Through Hole and SMT assembly are two distinct PCB assembly methods with their own advantages and disadvantages. Through Hole assembly offers stronger mechanical connections and easier repairability, while SMT assembly provides faster manufacturing, higher component density, and lower costs. The choice between the two methods depends on the specific requirements of the project, such as size, power handling, budget, and timeline.
By understanding the 10 key differences between Through Hole and SMT assembly outlined in this article, you can make an informed decision when selecting the most appropriate assembly method for your PCB project. In some cases, a mixed assembly approach combining both Through Hole and SMT components may be the best solution.
As technology continues to advance, SMT assembly has become increasingly popular due to its advantages in manufacturing efficiency and miniaturization. However, Through Hole assembly still has its place in the electronics industry, particularly for high-power applications and projects requiring stronger mechanical connections.
Ultimately, the success of your PCB assembly project relies on careful consideration of your specific needs and the selection of the most suitable assembly method to meet those requirements.
0 Comments