Introduction
In the world of electronic product development, time-to-market is a critical factor in determining the success of a product. Rapid PCB Prototyping is essential to accelerate the development process and ensure that the final product meets the desired specifications. However, the success of rapid PCB prototyping heavily relies on the optimization of the Bill of Materials (BOM). In this article, we will discuss why optimizing the BOM is crucial for rapid PCB prototyping and how it can help you streamline your development process.
What is a Bill of Materials (BOM)?
A Bill of Materials (BOM) is a comprehensive list of all the components, parts, and materials required to manufacture a product. In the context of PCB prototyping, a BOM typically includes the following information:
Component | Description | Quantity | Manufacturer | Part Number | Supplier |
---|---|---|---|---|---|
Resistor | 10kΩ, 0.25W | 10 | Yageo | RC0603FR-0710KL | Digi-Key |
Capacitor | 0.1µF, 50V | 5 | Murata | GRM188R71H104KA93D | Mouser |
IC | ATmega328P | 1 | Microchip | ATMEGA328P-AU | Newark |
A well-structured BOM ensures that all the necessary components are accounted for and helps prevent delays caused by missing or incorrect parts.
The Importance of BOM Optimization in Rapid PCB Prototyping
1. Reducing Lead Times
One of the primary goals of rapid PCB prototyping is to minimize lead times. By optimizing your BOM, you can ensure that all the required components are readily available and can be sourced quickly. This helps prevent delays caused by long lead times for specific components.
2. Cost Savings
An optimized BOM can help you identify cost-saving opportunities. By carefully selecting components and suppliers, you can reduce the overall cost of your PCB Prototype without compromising on quality. Additionally, by consolidating your component purchases, you may be able to negotiate better prices with suppliers.
3. Improved Component Availability
When creating your BOM, it’s essential to choose components that are readily available and have multiple suppliers. This helps mitigate the risk of supply chain disruptions and ensures that you can source the necessary components when needed.
4. Enhanced Design Flexibility
An optimized BOM allows for greater design flexibility. By selecting components with multiple footprint options or pin-compatible alternatives, you can make design changes more easily without requiring significant BOM revisions.
5. Streamlined Assembly Process
A well-organized BOM can streamline the PCB assembly process. By providing clear and accurate information about the components and their placement, you can reduce the likelihood of assembly errors and improve the overall efficiency of the prototyping process.
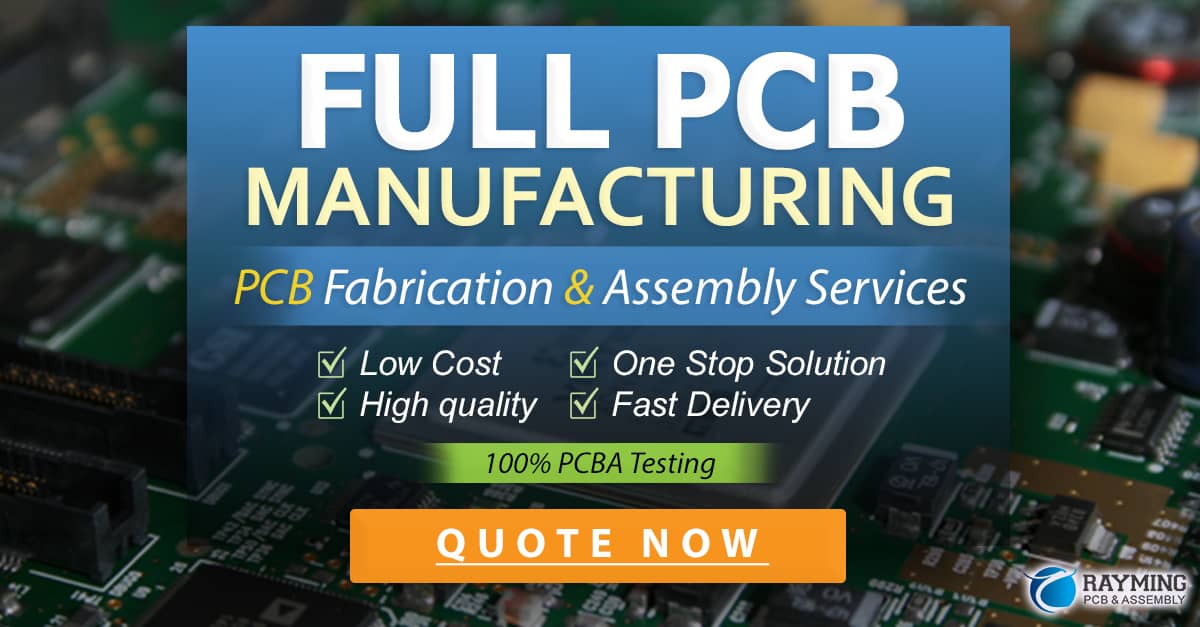
Strategies for Optimizing Your BOM
1. Standardize Components
Whenever possible, standardize the components used in your PCB design. This helps reduce the overall number of unique parts in your BOM, making it easier to manage and reducing the risk of obsolescence.
2. Use Generic Components
Using generic components instead of manufacturer-specific parts can provide greater flexibility in sourcing and help reduce costs. Generic components are often more readily available and have multiple suppliers, reducing the risk of supply chain disruptions.
3. Consider Alternative Components
When selecting components for your BOM, consider alternative parts that may offer similar performance at a lower cost or with better availability. This can help optimize your BOM without compromising on the functionality of your PCB prototype.
4. Collaborate with Suppliers
Establish strong relationships with your component suppliers and involve them early in the PCB prototyping process. They can provide valuable insights into component availability, lead times, and potential alternatives, helping you optimize your BOM more effectively.
5. Regularly Review and Update Your BOM
As your PCB design evolves, it’s essential to regularly review and update your BOM. This helps ensure that your BOM remains accurate and up-to-date, reducing the risk of delays or errors during the prototyping process.
FAQ
-
Q: What is the difference between a BOM and a parts list?
A: A BOM is a more comprehensive document that includes information about the components, their quantities, and their relationships to one another. A parts list, on the other hand, is a simpler list of the individual components used in a design. -
Q: How can I ensure that my BOM is accurate?
A: To ensure the accuracy of your BOM, double-check the component information, quantities, and part numbers. It’s also a good idea to have a peer or supervisor review your BOM before finalizing it. -
Q: What should I do if a component in my BOM becomes obsolete?
A: If a component becomes obsolete, you’ll need to find a suitable replacement. Work with your suppliers to identify alternative components that meet your design requirements and update your BOM accordingly. -
Q: Can I use the same BOM for multiple PCB designs?
A: While some components may be common across multiple designs, it’s generally best to create a unique BOM for each PCB design to ensure accuracy and avoid confusion. -
Q: How often should I review and update my BOM?
A: It’s a good practice to review and update your BOM whenever there are significant changes to your PCB design or when you encounter issues with component availability or pricing.
Conclusion
Optimizing your Bill of Materials is a critical step in ensuring the success of your rapid PCB prototyping efforts. By carefully selecting components, collaborating with suppliers, and regularly reviewing and updating your BOM, you can reduce lead times, save costs, and improve the overall efficiency of your prototyping process. Remember, a well-optimized BOM is the foundation of a successful PCB prototype and, ultimately, a successful electronic product.
0 Comments