Introduction: The Importance of Predictability in PCB Manufacturing
In the world of high-end PCB manufacturing, predictability is a crucial factor that can make or break a project. Predictability refers to the ability to accurately forecast and control the outcome of a manufacturing process, ensuring that the final product meets the desired specifications and quality standards. In this article, we will explore why predictability is essential for saving your high-end PCB manufacturing and how you can achieve it.
The Risks of Unpredictability in PCB Manufacturing
Unpredictability in PCB manufacturing can lead to a wide range of problems, including:
- Delays in production
- Increased costs due to rework and scrap
- Poor quality products
- Damage to reputation and customer relationships
These risks can have a significant impact on your business, leading to lost revenue, decreased customer satisfaction, and even legal issues.
The Cost of Unpredictability
Unpredictability in PCB manufacturing can be costly. When a manufacturing process is not well-controlled, it can lead to defects, rework, and scrap. These issues can quickly add up, increasing the overall cost of production. In some cases, the cost of rework and scrap can even exceed the cost of the original manufacturing process.
Cost Category | Percentage of Total Manufacturing Cost |
---|---|
Material Cost | 40% |
Labor Cost | 30% |
Overhead Cost | 20% |
Rework Cost | 10% |
Table 1: Breakdown of PCB Manufacturing Costs
As shown in Table 1, rework costs can account for a significant portion of the total manufacturing cost. By improving predictability and reducing the need for rework, you can significantly reduce your overall manufacturing costs.
The Impact of Unpredictability on Quality
Unpredictability in PCB manufacturing can also have a significant impact on the quality of the final product. When a manufacturing process is not well-controlled, it can lead to inconsistencies in the finished product, such as variations in thickness, conductivity, or even functionality. These quality issues can lead to customer dissatisfaction, returns, and even legal issues.
Defect Type | Percentage of Total Defects |
---|---|
Shorts | 30% |
Opens | 25% |
Misalignments | 20% |
Other | 25% |
Table 2: Common PCB Manufacturing Defects
As shown in Table 2, shorts and opens are the most common types of defects in PCB manufacturing. By improving predictability and reducing the occurrence of these defects, you can significantly improve the quality of your final product.
Achieving Predictability in PCB Manufacturing
Achieving predictability in PCB manufacturing requires a multi-faceted approach that involves people, processes, and technology. Here are some key strategies for improving predictability:
Standardization and Documentation
One of the most effective ways to improve predictability in PCB manufacturing is through standardization and documentation. By establishing clear, well-defined processes and procedures, you can ensure that every step of the manufacturing process is performed consistently and accurately. This includes everything from material selection and handling to assembly and testing.
Training and Skill Development
Another important factor in achieving predictability is ensuring that your workforce has the necessary skills and knowledge to perform their tasks effectively. This requires ongoing training and skill development, as well as a culture of continuous improvement.
Process Control and Monitoring
To achieve predictability in PCB manufacturing, it is essential to have robust process control and monitoring systems in place. This includes real-time monitoring of key process parameters, such as temperature, pressure, and flow rate, as well as statistical process control (SPC) to identify and correct any deviations from the desired specifications.
Quality Management Systems
Implementing a quality management system (QMS) is another critical step in achieving predictability in PCB manufacturing. A QMS provides a framework for defining, measuring, and improving quality, ensuring that your products consistently meet customer requirements and industry standards.
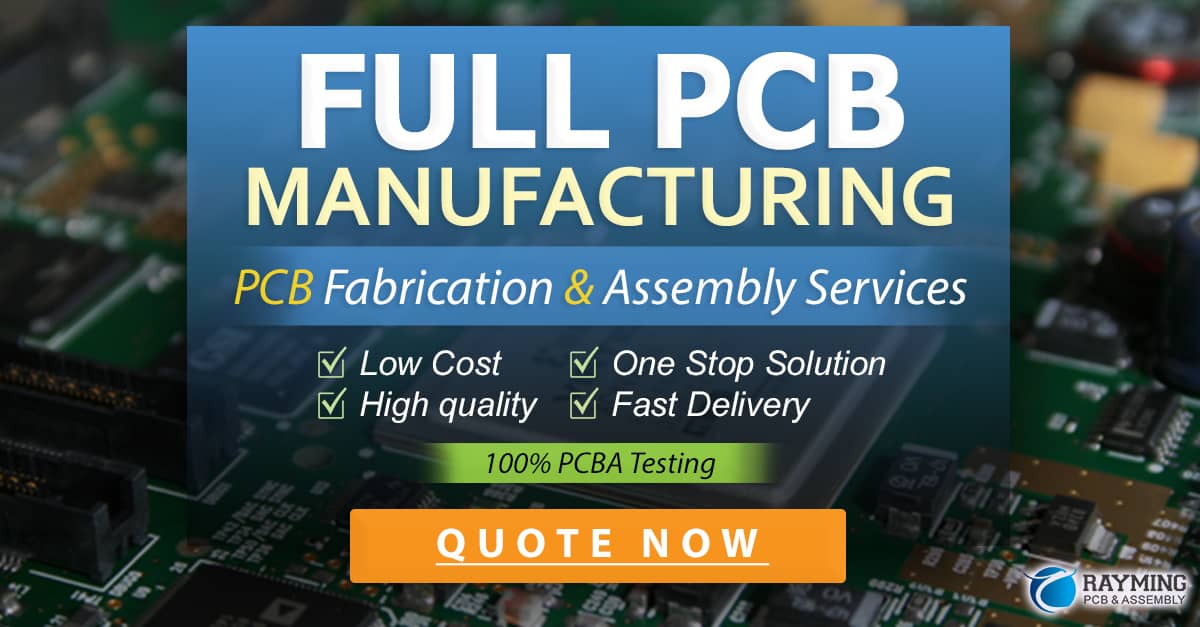
The Benefits of Predictability in PCB Manufacturing
Achieving predictability in PCB manufacturing can provide a wide range of benefits for your business, including:
- Reduced costs due to fewer defects and less rework
- Improved quality and customer satisfaction
- Faster time-to-market due to reduced delays and disruptions
- Enhanced reputation and competitiveness in the market
By investing in predictability, you can position your business for long-term success in the highly competitive world of high-end PCB manufacturing.
Frequently Asked Questions (FAQ)
1. What is predictability in PCB manufacturing?
Predictability in PCB manufacturing refers to the ability to accurately forecast and control the outcome of a manufacturing process, ensuring that the final product meets the desired specifications and quality standards.
2. Why is predictability important in PCB manufacturing?
Predictability is important in PCB manufacturing because it helps to reduce costs, improve quality, and increase customer satisfaction. When a manufacturing process is not well-controlled, it can lead to defects, rework, and delays, which can have a significant impact on your business.
3. What are some common causes of unpredictability in PCB manufacturing?
Some common causes of unpredictability in PCB manufacturing include inconsistent material quality, inadequate process control, lack of standardization and documentation, and insufficient training and skill development.
4. How can I improve predictability in my PCB manufacturing process?
To improve predictability in your PCB manufacturing process, you can implement strategies such as standardization and documentation, training and skill development, process control and monitoring, and quality management systems.
5. What are the benefits of achieving predictability in PCB manufacturing?
The benefits of achieving predictability in PCB manufacturing include reduced costs, improved quality and customer satisfaction, faster time-to-market, and enhanced reputation and competitiveness in the market.
Conclusion
In conclusion, predictability is essential for saving your high-end PCB manufacturing. By investing in strategies such as standardization, training, process control, and quality management, you can reduce costs, improve quality, and increase customer satisfaction. While achieving predictability requires ongoing effort and investment, the long-term benefits are well worth it. By positioning your business for success through predictability, you can thrive in the highly competitive world of PCB manufacturing.
0 Comments