Introduction to PCB Soldermask
Printed Circuit Boards (PCBs) are essential components in modern electronics, forming the backbone of countless devices we use every day. One crucial aspect of PCB manufacturing is the application of soldermask, a protective layer that covers the copper traces on the board. While soldermask comes in various colors, green has emerged as the most commonly used option in PCB fabrication. In this article, we will explore the reasons behind the popularity of green soldermask and its benefits in the PCB manufacturing process.
What is PCB Soldermask?
PCB soldermask, also known as solder resist or solder mask, is a thin layer of polymer applied to the surface of a printed circuit board. Its primary purpose is to protect the copper traces from oxidation, prevent solder bridges from forming during the soldering process, and provide electrical insulation between conductive areas. Soldermask also helps to improve the overall durability and reliability of the PCB.
Functions of PCB Soldermask
- Protection against oxidation
- Prevention of solder bridges
- Electrical insulation
- Improved durability and reliability
The Popularity of Green Soldermask
While soldermask is available in a variety of colors, including red, blue, yellow, and black, green has become the most widely used color in PCB fabrication. There are several reasons why green soldermask has gained such popularity:
1. Visibility and Contrast
One of the primary reasons for the widespread use of green soldermask is its excellent visibility and contrast. The green color provides a clear distinction between the soldermask and the copper traces, making it easier for technicians to inspect the PCB for any defects or issues during the manufacturing process. This high contrast also facilitates the identification of component placement and orientation, reducing the likelihood of assembly errors.
2. Reduced Eye Strain
Working with PCBs often involves long hours of focusing on intricate details. The green color of the soldermask is known to be less straining on the eyes compared to other colors, particularly when viewed under bright lighting conditions. This reduced eye strain contributes to improved productivity and fewer errors during the assembly and inspection processes.
3. Photosensitivity and Curing Process
Green soldermask has proven to be highly compatible with the photoimaging and curing processes used in PCB fabrication. The green color absorbs the appropriate wavelengths of light during the exposure process, resulting in a well-defined and accurate soldermask pattern. Additionally, green soldermask tends to cure more efficiently than other colors, ensuring a consistent and reliable protective layer on the PCB surface.
4. Industry Standard and Familiarity
Over time, green soldermask has become an industry standard, with a vast majority of PCB manufacturers adopting it as their default color choice. This widespread use has led to a high level of familiarity among engineers, technicians, and assemblers, making it easier for them to work with green soldermask PCBs. The consistency in color also helps to streamline the manufacturing process and ensures compatibility across different PCB designs and manufacturers.
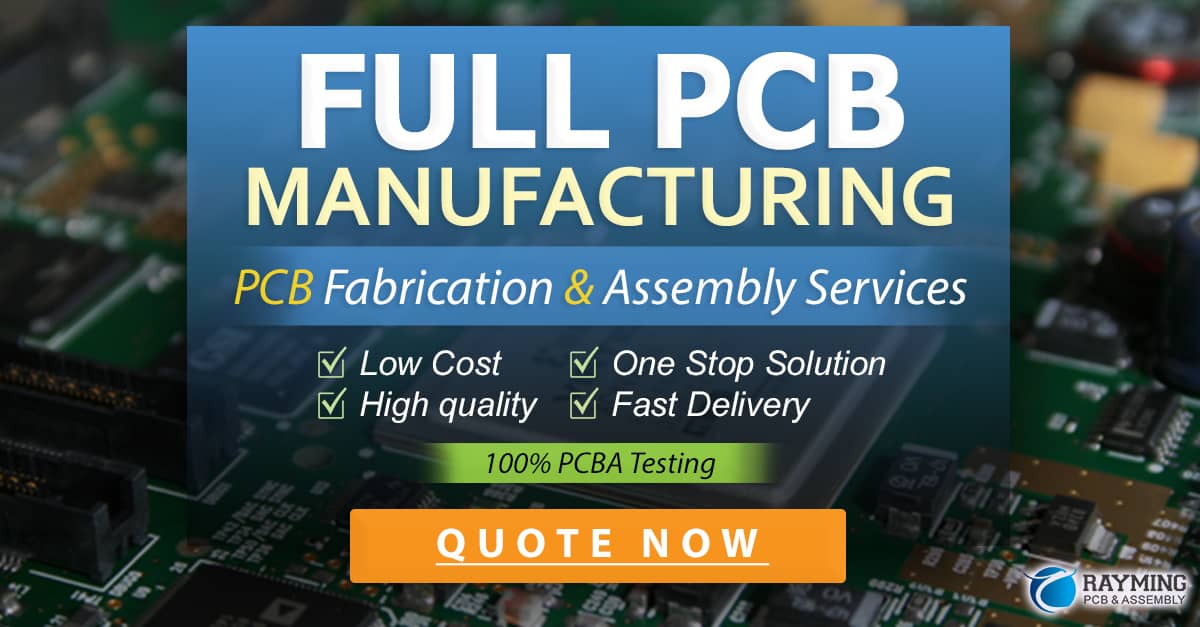
Benefits of Green Soldermask in PCB Fabrication
The use of green soldermask in PCB fabrication offers several key benefits that contribute to the overall quality and reliability of the final product:
1. Enhanced Protection
Green soldermask provides excellent protection against oxidation, moisture, and other environmental factors that can degrade the performance of the PCB over time. By shielding the copper traces from these elements, green soldermask helps to extend the lifespan of the PCB and maintain its electrical integrity.
2. Improved Solderability
The green soldermask acts as a barrier between the copper traces and the solder, preventing the formation of solder bridges that can cause short circuits and other functional issues. This improved solderability results in higher-quality solder joints and reduces the risk of defects during the assembly process.
3. Increased Durability
The application of green soldermask enhances the overall durability of the PCB, making it more resistant to scratches, abrasions, and other physical damage. This increased durability is particularly important for PCBs that are exposed to harsh environments or subjected to frequent handling.
4. Better Electrical Insulation
Green soldermask provides effective electrical insulation between the conductive areas of the PCB, reducing the risk of short circuits and signal interference. This improved insulation contributes to the overall reliability and performance of the electronic device in which the PCB is installed.
Choosing the Right Soldermask Color
While green soldermask is the most common choice in PCB fabrication, there may be instances where alternative colors are preferred or required. Some factors to consider when selecting a soldermask color include:
1. Design Aesthetics
In certain applications, such as consumer electronics or high-end audio equipment, the visual appearance of the PCB may be a significant consideration. In these cases, alternative soldermask colors like black, red, or blue may be chosen to match the overall design aesthetic of the device.
2. Specific Application Requirements
Some specialized applications may have specific requirements for soldermask color. For example, in medical devices or aerospace applications, white soldermask may be preferred for its ability to reflect heat and minimize thermal stress on the PCB.
3. Contrast and Visibility Needs
While green soldermask provides excellent contrast and visibility in most scenarios, there may be situations where a different color offers better performance. For instance, in applications with limited lighting or where the PCB is viewed through colored lenses, alternative soldermask colors may provide enhanced visibility and contrast.
Frequently Asked Questions (FAQ)
-
Q: Is green soldermask the only color option available for PCBs?
A: No, soldermask is available in various colors, including red, blue, yellow, black, and white. However, green is the most commonly used color in PCB fabrication. -
Q: Can I specify a custom soldermask color for my PCB design?
A: Yes, most PCB manufacturers offer the option to specify a custom soldermask color. However, this may incur additional costs and longer lead times compared to using the standard green soldermask. -
Q: Does the choice of soldermask color affect the performance of the PCB?
A: In most cases, the choice of soldermask color does not directly impact the electrical performance of the PCB. However, some colors may offer specific benefits in certain applications, such as white soldermask for improved heat reflection. -
Q: Is green soldermask more expensive than other colors?
A: No, green soldermask is typically the most cost-effective option due to its widespread use and availability. Other colors may incur slightly higher costs due to lower demand and production volumes. -
Q: Can I change the soldermask color of an existing PCB design?
A: Yes, it is possible to change the soldermask color of an existing PCB design. However, this will require updates to the design files and may involve additional costs and lead times from the PCB manufacturer.
Conclusion
Green soldermask has become the most commonly used color in PCB fabrication due to its numerous benefits, including excellent visibility and contrast, reduced eye strain, compatibility with photoimaging and curing processes, and its status as an industry standard. The use of green soldermask enhances the protection, solderability, durability, and electrical insulation of PCBs, contributing to the overall quality and reliability of electronic devices.
While alternative soldermask colors are available and may be preferred in specific applications, green remains the go-to choice for the majority of PCB manufacturers and designers. By understanding the reasons behind the popularity of green soldermask and its benefits in PCB fabrication, engineers and technicians can make informed decisions when designing and manufacturing PCBs for various applications.
As the electronics industry continues to evolve, it is likely that green soldermask will maintain its dominant position in PCB fabrication. However, advancements in materials science and manufacturing technologies may lead to the development of new soldermask formulations and colors that offer even better performance and functionality. Regardless of these future developments, the importance of selecting the appropriate soldermask color for each specific application cannot be overstated, as it plays a crucial role in ensuring the quality, reliability, and longevity of the final product.
Word count: 1399
0 Comments