What is a White PCB?
A white PCB, also known as a solder mask white PCB or a white solder mask PCB, is a type of printed circuit board (PCB) that features a white solder mask coating instead of the more common green color. The solder mask is a protective layer applied to the copper traces of a PCB to prevent short circuits and provide insulation. White PCBs offer a unique aesthetic appeal and have gained popularity in various applications, including consumer electronics, lighting systems, and high-end electronic devices.
Advantages of White PCBs
- Enhanced visual appeal
- Improved contrast for text and symbols
- Better heat dissipation
- Increased durability
- Compatibility with LED lighting
How are White PCBs Manufactured?
The manufacturing process of white PCBs is similar to that of standard PCBs, with a few key differences in the solder mask application stage.
PCB Manufacturing Process Overview
- Design and layout
- Substrate selection
- Copper lamination
- Drilling
- Plating
- Etching
- Solder mask application
- Silkscreen printing
- Surface finish application
- Cutting and profiling
White Solder Mask Application
The solder mask application stage is where white PCBs differ from standard PCBs. To achieve the white color, a specialized white solder mask ink is used. This ink is typically a two-component epoxy or UV-curable material that is applied to the PCB surface using screen printing or spraying techniques.
After application, the white solder mask undergoes a curing process, which involves exposure to heat or UV light, depending on the type of ink used. This curing process ensures that the solder mask adheres properly to the PCB surface and provides the necessary insulation and protection.
Challenges in White PCB Manufacturing
While white PCBs offer various benefits, there are some challenges associated with their manufacturing process.
Color Consistency
Achieving a consistent white color across multiple PCBs can be difficult due to variations in the solder mask ink and the curing process. Manufacturers must carefully control the ink formulation and curing parameters to ensure a uniform white appearance.
Opacity
White solder masks may not provide the same level of opacity as green or other darker-colored solder masks. This can potentially lead to the visibility of underlying copper traces, especially in areas with high copper density. Manufacturers often use thicker solder mask layers or multiple coats to mitigate this issue.
Cost
The specialized white solder mask inks and the additional processing steps required for white PCBs can result in higher manufacturing costs compared to standard green PCBs. However, the cost difference has been decreasing as white PCBs become more common and manufacturing processes improve.
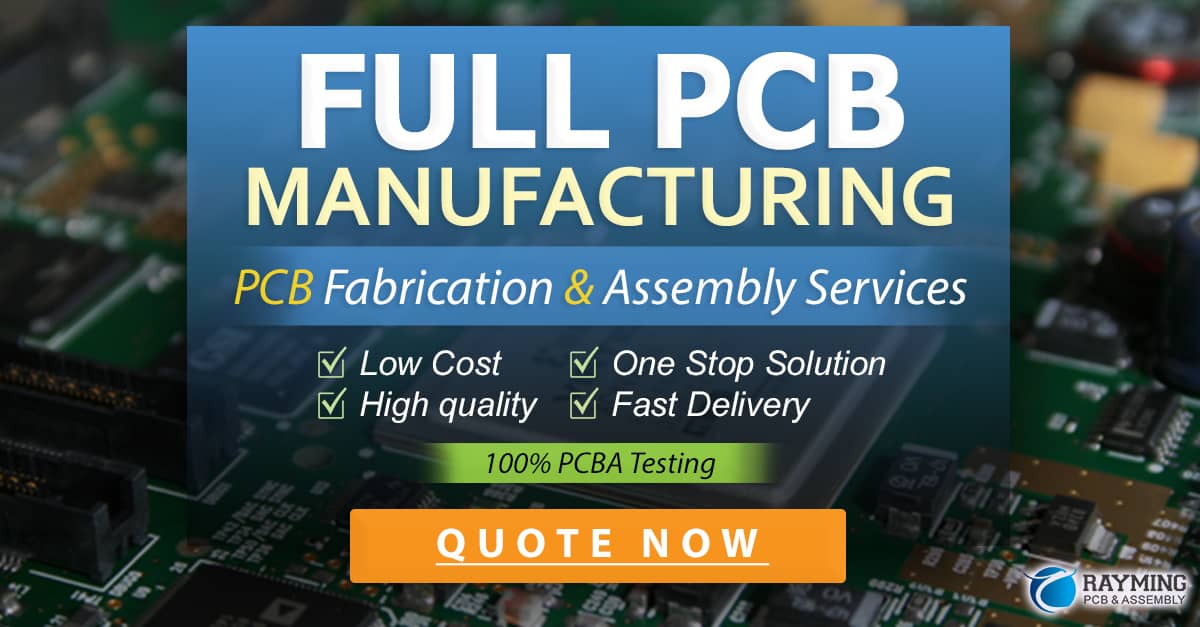
Applications of White PCBs
White PCBs have found applications in various industries and products, including:
- Consumer electronics (e.g., smartphones, tablets, laptops)
- IoT devices
- Wearable technology
- Medical devices
- Automotive electronics
- Lighting systems (e.g., LED boards)
- High-end audio equipment
The aesthetic appeal and improved contrast of white PCBs make them particularly suitable for devices with transparent or translucent enclosures, as well as products where the PCB is visible to the end-user.
Designing for White PCBs
When designing a white PCB, there are several considerations to keep in mind to ensure optimal performance and manufacturability.
Copper Trace Width and Spacing
To minimize the visibility of copper traces through the white solder mask, designers should use wider trace widths and larger spacing between traces whenever possible. This helps to improve the opacity of the white solder mask and maintain the desired aesthetic appearance.
Silkscreen Legibility
When choosing silkscreen colors for text and symbols on a white PCB, it is essential to select colors that provide sufficient contrast against the white background. Black, dark blue, or dark gray silkscreen colors are often used for optimal legibility.
Component Selection
Designers should consider the color and appearance of components when selecting them for a white PCB. Black or white components can help maintain a consistent visual theme, while colored components may provide an interesting contrast against the white background.
Design Rule Checks (DRC)
As with any PCB design, it is crucial to perform thorough design rule checks to ensure that the layout meets the manufacturing capabilities of the chosen PCB fabricator. This includes checking for minimum trace widths, clearances, and drill sizes, as well as verifying the solder mask and silkscreen layers.
White PCB Surface Finishes
In addition to the white solder mask, there are several surface finish options available for white PCBs, each with its own advantages and disadvantages.
Surface Finish | Advantages | Disadvantages |
---|---|---|
HASL (Hot Air Solder Leveling) | – Low cost – Good solderability – Suitable for through-hole components |
– Uneven surface – Potential for solder bridging – Not suitable for fine-pitch components |
ENIG (Electroless Nickel Immersion Gold) | – Flat surface – Excellent solderability – Good shelf life – Suitable for fine-pitch components |
– Higher cost than HASL – Potential for black pad syndrome |
OSP (Organic Solderability Preservative) | – Low cost – Flat surface – Suitable for fine-pitch components |
– Limited shelf life – Potential for poor solderability if not stored properly |
Immersion Silver | – Flat surface – Good solderability – Lower cost than ENIG |
– Limited shelf life – Potential for tarnishing over time |
Immersion Tin | – Flat surface – Good solderability – Lower cost than ENIG |
– Limited shelf life – Potential for Tin Whiskers |
The choice of surface finish depends on the specific requirements of the project, including cost, solderability, shelf life, and component compatibility.
Frequently Asked Questions (FAQ)
- Are white PCBs more expensive than green PCBs?
-
Yes, white PCBs are generally more expensive than standard green PCBs due to the specialized white solder mask inks and additional processing steps required.
-
Can white PCBs be used for all types of electronic devices?
-
White PCBs can be used in a wide range of electronic devices, but they are particularly well-suited for applications where aesthetic appeal and improved contrast are important, such as consumer electronics, lighting systems, and high-end audio equipment.
-
Do white PCBs have any performance advantages over green PCBs?
-
White PCBs offer improved heat dissipation compared to green PCBs, as the white color reflects more light and heat. This can help to reduce the operating temperature of the PCB and improve its overall performance and reliability.
-
Are there any special considerations when soldering components to a white PCB?
-
The soldering process for white PCBs is similar to that of standard PCBs. However, it is important to use solder wire and flux that are compatible with the chosen surface finish to ensure good solderability and avoid any potential issues.
-
How can I ensure the best visual appearance of my white PCB design?
- To achieve the best visual appearance for a white PCB, consider using wider copper traces, larger spacing between traces, and black or dark-colored silkscreen for text and symbols. Additionally, selecting black or white components can help maintain a consistent visual theme.
Conclusion
White PCBs offer a unique and visually appealing alternative to standard green PCBs, providing enhanced contrast, improved heat dissipation, and increased durability. While there are challenges associated with their manufacturing process, such as color consistency and opacity, the benefits of white PCBs have led to their adoption in various industries and applications.
When designing a white PCB, it is essential to consider factors such as copper trace width and spacing, silkscreen legibility, component selection, and design rule checks to ensure optimal performance and manufacturability. The choice of surface finish also plays a crucial role in the overall quality and reliability of the white PCB.
As white PCBs continue to gain popularity, it is likely that advances in manufacturing techniques and materials will further improve their performance and reduce their cost, making them an increasingly attractive option for a wide range of electronic devices and applications.
0 Comments