What is a Rigid PCB?
A rigid PCB, also known as a standard PCB, is a printed circuit board that is made from a solid, non-flexible material. Typically, rigid PCBs are fabricated using a substrate material called FR-4, which is a glass-reinforced epoxy laminate. The FR-4 material provides excellent mechanical strength, electrical insulation, and thermal stability, making it an ideal choice for most electronic applications.
Characteristics of Rigid PCBs
-
Rigidity: As the name suggests, rigid PCBs are stiff and do not bend or flex. They maintain their shape and structure even under moderate stress or pressure.
-
Thickness: Rigid PCBs are available in various thicknesses, typically ranging from 0.8mm to 3.2mm. The thickness depends on the number of layers and the specific application requirements.
-
Layering: Rigid PCBs can be single-sided (one conductive layer), double-sided (two conductive layers), or multi-layered (more than two conductive layers). Multi-layer rigid PCBs are used for complex designs that require high component density and intricate interconnections.
-
Durability: Due to their solid construction, rigid PCBs offer excellent durability and can withstand harsh environmental conditions, such as high temperatures, vibrations, and impacts.
Advantages of Rigid PCBs
-
Structural Integrity: The rigidity of the PCB ensures that the components remain securely in place, minimizing the risk of damage due to mechanical stress or vibrations.
-
High Density: Rigid PCBs can accommodate a large number of components and complex circuitry in a relatively small space, making them suitable for compact electronic devices.
-
Ease of Assembly: The flat and stable surface of rigid PCBs facilitates easy component placement and soldering, simplifying the assembly process.
-
Cost-effectiveness: For high-volume production, rigid PCBs are generally more cost-effective compared to flexible PCBs due to their standardized manufacturing processes and materials.
Applications of Rigid PCBs
Rigid PCBs find applications in a wide range of industries and products, including:
- Consumer electronics (smartphones, laptops, televisions)
- Industrial equipment (control systems, sensors, machinery)
- Automotive electronics (engine control units, infotainment systems)
- Medical devices (diagnostic equipment, monitoring systems)
- Aerospace and defense systems (avionics, communication devices)
What is a Flexible PCB?
A flexible PCB, also known as a flex circuit or flex PCB, is a printed circuit board that is designed to be flexible and bendable. Unlike rigid PCBs, flexible PCBs are made from thin, flexible materials such as polyimide or polyester films. These materials allow the PCB to conform to various shapes and contours, making them ideal for applications that require flexibility and space savings.
Characteristics of Flexible PCBs
-
Flexibility: Flexible PCBs can bend, twist, and fold without damaging the circuitry or components. They can conform to the shape of the enclosure or device in which they are used.
-
Thinness: Flex PCBs are typically thinner than rigid PCBs, with thicknesses ranging from 0.05mm to 0.25mm. This thinness contributes to their flexibility and allows for more compact designs.
-
Layering: Flexible PCBs can be single-sided, double-sided, or multi-layered, depending on the complexity of the design and the space constraints.
-
Lightweight: Due to their thin and flexible nature, flex PCBs are generally lighter in weight compared to rigid PCBs, making them suitable for portable and wearable devices.
Advantages of Flexible PCBs
-
Space Savings: Flex PCBs can be folded, bent, or rolled to fit into tight spaces, allowing for more compact and space-efficient designs.
-
Reduced Weight: The lightweight nature of flex PCBs contributes to overall weight reduction in electronic devices, which is particularly important for portable and wearable applications.
-
Improved Reliability: Flexible PCBs can withstand repeated bending and flexing without compromising the integrity of the circuitry, enhancing the reliability of the device.
-
Enhanced Connectivity: Flex PCBs can be used to connect multiple rigid PCBs or components in a three-dimensional space, enabling more complex and interconnected designs.
Applications of Flexible PCBs
Flexible PCBs are commonly used in applications that require flexibility, space savings, and portability, such as:
- Wearable electronics (smartwatches, fitness trackers)
- Medical devices (implantable devices, flexible sensors)
- Automotive electronics (dashboard displays, sensor connections)
- Aerospace and defense (avionics, satellite systems)
- Consumer electronics (smartphones, cameras, printers)
Rigid vs Flexible PCB: Key Differences
Now that we have a basic understanding of rigid and flexible PCBs, let’s summarize the key differences between them:
Characteristic | Rigid PCB | Flexible PCB |
---|---|---|
Material | FR-4 (glass-reinforced epoxy) | Polyimide or polyester films |
Flexibility | Stiff and non-flexible | Bendable and flexible |
Thickness | 0.8mm to 3.2mm | 0.05mm to 0.25mm |
Weight | Heavier compared to flex PCBs | Lightweight |
Durability | High durability and strength | Can withstand repeated bending |
Assembly | Easy component placement and soldering | Requires specialized assembly techniques |
Cost | More cost-effective for high volumes | Higher cost due to specialized materials and processes |
Applications | Consumer electronics, industrial equipment, automotive | Wearable devices, medical implants, aerospace |
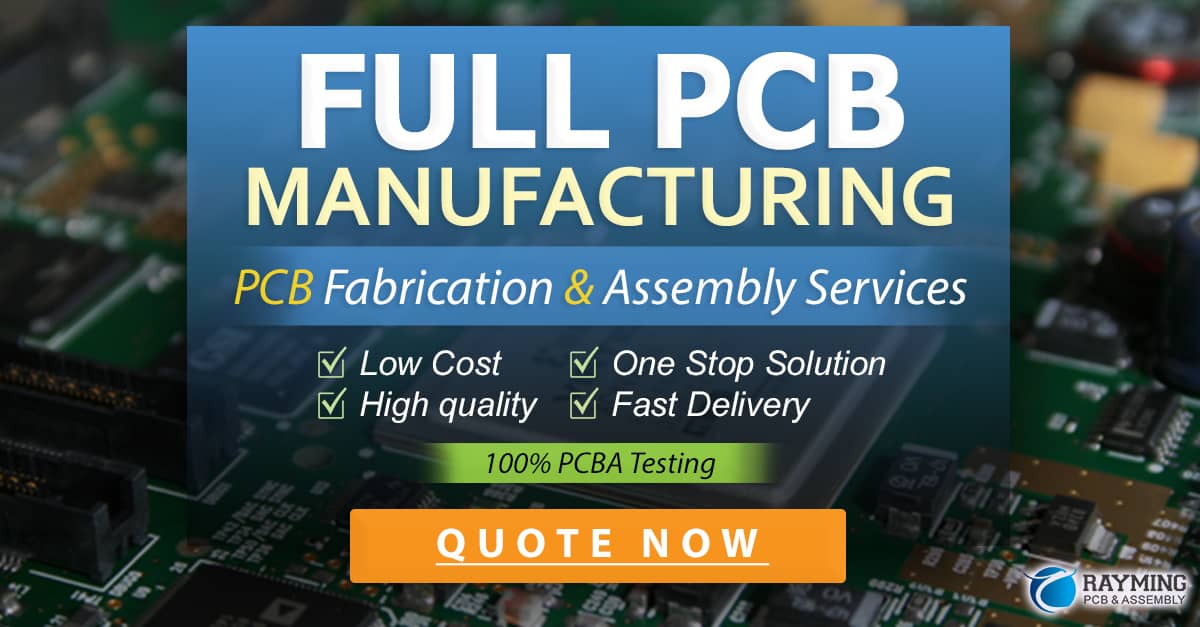
Frequently Asked Questions (FAQ)
-
Can flexible PCBs replace rigid PCBs in all applications?
No, flexible PCBs cannot replace rigid PCBs in all applications. While flex PCBs offer advantages in terms of flexibility and space savings, rigid PCBs are still preferred for applications that require high component density, structural integrity, and cost-effectiveness in high-volume production. -
Are flexible PCBs more expensive than rigid PCBs?
Yes, flexible PCBs are generally more expensive than rigid PCBs due to the specialized materials and manufacturing processes involved. The cost difference becomes more significant for low-volume production runs. -
Can rigid and flexible PCBs be combined in a single design?
Yes, it is possible to combine rigid and flexible PCBs in a single design, known as a rigid-flex PCB. Rigid-flex PCBs offer the advantages of both types, providing flexibility where needed while maintaining the structural integrity of rigid sections. -
What are the challenges in assembling flexible PCBs?
Assembling flexible PCBs requires specialized techniques compared to rigid PCBs. The flexible nature of the board can make component placement and soldering more challenging. Additionally, the choice of components and their attachment methods need to be compatible with the flexing requirements of the design. -
How do I choose between a rigid PCB and a flexible PCB for my project?
The choice between a rigid PCB and a flexible PCB depends on several factors, including the specific application requirements, space constraints, flexibility needs, durability, and cost considerations. It is essential to evaluate these factors and consult with PCB design experts to make an informed decision based on your project’s unique needs.
Conclusion
In conclusion, rigid PCBs and flexible PCBs serve different purposes and have their own unique characteristics. Rigid PCBs offer structural integrity, high component density, and cost-effectiveness for most electronic applications. On the other hand, flexible PCBs provide flexibility, space savings, and lightweight solutions for applications that require conformity and portability.
Understanding the differences between rigid and flexible PCBs is crucial for designers and engineers when selecting the appropriate type of PCB for their projects. By considering factors such as flexibility requirements, space constraints, durability, and cost, they can make informed decisions and optimize their designs accordingly.
As technology continues to evolve, the demand for both rigid and flexible PCBs will likely grow, driven by the increasing complexity and diversity of electronic devices. Whether it’s a rigid PCB powering a desktop computer or a flexible PCB enabling a wearable medical device, these circuit boards will continue to play a vital role in shaping the future of electronics.
0 Comments