Introduction to Soldermask Thickness
Soldermask, also known as solder resist or solder stop mask, is a thin layer of polymer applied to the copper traces of a printed circuit board (PCB) to prevent solder from bridging between conductors during the assembly process. The thickness of the soldermask plays a crucial role in the performance, reliability, and manufacturability of PCBs. In this article, we will explore the various aspects of soldermask thickness and its impact on PCB design and fabrication.
Importance of Soldermask Thickness
The thickness of the soldermask is a critical parameter in PCB manufacturing for several reasons:
-
Insulation: Soldermask acts as an insulating layer, preventing short circuits between adjacent copper traces. An appropriate soldermask thickness ensures adequate insulation and prevents electrical failures.
-
Solder control: Soldermask defines the areas where solder can be applied during the assembly process. The thickness of the soldermask affects the solder’s ability to adhere to the exposed copper pads and prevents solder bridges.
-
Protection: Soldermask protects the copper traces from oxidation, contamination, and mechanical damage. A sufficient soldermask thickness provides better protection and enhances the PCB’s durability.
-
Aesthetics: Soldermask also serves an aesthetic purpose by providing a uniform color to the PCB surface. The thickness of the soldermask can affect the color consistency and the overall appearance of the PCB.
Standard Soldermask Thicknesses
The soldermask thickness is typically measured in mils (thousandths of an inch) or microns (µm). The most common soldermask thicknesses used in the PCB industry are:
Thickness (mils) | Thickness (µm) | Application |
---|---|---|
0.5 – 0.8 | 12.7 – 20.3 | Standard thickness for most PCB applications |
1.0 – 1.2 | 25.4 – 30.5 | Thicker soldermask for higher insulation and protection |
2.0 – 3.0 | 50.8 – 76.2 | Very thick soldermask for specialized applications |
The choice of soldermask thickness depends on various factors such as the PCB’s intended application, the component density, the assembly process, and the manufacturing capabilities of the PCB fabricator.
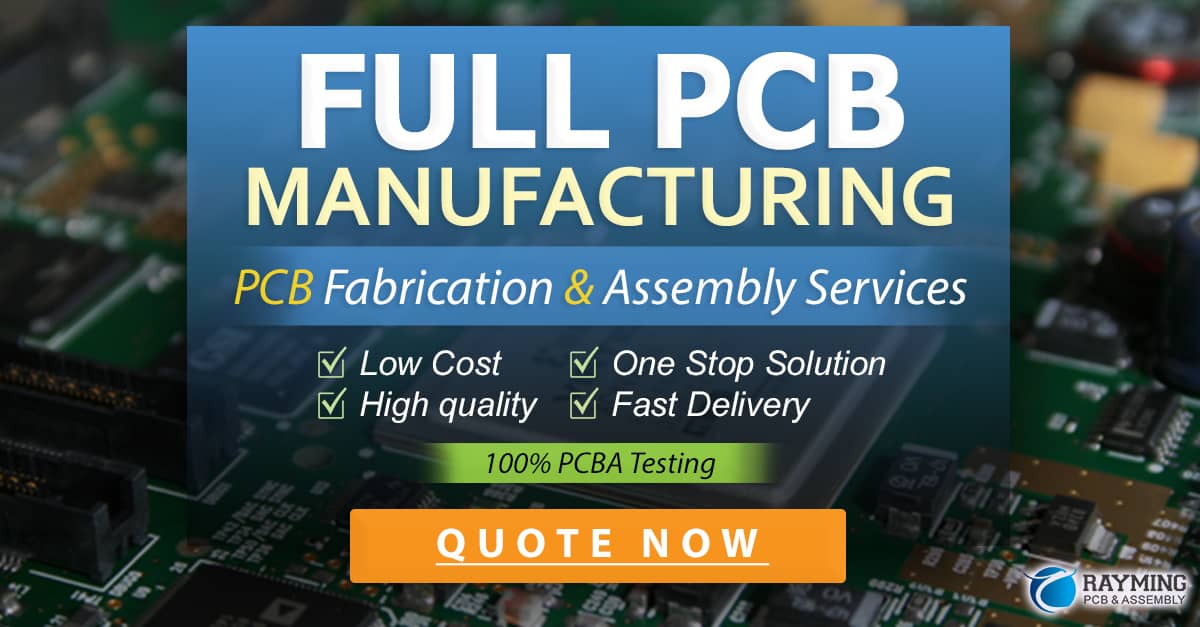
Impact on PCB Design
Clearance and Creepage
Soldermask thickness affects the clearance and creepage distances between conductors on a PCB. Clearance is the shortest distance through air between two conductors, while creepage is the shortest distance along the surface of the insulating material (soldermask) between two conductors.
Thicker soldermask increases the creepage distance, providing better insulation and reducing the risk of electrical breakdown. However, it also reduces the available space for routing traces and placing components. PCB designers must consider the soldermask thickness when determining the minimum clearance and creepage distances to ensure compliance with safety standards and optimal PCB layout.
Solder Mask Defined (SMD) vs. Non-Solder Mask Defined (NSMD) Pads
Soldermask thickness also influences the choice between SMD and NSMD pads in PCB design. SMD pads have the soldermask opening smaller than the copper pad size, while NSMD pads have the soldermask opening larger than the copper pad size.
SMD pads offer better control over the solder paste volume and provide a more consistent solder joint. However, they require tighter tolerances and may be more challenging to manufacture with thicker soldermask. NSMD pads, on the other hand, allow for easier alignment and accommodate thicker soldermask, but they may result in larger solder fillets and reduced solder joint reliability.
PCB designers must consider the soldermask thickness and the specific requirements of the application when choosing between SMD and NSMD pads.
Impact on PCB Manufacturing
Soldermask Application Methods
The soldermask thickness is influenced by the application method used during PCB manufacturing. The two primary methods for applying soldermask are:
-
Screen printing: In this method, the soldermask is applied through a fine mesh screen using a squeegee. Screen printing is suitable for thicker soldermask layers (>0.5 mils) and is the most common method used in the PCB industry.
-
Liquid photoimageable (LPI) coating: LPI coating involves applying a thin layer of photosensitive soldermask using a curtain coating or spraying process. This method is suitable for thinner soldermask layers (<0.5 mils) and offers higher resolution and finer pitch capabilities.
The choice of soldermask application method depends on the desired thickness, the required resolution, and the manufacturing capabilities of the PCB fabricator.
Soldermask Curing Process
After the soldermask is applied, it undergoes a curing process to harden and adhere to the PCB surface. The curing process can be carried out using either UV (ultraviolet) or thermal curing methods.
UV curing is the most common method and involves exposing the soldermask to UV light for a specific duration. The UV light initiates a polymerization reaction, causing the soldermask to harden and cross-link. UV curing is faster and more energy-efficient compared to thermal curing.
Thermal curing involves heating the soldermask to a specific temperature for a certain period. This method is slower and more energy-intensive than UV curing but may be necessary for certain soldermask materials or thicker layers.
The soldermask thickness can affect the curing process, as thicker layers may require longer exposure times or higher temperatures to ensure complete curing.
Soldermask Thickness Tolerance
PCB fabricators specify a tolerance range for the soldermask thickness to account for process variations. The typical tolerance for soldermask thickness is ±0.1 mils (±2.54 µm) for standard thicknesses and ±0.2 mils (±5.08 µm) for thicker layers.
PCB designers must consider the soldermask thickness tolerance when specifying the design requirements and ensure that the tolerance is compatible with the manufacturing capabilities of the chosen PCB fabricator.
Impact on PCB Assembly
Solder Paste Printing
Soldermask thickness plays a role in the solder paste printing process during PCB assembly. The thickness of the soldermask affects the solder paste’s ability to adhere to the exposed copper pads and the volume of solder paste deposited.
Thicker soldermask can lead to a higher volume of solder paste being deposited, which may result in solder bridging or excessive solder fillets. Conversely, thinner soldermask may result in insufficient solder paste volume, leading to weak solder joints or open connections.
PCB assemblers must optimize the solder paste printing process, considering the soldermask thickness, to ensure the right amount of solder paste is deposited on the pads for reliable solder joints.
Component Placement Accuracy
Soldermask thickness can also impact the accuracy of component placement during PCB assembly. Thicker soldermask may create a larger gap between the component leads and the copper pads, making it more challenging to achieve precise alignment.
Additionally, thicker soldermask may cause the component to sit higher on the PCB surface, affecting the overall height profile of the assembled board. This can be a concern for applications with strict height restrictions or when using automated optical inspection (AOI) systems for quality control.
PCB assemblers must account for the soldermask thickness when setting up the component placement machines and ensure that the placement accuracy meets the required tolerances.
Frequently Asked Questions (FAQ)
-
What is the standard soldermask thickness for PCBs?
The standard soldermask thickness for most PCB applications ranges from 0.5 to 0.8 mils (12.7 to 20.3 µm). However, thicker soldermask layers of 1.0 to 1.2 mils (25.4 to 30.5 µm) or even 2.0 to 3.0 mils (50.8 to 76.2 µm) may be used for higher insulation and protection requirements. -
How does soldermask thickness affect PCB design?
Soldermask thickness affects PCB design in terms of clearance and creepage distances between conductors, as well as the choice between solder mask defined (SMD) and non-solder mask defined (NSMD) pads. Thicker soldermask increases creepage distance but reduces available space for routing, while thinner soldermask allows for tighter tolerances but may compromise insulation and protection. -
What are the common methods for applying soldermask?
The two common methods for applying soldermask are screen printing and liquid photoimageable (LPI) coating. Screen printing is suitable for thicker soldermask layers (>0.5 mils) and is widely used in the PCB industry. LPI coating is used for thinner soldermask layers (<0.5 mils) and offers higher resolution and finer pitch capabilities. -
How does soldermask thickness impact PCB assembly?
Soldermask thickness can affect the solder paste printing process and the component placement accuracy during PCB assembly. Thicker soldermask may lead to excessive solder paste deposition and challenges in achieving precise component alignment, while thinner soldermask may result in insufficient solder paste volume and weak solder joints. -
What should PCB designers consider when specifying soldermask thickness?
PCB designers should consider factors such as the intended application, component density, assembly process, and manufacturing capabilities of the PCB fabricator when specifying soldermask thickness. They must also account for the soldermask thickness tolerance and ensure compatibility with the chosen manufacturing process and assembly requirements.
Conclusion
Soldermask thickness is a critical parameter in PCB design and manufacturing, with significant impacts on the performance, reliability, and manufacturability of PCBs. It affects various aspects of PCB design, such as clearance and creepage distances, pad definition, and component placement. Soldermask thickness also influences the manufacturing process, including the application method, curing process, and thickness tolerance.
PCB designers and fabricators must carefully consider the soldermask thickness throughout the design and manufacturing stages to ensure optimal PCB functionality and reliability. By understanding the implications of soldermask thickness and making informed decisions based on the specific requirements of the application, PCB professionals can create high-quality, robust, and manufacturable PCBs.
As PCB technology continues to evolve, with increasing component density and miniaturization, the importance of soldermask thickness will only grow. Staying up-to-date with the latest advancements in soldermask materials, application methods, and design guidelines is essential for success in the dynamic and ever-changing world of PCB design and manufacturing.
0 Comments