What is a Via?
A via is a small hole drilled through a PCB that allows electrical connections to be made between different layers of the board. Vias are an essential component of multi-layer PCBs, as they enable the routing of signals and power between layers.
There are several types of vias used in PCB design:
Via Type | Description |
---|---|
Through Hole Via | A via that goes through all layers of the PCB |
Blind Via | A via that connects an outer layer to an inner layer, but does not go through the entire board |
Buried Via | A via that connects two or more inner layers, but does not extend to the outer layers |
Microvia | A small via, typically less than 0.15mm in diameter, used for high-density interconnect (HDI) PCBs |
The Via in Pad Plating Process
The via in pad plating process involves several steps to create a conductive path through the vias and pads on the surface layer of a PCB.
Step 1: Drilling
The first step in the via in pad plating process is to drill the vias into the PCB. This is typically done using a CNC drilling machine, which can accurately drill small holes at high speeds.
Step 2: Desmear
After drilling, the vias must be cleaned to remove any debris or smear left behind by the drilling process. This is done using a chemical desmear process, which removes the resin and glass fibers from the via walls.
Step 3: Electroless Copper Deposition
Once the vias are cleaned, they are coated with a thin layer of electroless copper. This process involves immersing the PCB in a chemical bath that deposits a thin layer of copper onto the via walls and surface of the board.
Step 4: Electrolytic Copper Plating
After the electroless copper deposition, the PCB undergoes electrolytic copper plating. This process involves applying an electrical current to the board, which causes copper ions to be attracted to the via walls and surface of the board, building up a thicker layer of copper.
Step 5: Resist Application and Patterning
Once the vias and pads are plated with copper, a photoresist is applied to the surface of the board. The photoresist is then patterned using a photolithography process, which exposes the areas of the board that will be plated with additional copper.
Step 6: Copper Pattern Plating
The exposed areas of the board are then plated with additional copper, building up the thickness of the copper in the vias and pads. This process is typically done using an electrolytic plating process.
Step 7: Resist Stripping and Etching
After the copper pattern plating is complete, the photoresist is stripped away, leaving the plated copper on the surface of the board. The excess copper is then etched away, leaving only the desired copper pattern on the board.
Benefits of Via in Pad Plating
Via in pad plating offers several benefits for PCB designers and manufacturers:
-
Improved Signal Integrity: By plating the vias and pads on the surface layer of the PCB, via in pad plating helps to improve signal integrity by reducing impedance mismatches and reflections.
-
Increased Reliability: Via in pad plating helps to increase the reliability of the PCB by providing a robust electrical connection between layers. This is particularly important for high-density PCBs with small vias and pads.
-
Reduced Manufacturing Costs: Via in pad plating can help to reduce manufacturing costs by eliminating the need for additional processes, such as Via Filling or capping.
-
Improved Thermal Management: By providing a direct thermal path from the surface of the PCB to the inner layers, via in pad plating can help to improve thermal management in high-power applications.
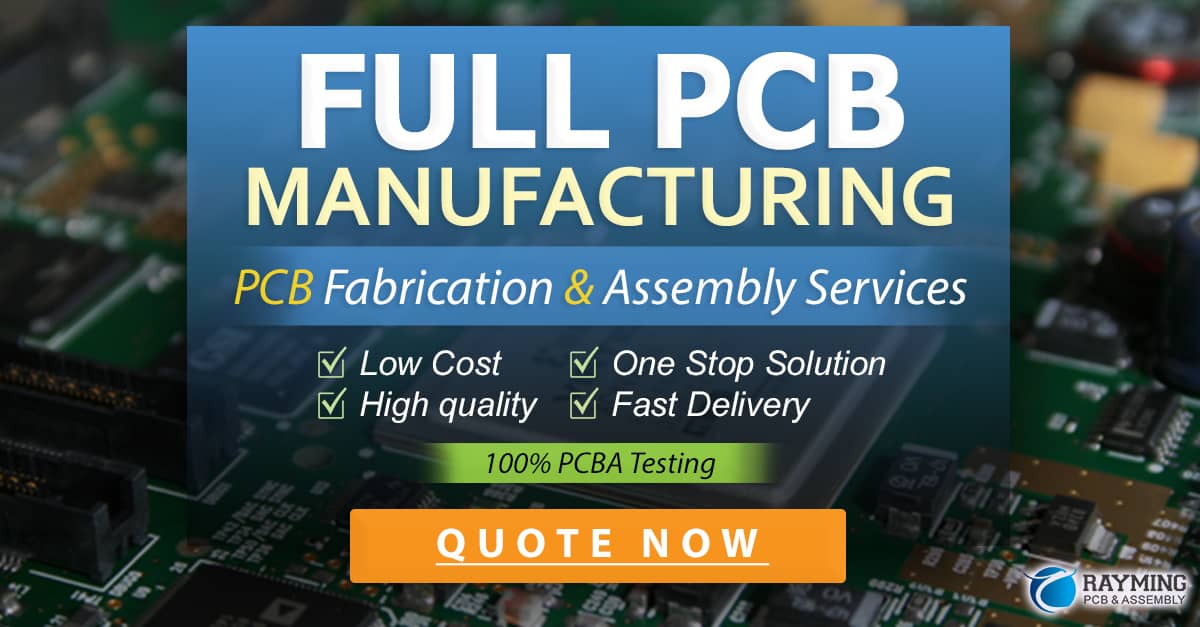
Challenges of Via in Pad Plating
While via in pad plating offers many benefits, there are also some challenges associated with this process:
-
Design Complexity: Via in pad plating requires careful design consideration to ensure that the vias and pads are properly sized and spaced. This can increase the complexity of the PCB design process.
-
Manufacturing Challenges: Via in pad plating can be challenging from a manufacturing perspective, as it requires tight control over the plating process to ensure consistent results.
-
Cost: While via in pad plating can help to reduce overall manufacturing costs, the process itself can be more expensive than traditional via filling or capping methods.
Applications of Via in Pad Plating
Via in pad plating is commonly used in a variety of PCB Applications, including:
-
High-Density Interconnect (HDI) PCBs: Via in pad plating is often used in HDI PCBs, where the high density of components requires small vias and pads.
-
RF and Microwave PCBs: Via in pad plating is often used in RF and microwave PCBs to improve signal integrity and reduce losses.
-
Automotive and Aerospace PCBs: Via in pad plating is often used in automotive and aerospace PCBs, where reliability and robustness are critical.
-
Medical Device PCBs: Via in pad plating is often used in medical device PCBs, where high reliability and small form factors are required.
Frequently Asked Questions (FAQ)
- What is the difference between via in pad plating and traditional via filling?
Via in pad plating involves plating the vias and pads on the surface layer of the PCB, while traditional via filling involves filling the vias with a conductive material, such as copper or conductive epoxy. Via in pad plating provides a more robust electrical connection and can help to improve signal integrity, while via filling is often used for thermal management or to provide structural support.
- Can via in pad plating be used with any type of via?
Via in pad plating can be used with most types of vias, including Through-hole vias, blind vias, and buried vias. However, the specific requirements for via size and spacing may vary depending on the application and manufacturing process.
- How does via in pad plating affect the impedance of a PCB?
Via in pad plating can help to reduce impedance mismatches and reflections in a PCB by providing a consistent electrical path through the vias and pads. This can help to improve signal integrity and reduce losses, particularly in high-speed or high-frequency applications.
- What materials are used for via in pad plating?
Via in pad plating typically uses copper as the conductive material, as it provides good electrical conductivity and can be easily plated onto the surface of the PCB. Other materials, such as gold or silver, may be used in specific applications where higher conductivity or corrosion resistance is required.
- How does via in pad plating affect the manufacturing cost of a PCB?
While via in pad plating can help to reduce overall manufacturing costs by eliminating the need for additional processes, such as via filling or capping, the process itself can be more expensive than traditional methods. The specific cost impact will depend on factors such as the size and complexity of the PCB, the number of layers, and the manufacturing volume.
Conclusion
Via in pad plating is a critical process in PCB manufacturing that provides a robust electrical connection between the layers of a multi-layer PCB. By plating the vias and pads on the surface layer of the board, via in pad plating helps to improve signal integrity, increase reliability, and reduce manufacturing costs.
While via in pad plating offers many benefits, it also presents some challenges in terms of design complexity and manufacturing control. However, for many applications, particularly those requiring high density, high reliability, or improved signal integrity, via in pad plating is an essential tool in the PCB designer’s toolkit.
As PCB technology continues to evolve, via in pad plating will likely play an increasingly important role in enabling the next generation of electronic devices and systems. By understanding the fundamentals of this process and its applications, PCB designers and manufacturers can leverage via in pad plating to create more advanced, reliable, and cost-effective PCBs for a wide range of industries and applications.
0 Comments