Introduction to Via covering
Via covering is an essential technique used in the manufacturing of printed circuit boards (PCBs) to ensure the reliability and functionality of the board. In PCB design, vias are small holes drilled through the board to connect different layers of copper tracks. These vias are then filled with conductive material, typically copper, to establish electrical connectivity between the layers.
However, vias can also pose challenges in PCB manufacturing, especially when it comes to the application of solder mask and the assembly of components. This is where via covering comes into play. Via covering involves applying a layer of material over the via to protect it from solder and other contaminants during the assembly process.
Types of Via Covering
There are several methods used for via covering in PCB manufacturing, each with its own advantages and disadvantages. The most common types of via covering include:
-
Solder Mask Via Covering: This method involves applying a layer of solder mask over the via. Solder mask is a thin, protective layer that is applied to the surface of the PCB to prevent solder from adhering to unwanted areas. When used for via covering, solder mask helps to prevent solder from flowing into the via during the assembly process.
-
Epoxy Via Covering: Epoxy via covering involves filling the via with a non-conductive epoxy material. This method provides a strong, durable covering that can withstand the high temperatures and pressures involved in PCB Assembly.
-
Conductive Via Covering: Conductive via covering involves filling the via with a conductive material, such as copper or silver. This method is often used in high-frequency applications where signal integrity is critical.
Advantages of Via Covering
Via covering offers several advantages in PCB manufacturing, including:
-
Improved Reliability: By protecting vias from solder and other contaminants, via covering helps to improve the overall reliability of the PCB. This is particularly important in applications where the PCB will be subjected to harsh environmental conditions or high levels of stress.
-
Enhanced Signal Integrity: Via covering can also help to improve signal integrity in high-frequency applications. By filling vias with conductive material, via covering reduces the impedance mismatch between the via and the surrounding copper tracks, which can lead to signal reflections and other issues.
-
Simplified Assembly: Via covering can also simplify the PCB assembly process by preventing solder from flowing into the via. This can help to reduce the risk of short circuits and other defects that can occur when solder flows into unwanted areas.
Via Covering Techniques
There are several techniques used for via covering in PCB manufacturing, each with its own advantages and disadvantages. The choice of technique will depend on factors such as the size and shape of the via, the material used for the covering, and the specific requirements of the application.
Solder Mask Via Covering
Solder mask via covering is one of the most common techniques used in PCB manufacturing. This method involves applying a layer of solder mask over the via to prevent solder from flowing into the hole during the assembly process.
The solder mask is typically applied using a screen printing process, where a stencil is used to apply the solder mask to the surface of the PCB. The stencil is designed to match the pattern of the vias on the board, allowing the solder mask to be applied only where it is needed.
Once the solder mask has been applied, it is cured using heat and UV light to create a hard, durable covering over the via. The cured solder mask is then inspected to ensure that it has been applied correctly and that there are no defects or voids in the covering.
Advantages of solder mask via covering include:
- Low cost compared to other via covering methods
- Easy to apply using standard PCB manufacturing processes
- Provides good protection against solder and other contaminants
Disadvantages of solder mask via covering include:
- May not provide sufficient protection for high-reliability applications
- Can be difficult to apply to small or oddly-shaped vias
- May not provide adequate insulation for high-voltage applications
Epoxy Via Covering
Epoxy via covering involves filling the via with a non-conductive epoxy material to create a strong, durable covering. This method is often used in high-reliability applications where the PCB will be subjected to harsh environmental conditions or high levels of stress.
The epoxy material is typically applied using a dispensing machine, which injects the epoxy into the via using a needle or nozzle. The epoxy is then cured using heat to create a solid, non-conductive covering over the via.
Advantages of epoxy via covering include:
- Provides excellent protection against solder and other contaminants
- Creates a strong, durable covering that can withstand harsh environmental conditions
- Provides good insulation for high-voltage applications
Disadvantages of epoxy via covering include:
- Higher cost compared to solder mask via covering
- Requires specialized equipment and processes for application
- May not be suitable for high-frequency applications due to the non-conductive nature of the epoxy material
Conductive Via Covering
Conductive via covering involves filling the via with a conductive material, such as copper or silver, to create a solid, conductive connection between the layers of the PCB. This method is often used in high-frequency applications where signal integrity is critical.
The conductive material is typically applied using a plating process, where the via is first cleaned and then plated with a thin layer of copper or other conductive material. The plated via is then filled with a conductive paste or ink to create a solid, conductive connection between the layers of the PCB.
Advantages of conductive via covering include:
- Provides excellent signal integrity for high-frequency applications
- Creates a solid, reliable connection between the layers of the PCB
- Can be used to create controlled impedance structures within the PCB
Disadvantages of conductive via covering include:
- Higher cost compared to other via covering methods
- Requires specialized equipment and processes for application
- May not be suitable for all applications due to the conductive nature of the material
Design Considerations for Via Covering
When designing a PCB that will use via covering, there are several important considerations to keep in mind to ensure the best possible results.
Via Size and Shape
The size and shape of the vias on the PCB can have a significant impact on the effectiveness of the via covering process. In general, smaller vias are more difficult to cover than larger vias, as there is less surface area for the covering material to adhere to.
Similarly, vias with irregular shapes or sizes can be more challenging to cover than vias with uniform shapes and sizes. When designing the PCB, it is important to consider the size and shape of the vias and to select a via covering method that is appropriate for the specific requirements of the application.
Material Selection
The choice of material used for via covering can also have a significant impact on the performance and reliability of the PCB. Different materials have different properties and characteristics that can affect the ability of the covering to protect against solder and other contaminants, as well as its ability to withstand harsh environmental conditions.
For example, solder mask is a relatively low-cost material that provides good protection against solder and other contaminants, but may not be suitable for high-reliability applications or harsh environmental conditions. Epoxy, on the other hand, provides excellent protection and durability, but is more expensive and may not be suitable for high-frequency applications.
When selecting a material for via covering, it is important to consider factors such as the specific requirements of the application, the environmental conditions that the PCB will be subjected to, and the cost and availability of the material.
Process Control
The success of the via covering process also depends on careful process control and quality assurance measures. This includes ensuring that the vias are properly cleaned and prepared before the covering material is applied, as well as monitoring the application process to ensure that the covering is applied consistently and uniformly.
It is also important to conduct thorough inspections and testing of the PCB after the via covering process is complete to ensure that the covering has been applied correctly and that there are no defects or voids in the covering.
Design for Manufacturability
Finally, when designing a PCB that will use via covering, it is important to consider the manufacturability of the design. This includes factors such as the placement and spacing of the vias, the size and shape of the PCB, and the overall complexity of the design.
By designing the PCB with manufacturability in mind, it is possible to streamline the via covering process and reduce the risk of defects or issues during manufacturing. This can help to improve the overall quality and reliability of the PCB, as well as reduce the time and cost associated with the manufacturing process.
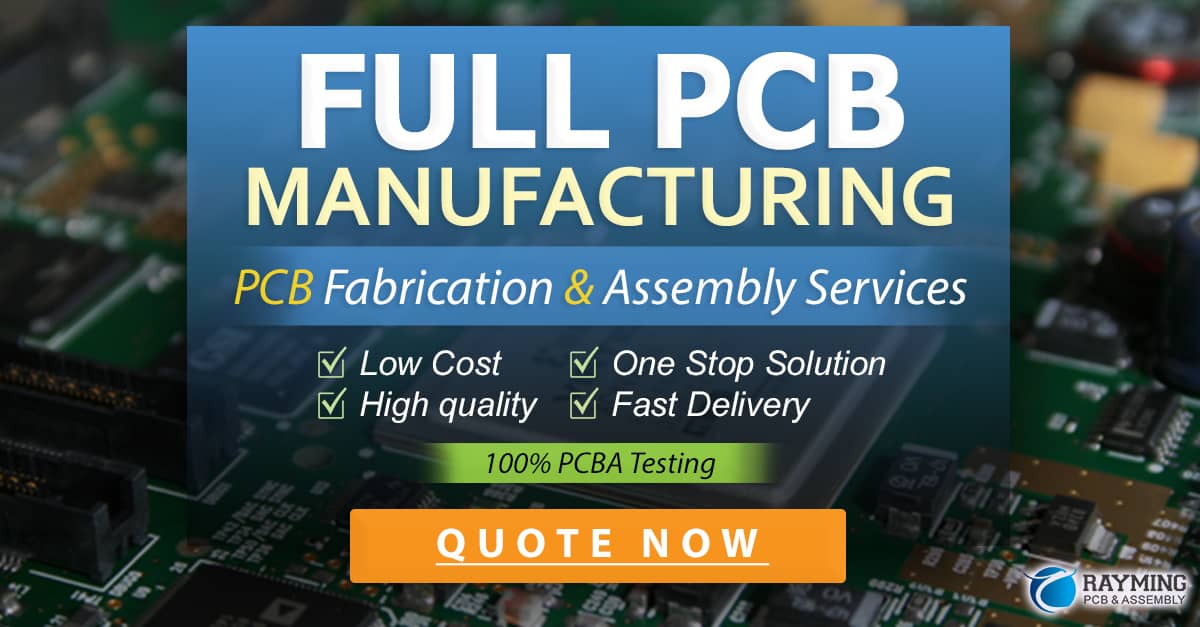
Benefits of Via Covering
Via covering offers several important benefits for PCB manufacturing and performance, including:
Improved Reliability
One of the primary benefits of via covering is improved reliability of the PCB. By protecting the vias from solder and other contaminants, via covering helps to prevent short circuits, open circuits, and other defects that can occur during the assembly process.
In addition, via covering can help to improve the overall durability and longevity of the PCB by protecting the vias from environmental factors such as moisture, dust, and other contaminants that can degrade the performance of the PCB over time.
Enhanced Signal Integrity
Via covering can also help to enhance the signal integrity of the PCB, particularly in high-frequency applications. By filling the vias with conductive material, via covering helps to reduce the impedance mismatch between the via and the surrounding copper traces, which can lead to signal reflections and other issues that can degrade signal quality.
In addition, via covering can help to reduce the overall inductance and capacitance of the vias, which can further improve signal integrity and reduce the risk of signal distortion or loss.
Simplified Assembly
Via covering can also help to simplify the PCB assembly process by reducing the risk of Solder Bridging and other defects that can occur when solder flows into the vias. This can help to reduce the time and cost associated with the assembly process, as well as improve the overall quality and reliability of the finished product.
Reduced Electromagnetic Interference
Finally, via covering can help to reduce electromagnetic interference (EMI) in the PCB by shielding the vias from external electromagnetic fields. This can be particularly important in applications where the PCB is located near other electronic devices or equipment that may generate electromagnetic interference.
By reducing EMI, via covering can help to improve the overall performance and reliability of the PCB, as well as reduce the risk of interference with other electronic devices or equipment.
Conclusion
Via covering is an essential technique used in PCB manufacturing to ensure the reliability, functionality, and performance of the finished product. By protecting the vias from solder and other contaminants, via covering helps to prevent defects and improve the overall quality of the PCB.
There are several different methods and materials used for via covering, each with its own advantages and disadvantages. The choice of method and material will depend on the specific requirements of the application, as well as factors such as cost, availability, and performance.
When designing a PCB that will use via covering, it is important to consider factors such as via size and shape, material selection, process control, and design for manufacturability. By considering these factors and selecting the appropriate via covering method and material, it is possible to achieve the best possible results and ensure the highest level of quality and reliability in the finished product.
Frequently Asked Questions (FAQ)
- What is the purpose of via covering in PCB manufacturing?
Via covering is used to protect the vias from solder and other contaminants during the assembly process, as well as to improve the overall reliability and performance of the PCB.
- What are the most common methods used for via covering?
The most common methods used for via covering include solder mask via covering, epoxy via covering, and conductive via covering. Each method has its own advantages and disadvantages, and the choice of method will depend on the specific requirements of the application.
- What are the benefits of using epoxy for via covering?
Epoxy via covering provides excellent protection against solder and other contaminants, and creates a strong, durable covering that can withstand harsh environmental conditions. Epoxy also provides good insulation for high-voltage applications.
- How does via covering improve signal integrity in high-frequency applications?
Via covering can help to improve signal integrity in high-frequency applications by reducing the impedance mismatch between the via and the surrounding copper traces, as well as reducing the overall inductance and capacitance of the vias. This can help to reduce signal reflections and other issues that can degrade signal quality.
- What factors should be considered when selecting a via covering method and material?
When selecting a via covering method and material, it is important to consider factors such as the specific requirements of the application, the environmental conditions that the PCB will be subjected to, and the cost and availability of the material. Other factors to consider include via size and shape, process control, and design for manufacturability.
0 Comments