What is a Solder Mask Made Of?
Solder masks are typically made of a polymer-based material, such as epoxy or acrylic. These materials are chosen for their excellent electrical insulation properties, durability, and resistance to heat and chemicals. The most common solder mask materials include:
-
Liquid Photoimageable Solder Mask (LPSM): A photosensitive liquid polymer that is applied to the PCB and then exposed to UV light to cure and harden.
-
Dry Film Photoimageable Solder Mask (DFSM): A photosensitive film that is laminated onto the PCB and then exposed to UV light to cure and harden.
-
Liquid Photoimageable Solder Mask (LPI): A liquid solder mask that is screen printed onto the PCB and then cured using UV light.
-
Epoxy Liquid Solder Mask: A two-part epoxy that is mixed and then applied to the PCB using a screen printing process.
The Solder Mask Application Process
The solder mask application process varies depending on the type of solder mask being used. However, the general steps involved in applying a solder mask to a PCB are as follows:
-
PCB Cleaning: The PCB is thoroughly cleaned to remove any dirt, grease, or contaminants that may interfere with the solder mask application.
-
Solder Mask Application: The chosen solder mask material is applied to the PCB using one of the methods mentioned above (screen printing, lamination, or coating).
-
UV Exposure: The PCB with the applied solder mask is exposed to UV light to cure and harden the mask. The exposure time and intensity depend on the specific solder mask material being used.
-
Developing: After UV exposure, the unexposed areas of the solder mask are removed using a developer solution, revealing the copper traces that need to be exposed for soldering.
-
Curing: The PCB is then subjected to a final curing process, which involves heating the board to a specific temperature for a set duration to ensure the solder mask is fully hardened and adhered to the board.
Types of Solder Masks
There are several types of solder masks available, each with its own unique properties and applications. Some of the most common types include:
-
Green Solder Mask: The most widely used color for solder masks, green provides excellent contrast against copper traces and is easy to inspect.
-
Black Solder Mask: Black solder masks are often used for high-end electronics and provide a sleek, professional appearance.
-
White Solder Mask: White solder masks are less common but can be used for specific applications where high reflectivity is required.
-
Matte Solder Mask: Matte solder masks have a non-glossy finish and are preferred for applications where glare reduction is important.
-
Glossy Solder Mask: Glossy solder masks have a shiny finish and are often used for aesthetic purposes.
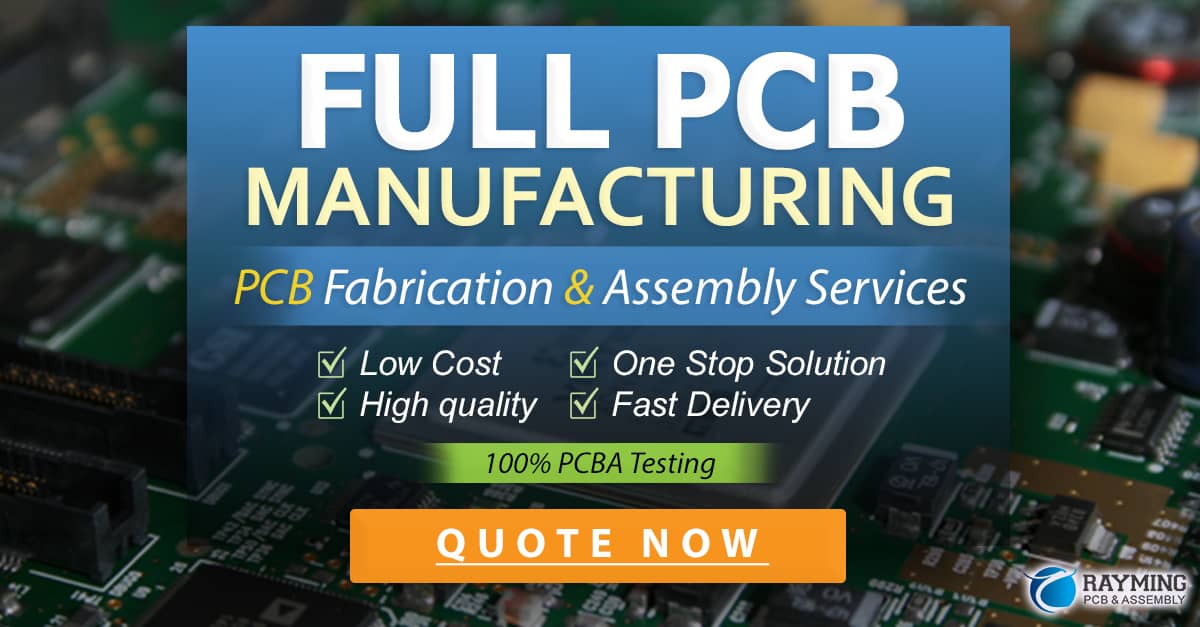
The Importance of Solder Masks in PCB Manufacturing
Solder masks play a crucial role in PCB manufacturing, offering several key benefits:
-
Insulation: Solder masks provide electrical insulation between copper traces, preventing short circuits and ensuring the proper functioning of the PCB.
-
Protection: The solder mask layer protects the copper traces from oxidation, corrosion, and mechanical damage, increasing the PCB’s longevity and reliability.
-
Solder Control: Solder masks help control the flow of molten solder during the soldering process, preventing bridging between adjacent traces and ensuring precise solder joint formation.
-
Aesthetics: Solder masks enhance the visual appearance of the PCB, providing a clean, professional look and allowing for customization with different colors and finishes.
-
Identification: Solder masks can be used to print text, logos, or other identifying information directly onto the PCB, aiding in assembly and troubleshooting processes.
Solder Mask Design Considerations
When designing a PCB, there are several key considerations related to solder masks:
-
Solder Mask Clearance: The solder mask clearance is the distance between the edge of a copper pad and the solder mask opening. Adequate clearance is essential to ensure proper soldering and prevent solder mask from interfering with the solder joint.
-
Solder Mask Expansion: During the curing process, solder masks may expand slightly. Designers must account for this expansion to ensure the final solder mask openings are within the specified tolerances.
-
Solder Mask Thickness: The thickness of the solder mask layer can impact its insulation and protection properties. Typical solder mask thicknesses range from 0.5 to 2 mils (0.0127 to 0.0508 mm).
-
Solder Mask Color: The choice of solder mask color can impact the PCB’s appearance and functionality. Green is the most common color, but other colors may be used for specific applications or to improve contrast for automated optical inspection (AOI) systems.
Solder Mask Defects and Quality Control
Ensuring the quality of the solder mask is critical to the overall performance and reliability of the PCB. Some common solder mask defects include:
-
Pinholes: Small holes in the solder mask that expose the underlying copper, potentially leading to short circuits or corrosion.
-
Solder Mask Residue: Incomplete removal of the solder mask in exposed areas, which can interfere with soldering and lead to poor solder joint formation.
-
Solder Mask Misregistration: Misalignment between the solder mask and the copper traces, which can result in exposed copper or inadequate pad coverage.
-
Solder Mask Blistering: Formation of bubbles or blisters in the solder mask due to improper curing or contamination.
To mitigate these defects, PCB manufacturers employ strict quality control measures, including:
-
Visual Inspection: Manual or automated visual inspection of the PCB to identify any visible solder mask defects.
-
Electrical Testing: Continuity and insulation resistance testing to ensure the solder mask provides adequate insulation between copper traces.
-
Microsectioning: Cross-sectional analysis of the PCB to assess solder mask thickness, adhesion, and coverage.
-
Surface Insulation Resistance (SIR) Testing: Evaluation of the solder mask’s ability to maintain electrical insulation under various environmental conditions, such as high humidity or elevated temperatures.
Environmental Impact and Sustainability
As with any manufacturing process, the production and use of solder masks can have an environmental impact. PCB manufacturers are increasingly focusing on developing more sustainable and eco-friendly solder mask materials and processes:
-
Lead-Free Solder Masks: Traditional solder masks may contain small amounts of lead, a toxic heavy metal. Lead-free solder masks are becoming more prevalent to reduce the environmental impact of PCB manufacturing.
-
Halogen-Free Solder Masks: Some solder mask materials may contain halogens, which can release toxic fumes during incineration. Halogen-free solder masks are being developed to minimize this risk.
-
UV-Curable Solder Masks: UV-curable solder masks require less energy to cure compared to traditional thermal-curing processes, reducing the overall energy consumption in PCB manufacturing.
-
Recycling and Waste Reduction: PCB manufacturers are implementing recycling programs and waste reduction initiatives to minimize the environmental impact of solder mask production and disposal.
Frequently Asked Questions (FAQ)
-
What is the purpose of a solder mask?
A: The primary purpose of a solder mask is to provide electrical insulation between copper traces on a PCB, prevent short circuits, and protect the board from environmental factors such as oxidation and corrosion. -
Can solder masks be applied to both sides of a PCB?
A: Yes, solder masks can be applied to both sides of a PCB. This is common practice for double-sided and multi-layer PCBs. -
What is the typical thickness of a solder mask?
A: The typical thickness of a solder mask ranges from 0.5 to 2 mils (0.0127 to 0.0508 mm), depending on the specific application and PCB design requirements. -
Are solder masks necessary for all PCBs?
A: While solder masks are highly recommended for most PCBs, they may not be necessary for very simple, low-density designs or prototype boards. However, for the vast majority of commercial and industrial PCBs, solder masks are considered essential for ensuring proper functionality, reliability, and longevity. -
Can solder masks be removed after application?
A: Solder masks are designed to be permanent and are difficult to remove once applied and cured. Attempting to remove a solder mask can damage the underlying copper traces and compromise the PCB’s integrity. If solder mask removal is necessary, specialized techniques such as micro-abrasion or laser ablation may be used, but these processes are typically only employed in rare circumstances.
Conclusion
Solder masks are a critical component in the manufacturing of reliable, high-quality printed circuit boards. By providing electrical insulation, environmental protection, and solder control, solder masks ensure the proper functioning and longevity of PCBs across a wide range of applications. As PCB technology continues to advance, the development of new solder mask materials and processes will play a crucial role in meeting the evolving demands of the electronics industry while prioritizing sustainability and environmental responsibility.
0 Comments