Understanding Flex PCB Materials
Polyimide (PI) Substrate
Polyimide (PI) is the most commonly used substrate material for flex PCBs. It offers excellent thermal stability, mechanical strength, and electrical insulation properties. PI substrates are available in various thicknesses, typically ranging from 12.5 μm to 125 μm. The choice of thickness depends on the specific application requirements, such as flexibility, durability, and signal integrity.
Adhesives
Adhesives are used to bond the copper foil to the PI substrate. The two main types of adhesives used in flex PCBs are acrylic and epoxy. Acrylic adhesives provide good flexibility and are suitable for dynamic flexing applications. Epoxy adhesives offer higher temperature resistance and better dimensional stability, making them ideal for static flexing applications.
Copper Foil
Copper foil is the conductive layer in flex PCBs, responsible for carrying electrical signals. The thickness of the copper foil is measured in ounces (oz), with 1 oz representing a thickness of approximately 35 μm. Flex PCBs typically use copper foils ranging from 0.5 oz to 2 oz. Thinner copper foils provide better flexibility but have lower current carrying capacity, while thicker foils offer higher current carrying capacity but reduced flexibility.
Coverlay
Coverlay is an insulating material that is laminated onto the outer layers of a flex PCB to protect the circuitry and provide electrical insulation. It is usually made of polyimide or polyester and comes in various thicknesses. The choice of coverlay thickness depends on the level of protection required and the overall thickness constraints of the flex PCB.
Flex PCB Layer Stackup Design
Single-Layer Flex PCBs
Single-layer flex PCBs consist of a single conductive layer sandwiched between two layers of PI substrate. They are the simplest and most cost-effective type of flex PCB. Single-layer flex PCBs are suitable for low-complexity designs and applications that require minimal interconnections.
Double-Layer Flex PCBs
Double-layer flex PCBs have two conductive layers, separated by a PI substrate layer. The conductive layers are interconnected through plated through-holes (PTHs). Double-layer flex PCBs offer increased routing density and signal routing flexibility compared to single-layer designs. They are commonly used in applications that require more complex circuitry and higher interconnection density.
Multi-Layer Flex PCBs
Multi-layer flex PCBs consist of three or more conductive layers, separated by PI substrate layers. They provide the highest level of routing density and design complexity. Multi-layer flex PCBs are used in advanced applications that demand high-speed signal transmission, dense interconnections, and enhanced functionality. The layer stackup of a multi-layer flex PCB requires careful design considerations to ensure signal integrity, impedance control, and manufacturability.
Rigid-Flex PCBs
Rigid-flex PCBs combine the benefits of both rigid and flexible PCBs. They consist of rigid PCB sections interconnected by flexible PCB sections. Rigid-flex PCBs offer the advantage of integrating multiple interconnected PCBs into a single assembly, reducing the overall size and weight of the device. The layer stackup of a rigid-flex PCB includes both rigid and flexible layers, with the flexible layers typically located in the middle of the stackup.
Flex PCB Stackup Design Considerations
Bend Radius
The bend radius is a critical parameter in flex PCB design. It refers to the minimum radius at which the flex PCB can be bent without causing damage to the copper traces or the substrate. The bend radius is influenced by factors such as the thickness of the copper foil, the thickness of the PI substrate, and the adhesive used. A smaller bend radius allows for tighter packaging and more compact designs, but it also increases the stress on the materials during flexing.
Copper Trace Width and Spacing
The width and spacing of copper traces on a flex PCB must be carefully designed to ensure proper signal integrity and manufacturability. Thinner traces allow for higher routing density but have lower current carrying capacity and are more susceptible to manufacturing defects. Wider traces provide better current carrying capacity and manufacturability but consume more space. The spacing between traces should be sufficient to prevent signal crosstalk and ensure reliable electrical insulation.
Impedance Control
Impedance control is crucial in high-speed flex PCB designs to ensure proper signal transmission and minimize signal reflections. The impedance of a trace is determined by factors such as the trace width, trace thickness, substrate thickness, and dielectric constant of the substrate material. Accurate impedance control requires careful design and simulation to determine the optimal trace geometry and layer stackup.
Via Design
Vias are used to interconnect different layers in a multi-layer flex PCB. The design of vias in flex PCBs requires special considerations due to the flexible nature of the substrate. Microvias, which are small-diameter vias, are commonly used in flex PCBs to minimize the impact on flexibility and reduce the overall thickness of the stackup. Proper via design, including via size, placement, and pad size, is essential for reliable interconnections and manufacturability.
Stiffener Placement
Stiffeners are used in flex PCBs to provide localized rigidity in areas where components are mounted or where the flex PCB needs to maintain a specific shape. Stiffeners are typically made of rigid materials such as FR-4 or polyimide and are laminated onto the flex PCB. The placement of stiffeners should be carefully considered to ensure proper mechanical support without compromising the flexibility of the overall design.
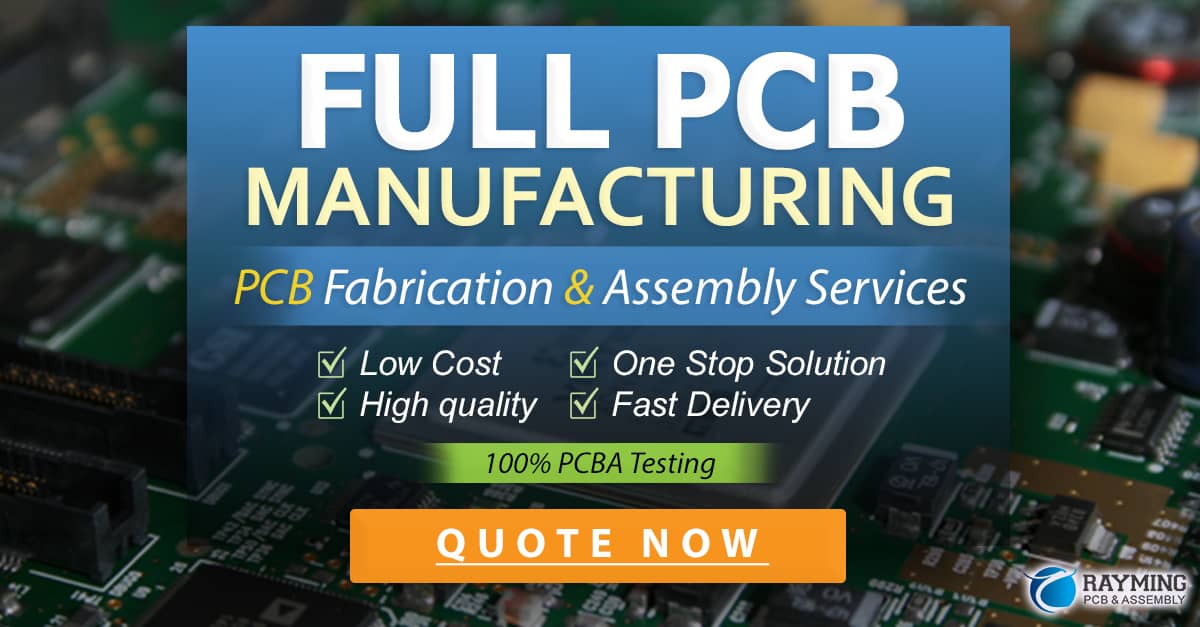
Flex PCB Material and Stackup Selection Guide
Application | Substrate Material | Copper Thickness | Adhesive | Coverlay | Layer Count |
---|---|---|---|---|---|
Dynamic Flexing | Polyimide (12.5 – 50 μm) | 0.5 – 1 oz | Acrylic | Polyimide (25 – 50 μm) | 1 – 2 |
Static Flexing | Polyimide (50 – 125 μm) | 1 – 2 oz | Epoxy | Polyimide (50 – 125 μm) | 2 – 4 |
High-Speed Signals | Polyimide (25 – 50 μm) | 0.5 – 1 oz | Acrylic or Epoxy | Polyimide (25 – 50 μm) | 4 – 8 |
High-Density Interconnect | Polyimide (25 – 50 μm) | 0.5 – 1 oz | Acrylic or Epoxy | Polyimide (25 – 50 μm) | 6 – 12 |
Rigid-Flex | Polyimide (50 – 125 μm) | 0.5 – 2 oz | Epoxy | Polyimide (50 – 125 μm) | 4 – 16 |
Frequently Asked Questions (FAQ)
1. What is the most common substrate material used in flex PCBs?
Polyimide (PI) is the most widely used substrate material for flex PCBs due to its excellent thermal stability, mechanical strength, and electrical insulation properties.
2. What are the advantages of using thinner copper foils in flex PCBs?
Thinner copper foils, such as 0.5 oz or 1 oz, provide better flexibility and allow for tighter bend radii in flex PCB designs. They are suitable for applications that require high flexibility and compact packaging.
3. How does the choice of adhesive affect the performance of a flex PCB?
Acrylic adhesives offer good flexibility and are suitable for dynamic flexing applications, while epoxy adhesives provide higher temperature resistance and better dimensional stability, making them ideal for static flexing applications.
4. What is the purpose of coverlay in flex PCBs?
Coverlay is an insulating material laminated onto the outer layers of a flex PCB to protect the circuitry and provide electrical insulation. It helps prevent damage to the copper traces and ensures reliable operation of the flex PCB.
5. What are the key considerations when designing the layer stackup of a multi-layer flex PCB?
When designing the layer stackup of a multi-layer flex PCB, key considerations include signal integrity, impedance control, bend radius, copper trace width and spacing, via design, and stiffener placement. Careful design and simulation are necessary to optimize the layer stackup for the specific application requirements.
Conclusion
Flex PCB material and layer stackup selection are critical aspects of designing reliable and high-performance flexible circuits. Understanding the properties and characteristics of different substrate materials, adhesives, copper foils, and coverlays is essential for making informed decisions. The layer stackup design should take into account factors such as bend radius, copper trace width and spacing, impedance control, via design, and stiffener placement to ensure optimal performance and manufacturability.
By carefully considering the application requirements and selecting the appropriate materials and layer stackup, designers can create flex PCBs that meet the demanding needs of various industries, including consumer electronics, automotive, medical devices, and aerospace. With the increasing demand for compact, lightweight, and flexible electronic devices, the importance of flex PCB material and layer stackup will only continue to grow in the future.
0 Comments