Introduction to PCB Silkscreen
The silkscreen, also known as the legend or nomenclature, is a crucial component of a printed circuit board (PCB). It is a layer of text, symbols, and logos printed on the surface of the PCB that provides essential information for assembly, testing, and maintenance. The silkscreen is typically white in color and is applied using a screen-printing process.
The Importance of PCB Silkscreen
PCB silkscreen serves several important functions:
-
Component identification: The silkscreen labels components with their reference designators (e.g., R1, C2, U3), making it easier for technicians to locate and replace them during assembly or repair.
-
Orientation indicators: Silkscreen markings often include orientation indicators, such as pin 1 markers or polarity symbols, to ensure correct component placement.
-
Branding and aesthetics: Company logos, product names, and other branding elements can be incorporated into the silkscreen to enhance the visual appeal of the PCB.
-
Regulatory compliance: Silkscreen markings may include certification logos, safety warnings, or other information required by regulatory standards.
The Silkscreen Printing Process
Screen Preparation
The silkscreen printing process begins with the creation of a stencil, also known as a screen. The screen is made by stretching a fine mesh fabric over a frame and coating it with a light-sensitive emulsion. The desired silkscreen design is then exposed onto the emulsion using UV light, hardening the exposed areas while leaving the unexposed areas soluble.
Printing
Once the screen is prepared, it is placed over the PCB, and ink is applied to the screen using a squeegee. The ink passes through the open areas of the screen, transferring the silkscreen design onto the surface of the PCB. The ink is then cured using heat or UV light to ensure its durability.
Ink Types
There are several types of ink used for PCB silkscreen printing:
-
Epoxy-based ink: Known for its excellent durability and resistance to chemicals and abrasion.
-
UV-curable ink: Offers fast curing times and high precision, making it suitable for fine-pitch designs.
-
Solvent-based ink: Provides good adhesion and flexibility but may require longer drying times.
The choice of ink depends on factors such as the PCB material, environmental conditions, and design requirements.
Silkscreen Design Considerations
Placement
When designing the silkscreen, it is essential to consider the placement of text and symbols in relation to other PCB elements. Some guidelines include:
-
Avoid placing silkscreen markings over pads, vias, or traces to prevent interference with soldering or electrical connections.
-
Maintain adequate clearance between silkscreen elements and component footprints to ensure legibility and avoid confusion.
-
Consider the orientation of text and symbols for optimal readability when the PCB is mounted in its final assembly.
Font and Size
The choice of font and size for silkscreen text is crucial for legibility. Some best practices include:
-
Use a simple, sans-serif font to ensure clarity at small sizes.
-
Maintain a minimum font size of 0.8mm (0.032″) for standard designs, or 0.5mm (0.020″) for high-density layouts.
-
Adjust the font size and style based on the viewing distance and lighting conditions in the intended application.
Color and Contrast
While white is the most common color for PCB silkscreen, other colors such as yellow or black may be used for specific applications or to enhance contrast. When choosing a silkscreen color, consider:
-
The color of the PCB substrate and solder mask to ensure adequate contrast.
-
The lighting conditions in the assembly and maintenance environment.
-
Any color-coding requirements for component identification or branding purposes.
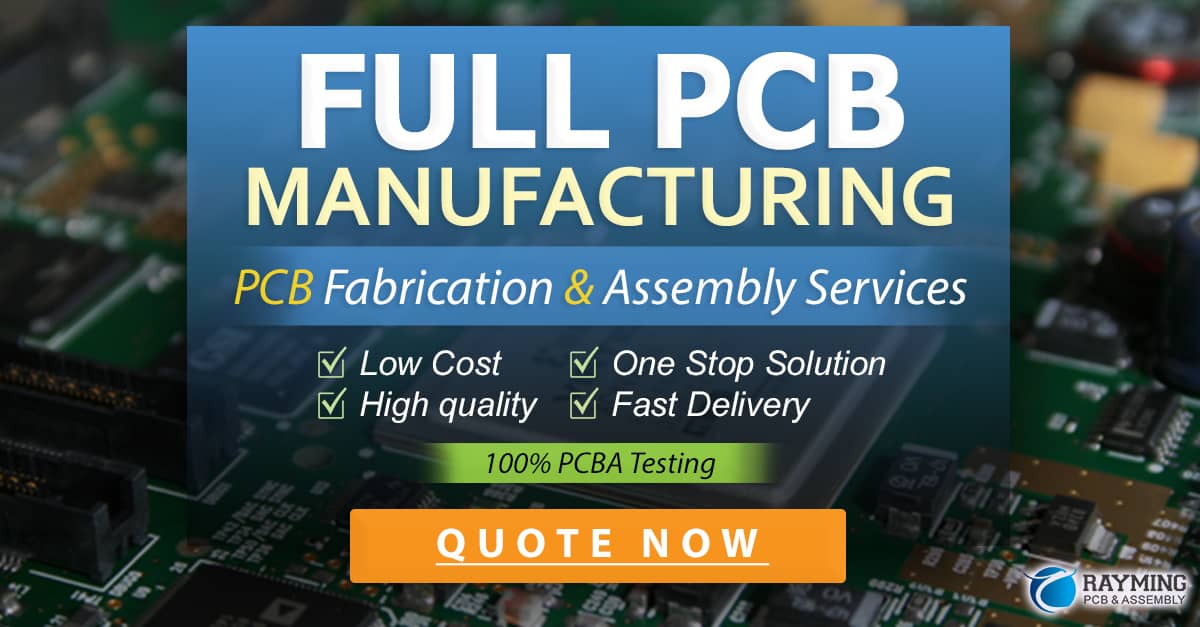
Silkscreen Quality Control
To ensure the quality and consistency of PCB silkscreen, several factors must be monitored and controlled during the printing process:
Ink Viscosity
The viscosity of the silkscreen ink affects its flow and adhesion properties. Ink that is too thin may result in incomplete coverage or smudging, while ink that is too thick may cause clogging or uneven distribution. Regularly monitoring and adjusting the ink viscosity helps maintain print quality.
Screen Tension
The tension of the screen mesh influences the ink deposit and resolution of the silkscreen print. A screen with too little tension may result in poor edge definition or ink bleeding, while excessive tension can cause mesh damage or inconsistent ink transfer. Proper screen tensioning and regular maintenance are essential for optimal print quality.
Curing Parameters
The curing process, whether using heat or UV light, must be carefully controlled to ensure the durability and adhesion of the silkscreen ink. Insufficient curing may result in ink smudging or flaking, while excessive curing can cause brittleness or discoloration. Following the ink manufacturer’s recommended curing parameters and monitoring the process helps achieve consistent results.
Silkscreen Defects and Troubleshooting
Despite careful design and process control, silkscreen defects can occur. Some common issues include:
Incomplete or Missing Print
Causes:
– Clogged screen mesh
– Low ink viscosity
– Insufficient squeegee pressure
Solutions:
– Clean or replace the screen
– Adjust ink viscosity
– Increase squeegee pressure or angle
Smudging or Bleeding
Causes:
– Excessive ink deposit
– Low screen tension
– Incorrect curing parameters
Solutions:
– Reduce ink viscosity or squeegee pressure
– Increase screen tension
– Adjust curing time or temperature
Poor Adhesion
Causes:
– Contaminated PCB surface
– Incompatible ink or substrate
– Insufficient curing
Solutions:
– Clean the PCB surface before printing
– Select a compatible ink for the substrate material
– Ensure proper curing parameters
Frequently Asked Questions (FAQ)
-
Q: Can silkscreen markings be removed or changed after printing?
A: Removing or changing silkscreen markings after printing is challenging and not recommended. In some cases, careful sanding or scraping may remove the ink, but this can damage the PCB surface. It is best to ensure the silkscreen design is correct before printing. -
Q: Are there any limitations on the complexity of silkscreen designs?
A: While silkscreen printing offers significant design flexibility, there are some limitations to consider. Very fine details or intricate logos may be difficult to reproduce accurately, especially at small sizes. It is essential to work with your PCB manufacturer to determine the feasibility of complex silkscreen designs. -
Q: Can silkscreen markings be used on both sides of the PCB?
A: Yes, silkscreen markings can be applied to both the top and bottom sides of a PCB. However, it is crucial to ensure that the markings on one side do not interfere with components or assembly processes on the other side. -
Q: Are there any environmental concerns associated with PCB silkscreen printing?
A: Some silkscreen inks, particularly solvent-based inks, may contain volatile organic compounds (VOCs) that can be harmful to the environment and human health if not handled properly. It is essential to follow proper safety and disposal guidelines when working with these inks and to consider using eco-friendly alternatives when possible. -
Q: How can I ensure the longevity of silkscreen markings on my PCBs?
A: To ensure the longevity of silkscreen markings, consider the following: - Choose a durable ink that is compatible with your PCB substrate and operating environment.
- Follow the manufacturer’s recommended curing parameters to ensure proper ink adhesion.
- Avoid exposing the PCB to excessive abrasion, chemicals, or extreme temperatures that can degrade the silkscreen over time.
- Consider applying a clear conformal coating over the silkscreen to provide additional protection against wear and environmental factors.
Conclusion
The silkscreen is a vital component of PCB design, providing essential information for assembly, testing, and maintenance. By understanding the silkscreen printing process, design considerations, and quality control factors, PCB designers and manufacturers can ensure the clarity, durability, and aesthetics of their silkscreen markings. While challenges may arise, proper planning and attention to detail can help overcome common silkscreen defects and achieve high-quality results.
As PCB technology continues to evolve, the role of silkscreen will remain crucial in facilitating effective communication between designers, manufacturers, and end-users. By staying informed about best practices and emerging trends in silkscreen printing, the electronics industry can continue to produce PCBs that are both functional and visually appealing.
0 Comments