Understanding PCB shelf life and Its Importance
Printed Circuit Boards (PCBs) are essential components in modern electronic devices. They provide a platform for electrical components to be mounted and interconnected, enabling the functioning of various electronic systems. One crucial aspect of PCB manufacturing and assembly is the shelf life of the boards, particularly for double-sided PCBs that undergo multiple reflow processes.
What is PCB Shelf Life?
PCB shelf life refers to the period during which a printed circuit board remains functional and reliable after its manufacture. It is the duration within which the PCB can be stored before being used in the assembly process without compromising its quality or performance.
Several factors influence the shelf life of a PCB, including:
– Storage conditions (temperature, humidity, etc.)
– Quality of materials used
– Surface finish
– Packaging
Why is PCB Shelf Life Important?
Ensuring an adequate PCB shelf life is crucial for several reasons:
-
Quality Assurance: PCBs that exceed their shelf life may suffer from degradation of materials, oxidation of surfaces, or other issues that can affect their functionality and reliability.
-
Cost Efficiency: Proper management of PCB shelf life helps minimize waste and reduces the need for rework or replacement of expired boards.
-
Production Planning: Understanding the shelf life of PCBs allows manufacturers to plan their inventory and production schedules effectively, ensuring that boards are used within their optimal timeframe.
Factors Affecting PCB Shelf Life
Several factors can impact the shelf life of a PCB. Understanding these factors is essential for maintaining the quality and reliability of the boards.
Storage Conditions
One of the most significant factors affecting PCB shelf life is the storage environment. PCBs should be stored in a controlled environment with the following conditions:
-
Temperature: The ideal storage temperature for PCBs is between 10°C and 30°C (50°F to 86°F). Extreme temperatures can cause thermal stress, leading to warping or delamination of the board.
-
Humidity: PCBs should be stored in an environment with relative humidity between 30% and 70%. High humidity can lead to moisture absorption, which can cause oxidation and degradation of the PCB materials.
-
Ventilation: Proper ventilation is necessary to prevent the buildup of corrosive gases or contaminants that can damage the PCB surfaces.
Surface Finish
The type of surface finish applied to the PCB can also affect its shelf life. Some common surface finishes and their impact on shelf life include:
Surface Finish | Shelf Life | Characteristics |
---|---|---|
Hot Air Solder Leveling (HASL) | 12-18 months | Good solderability, prone to oxidation |
Electroless Nickel Immersion Gold (ENIG) | 12-24 months | Excellent solderability, flat surface, longer shelf life |
Immersion Silver | 6-12 months | Good solderability, prone to tarnishing |
Immersion Tin | 6-12 months | Good solderability, prone to whisker growth |
Packaging
Proper packaging of PCBs is crucial for maintaining their shelf life. PCBs should be packaged in moisture-barrier bags (MBBs) with desiccants and humidity indicator cards (HICs) to protect them from moisture and contaminants.
Vacuum sealing or nitrogen flushing can provide additional protection against oxidation and moisture-related issues.
Shelf Life of Double-Sided PCBs After First Reflow
Double-sided PCBs undergo two reflow processes during assembly, one for each side of the board. The first reflow process can impact the shelf life of the PCB before the second reflow is performed.
Factors Affecting Shelf Life After First Reflow
-
Moisture Absorption: During the first reflow process, the PCB is exposed to high temperatures, which can cause moisture trapped within the board to expand and create internal stresses. If the PCB is not adequately dried before the second reflow, this moisture can lead to delamination or other defects.
-
Oxidation: The high temperatures of the reflow process can accelerate the oxidation of the PCB surfaces, particularly if the board is not properly cooled and stored after the first reflow.
-
Handling and Storage: Proper handling and storage of the PCB between the first and second reflow processes are essential to maintain its shelf life. Exposure to contaminants, moisture, or extreme temperatures during this period can degrade the board’s quality.
Maximizing Shelf Life After First Reflow
To maximize the shelf life of a double-sided PCB after the first reflow process, follow these guidelines:
-
Dry the PCB: After the first reflow, ensure that the PCB is adequately dried to remove any moisture absorbed during the process. This can be done using a baking process or a moisture-removal system.
-
Cool and Store Properly: Allow the PCB to cool down gradually after the first reflow to minimize thermal stress. Store the board in a controlled environment with proper temperature, humidity, and ventilation control.
-
Use Appropriate Packaging: Package the PCB in moisture-barrier bags with desiccants and humidity indicator cards to protect it from moisture and contaminants during storage.
-
Minimize Time Between Reflows: To reduce the risk of moisture absorption and oxidation, minimize the time between the first and second reflow processes. Plan the assembly process efficiently to ensure that the PCB is not stored for an extended period between reflows.
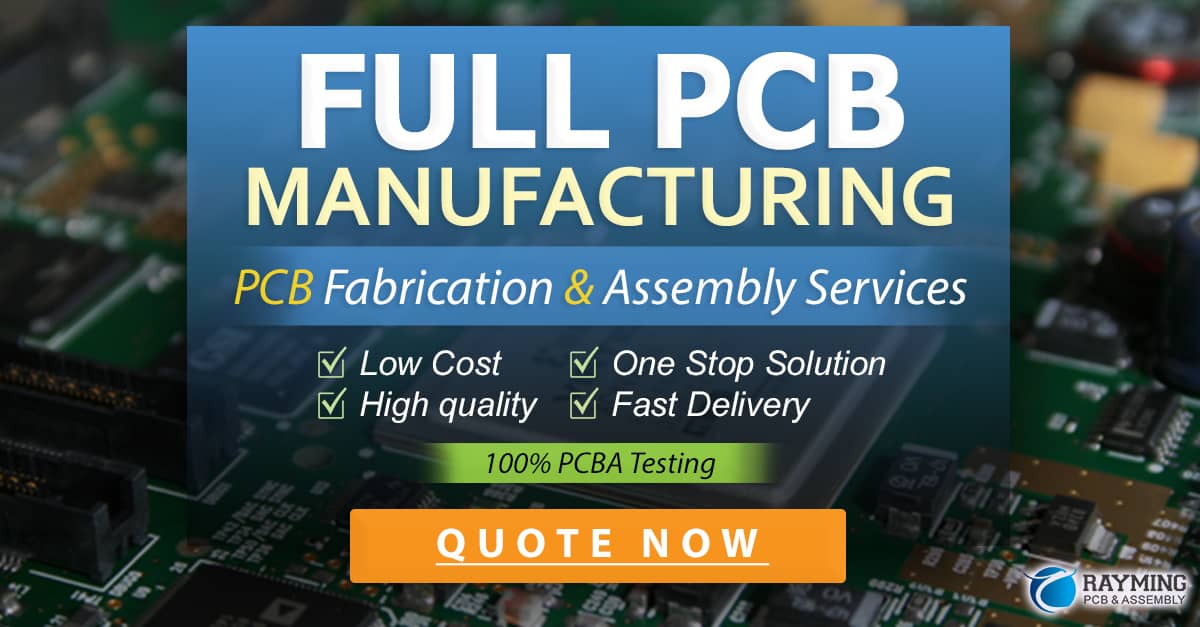
Maximum Shelf Life for Double-Sided PCBs After First Reflow
The maximum shelf life of a double-sided PCB after the first reflow process depends on various factors, such as the surface finish, storage conditions, and handling procedures. However, as a general guideline, the following shelf life durations can be considered:
Surface Finish | Maximum Shelf Life After First Reflow |
---|---|
HASL | 6-12 months |
ENIG | 6-12 months |
Immersion Silver | 3-6 months |
Immersion Tin | 3-6 months |
It is essential to note that these are approximate durations and can vary depending on the specific manufacturing process, materials used, and storage conditions. Proper handling, storage, and moisture control can help extend the shelf life of the PCB.
Frequently Asked Questions (FAQ)
-
Q: What happens if a PCB exceeds its shelf life?
A: If a PCB exceeds its shelf life, it may suffer from material degradation, oxidation, or moisture-related issues that can affect its functionality and reliability. This can lead to defects, poor solderability, or even failure of the board during the assembly process or in the final application. -
Q: Can the shelf life of a PCB be extended?
A: Yes, the shelf life of a PCB can be extended by proper handling, storage, and moisture control. Storing the boards in a controlled environment with appropriate temperature, humidity, and ventilation can help maximize their shelf life. Additionally, using moisture-barrier packaging with desiccants and humidity indicator cards can provide further protection. -
Q: How can I tell if a PCB has exceeded its shelf life?
A: Visual inspection of the PCB can provide some indication of its condition. Signs of oxidation, tarnishing, or discoloration on the surface may suggest that the board has exceeded its shelf life. Additionally, checking the humidity indicator card in the packaging can help determine if the PCB has been exposed to excessive moisture. -
Q: Can PCBs with expired shelf life be reworked?
A: In some cases, PCBs with expired shelf life can be reworked by removing the oxidation or contamination from the surface and applying a new surface finish. However, this process can be time-consuming and costly, and the resulting quality and reliability of the board may not be guaranteed. It is generally recommended to use PCBs within their specified shelf life to ensure optimal performance. -
Q: How can I optimize my inventory management to minimize PCB expiration?
A: To minimize PCB expiration, implement a first-in, first-out (FIFO) inventory management system, ensuring that older boards are used before newer ones. Monitor the shelf life of your PCBs closely and plan your production schedule accordingly. Regularly review your inventory levels and adjust your ordering practices to avoid excess stock that may expire before use.
Conclusion
Understanding and managing the shelf life of PCBs is crucial for ensuring the quality, reliability, and cost-efficiency of electronic assemblies. Double-sided PCBs that undergo multiple reflow processes require special attention to maintain their shelf life after the first reflow.
By implementing proper storage conditions, handling procedures, and moisture control measures, manufacturers can maximize the shelf life of their PCBs and minimize the risk of defects or failures. Regularly monitoring the condition of PCBs, using appropriate packaging, and planning production schedules efficiently can help optimize inventory management and reduce waste.
As a general guideline, the maximum shelf life for double-sided PCBs after the first reflow process ranges from 3 to 12 months, depending on the surface finish and other factors. However, it is essential to consult with your PCB manufacturer and follow their specific recommendations for shelf life and storage requirements.
By understanding and effectively managing PCB shelf life, manufacturers can ensure the quality and reliability of their electronic products while optimizing their production processes and minimizing costs.
0 Comments