Rogers Corporation pioneered some of the earliest commercial laminate materials used as insulating dielectric substrates for manufacturing printed circuit boards (PCB). Their branded materials offer enhanced electrical and thermal performance meeting demanding microwave applications. FR4 constitutes the baseline cost-effective epoxy-glass laminate grade heavily utilized across majority of electronics over many decades.
We explore key differences between Rogers laminates against standard FR4 in composition, electrical characteristics, processing factors, cost considerations and typical applications benefiting from each material’s strengths. Understanding tradeoffs guides appropriate selection fitting electrical and budget needs.
Dielectric Property Differences
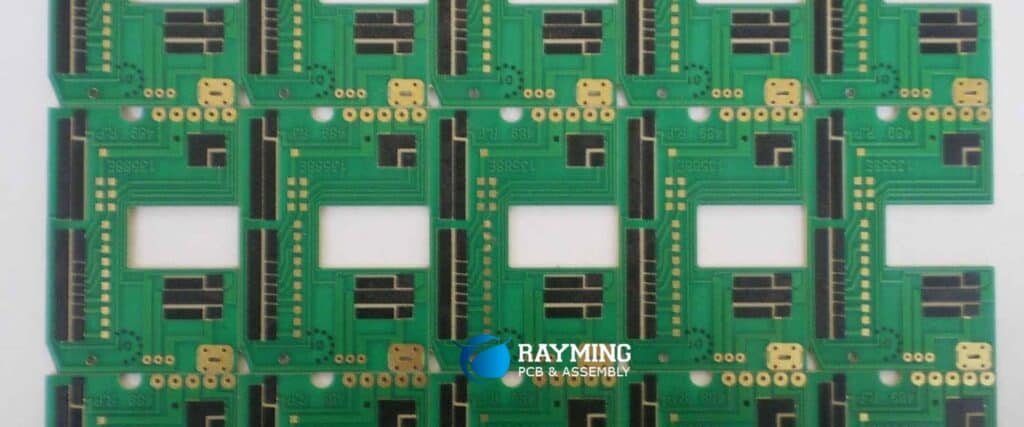
Several key electrical and physical dielectric properties differentiate Rogers laminates from common FR4 materials:
Dielectric Constant
Rogers maintain tight dielectric constant consistency around 3.0 over frequency while FR4 varies 4.2 to 4.8 up through GHz range – Rogers provides closer impedance tolerance.
Loss Tangent
With loss tangents below 0.0025, Rogers ensures signals transmit much further before absorption especially in thicker multilayers compared to FR4 nearing 0.02 inducing higher losses.
Water Absorption
Hydrophilic FR4 soaks measurable moisture degrading electrical performance unlike hydrophobic Rogers effectively impervious to water protecting high frequency behavior.
Thermal Conductivity
High thermal conductivity coefficients above 0.5 W/m-K transfers heat efficiently from Rogers keeping components cooler and more stable than poorer thermal dissipation through standard FR4 at lower 0.3 W/m-K.
Coefficient of Thermal Expansion (CTE)
With z-axis CTE around 60ppm/C, Rogers better matches copper minimizing registration issues through temperature excursions versus higher expansion of FR4 exacerbating alignment stresses over plated through holes and vias.
Precision controlling electrical and physical attributes allows Rogers laminates fitting applications requiring stability and tight parameter distributions where high volume FR4 lacks consistency between lots.
Composition Differences
Delving into the materials constituting Rogers laminates versus FR4 reveals some recipe contrasts driving performance distinctions:
Resin Systems
Rogers often utilizes PTFE-based fluoropolymer resin formulations rather than FR4’s brominated epoxy for the matrix encasing woven glass fabric. This accounts for tighter process controls.
Fiberglass Fabric Weaves
Rogers employs fine microfiber and non-woven glass styles for uniform dielectric spacing unlike conventional coarse weaves prone to gaps occurring with FR4 that undermine local property consistency.
Filler Inclusions
Proprietary ceramic filler particles raising thermal conductivity and dielectric constants precisely blend into Rogers resins rather than FR4 just adding silica fillers mainly just to reduce material costs.
Reinforcements
Materials like polyimide films or bonded metal inserts provide layered reinforcements preventing Z-axis fracturing through Rogers constructions prone to shattering under machining stresses absent from FR4.
Copper Foil Adhesion Treatments
Rogers utilizes lightweight adhesives and alternative oxide-replacement treatments promoting peel strength yet minimizing thickness added to foil unlike FR4 anchoring heavier glass/epoxy coatings that thicken overall.
These formula and composition factors underlying Roger’s laminates assist manufacturing boards with tightly bounded electrical tolerances compared to ordinary FR4 material more prone to batch-to-batch and within panel variations that disturb precision circuit performance.
Fabrication Process Differences
During PCB manufacturing processes, Rogers materials outperform FR4 on factors like:
Drilling – Fibrous Rogers cores avoid fracturing around holes better under bit thrust pressures allowing faster feed rates and superior hole walls compared to fraying with more brittle FR4.
Plating – Smooth drill surfaces promote rapid copper throwing power within holes helping accelerate plating speeds versus slower deposition dealing with glass fiber pull outs downhole walls of FR4.
Lamination – Rogers often bonds up better than FR4 reducing tendencies for inter-material separation or blistering coming off hot presses.
Automated Imaging – Tighter material property consistency allows more accurate imaging film exposures targeting tighter impedances across Rogers laminates versus materials-driven variability interfering with precise imaging of FR4.
Route Profiles – Microwave designs use tightly coupled lines or critical stubs needing Rogers while looser digital traces suit FR4 cost-effectively. Panelization allocates materials appropriately.
Leveraging fabrication process advantages allows reliably achieving more stringent PCB tolerances.
Typical Application Differences
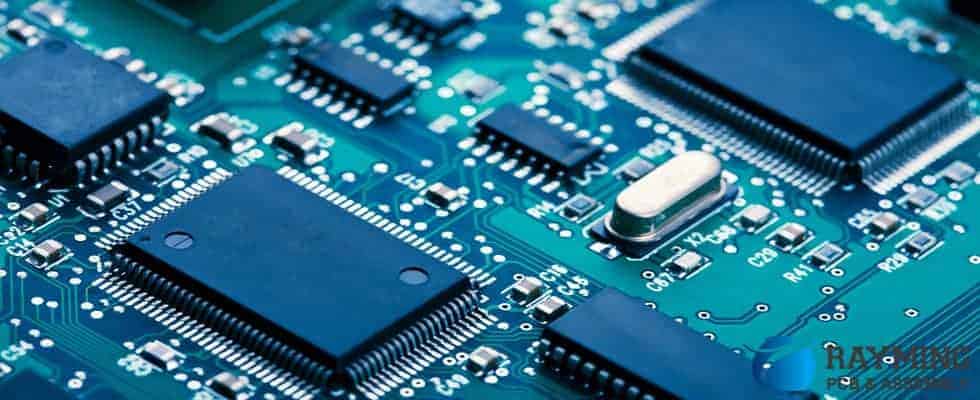
Roger’s superior electrical consistency and fabricated precision focuses usage towards:
High Frequency Applications
Controlled electrical properties maintain signal integrity at microwave frequencies for radar, telecom, aviation, medical and test equipment applications. FR4 fails above few GHz.
High Density Interconnects
Thinner dielectric layers fitting complex aerospace packaged ICs route many signals cleanly without crosstalk that otherwise creeps in with FR4. Signal speed also increases.
Impedance Control Boards
Tighter impedance distributions across Rogers facilitate proper terminations critical for memory interfaces. FR4 variances require cut-back compensation patterns.
Multilayer Coupler/Filters
Selective sandwiched planes etched precisely in Rogers afford high-rejection RF filter elements unattainable with inconsistent Dk inherent to FR4 between layers.
Hybrid Circuits
Combining thin film and wire bonded semiconductors demands Rogers reliability securing components operational over full military temperature ranges beyond what standard FR4 supports.
Conversely, FR4 suits cost-sensitive digital applications like consumer electronics or IoT devices not needing precision electrical parameters. High volume manufacturing offsets consistency limitations statistically.
Cost/Availability Differences
Rogers laminates’ specialized material composition carries inherent cost and lead time impacts:
Cost Factor
Sheet prices run from 5X to over 10X times standard FR4 rates resulting from low volume batches and proprietary ingredients. Howevertiny etched Rogers portions of boards localize expense.
Lead Times
Smaller special orders combined with customized reinforcement inserts tenure Roger’s laminate procurement around 8-12 weeks typically instead of 2-4 weeks for common FR4 grades shipping directly from distributor shelves.
Panel Sizes
FR4 panelizes more efficiently for fabrication with 18”x24” and 21”x24” sheets minimizing waste when ganging small PCB arrays. Rogers maximum 16”x20” panels often yield poorer utilization rates driving cost up.
Certifications
Medical and defense customers requiring certified GEIT or UL standards compliance drives applications towards proven industry-standard FR4 technology over Rogers still catching up on qualifications.
Understanding higher costs and lead times planning appropriate Rogers placement where essential electrical performance justifies expense keeps overall PCB expenditures reasonable.
Comparison Table of Key Attributes
Attribute | Rogers Laminates | FR4 |
---|---|---|
Dielectric Constant | 3.0 | 4.2 to 4.8 |
Dissipation Factor | 0.0025 | 0.02 |
Water Absorption | 0.02% | 0.2% |
Thermal Conductivity | >0.5W/m-K | 0.3 W/m-K |
Z-axis CTE | 60 ppm/C | 180 ppm/C |
Dielectric Composition | PTFE/Woven Glass | Epoxy/Woven Glass |
Fabrication Process Control | Tight bounds | Looser standard deviations |
Typical Applications | Microwave, military/aerospace | Consumer/Commercial |
Relative Cost Factor | 5X to 10X | Baseline |
Lead Time | 8-12 weeks | 2-4 weeks |
This covers key electrical, physical and processing characteristics contrasting Rogers and FR4 substrates used manufacturing printed circuit boards in various applications.
PCB Stackup Design Guidelines
Some good design practices help leverage Rogers selectively where most beneficial when combining with standard FR4 laminates:
- Place Rogers only locally on critical high-frequency signal layers avoiding full board layers to minimize costs
- Group high-speed interfaces nearby through sequential layers to isolate signals across constant materials
- Assign plane layers evenly spaced through stackups encasing sets of routing layers
- Transitions from Rogers-to-FR4 dielectrics require mitigating steps/tapers decreasing impedance deviations
- Condense imaging tolerance budget on thicker Rogers layers reserving space for looser FR4
By budgeting Rogers judiciously following electrical partitioning practices maximizes value from specialized laminates blended into cost-optimized PCB stackups.
Improved FR4 Materials Comparison
Newer FR4 material formulations enhance electrical performance approaching Rogers levels by utilizing:
Modified Resin Chemistry – Blends of cyanate esters into epoxy resins improve moisture resistance and dimensional stability at higher temperatures reaching 130°C
Tighter Weave Control – Employing 106 style glass fabrics with precise alignments reduces resin gaps stabilizing dielectric constants reaching ±5% distributions even with FR4
Additional Reinforcement – Layered polyimide films or bonded metal inserts strengthen constructions reducing fractures including around drilled holes and cuts
Yet despite better consistency, these improved FR4 variants still lag Rogers combinations of thermal conductivity and low water absorption important sustaining precision electrical parameters long-term especially for aerospace and defense applications. They strike cost/performance middle ground below Rogers but above basic FR4.
Future Outlook
Emergence of new thermoplastic dielectric materials offers potential cost and electrical performance surpassing both Rogers and FR4 as fabrication processes adapting handling requirements:
Polyphenylene Sulfide Alloys (PPS) – With low loss, stable dielectric constants under 3.4 and loss tangents below 0.005, PPS suits next-gen radar and communication designs.
LCP Blends – Liquid crystal polymer composites approach Rogers microwave characteristics at nearer FR4 pricing. Dimensional stability still trails thermosets however.
Polymide Films – Thin polyimide insulating layers bond into stackups isolate signals with low dielectric constants consistently leveraging flexible circuit technology.
As volumes scale reinforcing process knowledge using these new materials, engineers access superior performing alternatives to traditional thermoset laminates more affordably.
Conclusion
This detailed contrast explored how Rogers and FR4 differ substantially regarding:
- Electrical factors like dielectric consistency benefiting high frequency signals
- Material composition and additive elements controlling properties precisely
- Fabrication process tolerances reachable with each substrate types
- Cost and lead time overheads using niche Roger’s materials
- Usage cases from commercial towards precision microwave/aerospace PCB technologies
Blending appropriate Rogers materials only where critical electrical requirements justify additional expenses optimizes overall printed circuit board cost structures fitting widely varied product technology needs leveraging relative strengths of both platform material families as new options keep emerging.
Understanding these fundamental tradeoffs empowers engineers selecting ideal substrates matching application requirements.
Frequently Asked Questions
Here are answers to common questions regarding Roger’s versus FR4 substrates used in PCBs:
Can traces be routed between Rogers and FR4 layers or should they stay isolated?
Seamless transitions prove extremely difficult given different properties. Use tapers/steps to transition. Better to assign whole layers commiting to either material type when routing groups of signals.
Do surface finishes like ENIG or Immersion Silver coat as evenly on Rogers as well as FR4?
Yes, since both use copper foil starting points, common finishes adhere evenly. But lower glass content on Roger’s means more foil adjustment expansion and contractions stressing layers.
Why does Rogers have higher fabrication costs if made up of epoxy resin like FR4?
Proprietary fluoropolymer, ceramic and microfiber ingredient processing costs exceed standard FR4 formulations leveraging ubiquitous silica fills and coarse weaves bringing economy of scale.
Can Rogers effectively replace FR4 for typical consumer electronics applications?
Technically yes, but excessive expense not warranted for non-critical digital functions. However selected microwave portions like antenna signal traces or oscillators may justify localized Rogers usage even on cost-focused commercial boards.
What causes order lead times much longer for Rogers laminates compared to FR4?
Smaller custom Rogers production batches require procuring specialized raw materials made-to-order rather than pulling common FR4 sheets off warehouse shelves already manufactured at huge economies of scale.
0 Comments