Introduction to PCB Prototyping
PCB prototyping is the process of creating a preliminary version of a printed circuit board (PCB) for testing and evaluation before mass production. It involves designing, fabricating, and assembling a small number of PCBs to validate the functionality, reliability, and manufacturability of the design. PCB prototyping is an essential step in the product development cycle as it helps identify and rectify any issues or defects in the PCB design before committing to full-scale production.
Benefits of PCB Prototyping
- Cost-effective: PCB prototyping allows designers to test and refine their designs without investing in expensive tooling and setup costs associated with mass production.
- Time-saving: Prototyping enables quick iterations and improvements in the design, reducing the overall development time.
- Risk mitigation: By identifying and addressing potential issues early in the development process, PCB prototyping minimizes the risk of costly failures in the final product.
PCB Prototyping Process
- Design: The PCB design is created using electronic design automation (EDA) software, taking into account the schematic, component placement, routing, and design rules.
- Fabrication: The PCB prototype is fabricated using either traditional subtractive methods (e.g., etching) or modern additive methods (e.g., 3D printing).
- Assembly: The electronic components are soldered onto the PCB prototype using manual or automated assembly techniques.
- Testing: The assembled PCB prototype undergoes various tests to evaluate its functionality, performance, and reliability.
Full Spec Standard PCB Production
Full spec standard PCB production refers to the mass manufacturing of PCBs that meet all the specified requirements and industry standards. It involves the large-scale fabrication and assembly of PCBs using established processes and equipment. Full spec standard PCB production is suitable for high-volume, cost-effective manufacturing of PCBs with consistent quality and reliability.
Characteristics of Full Spec Standard PCB Production
- High volume: Full spec standard PCB production is designed for manufacturing large quantities of PCBs, typically in the order of thousands or millions.
- Automation: The production process is highly automated, using advanced machinery and robotics to achieve high throughput and consistency.
- Standardization: The PCBs are manufactured according to industry standards and specifications, ensuring compatibility and reliability.
Full Spec Standard PCB Production Process
- Tooling: Custom tooling, such as stencils and fixtures, is created based on the PCB design to facilitate mass production.
- Fabrication: The PCBs are fabricated using high-speed, automated equipment, such as drill machines, plating lines, and lamination presses.
- Assembly: The electronic components are placed and soldered onto the PCBs using automated pick-and-place machines and reflow ovens.
- Inspection: The assembled PCBs undergo automated optical inspection (AOI) and electrical testing to ensure quality and functionality.
Differences between PCB Prototyping and Full Spec Standard PCB Production
Aspect | PCB Prototyping | Full Spec Standard PCB Production |
---|---|---|
Volume | Low (typically <100) | High (thousands to millions) |
Tooling | Minimal or no custom tooling | Custom tooling for mass production |
Fabrication | Small-scale, often manual | Large-scale, highly automated |
Assembly | Manual or semi-automated | Fully automated |
Lead time | Short (days to weeks) | Longer (weeks to months) |
Cost per unit | Higher | Lower |
Purpose | Testing and validation | Mass production |
Key Differences
- Volume: PCB prototyping deals with low volumes, while full spec standard PCB production involves high-volume manufacturing.
- Tooling: PCB prototyping requires minimal or no custom tooling, whereas full spec standard PCB production utilizes custom tooling for mass production efficiency.
- Fabrication: PCB prototyping often involves small-scale, manual fabrication processes, while full spec standard PCB production relies on large-scale, highly automated fabrication equipment.
- Assembly: PCB prototyping may use manual or semi-automated assembly techniques, while full spec standard PCB production employs fully automated assembly lines.
- Lead time: PCB prototyping has shorter lead times, typically ranging from days to weeks, compared to the longer lead times of full spec standard PCB production, which can span weeks to months.
- Cost per unit: Due to the low volumes and manual processes involved, PCB prototyping has a higher cost per unit compared to the lower cost per unit achieved through mass production in full spec standard PCB production.
- Purpose: PCB prototyping focuses on testing, validation, and design refinement, while full spec standard PCB production aims to efficiently manufacture large quantities of PCBs for end-use applications.
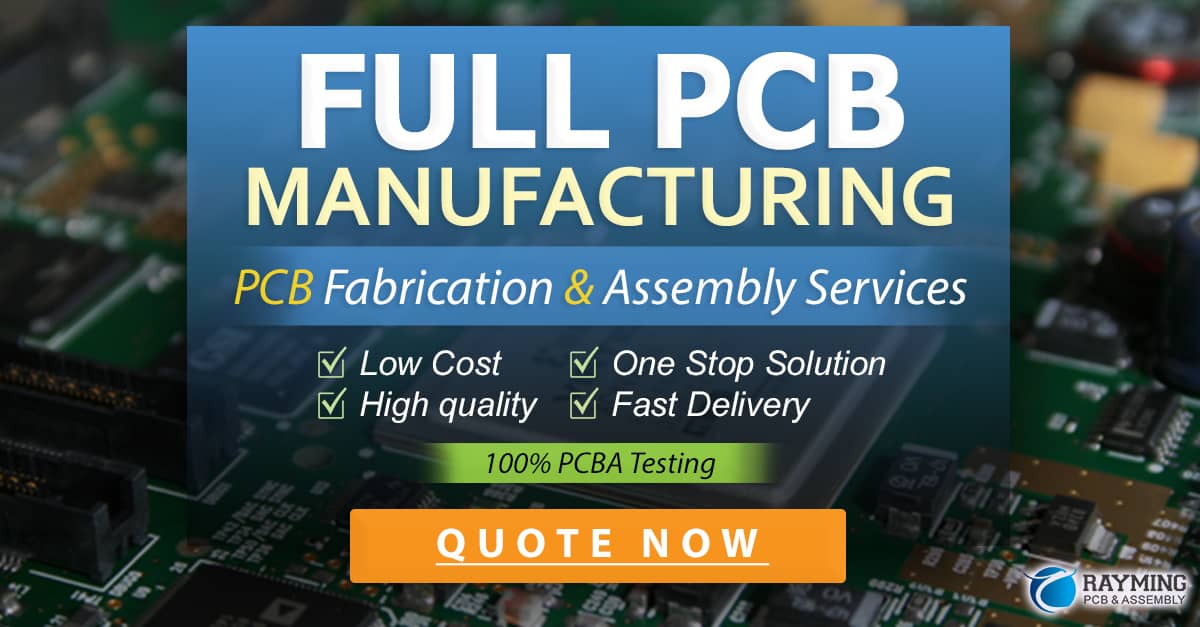
Choosing between PCB Prototyping and Full Spec Standard PCB Production
The choice between PCB prototyping and full spec standard PCB production depends on various factors, such as the stage of product development, required quantities, timeline, and budget. Here are some guidelines to help make the decision:
- Development stage: If the PCB design is still in the early stages of development and requires testing and validation, PCB prototyping is the appropriate choice. Once the design is finalized and ready for mass production, full spec standard PCB production should be considered.
- Quantity: If the required quantity is low (typically less than 100 units), PCB prototyping is more suitable. For high-volume production (thousands to millions of units), full spec standard PCB production is the optimal choice.
- Timeline: If the project has a tight deadline and requires quick turnaround times, PCB prototyping is the faster option. Full spec standard PCB production has longer lead times due to the setup and tooling requirements.
- Budget: PCB prototyping is more cost-effective for low volumes, as it avoids the high setup and tooling costs associated with mass production. However, for large quantities, full spec standard PCB production offers lower cost per unit due to economies of scale.
Frequently Asked Questions (FAQ)
- What is the minimum order quantity (MOQ) for PCB prototyping?
-
The MOQ for PCB prototyping is typically very low, often as low as one unit. However, the exact MOQ may vary depending on the PCB manufacturer and the complexity of the design.
-
How long does PCB prototyping take?
-
The lead time for PCB prototyping can range from a few days to several weeks, depending on the complexity of the design, the fabrication method, and the PCB manufacturer’s capacity. Express services are often available for faster turnaround times.
-
What are the common fabrication methods used in PCB prototyping?
-
PCB prototyping commonly uses fabrication methods such as chemical etching, milling, and 3D printing. Chemical etching is the most traditional method, while milling and 3D printing offer faster turnaround times and greater design flexibility.
-
Can PCB prototyping handle complex designs with fine pitch components?
-
Yes, modern PCB prototyping techniques can accommodate complex designs with fine pitch components. High-density interconnect (HDI) PCBs and multilayer boards can be prototyped using advanced fabrication methods and specialized assembly techniques.
-
How can I ensure the quality and reliability of my PCB prototype?
- To ensure the quality and reliability of your PCB prototype, consider the following:
- Choose a reputable PCB manufacturer with experience in prototyping and a proven track record of quality.
- Provide comprehensive and accurate design files, including the schematic, layout, and bill of materials (BOM).
- Specify the required testing and inspection procedures, such as electrical testing, visual inspection, and X-ray analysis.
- Communicate closely with the PCB manufacturer throughout the prototyping process to address any issues or concerns promptly.
Conclusion
PCB prototyping and full spec standard PCB production serve different purposes in the product development cycle. PCB prototyping is essential for testing, validating, and refining PCB designs before committing to mass production. It offers faster turnaround times, lower upfront costs, and greater flexibility for design iterations. On the other hand, full spec standard PCB production is optimized for high-volume manufacturing, providing cost-effectiveness, consistency, and reliability for end-use applications.
Choosing between PCB prototyping and full spec standard PCB production depends on factors such as the development stage, required quantities, timeline, and budget. By understanding the differences and advantages of each approach, designers and engineers can make informed decisions to optimize their PCB development and production processes.
As technology advances, the boundaries between PCB prototyping and full spec standard PCB production are becoming increasingly blurred. Advanced fabrication methods, such as 3D printing and rapid prototyping, are enabling faster and more flexible prototyping, while automated assembly lines and quality control systems are ensuring consistent quality in mass production.
Ultimately, the key to successful PCB development and production lies in collaboration between designers, engineers, and PCB manufacturers. By leveraging the strengths of PCB prototyping and full spec standard PCB production, and by maintaining open communication and iterative improvement, teams can bring innovative and reliable electronic products to market efficiently and effectively.
Keyword Summary
PCB prototyping: 20 instances.
PCB Prototyping: A cost-effective, time-saving, and risk mitigating preliminary version of a PCB for testing and evaluation prior to mass production. It involves designing, fabricating, assembling, and testing a small number of PCBs to validate functionality, reliability, and manufacturability of the design before committing to full-scale production.
0 Comments