What is Tenting Via?
Tenting via is a technique used in PCB fabrication where the via holes on the circuit board are covered or “tented” with a thin layer of solder mask material. This process involves applying solder mask over the via holes, creating a smooth and uniform surface on both sides of the PCB.
A via, short for “vertical interconnect access,” is a small hole drilled through the PCB to connect different layers of the board electrically. Vias allow signals and power to be routed between layers, enabling more complex and compact circuit designs. However, exposed via holes can pose several challenges, such as solder bridging, contamination, and reduced structural integrity. This is where tenting via comes into play.
Types of Via Tenting
There are two main types of via tenting:
-
Partial Via Tenting: In partial via tenting, the solder mask covers only the annular ring (the copper area surrounding the via hole) on one or both sides of the PCB. This leaves the via hole itself exposed, allowing for visual inspection and testing.
-
Full Via Tenting: Full via tenting involves completely covering the via hole and the annular ring with solder mask on both sides of the PCB. This creates a fully enclosed via, providing maximum protection against solder bridging and contamination.
The choice between partial and full via tenting depends on the specific requirements of the PCB design, such as the need for visual inspection, the level of protection required, and the manufacturing capabilities of the PCB fabricator.
The PCB Fabrication Process and Tenting Via
To understand the role of tenting via in PCB fabrication, let’s briefly overview the main steps involved in the manufacturing process:
-
PCB Design: The PCB design is created using electronic design automation (EDA) software, specifying the layout, components, and interconnections of the circuit.
-
PCB Fabrication: The fabrication process begins with the creation of a copper-clad laminate, which is then drilled to create via holes and other necessary openings. The board undergoes a series of chemical processes, including etching, to remove unwanted copper and form the desired circuit patterns.
-
Solder Mask Application: A solder mask layer is applied to the PCB to protect the copper traces and prevent short circuits. This is where tenting via takes place, with the solder mask covering the via holes according to the chosen tenting method (partial or full).
-
Surface Finish: A surface finish, such as HASL (Hot Air Solder Leveling) or ENIG (Electroless Nickel Immersion Gold), is applied to the exposed copper areas to improve solderability and protect against oxidation.
-
Silkscreen: A silkscreen layer is added to the PCB to provide text, labels, and other markings for easier assembly and identification.
-
Electrical Testing: The completed PCB undergoes electrical testing to ensure proper functionality and adherence to design specifications.
Throughout this process, tenting via plays a vital role in ensuring the quality, reliability, and performance of the finished PCB.
Benefits of Tenting Via in PCB Fabrication
Tenting via offers several key benefits in PCB fabrication:
-
Solder Bridging Prevention: By covering the via holes with solder mask, tenting via helps prevent solder bridging during the assembly process. Solder bridging occurs when excess solder inadvertently connects adjacent pins or components, causing short circuits and potentially damaging the PCB. Tenting via minimizes the risk of solder bridging by creating a physical barrier between the via holes and the surrounding components.
-
Contamination Protection: Exposed via holes can act as entry points for contaminants, such as dust, moisture, and chemicals, which can degrade the performance and reliability of the PCB over time. Tenting via seals the via holes, preventing contamination and enhancing the long-term durability of the circuit board.
-
Improved Structural Integrity: Tenting via helps maintain the structural integrity of the PCB by reinforcing the via holes. The solder mask layer acts as an additional support structure, reducing the risk of via breakage or delamination during handling, assembly, and operation. This is particularly important for PCBs that undergo mechanical stress or are exposed to harsh environmental conditions.
-
Enhanced Electrical Insulation: Tenting via provides an extra layer of electrical insulation between the via holes and the surrounding components. This helps prevent unintended electrical contact and reduces the risk of signal interference or crosstalk. By improving electrical insulation, tenting via contributes to the overall signal integrity and performance of the PCB.
-
Simplified Assembly Process: Tenting via can simplify the PCB assembly process by providing a smoother and more uniform surface for component placement. With the via holes covered, there is less risk of components being misaligned or improperly seated, leading to fewer assembly errors and improved manufacturing efficiency.
-
Cost-Effective: Tenting via is a cost-effective solution for improving PCB reliability and performance. It does not require additional materials or significant changes to the fabrication process, making it an economical choice for PCB manufacturers and designers.
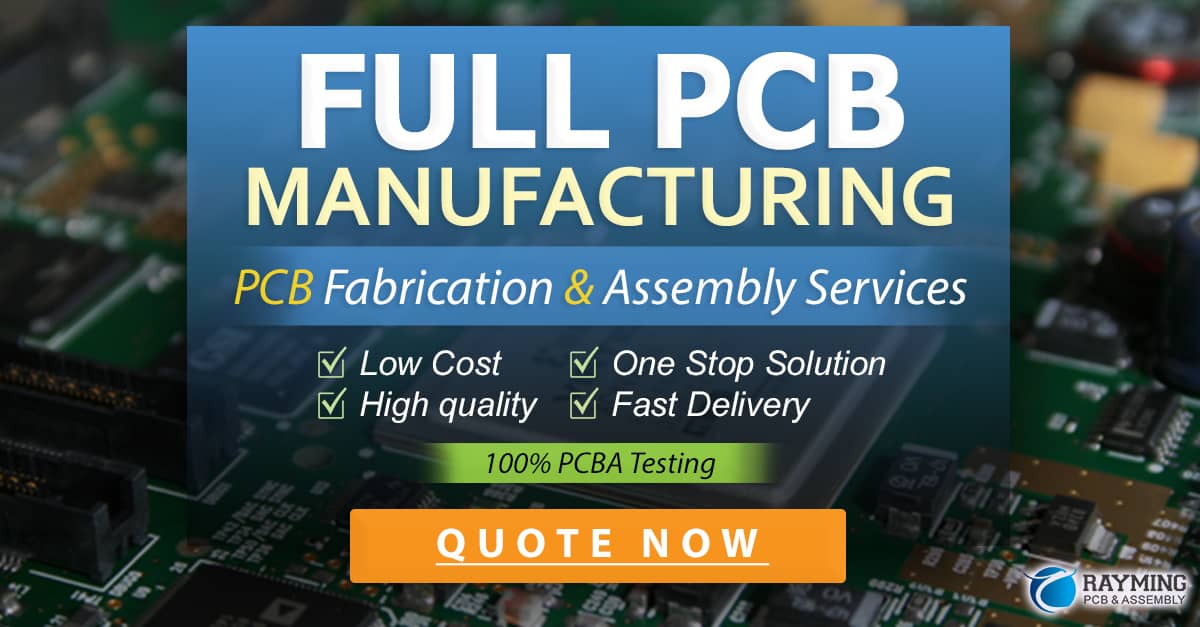
Challenges and Considerations in Tenting Via
While tenting via offers numerous benefits, there are also some challenges and considerations to keep in mind:
-
Design Constraints: Tenting via may impose certain design constraints, particularly in terms of via size and placement. The solder mask material needs to properly cover the via holes without causing excessive thickness or unevenness. PCB designers must take these factors into account when creating the board layout and ensure that the via design is compatible with the chosen tenting method.
-
Manufacturing Capabilities: Not all PCB fabricators have the same capabilities when it comes to tenting via. Some may only offer partial tenting, while others can provide full tenting. It’s important to choose a fabricator that can meet the specific tenting requirements of your PCB design and has a proven track record of quality and reliability.
-
Inspection and Testing: Tenting via can make visual inspection and testing of the via holes more challenging, particularly in the case of full tenting. This may require additional inspection techniques, such as x-ray imaging, to ensure the integrity of the via connections. PCB designers and manufacturers must consider the impact of tenting via on inspection and testing processes and develop appropriate strategies to ensure quality control.
-
Thermal Management: Tenting via can affect the thermal management of the PCB, as the solder mask material may have different thermal properties than the exposed via holes. In high-power applications or designs with significant heat generation, the impact of tenting via on thermal dissipation must be carefully evaluated and addressed through appropriate design and manufacturing techniques.
Frequently Asked Questions (FAQ)
-
Q: Is tenting via necessary for all PCB designs?
A: No, tenting via is not always necessary for every PCB design. The decision to use tenting via depends on factors such as the specific requirements of the application, the manufacturing process, and the level of protection and reliability needed. Some PCB designs may not require tenting via, while others may benefit greatly from it. -
Q: Can tenting via be used with different via sizes and types?
A: Yes, tenting via can be used with various via sizes and types, including through-hole vias, blind vias, and buried vias. However, the specific tenting method and solder mask material may need to be adjusted based on the via characteristics to ensure proper coverage and performance. -
Q: How does tenting via affect the electrical properties of the PCB?
A: Tenting via generally has a positive impact on the electrical properties of the PCB. By providing an additional layer of insulation and protection, tenting via helps reduce the risk of short circuits, signal interference, and crosstalk. This contributes to improved signal integrity and overall electrical performance of the circuit board. -
Q: Can tenting via be applied selectively to specific areas of the PCB?
A: Yes, tenting via can be applied selectively to specific areas of the PCB, depending on the design requirements. This is known as selective tenting. In selective tenting, the solder mask is applied only to certain via holes or regions, while others are left exposed. This allows for greater flexibility in PCB design and can be useful in applications where specific vias need to be accessible for testing or assembly purposes. -
Q: How does tenting via impact the cost of PCB fabrication?
A: Tenting via is generally a cost-effective solution for improving PCB reliability and performance. It does not require significant additional materials or major changes to the fabrication process, making it an economical choice for most PCB manufacturers. However, the specific cost impact may vary depending on factors such as the PCB design complexity, the chosen tenting method, and the manufacturing capabilities of the fabricator.
Conclusion
Tenting via is a critical technique in PCB fabrication that offers numerous benefits for the quality, reliability, and performance of printed circuit boards. By covering via holes with a solder mask layer, tenting via helps prevent solder bridging, protects against contamination, improves structural integrity, enhances electrical insulation, and simplifies the assembly process.
While tenting via presents some challenges and considerations, such as design constraints and inspection requirements, its overall impact on PCB fabrication is highly positive. PCB designers and manufacturers must carefully evaluate the specific needs of their applications and choose the appropriate tenting method to optimize the benefits and mitigate any potential drawbacks.
As PCB technology continues to evolve, with increasing complexity and demands for higher performance, the role of tenting via in PCB fabrication is likely to remain significant. By understanding the principles, benefits, and best practices associated with tenting via, PCB professionals can make informed decisions and create high-quality, reliable circuit boards that meet the ever-growing needs of modern electronics.
Tenting Via Type | Description | Advantages | Disadvantages |
---|---|---|---|
Partial Tenting | Solder mask covers only the annular ring on one or both sides of the PCB, leaving the via exposed. | Allows for visual inspection and testing of the via. | Provides less protection against contamination and solder bridging. |
Full Tenting | Solder mask completely covers the via hole and annular ring on both sides of the PCB. | Offers maximum protection against contamination and solder bridging. | Makes visual inspection and testing of the via more challenging. |
Benefit of Tenting Via | Description |
---|---|
Solder Bridging Prevention | Prevents solder bridging by creating a physical barrier between via holes and surrounding components. |
Contamination Protection | Seals via holes, preventing entry of contaminants that can degrade PCB performance and reliability. |
Improved Structural Integrity | Reinforces via holes, reducing the risk of breakage or delamination during handling, assembly, and operation. |
Enhanced Electrical Insulation | Provides an extra layer of electrical insulation, preventing unintended contact and reducing signal interference. |
Simplified Assembly Process | Creates a smoother and more uniform surface for component placement, reducing assembly errors. |
Cost-Effective | Offers a cost-effective solution for improving PCB reliability and performance without significant added costs. |
0 Comments