Understanding Solder Paste Slump
Definition of Solder Paste Slump
Solder paste slump is defined as the undesired flow or spreading of solder paste after it has been deposited onto the PCB pads through a stencil printing process. In other words, it is the tendency of the solder paste to lose its original printed shape and geometry over time, especially when exposed to elevated temperatures or prolonged storage periods. Slump can occur in both the horizontal and vertical directions, referred to as x-y slump and z-slump, respectively.
Importance of Controlling Solder Paste Slump
Controlling solder paste slump is crucial for several reasons:
- Solder joint integrity: Excessive slump can lead to bridging between adjacent pads, causing short circuits and compromising the electrical integrity of the solder joints.
- Component placement accuracy: Slumped solder paste may cause misalignment of components during the placement process, resulting in poor soldering and reduced reliability.
- Consistent solder joint volume: Slump can alter the volume of solder paste on each pad, leading to inconsistent solder joint formation and potentially impacting the mechanical strength of the solder joint.
- Aesthetics: Slumped solder joints may have an uneven or distorted appearance, which can be undesirable from a cosmetic standpoint.
Factors Influencing Solder Paste Slump
Several factors can contribute to the occurrence and extent of solder paste slump. Understanding these factors is essential for implementing effective slump control measures.
Solder Paste Composition
The composition of solder paste plays a significant role in its slump behavior. Key components that influence slump include:
- Solder alloy: The type of solder alloy used in the paste, such as tin-lead (SnPb) or lead-free alloys (e.g., SAC305), can affect slump characteristics due to differences in melting temperatures and rheological properties.
- Particle size distribution: The size and distribution of solder particles in the paste impact its flow and slump behavior. Finer particles tend to exhibit less slump compared to coarser particles.
- Flux chemistry: The flux system used in the solder paste, including the type of activators, rheology modifiers, and thixotropic agents, influences the paste’s ability to resist slump.
Stencil Design and Printing Parameters
The stencil design and printing process parameters also play a crucial role in managing solder paste slump:
- Aperture size and shape: The dimensions and geometry of the stencil apertures determine the initial volume and shape of the printed solder paste deposits. Optimal aperture design can help minimize slump.
- Stencil thickness: Thicker stencils generally result in higher solder paste deposits, which may be more prone to slump compared to thinner deposits.
- Printing pressure and speed: The pressure applied during stencil printing and the speed of the squeegee can affect the solder paste deposit consistency and potential for slump.
- Stencil surface finish: The surface finish of the stencil, such as nano-coating or laser-cut finish, can influence the release characteristics of the solder paste and its slump behavior.
Environmental Conditions
Environmental factors, particularly temperature and humidity, can impact solder paste slump:
- Temperature: Higher ambient temperatures can accelerate the slumping process by reducing the viscosity of the solder paste.
- Humidity: Excessive humidity can cause the solder paste to absorb moisture, leading to changes in its rheological properties and increased slump tendency.
Storage and Handling
Proper storage and handling of solder paste are essential to minimize slump:
- Storage temperature: Solder paste should be stored at the manufacturer-recommended temperature range to maintain its stability and prevent premature slumping.
- Shelf life: Using solder paste within its specified shelf life ensures optimal performance and reduces the risk of slump-related issues.
- Handling practices: Gentle handling of solder paste, avoiding excessive agitation or exposure to temperature fluctuations, helps preserve its integrity and minimize slump.
Measuring and Quantifying Solder Paste Slump
To effectively control solder paste slump, it is necessary to have reliable methods for measuring and quantifying slump behavior. Several techniques are commonly used in the industry:
Slump Test Methods
- Cold slump test: This test involves printing solder paste on a test substrate and measuring the change in deposit dimensions after a specified time period at room temperature. The cold slump test provides an indication of the paste’s ability to maintain its shape under ambient conditions.
- Hot slump test: In this test, the printed solder paste is subjected to elevated temperatures, typically close to the solder alloy’s melting point, to simulate the effects of the reflow process. The hot slump test evaluates the paste’s resistance to slumping under thermal stress.
- Tack life test: This test assesses the solder paste’s ability to retain its tack strength (adhesion to components) over time. A longer tack life generally correlates with better slump resistance.
Slump Measurement Techniques
- Visual inspection: Simple visual examination of the printed solder paste deposits can provide a qualitative assessment of slump. Bridging, spreading, or distortion of the deposits can be observed visually.
- Optical measurement: Automated optical inspection (AOI) systems or microscopes can be used to measure the dimensions of solder paste deposits before and after slump testing. These tools provide quantitative data on slump behavior.
- 3D profiling: Advanced 3D solder paste inspection (SPI) systems use laser scanning or structured light techniques to create detailed 3D profiles of the solder paste deposits. These systems can accurately measure the volume, height, and shape of the deposits, enabling precise slump characterization.
Slump Test Method | Description | Purpose |
---|---|---|
Cold Slump Test | Measures slump at room temperature | Evaluates paste stability under ambient conditions |
Hot Slump Test | Measures slump at elevated temperatures | Assesses paste performance during reflow |
Tack Life Test | Evaluates paste’s ability to retain tack strength | Relates tack life to slump resistance |
Slump Measurement Technique | Description | Advantage |
---|---|---|
Visual Inspection | Qualitative assessment of slump | Quick and simple method |
Optical Measurement | Quantitative measurement using AOI or microscopes | Provides dimensional data for slump analysis |
3D Profiling | Detailed 3D characterization using SPI systems | Accurate volume and shape measurement of deposits |
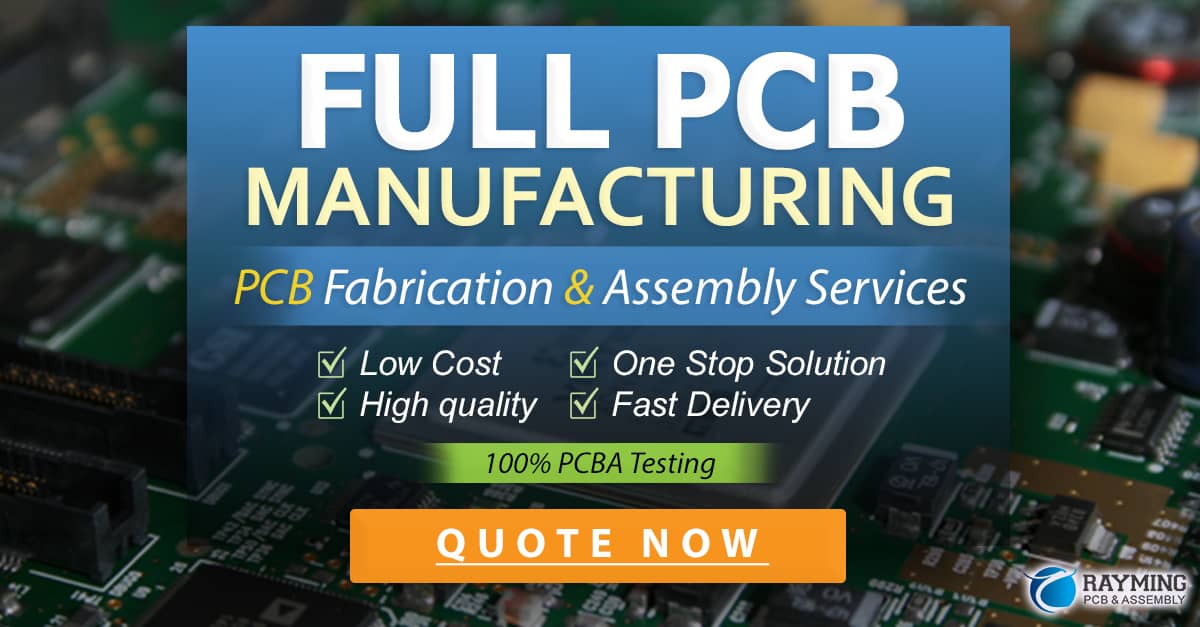
Strategies for Controlling Solder Paste Slump
To minimize the occurrence and impact of solder paste slump, several strategies can be employed:
Solder Paste Selection
Choosing the right solder paste is crucial for managing slump. Consider the following factors when selecting a solder paste:
- Alloy composition: Select a solder alloy that is compatible with the PCB and component requirements while offering good slump resistance properties.
- Particle size distribution: Opt for solder pastes with finer particle sizes, as they tend to exhibit better slump resistance compared to coarser pastes.
- Flux system: Choose a solder paste with a robust flux system that provides good rheological control and slump resistance.
Stencil Design Optimization
Optimizing the stencil design can help control solder paste slump:
- Aperture size and shape: Use aperture dimensions and shapes that are appropriate for the pad sizes and pitch of the PCB. Avoid excessively large or small apertures that may promote slump.
- Stencil thickness: Select a stencil thickness that provides sufficient solder paste volume while minimizing the risk of slump. Thinner stencils may be preferred for fine-pitch applications.
- Aperture wall tapering: Implement tapered aperture walls in the stencil design to facilitate solder paste release and reduce the likelihood of slump.
Printing Process Control
Proper control of the stencil printing process parameters is essential for managing slump:
- Printing pressure: Adjust the printing pressure to achieve consistent solder paste deposits without excessive compression, which can lead to slump.
- Squeegee speed: Optimize the squeegee speed to ensure uniform solder paste distribution and minimize the potential for slump.
- Stencil cleaning: Regularly clean the stencil to remove any residual solder paste or contaminants that may affect the printing quality and contribute to slump.
Environmental Control
Maintaining a controlled environment during solder paste storage, handling, and printing can help mitigate slump:
- Temperature control: Ensure that the solder paste is stored and used within the recommended temperature range to prevent premature slumping.
- Humidity control: Maintain a suitable humidity level in the production area to avoid excessive moisture absorption by the solder paste, which can impact its slump behavior.
Reflow Profile Optimization
Optimizing the reflow soldering profile can help minimize slump during the heating process:
- Ramp rate: Use an appropriate ramp rate during the initial heating stage to allow the solder paste to gradually dry and stabilize before reaching the melting temperature.
- Peak temperature: Ensure that the peak reflow temperature is within the recommended range for the solder paste and PCB materials to avoid excessive slump.
- Time above liquidus: Control the time above liquidus (TAL) to minimize the duration for which the solder paste remains in a molten state, reducing the opportunity for slump to occur.
Frequently Asked Questions (FAQ)
-
What is solder paste slump, and why is it important to control?
Solder paste slump refers to the undesired flow or spreading of solder paste after it has been printed on PCB pads. Controlling slump is important to ensure solder joint integrity, component placement accuracy, consistent solder joint volume, and acceptable aesthetics. -
What are the main factors that influence solder paste slump?
The main factors influencing solder paste slump include solder paste composition (alloy, particle size, flux chemistry), stencil design and printing parameters (aperture size and shape, thickness, pressure, speed), environmental conditions (temperature, humidity), and storage and handling practices. -
How can solder paste slump be measured and quantified?
Solder paste slump can be measured using various methods, such as cold slump test, hot slump test, and tack life test. Measurement techniques include visual inspection, optical measurement using AOI or microscopes, and 3D profiling using SPI systems. -
What strategies can be employed to control solder paste slump?
Strategies for controlling solder paste slump include careful solder paste selection (considering alloy composition, particle size, flux system), stencil design optimization (aperture size and shape, thickness, wall tapering), printing process control (pressure, speed, cleaning), environmental control (temperature, humidity), and reflow profile optimization (ramp rate, peak temperature, time above liquidus). -
How does the reflow soldering profile affect solder paste slump?
The reflow soldering profile can impact solder paste slump during the heating process. Optimizing the ramp rate, peak temperature, and time above liquidus can help minimize slump. A gradual ramp rate allows the solder paste to dry and stabilize before reaching the melting temperature, while controlling the peak temperature and time above liquidus reduces the opportunity for slump to occur when the solder is in a molten state.
Conclusion
Solder paste slump is a critical aspect of SMT assembly that requires careful attention and control to ensure the quality and reliability of solder joints. By understanding the factors influencing slump, employing appropriate measurement techniques, and implementing targeted control strategies, manufacturers can effectively manage solder paste slump and achieve optimal soldering results.
Selecting the right solder paste, optimizing stencil design, controlling printing parameters, maintaining a suitable environment, and optimizing the reflow profile are key elements in minimizing slump. Regular monitoring, measurement, and process optimization are essential for consistently producing high-quality PCB assemblies with minimal solder paste slump issues.
By addressing solder paste slump through a comprehensive approach, manufacturers can improve yield, reduce rework, and enhance the overall reliability of their electronic products. Staying updated with the latest advancements in solder paste technology, printing processes, and inspection methods will enable continuous improvement in slump control and SMT assembly performance.
0 Comments