Introduction to Prepreg PCB
Printed Circuit Boards (PCBs) are essential components in modern electronic devices. They provide a platform for mounting and interconnecting electronic components, ensuring efficient and reliable operation. One crucial element in the construction of high-quality PCBs is the use of prepreg material. In this article, we will delve into the world of prepreg PCBs, exploring what prepreg is, its properties, manufacturing process, and its significance in the PCB industry.
What is Prepreg?
Prepreg, short for pre-impregnated, is a composite material used in the manufacturing of PCBs. It consists of a reinforcing fabric, typically glass fiber, that is pre-impregnated with a partially cured resin system. The resin is usually an epoxy-based material that has been partially cured to a specific stage, known as the B-stage.
Composition of Prepreg
The composition of prepreg can be broken down into two main components:
- Reinforcing Fabric:
- Glass fiber: The most common reinforcing fabric used in prepreg is glass fiber. It provides excellent mechanical strength, dimensional stability, and electrical insulation properties.
-
Other materials: In some specialized applications, other reinforcing fabrics such as aramid or carbon fiber may be used.
-
Resin System:
- Epoxy resin: Epoxy resin is the most widely used resin system in prepreg. It offers good mechanical strength, chemical resistance, and thermal stability.
- Other resins: Depending on specific requirements, other resin systems like polyimide or bismaleimide may be employed.
The combination of the reinforcing fabric and the partially cured resin system gives prepreg its unique properties and makes it an essential material in PCB fabrication.
Properties of Prepreg
Prepreg exhibits several key properties that make it suitable for use in PCB manufacturing:
- Mechanical Strength:
- High tensile strength: The reinforcing fabric, such as glass fiber, provides prepreg with excellent tensile strength, allowing it to withstand the stresses encountered during PCB manufacturing and operation.
-
Dimensional stability: Prepreg maintains its shape and dimensions even under high temperatures and pressures, ensuring the integrity of the PCB structure.
-
Electrical Properties:
- Insulation: The resin system in prepreg acts as an electrical insulator, preventing short circuits and ensuring proper functioning of the PCB.
-
Dielectric constant: Prepreg has a controlled dielectric constant, which is essential for maintaining signal integrity and minimizing signal loss in high-frequency applications.
-
Thermal Properties:
- Glass transition temperature (Tg): Prepreg has a specific glass transition temperature, above which the resin system softens and becomes more flexible. This property is crucial during the lamination process of PCB manufacturing.
-
Thermal conductivity: The resin system in prepreg provides good thermal conductivity, allowing heat to dissipate efficiently from the electronic components mounted on the PCB.
-
Chemical Resistance:
- Prepreg exhibits excellent chemical resistance, withstanding exposure to various chemicals and solvents commonly used in PCB manufacturing and assembly processes.
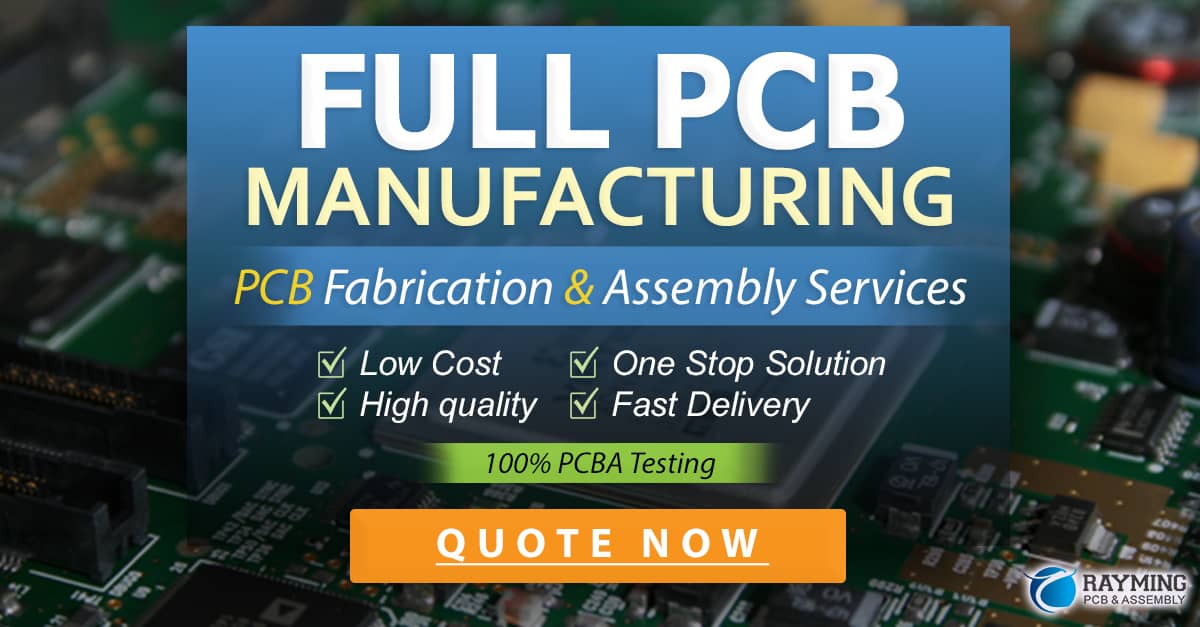
Manufacturing Process of Prepreg PCB
The manufacturing process of prepreg PCBs involves several key steps:
- Impregnation:
- The reinforcing fabric, such as glass fiber, is impregnated with the partially cured resin system.
-
The impregnation process ensures uniform distribution of the resin throughout the fabric.
-
Partial Curing:
- After impregnation, the prepreg is partially cured to the B-stage.
-
The B-stage represents a state where the resin is not fully cured but has reached a stable, handleable form.
-
Cutting and Lamination:
- The prepreg is cut to the desired size and shape based on the PCB design.
- Multiple layers of prepreg are stacked along with copper foils and other materials to form the PCB stackup.
-
The stackup is then subjected to high temperature and pressure in a lamination press, causing the resin in the prepreg to flow and bond the layers together.
-
Drilling and Plating:
- After lamination, holes are drilled through the PCB stack to accommodate component leads and vias.
-
The holes are then plated with copper to establish electrical connections between layers.
-
Etching and Finishing:
- The copper foils on the outer layers of the PCB are etched to create the desired circuit patterns.
- Additional finishing processes, such as solder mask application and silkscreen printing, are carried out to complete the PCB manufacturing process.
The use of prepreg in PCB manufacturing ensures a strong, reliable, and high-quality board that can withstand the rigors of electronic applications.
Advantages of Using Prepreg in PCBs
Prepreg offers several advantages in the manufacturing and performance of PCBs:
- Enhanced Mechanical Strength:
- The reinforcing fabric in prepreg provides excellent mechanical strength to the PCB.
-
This strength ensures the PCB can withstand physical stresses during manufacturing, assembly, and operation.
-
Improved Dimensional Stability:
- Prepreg helps maintain the dimensional stability of the PCB, preventing warping or twisting.
-
This stability is crucial for maintaining the alignment of components and ensuring proper functionality.
-
Consistent Electrical Properties:
- The controlled dielectric constant of prepreg ensures consistent electrical properties throughout the PCB.
-
This consistency is essential for maintaining signal integrity and minimizing signal loss, especially in high-frequency applications.
-
Better Thermal Management:
- The thermal conductivity of prepreg helps dissipate heat generated by electronic components.
-
Efficient heat dissipation prevents overheating and enhances the reliability and longevity of the PCB.
-
Enhanced Durability:
- The chemical resistance and mechanical strength of prepreg contribute to the overall durability of the PCB.
- PCBs made with prepreg can withstand harsh environmental conditions and have an extended lifespan.
Types of Prepreg PCBs
Prepreg PCBs can be categorized based on the type of reinforcing fabric and resin system used. Here are some common types of prepreg PCBs:
Type | Reinforcing Fabric | Resin System | Characteristics |
---|---|---|---|
FR-4 | Glass Fiber | Epoxy | General-purpose, widely used in PCB industry |
High Tg FR-4 | Glass Fiber | Epoxy | Higher glass transition temperature (Tg) |
Polyimide | Glass Fiber | Polyimide | High temperature resistance, used in aerospace |
Bismaleimide Triazine | Glass Fiber | BT Resin | High Tg, low moisture absorption, high reliability |
PTFE | Glass Fiber | PTFE | Low dielectric constant, used in RF applications |
Applications of Prepreg PCBs
Prepreg PCBs find applications in various industries and electronic products:
- Consumer Electronics:
- Smartphones, tablets, laptops
- Wearable devices
-
Gaming consoles
-
Automotive Electronics:
- Engine control units (ECUs)
- Infotainment systems
-
Advanced driver assistance systems (ADAS)
-
Aerospace and Defense:
- Avionics systems
- Radar and communication equipment
-
Military-grade electronics
-
Medical Devices:
- Diagnostic equipment
- Monitoring systems
-
Implantable devices
-
Industrial Automation:
- Process control systems
- Robotics and machine control
- Industrial sensors and actuators
Frequently Asked Questions (FAQ)
- What is the difference between prepreg and core material in PCBs?
-
Prepreg is a partially cured composite material used to bond the layers of a PCB together during the lamination process. Core material, on the other hand, is a fully cured and rigid substrate that provides structural support to the PCB.
-
Can prepreg be used for single-layer PCBs?
-
While prepreg is primarily used in multi-layer PCBs to bond the layers together, it can also be used as a base material for single-layer PCBs. However, for single-layer PCBs, other materials like FR-4 laminates are more commonly used.
-
How does the type of resin system affect the properties of prepreg?
-
The type of resin system used in prepreg determines its specific properties. For example, epoxy resin provides good mechanical strength and chemical resistance, while polyimide resin offers high temperature resistance. The choice of resin system depends on the specific requirements of the PCB application.
-
What is the shelf life of prepreg material?
-
The shelf life of prepreg material varies depending on the specific formulation and storage conditions. Typically, prepreg has a shelf life of 6 to 12 months when stored at room temperature in a sealed moisture barrier bag. It is important to follow the manufacturer’s storage guidelines to ensure optimal performance.
-
Can prepreg be used for flexible PCBs?
- Yes, prepreg can be used in the construction of flexible PCBs. However, the type of reinforcing fabric and resin system used may differ from those used in rigid PCBs. Flexible prepregs often utilize polyimide or polyester reinforcing fabrics and flexible resin systems to achieve the desired flexibility.
Conclusion
Prepreg is a vital component in the manufacturing of high-quality PCBs. Its unique combination of reinforcing fabric and partially cured resin system provides PCBs with excellent mechanical strength, dimensional stability, and consistent electrical properties. The use of prepreg enables the fabrication of reliable and durable PCBs that can withstand the demands of various electronic applications.
As electronic devices continue to advance and become more complex, the role of prepreg in PCB manufacturing remains crucial. Understanding the properties, manufacturing process, and advantages of prepreg PCBs is essential for engineers, designers, and manufacturers in the electronics industry.
By leveraging the benefits of prepreg technology, PCB manufacturers can produce high-performance boards that meet the stringent requirements of modern electronic applications. From consumer electronics to aerospace and defense, prepreg PCBs find widespread use across industries, contributing to the advancement of technology and the development of innovative products.
0 Comments