Introduction to PCB Vias
A PCB (printed circuit board) via is a small hole drilled through a PCB that allows electrical connections to be made between different layers of the board. Vias are a crucial component in PCB design, enabling more complex circuits and denser board layouts by utilizing the inner layers of a multi-layer PCB.
Types of PCB Vias
There are several types of PCB vias, each with their own characteristics and uses:
Via Type | Description |
---|---|
Through Hole Via | Goes through the entire board, with pad on top and bottom |
Blind Via | Connects an outer layer to an inner layer, with pad on one side |
Buried Via | Connects inner layers, with no pad on outer layers |
Micro Via | A small blind via, typically laser drilled |
The choice of via type depends on the specific PCB design requirements, such as the number of layers, board thickness, component placement, and manufacturing capabilities.
PCB Via Design Considerations
Via Size and Drill Diameter
The size of a PCB via is an important design consideration. The via size is determined by the drill diameter and the annular ring, which is the copper pad surrounding the drilled hole. Smaller vias allow for denser board layouts but can be more challenging and expensive to manufacture.
Typical via drill diameters range from 0.2mm to 0.5mm, with smaller micro vias drilled by laser down to 0.1mm or less. The annular ring is typically 0.15mm to 0.3mm larger than the drill diameter on each side.
Via Placement and Spacing
The placement and spacing of vias on a PCB is critical for both functionality and manufacturability. Vias should be placed to minimize the length of traces and provide efficient connections between components and layers.
At the same time, vias must be spaced far enough apart to meet manufacturing tolerances and avoid defects such as shorts or open circuits. The minimum via spacing depends on the PCB fabrication capabilities and is typically 0.4mm to 0.6mm for standard vias and 0.2mm to 0.3mm for micro vias.
Signal Integrity and Impedance Matching
In high-speed PCB designs, the size and placement of vias can have a significant impact on signal integrity and impedance matching. Vias can introduce discontinuities in the signal path, causing reflections, crosstalk, and other issues that degrade signal quality.
To minimize these effects, PCB designers must carefully consider via geometry, including the drill diameter, pad size, and anti-pad size (clearance hole in adjacent layers). Techniques such as via stitching, where multiple vias are used in parallel, and differential pair via placement can help maintain signal integrity.
Thermal Management and Current Carrying Capacity
Vias also play a role in thermal management and current carrying capacity of a PCB. Large vias or multiple vias in parallel can be used to transfer heat from power-dissipating components to the PCB Copper planes or external heatsinks.
The current carrying capacity of a via depends on its cross-sectional area, determined by the drill diameter and plating thickness. PCB designers must ensure that vias are sized appropriately to handle the required current without excessive heating or voltage drop.
PCB Via Manufacturing Process
Drilling
The first step in creating PCB vias is drilling the holes through the board. For standard through-hole vias, mechanical drilling is used with carbide or diamond-tipped drill bits. The drilling process is carefully controlled to ensure accurate hole placement and avoid defects such as burrs or rough hole walls.
For blind and buried vias, controlled depth drilling is used to drill only partially through the board. This requires precise depth control and specialized equipment. Micro vias are typically drilled using laser drilling, which allows for smaller diameters and higher precision than mechanical drilling.
Plating
After drilling, the via holes are plated with copper to create an electrical connection between the layers. The most common plating method is electroless copper plating, where the board is immersed in a copper solution and the copper is deposited onto the hole walls through a chemical reaction.
The plating process starts with a thin conductive seed layer, typically applied by electroless deposition or sputtering. Then, additional copper is electroplated onto the seed layer to build up the desired thickness, typically 25µm to 35µm for standard vias and 5µm to 15µm for micro vias.
Filling and Capping
In some cases, vias may be filled with a non-conductive material or capped with copper pads on one or both sides. Via filling is used to improve thermal transfer, increase mechanical strength, or provide a flat surface for component placement or printing.
Via capping is used to create blind or buried vias, where the via is only accessible from one side of the board. The via is drilled and plated, then filled with a non-conductive material and capped with a copper pad on one side. This allows the via to connect to an inner layer without being visible on the outer layer.
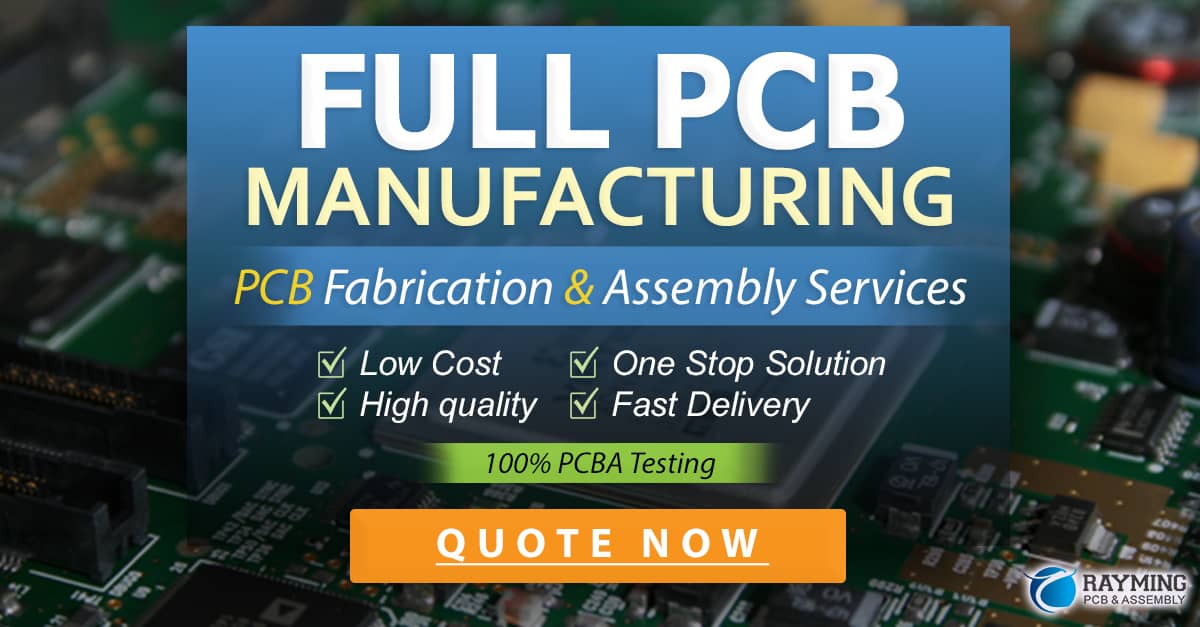
PCB Via Reliability and Testing
Via Reliability Concerns
PCB vias are subject to various reliability concerns, including:
-
Thermal stress: Vias can experience thermal stress due to the mismatch in thermal expansion between the PCB material and the copper plating. This can cause via cracking or delamination over time.
-
Mechanical stress: Vias can be subjected to mechanical stress during PCB Assembly, such as during component placement or soldering. This can cause via damage or disconnection.
-
Contamination: Contaminants such as flux residue or moisture can enter via holes and cause corrosion or insulation resistance issues.
-
Plating defects: Incomplete or non-uniform plating can result in weak or open connections, while overplating can cause via protrusion or shorts.
Via Testing Methods
To ensure the reliability of PCB vias, various testing methods are used during manufacturing and assembly:
-
Continuity test: A simple electrical test to verify that vias are properly connected and not open or shorted.
-
Cross-section analysis: A destructive test where the PCB is cut and the via cross-section is examined under a microscope to check plating thickness, uniformity, and any defects.
-
Thermal stress test: The PCB is subjected to temperature cycling to simulate the thermal stresses experienced during operation and check for via cracking or delamination.
-
Impedance test: For high-speed designs, the impedance of the via is measured to ensure it matches the specified impedance of the signal traces.
-
X-ray inspection: Non-destructive X-ray imaging can be used to check for via defects such as voids, cracks, or shorts, especially in blind and buried vias.
Future Trends in PCB Via Technology
As PCB designs continue to push the limits of density and performance, via technology is evolving to keep pace. Some of the emerging trends in PCB via technology include:
High Density Interconnect (HDI)
HDI PCBs use micro vias and fine-pitch traces to achieve very high routing density. Sequential lamination processes are used to build up multiple layers of micro vias, allowing for complex 3D interconnects. HDI technology enables smaller, thinner, and more highly integrated PCB designs.
Embedded Components
Embedding active and passive components within the PCB substrate is an emerging technique to further increase density and reduce board size. Vias play a critical role in connecting to embedded components, requiring precise depth control and specialized materials and processes.
Advanced Via Structures
New via structures are being developed to address signal integrity and thermal management challenges in high-speed designs. Examples include coaxial vias, where a central signal via is surrounded by a concentric ground via, and thermal vias, where a large array of vias is used to transfer heat to internal copper planes.
3D Printed Electronics
Additive manufacturing techniques such as 3D printing are being explored for PCB fabrication, potentially enabling new via geometries and materials. Conductive inks and pastes can be used to create vias in 3D printed PCBs, offering greater design flexibility and rapid prototyping capabilities.
Frequently Asked Questions (FAQ)
1. What is the difference between a through hole via and a blind via?
A through hole via goes through the entire thickness of the PCB, with a pad on both the top and bottom surfaces. A blind via only connects an outer layer to an inner layer, with a pad on one side of the board.
2. How small can PCB vias be?
The minimum size of PCB vias depends on the manufacturing capabilities. Standard mechanical drilled vias can be as small as 0.2mm in diameter, while laser-drilled micro vias can be 0.1mm or less.
3. What is via-in-pad technology?
Via-in-pad is a technique where a via is placed directly in the solder pad of a surface-mount component. This saves space by eliminating the need for a separate via pad and trace. However, it requires careful control of the via filling and capping process to ensure a flat and solderable surface.
4. Can vias be used for thermal management?
Yes, vias can be used to transfer heat from power-dissipating components to internal copper planes or external heatsinks. Thermal vias are typically larger in diameter or arranged in arrays to maximize the heat transfer area.
5. What is the purpose of via stitching?
Via stitching is a technique where multiple vias are placed in close proximity to each other, often in a circular or staggered pattern. This helps to minimize the inductance and impedance discontinuity of the via, improving signal integrity in high-speed designs. Via stitching can also increase the mechanical strength and thermal conductivity of the via.
Conclusion
PCB vias are a critical component in modern PCB design, enabling high-density interconnects and complex multi-layer boards. Understanding the types of vias, design considerations, manufacturing processes, and reliability factors is essential for creating successful PCB designs.
As PCB technology continues to evolve, new via techniques and structures are emerging to address the challenges of high-speed, high-density, and high-reliability applications. From HDI and embedded components to 3D printed electronics, the future of PCB via technology promises ever-greater capabilities and innovation.
0 Comments