How does PCB V-Scoring work?
The V-Scoring process involves creating V-shaped grooves on the surface of a PCB panel using a specialized cutting tool. The grooves are typically cut at a 30-degree angle on both sides of the board, creating a 60-degree V-shaped channel. The depth of the groove is carefully controlled to ensure that it penetrates through the majority of the board’s thickness, leaving only a thin layer of material at the bottom of the groove.
The remaining thin layer, known as the “web,” holds the individual PCBs together within the panel during the manufacturing process. Once all the necessary components have been attached and the PCBs are ready for separation, the boards can be easily broken apart along the V-Scored lines, thanks to the weakened web.
Advantages of PCB V-Scoring
-
Increased efficiency: By allowing multiple PCBs to be manufactured on a single panel, V-Scoring significantly increases production efficiency and reduces overall fabrication time.
-
Cost-effective: V-Scoring minimizes material waste by enabling the production of more PCBs per panel, ultimately reducing the cost per unit.
-
Improved accuracy: V-Scored PCBs have cleaner and more precise edges compared to boards separated using other methods, such as routing or punching.
-
Enhanced flexibility: V-Scoring allows for the creation of PCBs in various shapes and sizes, as the grooves can be cut in any desired pattern.
-
Reduced stress: The V-shaped grooves help distribute stress evenly along the edges of the PCB during the separation process, minimizing the risk of damage to the board or its components.
V-Scoring vs. other PCB separation methods
There are several methods for separating individual PCBs from a larger panel, each with its own advantages and disadvantages. Some of the most common alternatives to V-Scoring include:
Routing
Routing involves using a specialized cutting tool, known as a router, to cut through the entire thickness of the PCB panel, creating individual boards. While routing offers a high degree of precision, it is generally slower and more expensive than V-Scoring, as it requires more time and material to create each cut.
Punching
Punching uses a die to cut through the PCB panel, creating individual boards in a single step. This method is fast and efficient but is limited in terms of the shapes and sizes of PCBs that can be produced. Additionally, punching can sometimes cause stress or damage to the edges of the board.
Scoring and breaking
Scoring and breaking is similar to V-Scoring but involves creating a single, straight score line on the surface of the PCB panel. The panel is then bent along the score line until the individual boards break apart. While this method is simple and cost-effective, it can result in less precise and less consistent edge quality compared to V-Scoring.
Method | Advantages | Disadvantages |
---|---|---|
V-Scoring | Efficient, cost-effective, accurate, flexible | Requires specialized equipment |
Routing | High precision | Slower, more expensive |
Punching | Fast, efficient | Limited shapes and sizes, potential stress or damage |
Scoring and breaking | Simple, cost-effective | Less precise and consistent edge quality |
Factors to consider when implementing PCB V-Scoring
When incorporating V-Scoring into your PCB manufacturing process, there are several key factors to consider:
-
Material: The type of material used for your PCBs can impact the effectiveness of V-Scoring. Some materials, such as FR-4, are well-suited to V-Scoring, while others may require alternative separation methods.
-
Groove depth: The depth of the V-Score groove must be carefully controlled to ensure that it penetrates through the majority of the board’s thickness without completely severing the individual PCBs. The ideal groove depth will depend on the specific material and thickness of your PCBs.
-
Groove angle: The standard angle for V-Score grooves is 30 degrees on each side, creating a 60-degree V-shape. However, some manufacturers may use different angles depending on their specific requirements and equipment capabilities.
-
Panel design: When designing your PCB panel, it’s essential to consider the placement and orientation of the V-Score grooves to ensure optimal material usage and minimize waste. Proper panel design can also help facilitate the easy separation of individual boards once the manufacturing process is complete.
-
Equipment: V-Scoring requires specialized cutting tools and equipment to create the precise grooves needed for successful PCB separation. Investing in high-quality, well-maintained V-Scoring equipment is crucial for achieving consistent and accurate results.
Best practices for successful PCB V-Scoring
To ensure the success of your PCB V-Scoring process, follow these best practices:
-
Work with experienced PCB manufacturers: Partner with PCB manufacturers who have extensive experience with V-Scoring and can provide guidance on the best materials, groove depths, and panel designs for your specific projects.
-
Use high-quality materials: Choose PCB materials that are well-suited to V-Scoring, such as FR-4, to ensure clean and precise separation of individual boards.
-
Optimize panel design: Design your PCB panels with V-Scoring in mind, considering factors such as groove placement, orientation, and material usage to minimize waste and maximize efficiency.
-
Regularly maintain equipment: Keep your V-Scoring equipment well-maintained and calibrated to ensure consistent and accurate groove depths and angles.
-
Test and refine: Continuously test and refine your V-Scoring process, making adjustments as needed to achieve the best possible results for your specific PCB designs and manufacturing requirements.
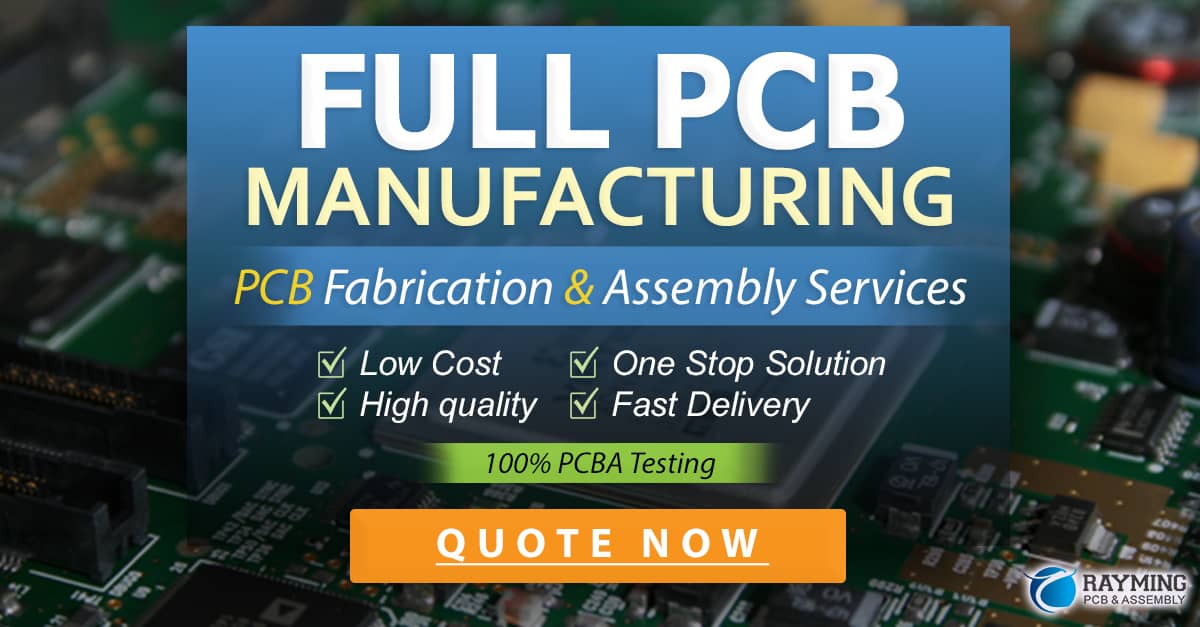
The future of PCB V-Scoring
As the demand for smaller, more complex, and more cost-effective PCBs continues to grow, V-Scoring is likely to remain an essential technique in PCB manufacturing. Advancements in materials, equipment, and design software will enable even more precise and efficient V-Scoring processes, allowing manufacturers to produce high-quality PCBs at a lower cost per unit.
One potential development in the field of PCB V-Scoring is the increasing adoption of laser-based V-Scoring systems. Laser V-Scoring offers several advantages over traditional mechanical V-Scoring methods, including higher precision, improved flexibility, and reduced wear on cutting tools. As laser technology continues to advance and become more affordable, it’s likely that more PCB manufacturers will begin to incorporate laser V-Scoring into their production processes.
Another area of growth for PCB V-Scoring is the increasing use of advanced materials, such as high-frequency laminates and flexible substrates. These materials may require specialized V-Scoring techniques and equipment to ensure clean and precise separation of individual boards. As the use of these advanced materials becomes more widespread, PCB manufacturers will need to adapt their V-Scoring processes accordingly.
Frequently Asked Questions (FAQ)
-
What is the purpose of PCB V-Scoring?
PCB V-Scoring is used to create V-shaped grooves on the surface of a PCB panel, allowing for the easy separation of individual PCBs once the manufacturing process is complete. This technique enables the production of multiple PCBs on a single panel, increasing efficiency and reducing material waste. -
What is the standard angle for V-Score grooves?
The standard angle for V-Score grooves is 30 degrees on each side of the groove, creating a 60-degree V-shape. However, some manufacturers may use different angles depending on their specific requirements and equipment capabilities. -
How does V-Scoring differ from other PCB separation methods?
V-Scoring differs from other separation methods, such as routing and punching, in terms of the groove shape and depth. V-Scoring creates a V-shaped groove that penetrates through most of the board’s thickness, leaving a thin web of material to hold the individual PCBs together. This method offers improved efficiency, cost-effectiveness, and edge quality compared to alternative separation techniques. -
Can all PCB materials be V-Scored?
While many common PCB materials, such as FR-4, are well-suited to V-Scoring, some advanced materials may require specialized V-Scoring techniques or alternative separation methods. It’s essential to consult with experienced PCB manufacturers to determine the best approach for your specific material and design requirements. -
What equipment is needed for PCB V-Scoring?
PCB V-Scoring requires specialized cutting tools and equipment designed to create precise V-shaped grooves on the surface of the PCB panel. This equipment must be well-maintained and calibrated to ensure consistent and accurate results. Some manufacturers may also invest in advanced technologies, such as laser V-Scoring systems, to improve precision and flexibility.
In conclusion, PCB V-Scoring is a crucial technique in the manufacturing of printed circuit boards, offering numerous benefits in terms of efficiency, cost-effectiveness, and edge quality. By understanding the principles behind V-Scoring, as well as the best practices for implementation, PCB manufacturers can optimize their production processes and deliver high-quality, cost-effective PCBs to meet the ever-growing demands of the electronics industry. As technology continues to advance, it’s likely that V-Scoring will remain an essential tool in PCB manufacturing, adapting to new materials, designs, and production requirements.
0 Comments