The Importance of PCB Etching
PCB etching plays a crucial role in the production of high-quality and reliable printed circuit boards. Some of the key reasons why PCB etching is important include:
-
Creating the desired circuit pattern: Etching removes the unwanted copper from the PCB substrate, leaving behind the desired circuit pattern. This ensures that the electronic components are connected correctly and the device functions as intended.
-
Ensuring proper electrical conductivity: By removing the excess copper, etching helps maintain the proper electrical conductivity of the circuit. This is essential for the accurate transmission of signals and the overall performance of the electronic device.
-
Improving the reliability of the PCB: Proper etching techniques help create clean and precise circuit patterns, which contribute to the reliability and longevity of the PCB. Poorly etched boards can lead to short circuits, signal interference, and other issues that can compromise the device’s performance.
-
Facilitating miniaturization: As electronic devices become smaller and more compact, PCB etching techniques have evolved to create finer and more intricate circuit patterns. This allows for the development of smaller, more advanced electronic devices.
The PCB Etching Process
The PCB etching process typically involves the following steps:
-
PCB design and layout: The first step is to create the PCB design using specialized software. This includes determining the placement of components, routing the traces, and generating the necessary files for manufacturing.
-
PCB fabrication: The PCB substrate, usually made of fiberglass or other insulating materials, is coated with a thin layer of copper on one or both sides. This copper layer will be etched to create the desired circuit pattern.
-
Applying the etching resist: A photoresist or screen-printed etch resist is applied to the copper surface. This resist is a protective layer that will prevent the copper from being etched away in the desired circuit areas.
-
Exposing the resist: The PCB is then exposed to UV light through a photomask or film containing the circuit pattern. This hardens the resist in the exposed areas, while the unexposed areas remain soluble.
-
Developing the resist: The PCB is placed in a developing solution that removes the unexposed resist, revealing the copper areas to be etched away.
-
Etching the copper: The PCB is then submerged in an etching solution, typically containing ferric chloride or ammonium persulfate. This solution chemically reacts with the exposed copper, dissolving it and leaving behind the desired circuit pattern protected by the hardened resist.
-
Removing the resist: After etching, the remaining resist is stripped away using a chemical solution, revealing the final circuit pattern on the PCB.
-
Cleaning and inspecting: The PCB is cleaned and inspected for any defects or irregularities. If necessary, minor corrections can be made before the board moves on to the next stages of production.
Types of PCB Etching
There are two main types of PCB etching: chemical etching and plasma etching.
Chemical Etching
Chemical etching is the most common method used in PCB manufacturing. It involves the use of chemical solutions, such as ferric chloride or ammonium persulfate, to dissolve the unwanted copper from the PCB substrate.
Advantages of chemical etching include:
- Cost-effectiveness for high-volume production
- Compatibility with a wide range of PCB materials
- Well-established and widely used process
Disadvantages of chemical etching include:
- Potential environmental concerns related to the disposal of etching solutions
- Limitations in creating very fine pitch traces and high-density designs
- Slower etching process compared to plasma etching
Plasma Etching
Plasma etching, also known as dry etching, uses ionized gas (plasma) to remove the unwanted copper from the PCB substrate. This method is gaining popularity due to its ability to create finer and more precise circuit patterns.
Advantages of plasma etching include:
- Higher precision and resolution compared to chemical etching
- Ability to create very fine pitch traces and high-density designs
- Faster etching process
- More environmentally friendly, as it does not require the use of harsh chemicals
Disadvantages of plasma etching include:
- Higher equipment and operation costs compared to chemical etching
- Limited compatibility with certain PCB materials
- Requires specialized equipment and skilled operators
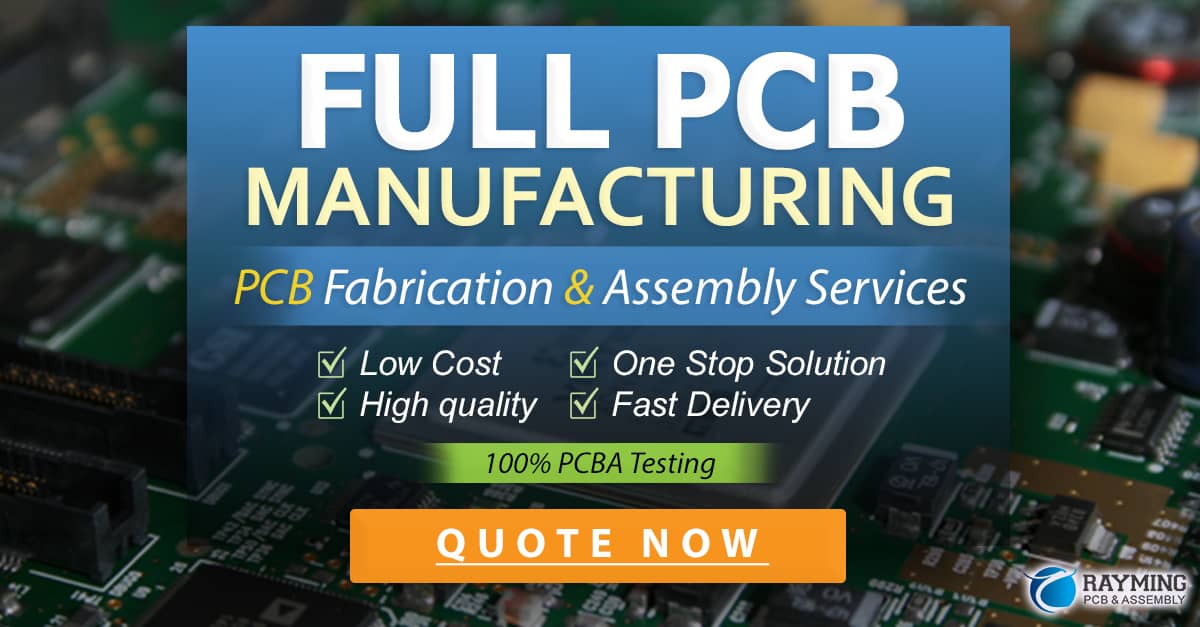
Factors Affecting PCB Etching Quality
Several factors can affect the quality and accuracy of PCB etching:
-
Etching solution concentration and temperature: The concentration and temperature of the etching solution can impact the etching rate and the quality of the resulting circuit pattern. Optimal conditions must be maintained to ensure consistent results.
-
Etching time: The duration of the etching process must be carefully controlled to avoid over-etching or under-etching the copper. Over-etching can lead to damaged traces, while under-etching can result in unwanted copper remnants.
-
PCB material and copper thickness: Different PCB materials and copper thicknesses may require adjustments to the etching process parameters to achieve the desired results.
-
Resist quality and application: The quality and proper application of the etching resist are crucial for creating accurate and clean circuit patterns. Any defects or inconsistencies in the resist can lead to etching errors.
-
Equipment maintenance and calibration: Regular maintenance and calibration of etching equipment are essential to ensure consistent performance and high-quality results.
Advancements in PCB Etching Technology
As the demand for smaller, more complex, and high-performance electronic devices grows, PCB etching technology continues to evolve. Some of the recent advancements in this field include:
-
Direct Imager (DI) technology: DI systems use high-resolution lasers or LED light sources to directly expose the resist on the PCB, eliminating the need for photomasks. This technology enables faster processing times, higher precision, and reduced costs.
-
Laser-assisted etching: Laser-assisted etching uses focused laser beams to selectively remove copper from the PCB substrate. This method offers high precision, fine feature resolution, and the ability to create intricate circuit patterns.
-
Inkjet printing of etch resist: Inkjet printing technology is being explored as an alternative method for applying etch resist to PCBs. This approach offers the potential for faster, more flexible, and cost-effective resist application, especially for low-volume or prototype production.
-
Environmentally friendly etching solutions: Researchers are developing more eco-friendly etching solutions and processes to reduce the environmental impact of PCB manufacturing. This includes the use of less hazardous chemicals and the implementation of closed-loop systems for etching solution recycling.
FAQ
-
What is the purpose of PCB etching?
PCB etching removes unwanted copper from the PCB substrate to create the desired circuit pattern, ensuring proper electrical conductivity and the correct functioning of the electronic device. -
What are the two main types of PCB etching?
The two main types of PCB etching are chemical etching, which uses chemical solutions to dissolve the unwanted copper, and plasma etching, which uses ionized gas to remove the copper. -
What factors can affect the quality of PCB etching?
Factors that can affect PCB etching quality include etching solution concentration and temperature, etching time, PCB material and copper thickness, resist quality and application, and equipment maintenance and calibration. -
What are some recent advancements in PCB etching technology?
Recent advancements in PCB etching technology include Direct Imager (DI) technology, laser-assisted etching, inkjet printing of etch resist, and the development of more environmentally friendly etching solutions. -
Why is the development of environmentally friendly etching solutions important?
Developing environmentally friendly etching solutions is important to reduce the environmental impact of PCB manufacturing. This includes using less hazardous chemicals and implementing closed-loop systems for etching solution recycling, which can help minimize waste and pollution associated with the etching process.
Etching Method | Advantages | Disadvantages |
---|---|---|
Chemical Etching | – Cost-effective for high-volume production – Compatible with a wide range of PCB materials – Well-established and widely used process |
– Potential environmental concerns related to the disposal of etching solutions – Limitations in creating very fine pitch traces and high-density designs – Slower etching process compared to plasma etching |
Plasma Etching | – Higher precision and resolution compared to chemical etching – Ability to create very fine pitch traces and high-density designs – Faster etching process – More environmentally friendly, as it does not require the use of harsh chemicals |
– Higher equipment and operation costs compared to chemical etching – Limited compatibility with certain PCB materials – Requires specialized equipment and skilled operators |
PCB etching is a vital process in the manufacturing of printed circuit boards, ensuring the proper functioning and reliability of electronic devices. As technology advances and the demand for more complex and high-performance devices grows, PCB etching techniques will continue to evolve to meet these challenges. By understanding the importance of PCB etching, the various methods available, and the factors that affect etching quality, manufacturers can optimize their processes to produce high-quality, reliable, and environmentally sustainable PCBs.
0 Comments