Understanding PCB Copper Layers
What are PCB Copper Layers?
PCB copper layers are thin sheets of copper foil laminated onto the surface of a non-conductive substrate, typically made of fiberglass or other materials. These copper layers form the conductive pathways that allow electrical signals to travel between components on the PCB. The number and arrangement of copper layers can vary depending on the complexity and requirements of the electronic design.
The Importance of PCB Copper Layers
PCB copper layers play a crucial role in the functionality and performance of electronic devices. They serve several key purposes:
-
Electrical Connectivity: Copper layers provide the conductive pathways necessary for electrical signals to flow between components on the PCB. They enable the interconnection of various electronic components, such as resistors, capacitors, and integrated circuits (ICs).
-
Signal Integrity: Well-designed copper layers help maintain signal integrity by minimizing electromagnetic interference (EMI) and crosstalk between different signals. Proper routing and spacing of copper traces can reduce signal distortion and ensure reliable communication within the circuit.
-
Power Distribution: Copper layers are also used to distribute power throughout the PCB. Dedicated power planes or wider traces are often employed to provide a low-impedance path for power delivery to the components, ensuring stable and efficient operation.
-
Heat Dissipation: Copper layers can act as heat sinks, helping to dissipate heat generated by electronic components. The thermal conductivity of copper allows it to effectively transfer heat away from hot spots on the PCB, preventing overheating and improving the overall reliability of the device.
Types of PCB Copper Layers
PCBs can be categorized based on the number and arrangement of copper layers they contain. The most common types of PCB copper layers include:
Single-Layer PCBs
Single-layer PCBs, also known as Single-sided PCBs, have copper on only one side of the substrate. Components are mounted on the opposite side, and the copper layer is used for both signal routing and component connectivity. Single-layer PCBs are the simplest and most cost-effective option, suitable for basic and low-density designs.
Double-Layer PCBs
Double-layer PCBs, or Double-Sided PCBs, have copper layers on both sides of the substrate. Components can be mounted on either side, and the two layers are interconnected through conductive vias. Double-layer PCBs offer increased routing flexibility and higher component density compared to single-layer PCBs. They are commonly used in more complex designs where single-layer PCBs are insufficient.
Multi-Layer PCBs
Multi-layer PCBs consist of three or more copper layers, with insulating layers separating them. The inner layers are typically used for power and ground planes, while the outer layers are used for signal routing and component placement. Multi-layer PCBs offer several advantages:
- Increased routing density and complexity
- Improved signal integrity and reduced EMI
- Better power distribution and heat dissipation
- Compact and space-saving designs
The number of layers in a multi-layer PCB can vary, with common configurations being 4, 6, 8, or even more layers, depending on the complexity and requirements of the design.
PCB Copper Layer Specifications
When designing and fabricating PCBs, several key specifications related to copper layers must be considered:
Copper Thickness
The thickness of the copper layers is an important factor in PCB design. It is typically measured in ounces per square foot (oz/ft²) or microns (μm). Common copper thicknesses include:
Copper Thickness | Ounces per Square Foot (oz/ft²) | Microns (μm) |
---|---|---|
0.5 oz | 0.5 | 17.5 |
1 oz | 1.0 | 35 |
2 oz | 2.0 | 70 |
3 oz | 3.0 | 105 |
The choice of copper thickness depends on factors such as current carrying capacity, trace width, and manufacturing constraints. Thicker copper layers can handle higher currents and provide better heat dissipation but may increase the overall cost and weight of the PCB.
Copper Trace Width and Spacing
The width and spacing of copper traces on a PCB are critical for ensuring proper signal integrity and preventing signal interference. The trace width determines the current carrying capacity and resistance of the trace, while the spacing between traces affects crosstalk and EMI.
Designers must adhere to specific design rules and guidelines when determining trace width and spacing. These rules consider factors such as the signal frequency, impedance requirements, and manufacturing capabilities. Proper trace width and spacing help maintain signal integrity, reduce signal distortion, and ensure reliable operation of the electronic device.
Copper Pour and Ground Planes
Copper pour, also known as copper fill or copper flooding, is a technique used to fill unused areas of a PCB layer with copper. This technique offers several benefits:
- Improved EMI Shielding
- Better heat dissipation
- Reduced impedance for power distribution
- Enhanced mechanical stability of the PCB
Ground planes are dedicated copper layers that provide a low-impedance reference for electrical signals. They help to minimize EMI, reduce signal noise, and provide a stable reference voltage for the circuit. Ground planes are commonly used in multi-layer PCBs to improve signal integrity and power distribution.
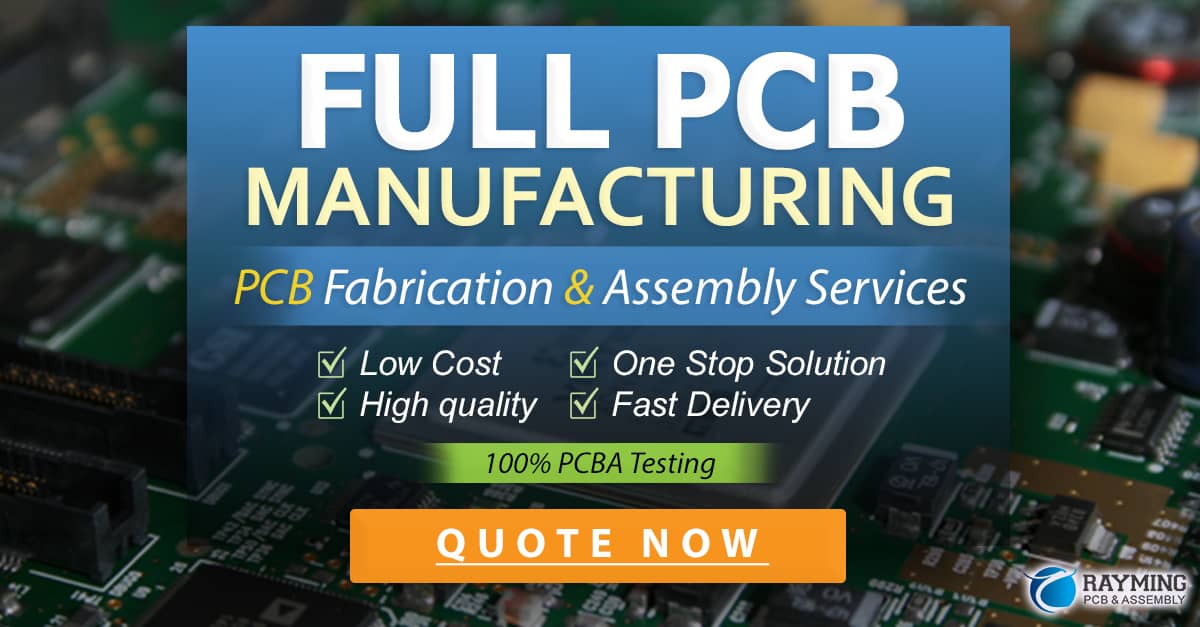
PCB Copper Layer Manufacturing Process
The manufacturing process for PCB copper layers involves several key steps:
-
Copper Foil Lamination: The PCB substrate is laminated with copper foil on one or both sides using heat and pressure. The copper foil is typically pre-coated with an adhesive to ensure proper bonding to the substrate.
-
Photoresist Application: A photoresist layer is applied to the copper surface. This light-sensitive material will later be used to transfer the desired copper pattern onto the PCB.
-
Exposure and Development: The photoresist-coated PCB is exposed to UV light through a photomask, which contains the desired copper pattern. The exposed areas of the photoresist become soluble and are removed during the development process, leaving the desired copper pattern protected by the remaining photoresist.
-
Etching: The exposed copper areas not protected by the photoresist are chemically etched away using an etchant solution, typically containing cupric chloride or ammonium persulfate. This process removes the unwanted copper, leaving only the desired copper traces and features on the PCB.
-
Photoresist Removal: After etching, the remaining photoresist is stripped away, revealing the final copper pattern on the PCB.
-
Inspection and Quality Control: The manufactured PCB undergoes thorough inspection and quality control procedures to ensure the accuracy and integrity of the copper layers. This includes visual inspection, electrical testing, and automated optical inspection (AOI) to detect any defects or irregularities.
Designing with PCB Copper Layers
When designing PCBs, engineers and designers must consider several factors related to copper layers to ensure optimal performance and manufacturability:
Design for Manufacturing (DFM)
Design for Manufacturing (DFM) principles should be applied to PCB copper layer design to ensure the design is compatible with the manufacturing process. This includes adhering to minimum trace widths, spacing requirements, and copper thicknesses specified by the PCB manufacturer. DFM guidelines help to minimize manufacturing issues, improve yield, and reduce overall production costs.
Signal Integrity and EMI Considerations
Proper design of PCB copper layers is crucial for maintaining signal integrity and minimizing electromagnetic interference (EMI). Designers should consider factors such as trace routing, impedance control, and layer stackup to optimize signal quality and reduce noise. Techniques such as ground planes, shielding, and proper trace spacing can help mitigate EMI and ensure reliable operation of the electronic device.
Thermal Management
Copper layers play a significant role in thermal management of PCBs. Designers should consider the thermal requirements of the electronic components and design the copper layers accordingly. Techniques such as copper pours, thermal vias, and dedicated thermal layers can help dissipate heat effectively and prevent overheating of components.
Design Tools and Simulation
PCB design software and simulation tools are essential for creating and validating PCB copper layer designs. These tools allow designers to create schematic diagrams, perform layout and routing, and simulate the electrical and thermal behavior of the PCB. Popular PCB design software includes Altium Designer, Cadence OrCAD, and KiCad, among others. Simulation tools help to identify potential issues and optimize the design before manufacturing, saving time and reducing development costs.
Frequently Asked Questions (FAQ)
-
What is the purpose of PCB copper layers?
PCB copper layers provide the conductive pathways for electrical signals to flow between components on the PCB. They enable electrical connectivity, power distribution, and help maintain signal integrity. -
How do I choose the appropriate copper thickness for my PCB?
The choice of copper thickness depends on factors such as current carrying capacity, trace width, and manufacturing constraints. Thicker copper layers can handle higher currents and provide better heat dissipation but may increase the overall cost and weight of the PCB. Consult with your PCB manufacturer and consider the specific requirements of your design to determine the appropriate copper thickness. -
What is the difference between single-layer and multi-layer PCBs?
Single-layer PCBs have copper on only one side of the substrate, while multi-layer PCBs consist of three or more copper layers with insulating layers separating them. Multi-layer PCBs offer increased routing density, improved signal integrity, and better power distribution compared to single-layer PCBs. The choice between single-layer and multi-layer PCBs depends on the complexity and requirements of the electronic design. -
How do I ensure proper signal integrity in my PCB copper layer design?
To ensure proper signal integrity, consider factors such as trace routing, impedance control, and layer stackup. Use techniques like ground planes, shielding, and proper trace spacing to minimize EMI and reduce signal distortion. Simulate your design using PCB design software and perform thorough testing to validate the signal integrity of your PCB. -
What is the role of copper pour in PCB design?
Copper pour, also known as copper fill or copper flooding, is a technique used to fill unused areas of a PCB layer with copper. It offers benefits such as improved EMI shielding, better heat dissipation, reduced impedance for power distribution, and enhanced mechanical stability of the PCB. Copper pour helps to optimize the performance and reliability of the electronic device.
Conclusion
PCB copper layers are essential components in the design and fabrication of electronic devices. They provide the necessary electrical connectivity, power distribution, and signal integrity required for reliable operation. Understanding the types, specifications, and manufacturing process of PCB copper layers is crucial for designers and engineers to create high-quality and efficient electronic products.
By considering factors such as copper thickness, trace width and spacing, copper pour, and ground planes, designers can optimize the performance and manufacturability of their PCB designs. Adhering to DFM principles, applying signal integrity and EMI mitigation techniques, and utilizing design tools and simulations further enhance the quality and reliability of PCB copper layer designs.
As technology advances and electronic devices become increasingly complex, the importance of well-designed PCB copper layers will only continue to grow. By staying updated with the latest techniques, materials, and manufacturing processes, designers and engineers can create innovative and reliable electronic products that meet the evolving needs of the industry.
0 Comments